Определение прочности бетона и методы контроля
Определение прочности бетона – это обязательное условие контроля качества железобетонных изделий при их производстве. От прочности бетона зависит безопасность и срок эксплуатации любой железобетонной конструкции. На прочность бетона влияет много факторов, начиная от качества используемых для изготовления материалов, заканчивая соблюдением технологических требований к процессу производства. Прочность бетона определяет его маркировку, под которой состав поступает в продажу. Например, марка М400 свидетельствует о том, что максимальная нагрузка, выдерживаемая материалом, составляет 400 кг/см2.
Испытание бетона на прочность подразумевает приложение к нему контрольной нагрузки, направленной на разрушение целостности его структуры. Для данных испытаний используют контрольные образцы либо производят отбор проб бетона непосредственно из обследуемой конструкции.
Методы определения прочности бетона
Проводить определение прочности бетона в России можно только с учетом нормативов, установленных стандартом ГОСТ 18105-2010.
- Разрушающие. Испытание бетона в этом случае проводят с использованием контрольных образцов, подвергающихся твердению в одинаковых с конструкцией условиях, либо изымаемых непосредственно из бетонного монолита после достижения им необходимых показателей твердости. Эти методы определения прочности бетона считаются наиболее точными.
- Неразрушающие косвенные. К этой категории относят ультразвуковые исследования (по ГОСТ 17624-2012), методы упругого отскока и ударного импульса (ГОСТ 22690-2015). Важно отметить, что эти методы названы так потому что прочность оценивают косвенно, через другой параметр, измеряя, например скорость ультразвука, а по ней вычисляя прочность на основании установленных экспериментально зависимостей. Эти методы определения прочности бетона без предварительно градуировки могут дать погрешность до 30…50%, их нельзя использовать для вычислений, требующих достоверности и точности получаемых значений без корректировок результатов на основе прямых методов.
- Неразрушающие прямые. Испытание бетона в этом случае можно выполнять одним из двух методов. Первый из них предусматривает отрыв заделанного в бетон металлического анкера и измерение необходимой для этого нагрузки создаваемой при помощи специального оборудования. Второй (в данной подгруппе) метод определения прочности бетона основан на измерении усилия, прилагаемого для скалывания участка внешнего ребра бетонной конструкции.
Все замеры и испытания, в рамках которых производится определение прочности бетона, подразумевают использование специальных инструментов и приборов (измерители прочности бетона), позволяющих гарантировать точность выполняемых процедур. Именно аппаратные измерения дают наиболее достоверный результат и позволяют выполнять все необходимые манипуляции в кратчайшие сроки и без остановки процессов строительства и ведения других работ на объекте.
Приборы серии ОНИКС для определения прочности бетона
Современные приборы для определения прочности бетона серий ОНИКС и ПУЛЬСАР, выпускаемые компанией «Интерприбор», ориентированы на использование всех имеющихся методов определения прочности и прекрасно подходят для проведения испытаний и в лаборатории и на строительной площадке методами скола ребра, отрыва со скалыванием, по скорости прохождения ультразвука и методом ударного импульса.
Использование высокоточных технических средств гарантирует высокую скорость и точность при фиксации параметров прочности. Это позволяет быстро получать достоверные результаты при определении прочности бетона непосредственно на исследуемом объекте без разрушения бетонного монолита.
Испытание бетона на прочность. Определение прочности бетона.
№ п/п | Наименование испытания | Нормативный документ | Стоимость в рублях |
---|---|---|---|
Испытание бетона на прочность, растворов, ж/б конструкций |
|||
1 | Определение прочности одного образца-куба бетона(раствора) на сжатие |
ГОСТ 10180-2012 | 250 |
2 | Определение прочности одного образца-керна, отобранного из конструкции, на сжатие | ГОСТ 28570-90 ГОСТ 10180-2012 |
550 |
3 | Определение прочности образца раствора, отобранного из швов кладки | ГОСТ 5802-86 | 1 500 |
4 | Определение прочности бетона (раствора) неразрушающими методами контроля на участке конструкции (Методы: упругий отскок, ударный импульс, ультразвуковой) | ГОСТ 22690-2015 ГОСТ 17624-2012 ГОСТ 31914-2012 |
250 |
5 | Определение прочности бетона методом отрыва со скалыванием |
ГОСТ 22690-2015 | 800 |
6 | Определение расположения арматуры и закладных деталей | ГОСТ 22904-93 | 500 |
7 | Определение ширины и глубины раскрытия трещин | ГОСТ 31937-2011 | 800 |
8 | Определение толщины защитного слоя бетона и диаметра арматуры | ГОСТ 22904-93 | 500 |
9 | Определение водонепроницаемости бетона на образцах/конструкциях | ГОСТ 12730.![]() ГОСТ 12730.5-84 |
400/700 |
10 | Определение влажности бетона/раствора | ГОСТ 12730.0-78 ГОСТ 12730.2-78 ГОСТ 5802-86 |
250 |
11 | Определение удобоукладываемости (подвижности) бетонной (растворной) смеси | ГОСТ 10181-2014 | 600 |
12 | Определение концентрации химических добавок строительных растворов | ГОСТ 30459-2008 | 1 500 |
13 | Определение средней плотности бетонной смеси | ГОСТ 10181-2014 | 500 |
14 | Определение прочности (марки) цемента с изготовлением образцов | ГОСТ 310.4-81 | 12 000 |
15 | Определение прочности стяжки и штукатурки | ГОСТ 22690-2015 |
500 |
Строительная лаборатория «Тест Констракшн» выполняет услуги по проведению испытаний бетона, строительных растворов и железобетонных конструкций. Испытания производятся в строгом соответствии с действующими ГОСТ как в лабораторных условиях, так и на строительных площадках.
При проведении испытаний проверяются следующие параметры:
- Плотность;
- Прочность;
- Водонепроницаемость;
- Морозостойкость;
- Расположение арматуры в конструкциях
- Толщины защитного слоя;
- Влажность.
Методы определения прочности бетона
Существует два способа определения прочности: разрушающий и не разрушающий.
Ультразвуковое определение прочности бетона
Одним из самых эффективных методов проверки прочности и дефектов бетона, является ультразвуковая проверка. Кроме прочности, таким методом можно определить наличие пустот и других дефектов.
Существует два основных метода проверки бетона ультразвуком:
- Сквозной метод, когда через всю толщину конструкции происходит просвечивание. При проведении данного метода, датчики измерения скорости ультразвуковых волн располагаются на противоположных сторонах;
- поверхностный метод, когда датчики измерения скорости ультразвука располагаются на одной стороне.
Определение водонепроницаемости бетона
Водонепроницаемость – это одна из основных характеристик. От водонепроницаемости зависит, требуются ли дополнительные гидроизолирующие мероприятия, пластификатор и подходит ли бетон вообще. Значение параметра определяется лабораторно в соответствии с требованиями по ГОСТ 12730.5-84.
Виды испытаний на водонепроницаемость:
- По мокрому пятну.
- Коэффициент фильтрации.
- Фильтратометрия за короткие сроки.
- Вычисление воздухопроницаемости ускоренное.
Мокрое пятно
При проведении данного испытания, исследуются не менее шести образцов, с предварительным определением влажности бетона. К образцам в специальной форме, внутренним диаметром которого составляет 150 мм, с открытыми торцами, прикладывается водяное давление с шагом 0,2 МПа. Не менее часа вода должна обязательно пройти деаэрацию. Если вода просачивается через верхний торец в виде мокрого пятна или каплей, то испытания завершаются.
Образцы имеют разную высоту: 30, 50,100, 150 мм. Время выдержки для каждого образца тоже разное: 4, 6, 12, 16 часов.
Определение коэффициента фильтрации
Суть данного метода является определение объема фильтрата, проходящего при заданном давлении через образец. Проводится данный метод на специальной установке, где все образцы перед началом выдерживаются в специальных условиях. Выбуренные образцы также могут использоваться.
Давление с выдержкой через каждый час, поднимают ступенчато. Вода, которая прошла через образец, собирается и взвешивается. Влага, которая не имеет вид капель — поглощается сорбентом типа силикагеля. Данный метод достаточно долгий по времени и трудоемкий.
Фильтратометрия
Данный метод считается ускоренным и для его проведения используется ручной прибор-фильтратомер. Исследуются не менее шести образцов, путем измерения скорости падения давления, созданного насосом в 10 МПа. По результатам всех испытаний вычисляется среднее значение. Если давление падает быстро и поддерживать его получается, то коэффициент принимается большим, чем 10-8 см/с, что соответствует марке В2 или менее.
Определение воздушной проницаемости
Данный метод проводится при помощи прибора «Агама-2Р» в соответствии инструкцией.
Влияющие факторы на водонепроницаемость
Водонепроницаемость может регулироваться путем использования специальных вяжущих веществ, которые уменьшают пористость бетона, а также использование химических добавок. Современные добавки, присадки, уплотнители позволяют сократить пористость и придать материалу необходимую гидрофобность.
Водонепроницаемость можно повысить при помощи использования горизонтальной и/или вертикальной гидроизоляции. Но самой эффективной на сегодняшний день остается проникающая изоляция.
Определение подвижности бетона
Подвижность бетонной смеси одна из основных факторов, влияющих на формование материала в опалубке.
Основной технологический параметр бетонной смеси — удобоукладываемость – это способность раствора заполнять опалубку и принимать ее форму.
Определение подвижности бетонной смеси производится как на строительной площадке, так и в лаборатории.
Определение эластичности конусом является самым простым и частым методом измерения.
Определение прочности бетона на сжатие
В настоящее время классификация бетона (марка бетона) помогает проектировать бетонные и железобетонные конструкции с оптимальными характеристиками.
При использовании средних показателей прочности возникает риск, что реальные характеристики бетона окажутся ниже расчетных. Когда средние показатели используются в качестве наименьших, то приходится увеличивать размеры бетонной конструкции, а это шаг к удорожанию.
Методы определения прочности
Существует два способа определить прочность бетона и в обоих случаях необходимо использование сертифицированного оборудования. Существует два способа определения прочности разрушающий и неразрушающий.
Разрушающий способ
При проведении этого испытания используются образцы, очищенные от загрязнений и абсолютно ровными гранями. Их по очереди устанавливают под пресс и подвергают нагрузке, при этом показатели, при которых образцы начинают разрушатся, фиксируются в протоколе. По результатам испытания определяется фактическое значение, которое сравнивается с проектным и нормативным показателем.
Разрушающий способ обязательно используется на заводах, занимающихся производством ЖБИ и на строительных площадках.
Лабораторные исследования разрушающим способом считаются наиболее достоверными, а полученные значения учитываются архитекторами и конструкторами.
№ п/п | Наименование испытания | Нормативный документ | Стоимость в рублях |
---|---|---|---|
Испытание бетона на прочность, растворов, ж/б конструкций |
|||
1 | Определение прочности одного образца-куба бетона(раствора) на сжатие |
ГОСТ 10180-2012 | 250 |
2 | Определение прочности одного образца-керна, отобранного из конструкции, на сжатие | ГОСТ 28570-90 ГОСТ 10180-2012 |
550 |
3 | Определение прочности образца раствора, отобранного из швов кладки | ГОСТ 5802-86 | 1 500 |
4 | Определение прочности бетона (раствора) неразрушающими методами контроля на участке конструкции (Методы: упругий отскок, ударный импульс, ультразвуковой) | ГОСТ 22690-2015 ГОСТ 17624-2012 ГОСТ 18105-2010 ГОСТ 31914-2012 |
250 |
5 | Определение прочности бетона методом отрыва со скалыванием |
ГОСТ 22690-2015 | 800 |
6 | Определение расположения арматуры и закладных деталей | ГОСТ 22904-93 | 500 |
7 | Определение ширины и глубины раскрытия трещин | ГОСТ 31937-2011 | 800 |
8 | Определение толщины защитного слоя бетона и диаметра арматуры | ГОСТ 22904-93 | 500 |
9 | Определение водонепроницаемости бетона на образцах/конструкциях | ГОСТ 12730.![]() ГОСТ 12730.5-84 |
400/700 |
10 | Определение влажности бетона/раствора | ГОСТ 12730.0-78 ГОСТ 12730.2-78 ГОСТ 5802-86 |
250 |
11 | Определение удобоукладываемости (подвижности) бетонной (растворной) смеси | ГОСТ 10181-2014 | 600 |
12 | Определение концентрации химических добавок строительных растворов | ГОСТ 30459-2008 | 1 500 |
13 | Определение средней плотности бетонной смеси | ГОСТ 10181-2014 | 500 |
14 | Определение прочности (марки) цемента с изготовлением образцов | ГОСТ 310.4-81 | 12 000 |
15 | Определение прочности стяжки и штукатурки | ГОСТ 22690-2015 |
500 |
Строительная лаборатория «Тест Констракшн» выполняет услуги по проведению испытаний бетона, строительных растворов и железобетонных конструкций. Испытания производятся в строгом соответствии с действующими ГОСТ как в лабораторных условиях, так и на строительных площадках.
При проведении испытаний проверяются следующие параметры:
- Плотность;
- Прочность;
- Водонепроницаемость;
- Морозостойкость;
- Расположение арматуры в конструкциях
- Толщины защитного слоя;
- Влажность.
Методы определения прочности бетона
Существует два способа определения прочности: разрушающий и не разрушающий.
Ультразвуковое определение прочности бетона
Одним из самых эффективных методов проверки прочности и дефектов бетона, является ультразвуковая проверка. Кроме прочности, таким методом можно определить наличие пустот и других дефектов.
Существует два основных метода проверки бетона ультразвуком:
- Сквозной метод, когда через всю толщину конструкции происходит просвечивание. При проведении данного метода, датчики измерения скорости ультразвуковых волн располагаются на противоположных сторонах;
- поверхностный метод, когда датчики измерения скорости ультразвука располагаются на одной стороне.
Определение водонепроницаемости бетона
Водонепроницаемость – это одна из основных характеристик. От водонепроницаемости зависит, требуются ли дополнительные гидроизолирующие мероприятия, пластификатор и подходит ли бетон вообще. Значение параметра определяется лабораторно в соответствии с требованиями по ГОСТ 12730.5-84.
Виды испытаний на водонепроницаемость:
- По мокрому пятну.
- Коэффициент фильтрации.
- Фильтратометрия за короткие сроки.
- Вычисление воздухопроницаемости ускоренное.
Мокрое пятно
При проведении данного испытания, исследуются не менее шести образцов, с предварительным определением влажности бетона. К образцам в специальной форме, внутренним диаметром которого составляет 150 мм, с открытыми торцами, прикладывается водяное давление с шагом 0,2 МПа. Не менее часа вода должна обязательно пройти деаэрацию. Если вода просачивается через верхний торец в виде мокрого пятна или каплей, то испытания завершаются.
Образцы имеют разную высоту: 30, 50,100, 150 мм. Время выдержки для каждого образца тоже разное: 4, 6, 12, 16 часов.
Определение коэффициента фильтрации
Суть данного метода является определение объема фильтрата, проходящего при заданном давлении через образец. Проводится данный метод на специальной установке, где все образцы перед началом выдерживаются в специальных условиях. Выбуренные образцы также могут использоваться.
Давление с выдержкой через каждый час, поднимают ступенчато. Вода, которая прошла через образец, собирается и взвешивается. Влага, которая не имеет вид капель — поглощается сорбентом типа силикагеля. Данный метод достаточно долгий по времени и трудоемкий.
Фильтратометрия
Данный метод считается ускоренным и для его проведения используется ручной прибор-фильтратомер. Исследуются не менее шести образцов, путем измерения скорости падения давления, созданного насосом в 10 МПа. По результатам всех испытаний вычисляется среднее значение. Если давление падает быстро и поддерживать его получается, то коэффициент принимается большим, чем 10-8 см/с, что соответствует марке В2 или менее.
Определение воздушной проницаемости
Данный метод проводится при помощи прибора «Агама-2Р» в соответствии инструкцией.
Влияющие факторы на водонепроницаемость
Водонепроницаемость может регулироваться путем использования специальных вяжущих веществ, которые уменьшают пористость бетона, а также использование химических добавок. Современные добавки, присадки, уплотнители позволяют сократить пористость и придать материалу необходимую гидрофобность.
Водонепроницаемость можно повысить при помощи использования горизонтальной и/или вертикальной гидроизоляции. Но самой эффективной на сегодняшний день остается проникающая изоляция.
Определение подвижности бетона
Подвижность бетонной смеси одна из основных факторов, влияющих на формование материала в опалубке.
Основной технологический параметр бетонной смеси — удобоукладываемость – это способность раствора заполнять опалубку и принимать ее форму.
Определение подвижности бетонной смеси производится как на строительной площадке, так и в лаборатории.
Определение эластичности конусом является самым простым и частым методом измерения.
Определение прочности бетона на сжатие
В настоящее время классификация бетона (марка бетона) помогает проектировать бетонные и железобетонные конструкции с оптимальными характеристиками.
При использовании средних показателей прочности возникает риск, что реальные характеристики бетона окажутся ниже расчетных. Когда средние показатели используются в качестве наименьших, то приходится увеличивать размеры бетонной конструкции, а это шаг к удорожанию.
Методы определения прочности
Существует два способа определить прочность бетона и в обоих случаях необходимо использование сертифицированного оборудования. Существует два способа определения прочности разрушающий и неразрушающий.
Разрушающий способ
При проведении этого испытания используются образцы, очищенные от загрязнений и абсолютно ровными гранями. Их по очереди устанавливают под пресс и подвергают нагрузке, при этом показатели, при которых образцы начинают разрушатся, фиксируются в протоколе. По результатам испытания определяется фактическое значение, которое сравнивается с проектным и нормативным показателем.
Разрушающий способ обязательно используется на заводах, занимающихся производством ЖБИ и на строительных площадках.
Лабораторные исследования разрушающим способом считаются наиболее достоверными, а полученные значения учитываются архитекторами и конструкторами.
ГОСТ 25192-82 Бетоны. Классификация и общие технические требования
ГОСУДАРСТВЕННЫЙ СТАНДАРТ СОЮЗА ССР
БЕТОНЫ
КЛАССИФИКАЦИЯ
И ОБЩИЕ
ТЕХНИЧЕСКИЕ ТРЕБОВАНИЯ
ГОСТ 25192-82
СТ СЭВ 6550-88
ГОСУДАРСТВЕННЫЙ СТРОИТЕЛЬНЫЙ КОМИТЕТ СССР
Москва
ГОСУДАРСТВЕННЫЙ СТАНДАРТ СОЮЗА ССР
БЕТОНЫ Классификация и общие технические требования Concretes. |
ГОСТ |
Постановлением Государственного комитета СССР по делам строительства от 4 марта 1982 г. № 43 срок введения установлен
с 01.01.83
Несоблюдение стандарта преследуется по закону
Настоящий стандарт распространяется на бетоны, применяемые в промышленном, энергетическом, транспортном, водохозяйственном, жилищно-гражданском, сельскохозяйственном и других видах строительства.
Стандарт устанавливает классификацию бетонов и общие технические требования к ним.
Стандарт не распространяется на бетоны на битумных вяжущих.
Требования настоящего
стандарта должны соблюдаться при разработке новых и пересмотре действующих
стандартов и другой нормативно-технической, а также проектной и технологической
документации по бетонам, бетонным и железобетонным конструкциям и изделиям.
Основные термины, применяемые в настоящем стандарте, и их пояснения приведены в
обязательном приложении 1.
1.1. Бетоны классифицируются по следующим признакам:
основному назначению;
виду вяжущего;
виду заполнителей;
структуре;
условия твердения.
1.2. В зависимости от основного назначения бетоны подразделяются на:
конструкционные;
специальные (жаростойкие, химические стойкие, декоративные, радиационно-защитные, теплоизоляционные и др.).
1.3. По виду вяжущего бетоны могут быть на основе:
цементных вяжущих;
известковых вяжущих;
шлаковых вяжущих;
гипсовых вяжущих;
специальных вяжущих.
1.4. По виду заполнителей бетоны могут быть на:
плотных заполнителях;
пористых заполнителях;
специальных заполнителях.
1.5. По структуре бетоны могут быть:
плотной структуры;
поризованной структуры;
ячеистой структуры;
крупнозернистой структуры.
1.5а. По условиям твердения бетоны подразделяются на твердевшие:
в естественных условиях;
в условиях тепловлажностной обработки при атмосферном давлении;
в условиях тепловлажностной обработки при давлении выше атмосферного (автоклавного твердения).
1.6. Наименование бетонов
1.6.1. Наименования бетонов определенных видов должны включать, как правило, все признаки, установленные настоящим стандартом. Признаки, не являющиеся определяющими для бетона данного вида, в его наименование допускается не включать.
В наименованиях специальных видов бетонов указывается их основное назначение, а в наименованиях конструкционных бетонов слово «конструкционный» может быть опущено.
1.6.2. При необходимости уточнения характеристики бетонов в их наименованиях могут указываться конкретные виды вяжущих, заполнителей или условий твердения.
1.6.3. Для бетонов,
характеризуемых наиболее часто применяемыми сочетаниями признаков, применяют
следующие наименования: «бетон тяжелый», «бетон легкий», «бетон ячеистый»,
«бетон силикатный (плотный и ячеистый)».
1.6.4. Наименования основных видов бетонов, образованные в соответствии с установленной настоящим стандартов классификацией, приведены в справочном приложении 2.
2.1. Требования к качеству бетонов должны устанавливаться в соответствии с требованиями настоящего стандарта в зависимости от их назначения и условий работы в конструкциях зданий и сооружений:
в стандартах на бетоны определенного вида;
в стандартах и технических условиях на сборные бетонные и железобетонные изделия;
в рабочих чертежах монолитных бетонных и железобетонных конструкций.
2.2. Требования должны
устанавливаться по показателям, характеризующим прочность, среднюю плотность,
стойкость к различным воздействиям, упругопластические, теплофизические,
защитные, декоративные и другие свойства бетонов, а также по применению
материалов для их приготовления и отдельным технологическим параметрам,
обеспечивающим требуемое качество конструкций и изделий.
Требования к материалам для приготовления бетона (вяжущим, добавкам, заполнителям), его составу и технологическим параметрам должны устанавливаться в нормативно-технической документации на бетон конкретного вида исходя из основных характеристик бетона и условий его твердения, а также в зависимости от назначения конструкций и условий их работы.
2.3. По показателям прочности бетона устанавливаются их гарантированные значения — классы в соответствии с СТ СЭВ 1406-78.
Примечание. Для конструкций, запроектированных ранее без учета требований СТ СЭВ 1406-78, показатели прочности бетона характеризуются марками.
2.4. Марка или класс бетона по прочности определяются прочностью базовых образцов бетона в установленном проектном возрасте, определяемой в соответствии с действующими государственными стандартами.
2.5. Марка бетонов по
морозостойкости определяется количеством циклов попеременного замораживания и
оттаивания в воде, которое выдерживают образцы, изготовленные и испытанные на
морозостойкость согласно требованиям действующих государственных стандартов.
2.6. Марка бетонов по водонепроницаемости определяется максимальной величиной давления воды, при котором не наблюдается ее просачивания через образцы, изготовленные и испытанные на водонепроницаемость согласно требованиям действующих государственных стандартов.
2.7. Марка бетона по средней плотности определяется фактическим значением показателя массы в единице объема (в кг/м3) образцов, изготовленных и испытанных согласно требованиям действующих государственных стандартов.
2.8. Ряды унифицированных значений показателей качества бетонов по маркам или классам устанавливаются в стандартах на соответствующие виды бетонов.
2.9. Соответствие бетонов
установленным требованиям должно обеспечиваться рациональным выбором
материалов, подбором их состава и технологических режимов приготовления,
укладки, уплотнения и твердения в соответствии с действующими технологическими
правилами или стандартами предприятия.
2.10. Определение значений показателей качества бетонов производится путем испытания бетона в конструкциях или испытаний специально изготовленных контрольных образцов.
Соответствие показателей бетонов заданным требованиям устанавливаются путем оценки результатов испытаний, как правило, с учетом показателей однородности.
2.11. Определение значений показателей качества бетонов может осуществляться несколькими методами испытаний, но при этом должна быть обеспечена сравнимость результатов путем установления переходных коэффициентов или другими способами.
Обязательное
ТЕРМИНЫ И ОПРЕДЕЛЕНИЯ
Термин |
Определение |
1. Бетон |
Искусственный
камневидный материал, представляющий собой затвердевшую бетонную смесь. Различают следующие стадии готовности бетона: бетонная смесь, свежеуложенный бетон и затвердевший бетон |
2. Смесь бетонная |
Смесь вяжущих, заполнителей, затворителей и, при необходимости, добавок до ее укладки |
3. Смесь сухая бетонная |
Бетонная смесь без затворителя |
4. Бетоны конструкционные |
Бетоны несущих и ограждающих конструкций зданий и сооружений, определяющими требованиями к качеству которых являются требования по физико-механическим характеристикам |
5. Бетоны специальные |
Бетоны, к которым предъявляются специальные требования в соответствии с их назначением |
5. |
Специальные бетоны, предназначенные для тепловой изоляции конструкций, зданий и сооружений |
5.2. Бетоны жаростойкие |
Специальные бетоны, предназначенные для работы в условиях воздействия температур от 200 до 1800 °С |
5.3. Бетоны химические стойкие |
Специальные бетоны, предназначенные для работы в условиях воздействия агрессивных сред |
5.4. Бетоны напрягающие |
Специальные бетоны на основе напрягающего цемента, расширяющиеся при твердении и предназначенные для создания предварительного напряжения (самонапряжения) и конструкции при его твердении |
5. |
Специальные бетоны, предназначенные для отделки зданий и сооружений |
5.6. Бетоны радиационно-защитные |
Специальные бетоны, предназначенные для защиты от воздействия радиационных излучений |
6. Бетоны на цементных вяжущих (цементные бетоны) |
Бетоны на основе клинкерных цементов |
7. Бетоны на известковых вяжущих |
Бетоны на основе извести в сочетании с гидравлическими активными и (или) кремнеземистыми компонентами (цемент, шлаки, золы, кварцевый песок и активные минеральные добавки) |
8. Бетоны на гипсовых вяжущих |
Бетоны на
основе полуводного гипса или ангидрита (включая гипсоцементно-пуццолановые и
т. |
9. Бетоны на шлаковых вяжущих |
Бетоны на основе молотых шлаков и зол с активизаторами твердения (щелочными растворами, известью, цементом или гипсом) |
10. Бетонополимеры |
Специальные бетоны на минеральном вяжущем, пропитанные монополимерами с их последующим отверждением |
11. Полимербетоны |
Специальные бетоны на основе полимерного вяжущего, химически стойких минеральных заполнителей, наполнителей и добавок |
11а. Бетоны цементно-полимерные |
Специальные бетоны на цементном вяжущем, заполнители которого перед изготовлением бетонной смеси обработаны полимерным составом |
12. |
Бетоны на заполнителях из плотных горных пород или шлаков |
13. Бетоны на пористых заполнителях |
Бетоны на искусственных и естественных минеральных пористых заполнителях, а также на пористых крупных и плотных мелких заполнителях |
14. Бетоны на органических заполнителях (арболит) |
Бетоны на цементном вяжущем и растительного происхождения органических заполнителей (измельченные древесина из отходов производства, стебли хлопчатника или рисовой соломы, костра конопли и льна) |
15. Бетоны мелкозернистые (пескобетон) |
Бетоны плотной структуры на цементном вяжущем и плотных мелких заполнителях |
16. |
Бетоны, у которых пространство между зернами крупного и мелкого или только мелкого заполнителя заполнено затвердевшим вяжущим и порами вовлеченного газа или воздуха, в том числе образующихся за счет применения добавок, регулирующих пористость в объеме не более 7 % |
18. Бетоны крупнопористые |
Бетоны, у которых пространство между зернами крупного и мелкого заполнителя неполностью заполнено или совсем не заполнено мелкими заполнителями и затвердевшими вяжущими, поризованными добавками, регулирующих пористость в объеме не более 7 % |
19. Бетоны ячеистые |
Бетоны, у которых основную часть объема составляют равномерно распределенные поры в виде ячеек, полученных с помощью газо- или пенообразователей |
20. |
Бетоны плотные на цементном вяжущем и плотных крупных и мелких заполнителях |
21. Бетоны легкие |
Бетоны на цементном вяжущем, пористом крупном и пористом или плотном мелком заполнителе |
22. Бетоны силикатные |
Бетоны на известковых вяжущих автоклавного и неавтоклавного твердения |
23. Марка бетона |
Одно из нормируемых значений унифицированного ряда данного показателя качества бетона, принимаемого по его среднему значению |
24. Класс бетона |
Одно из нормируемых значений унифицированного ряда данного показателя качества бетона, принимаемого с гарантированной обеспеченностью |
25. |
Время, в течение которого должно быть обеспечено достижение бетоном заданных требований по маркам, классам или по другим показателям, которое устанавливается в нормативно-технической документации на бетонные или железобетонные изделия или в рабочих чертежах бетонных и железобетонных монолитных сооружений |
Справочное
НАИМЕНОВАНИЯ ОСНОВНЫХ ВИДОВ БЕТОНОВ
1. Конструкционные бетоны
1.1. Бетоны конструкционные на цементных вяжущих и плотных заполнителях, плотной структуры.
Сокращенное наименование: бетоны конструкционные тяжелые.
Примеры уточненных наименований: бетон тяжелый на щебне из доменного шлака.
1.2. Бетоны конструкционные
на цементном вяжущем и плотных заполнителях, крупнопористой структуры.
1.3. Бетоны конструкционные на цементных вяжущих и пористых заполнителях.
Сокращенное наименование: бетоны конструкционные легкие.
Примеры уточненных наименований.
бетон легкий плотной структуры;
бетон легкий поризованной структуры,
бетон легкий крупнопористой структуры;
бетон легкий на керамзитовом гравии (керамзитобетон).
1.4. Бетоны конструкционные на известковом вяжущем плотной структуры.
Сокращенное наименование: бетон силикатный.
Пример уточненного наименования, бетон конструкционный силикатный на известковом вяжущем.
1.5. Бетоны конструкционные на цементном, шлаковом или известковом вяжущем, ячеистой структуры.
Сокращенное наименование: бетон конструкционный ячеистый.
Пример уточненного наименования: бетон конструкционный ячеистый силикатный.
1.6 Бетоны конструкционные
на шлаковом вяжущем.
Пример уточненного наименования: бетон конструкционный на шлакощелочном вяжущем и плотных заполнителях.
1.7. Бетоны конструкционные на гипсовом вяжущем.
Пример уточненного наименования: бетон конструкционный на гипсовом вяжущем (гипсобетон).
1.8. Бетоны конструкционные на специальных вяжущих.
2. Бетоны жаростойкие
Примеры уточненных наименований:
бетон жаростойкий тяжелый;
бетон жаростойкий легкий;
бетон жаростойкий на жидком стекле и бое глиняного кирпича;
бетон жаростойкий на глиноземистом цементе и шамоте.
3. Бетоны теплоизоляционные
Примеры уточненных наименований:
бетон теплоизоляционный легкий поризованной структуры;
бетон теплоизоляционный ячеистый на цементом вяжущем;
бетон теплоизоляционный ячеистый на известково-кремнеземистом вяжущем (теплоизоляционный газо- или пеносиликат).
4. Бетоны радиационно-защитные
Примеры уточненного наименования: бетон радиационно-защитный на цементном вяжущем и чугунной дроби.
5. Бетоны химически стойкие
Пример уточненного наименования: бетон химически стойкий на полимерном связующем и специальных заполнителях.
6. Бетоны декоративные
Пример уточненного наименования: бетон декоративный тяжелый.
7. Бетоны напрягающие
Примеры уточненных наименований: бетон напрягающий тяжелый;
бетон напрягающий легкий;
бетон напрягающий на шлаковых заполнителях.
Справочное
Зависимость между классом бетона по прочности и его средней прочностью в контролируемой партии бетона
где В — класс бетона по прочности, МПа;
— средняя прочность бетона, МПа, которую следует обеспечить при производстве конструкций
v — коэффициент вариации прочности бетона;
t — коэффициент,
характеризующий принятую при проектировании обеспеченность класса бетона.
Основные методы определения прочности тяжелого бетона на сжатие в сборных и монолитных бетонных и железобетонных конструкциях и изделиях
Основные методы определения прочности тяжелого бетона на сжатие в сборных и монолитных бетонных и железобетонных конструкциях и изделияхРассмотрим некоторые основные методы и приборы определения прочности бетона в конструкциях, которыми пользуются на практике. Определение прочности механическими методами неразрушающего контроля осуществляется согласно ГОСТ 22690-88 «Бетоны. Определение прочности механическими методами неразрушающего контроля», определения прочности ультразвуковым методом неразрушающего контроля осуществляется по ГОСТ 17624-87 «Бетоны. Ультразвуковой метод определения прочности», определение прочности по бетонным образцам, выбуренным или выпиленным из конструкций, осуществляется по ГОСТ 28570-90 «Бетоны. Методы определения прочности по образцам, отобранным из конструкций».
Неразрушающие методы определения прочности на сжатие бетонных конструкций основаны на косвенных характеристиках показаний приборов, основанных на методах упругого отскока, ударного импульса, пластической деформации,отрыва, скалывания ребра и отрыва со скалыванием, скорости прохождения ультразвука. Определение прочности на сжатия по образцам, отобранным из конструкций, подразумевает испытание их на прессе.
Для определения класса и марки бетона в зависимости от прочности сжатия или растяжения, можно использовать табл.6, приложения 1, ГОСТ 26633-91 «Бетоны тяжелые и мелкозернистые»
СООТНОШЕНИЕ МЕЖДУ КЛАССАМИ БЕТОНА ПО ПРОЧНОСТИ НА СЖАТИЕ И РАСТЯЖЕНИЕ И МАРКАМИТаблица 6
Класс бетона по прочности
Средняя прочность бетона ()*, кгс/см2
Ближайшая марка бетона по прочности М
Отклонение ближайшей марки бетона от средней прочности класса, %,
Сжатие
В3,5
45,8
M50
+9,2
В5
65,5
M75
+14,5
В7,5
98,2
M100
+1,8
В10
131,0
M150
+14,5
B12,5
163,7
M150
-8,4
B15
196,5
M200
+1,8
В20
261,9
M250
-4,5
В22,5
294,7
M300
+1,8
В25
327,4
M350
+6,9
В27,5
360,2
M350
-2,8
В30
392,9
M400
+1,8
В35
458,4
M450
-1,8
В40
523,9
М550
+5,0
В45
589,4
M600
+1,8
B50
654,8
M700
+6,9
В55
720,3
M700
-2,8
В60
785,8
M800
+1,8
В65
851,3
M900
+5,7
В70
916,8
M900
-1,8
В75
982,3
М1000
+1,8
В80
1047,7
M1000
-4,6
____________
• Средняя прочность бетона R рассчитана при коэффициенте вариации V, равном 13,5 %, и обеспеченности- 95 % для всех видов бетона, а для массивных гидротехнических конструкций- при коэффициенте вариации V, равном 17 %, и обеспеченности- 90%.
Методы и приборы неразрушающего контроля
Для определения прочности бетона на сжатие данные показаний необходимо преобразовывать с помощью предварительно установленных градуировочных зависимостей между прочностью бетона и косвенной характеристикой прочности (в виде графика, таблицы или формулы), по методикам, указанным в ГОСТ 22690-88 и по прилагаемым графикам градуировочных зависимостей к приборам, установленным на заводе-изготовителей прибора.
Испытание прочности приборами неразрушающего контроля выполняют, непосредственно, в местах расположения конструкций, однако, также можно выполнять испытание бетона проб из конструкций. Испытание бетона в пробах рекомендуется для определения его прочности в труднодоступных зонах конструкций и в конструкциях, находящихся при отрицательной температуре. Пробу вмоноличивают в раствор, прочность которого на день испытания должна быть не менее половины прочности бетона пробы (для предотвращения разрушения пробы при испытании). Вмоноличивание проб в раствор удобно производить с использованием стандартных форм, для изготовления бетонных контрольных образцов по ГОСТ 10180-90. Расположение проб после распалубки представлено на рис.1.
Рис.1. 1 — проба бетона; 2 — наиболее удобная для испытания сторона пробы 3 — раствор, в котором закреплена проба
Обычно приборы поставляются с графиками градуировочной зависимости или с базовыми настройками для тяжелого бетона средних марок. Для обследования конструкций допускается применять методы упругого отскока, ударного импульса или пластической деформации, используя градуировочную зависимость, установленную для бетона, отличающегося от испытываемого (по составу, возрасту, условиям твердения, влажности), с уточнением ее в соответствии с методикой, приведенной в приложении 9 (ГОСТ 22690-88). Для ультразвуковых приборов требуется градуировка и корректировка согласно ГОСТ 17624, ГОСТ 24332 и методических рекомендаций МДС 62-2.01 ГУП «НИИЖБ» по контролю прочности бетона монолитных конструкций ультразвуковым методом поверхностного прозвучивания.
Согласно ГОСТ 22690-88 п. 4. 4. для методов неразрушающего контроля число испытаний на одном участке, расстояние между местами испытаний на участке и от края конструкции, толщина конструкции на участке испытания должны быть не меньше значений, приведенных в табл. 3.
Таблица 3
Наименование метода
Число испытаний на участке
Расстояние между местами испытаний, мм
Расстояние от края конструкции до места испытаний, мм
Толщина конструкции
Упругий отскок
5
30
50
100
Ударный импульс
10
15
50
50
Пластическая деформация
5
30
50
70
Скалывание ребра
2
200
—
170
Отрыв
1
2 диаметра диска
50
50
Отрыв со скалыванием
1
5 глубин вырыва
150
Удвоенная глубина установки анкера
Метод упругого отскока
При испытании методом упругого отскока, расстояние, от мест проведения испытания до арматуры, должно быть, не менее 50 мм.
Испытание проводят в следующей последовательности:
- прибор располагают так, чтобы усилие прикладывалось, перпендикулярно к испытываемой поверхности, в соответствии с инструкцией по эксплуатации прибора;
- положение прибора, при испытании конструкции относительно горизонтали, рекомендуется принимать таким же, как при испытании образцов для установления градуировочной зависимости; при другом положении, необходимо вносить поправку на показания в соответствии с инструкцией по эксплуатации прибора;
- фиксируют значение косвенной характеристики, в соответствии с инструкцией по эксплуатации прибора;
- вычисляют среднее значение косвенной характеристики на участке конструкции.
Определение прочности бетона прибором «Склерометр – ОМШ1»
Склерометр предназначен для определения прочности бетона и раствора методом упругого отскока по ГОСТ 22690-88. Пределы измерений для данного метода- от 5, до 50 МПа (для марок бетона от М50 до М500)
Прибор представляет собой цилиндрический корпус со шкалой, в котором размещены ударный механизм с пружинами и стрелка – индикатор. Испытания проводят путем нажатия приставленного к бетону склерометра и после удара бойка и величине его отскока, зафиксированного стрелкой-индикатором по графику, определяют прочность бетона(раствора). Продолжительность одного испытания- 20 сек.
К склерометру прилагается график, определяющий зависимость между твердостью при ударе и прочностью бетона. График, построен путем выполнения большой серии испытаний на кубиках, причем каждый кубик раздавливался в прессе непосредственно, после испытания склерометром (до ± 32%).
Отрыв со скалыванием
При испытании, методом отрыва, участки должны располагаться в зоне наименьших напряжений, вызываемых эксплуатационной нагрузкой или усилием обжатия, предварительно напряженной арматуры.
Испытания проводят в следующей последовательности:
- если анкерное устройство не было установлено до бетонирования, то в бетоне сверлят или пробивают шпур, размер которого выбирают в соответствии с инструкцией по эксплуатации прибора в зависимости от типа анкерного устройства;
- в шпуре закрепляют анкерное устройство на глубину, предусмотренную инструкцией по эксплуатации прибора, в зависимости от типа анкерного устройства;
- прибор соединяют с анкерным устройством;
- нагрузку увеличивают, со скоростью 1,5 — 3,0 кН/с;
- фиксируют показание силоизмерителя прибора и глубину вырыва с точностью не менее 1 мм.
Если наибольший и наименьший размеры вырванной части бетона от анкерного устройства до границ разрушения по поверхности конструкции отличаются более чем в два раза, а также если глубина вырыва отличается от глубины заделки анкерных устройств более чем на 5 %, то результаты испытаний допускается учитывать только для ориентировочной оценки прочности бетона.
Еслис прибором применяются анкерные устройства в соответствии с приложением 2 ГОСТ 22690-88, то допускается использовать следующую градуировочную зависимость:
ПРИЛОЖЕНИЕ 5
Рекомендуемое
ГРАДУИРОВОЧНАЯ ЗАВИСИМОСТЬ ДЛЯ МЕТОДА ОТРЫВА СО СКАЛЫВАНИЕМ
При использовании анкерных устройств, приведенных в приложении 2, прочность бетона R, МПа можно вычислять по градуировочной зависимости по формуле
(1)
где m1 — коэффициент, учитывающий максимальный размер крупного заполнителя в зоне вырыва и принимаемый равным 1 при крупности менее 50 мм и 1,1 при крупности 50 мм и более;
m2 — коэффициент пропорциональности для перехода от усилия вырыва, кН, к прочности бетона, МПа;
Р — усилие вырыва анкерного устройства, кН.
При испытании тяжелого бетона прочностью 10 МПа и более и керамзитобетона прочностью от 5 до 40 МПа значения коэффициента пропорциональности m2 принимают по табл. 9.
Таблица 9
Условие твердения бетона
Тип анкерного устройства
Предполагаемая прочность бетона, МПа
Глубина заделки анкерного устройства, мм
Значение коэффициента m2 для бетона
тяжелого
легкого
Естественное
I
? 50
48
1,1
1,2
> 50
35
2,4
—
II
? 50
48
0,9
1,0
> 50
30
2,5
—
III
? 50
35
1,5
—
Тепловая обработка
I
? 50
48
1,3
1,2
> 50
35
2,6
—
II
? 50
48
1,1
1,0
> 50
30
2,7
—
III
? 50
35
1,8
—
Прибор для определения прочности бетона «ПИБ»
На испытываемой конструкции выбирают ровный участок размером 0,2×0,2 м и выполняют пробивку отверстия, глубиной 55×10-3 м перпендикулярно испытываемой поверхности. Допускается отклонение оси отверстия от нормали испытываемой поверхности до 1 градуса. Пробивку отверстия выполняют шлямбуром с оправкой или механизированным (электромеханическим) инструментом, обеспечивающим выполнение заданных требований.
В подготовленное отверстие устанавливается анкерное устройство, состоящее из конуса и 3-х сегментов, и накручивают гайку-тягу с усилием, предотвращающим проскальзывание анкерного устройства при испытании.
Опору прибора закручивают до упора в рабочий цилиндр. Винт поршневого насоса выкручивают в крайнее верхнее положение. Присоединяют прибор к гайке-тяге и выкручивают опору 4 до упора в поверхность испытываемого материала.
После проведения подготовительных операций производят вырыв анкерного устройства (тип 1 или 2). Вращают ручку поршневого насоса со скоростью, обеспечивающей приложение нагрузки равной 1,5 … ЗкН/с.
В момент разрушения испытываемого материала визуально устанавливают максимальное давление по манометру. Снятие показаний по манометру следует выполнять с точностью до 2,5 кгс/см2.
При проведении испытаний необходимо следить за тем, чтобы не происходило проскальзывания анкерного устройства. Результаты испытаний не учитываются, если произошло проскальзывание анкерного устройства более 5×10-3 м. Повторное испытание данного отверстия не допускается из-за возможности получения заниженных результатов. После вырыва анкерного устройства необходимо уточнить глубину разрушения бетона, используя для ее определения две линейки, одну из которых устанавливают ребром на поверхность бетона в зоне испытаний, другой — замеряют глубину.
Ультразвуковой метод
Ультразвуковой метод основан на связи между скоростью распространения ультразвуковых колебаний в бетоне и его прочностью. Прочность бетона в конструкциях определяют по экспериментально установленным градуировочным зависимостям «скорость распространения ультразвука — прочность бетона» или «время распространения ультразвука — прочность бетона» в зависимости от способа прозвучивания.
Ультразвуковые измерения в бетоне проводят способами сквозного или поверхностного прозвучивания. Сборные линейные конструкции (балки, ригели, колонны и др.) испытывают, как правило, способом сквозного прозвучивания в поперечном направлении. Изделия, конструктивные особенности которых затрудняют осуществление сквозного прозвучивания, а также плоские конструкции (плоские, ребристые и многопустотные панели перекрытия, стеновые панели и т. д.) испытывают способом поверхностного прозвучивания. При этом база прозвучивания при измерениях на конструкциях должна быть такой же, как на образцах при установлении градуировочной зависимости.
Между бетоном и рабочими поверхностями ультразвуковых преобразователей должен быть обеспечен надежный акустический контакт, для чего применяют вязкие контактные материалы (солидол по ГОСТ 4366, технический вазелин по ГОСТ 5774 и др.).
Градуировочную зависимость «скорость — прочность» устанавливают при испытании конструкций способом сквозного прозвучивания. Градуировочную зависимость «время — прочность» устанавливают при испытании конструкций способом поверхностного прозвучивания.
Допускается при испытании конструкций способом поверхностного прозвучивания использовать градуировочную зависимость «скорость — прочность» с учетом коэффициента перехода, определяемого в соответствии с приложением 3.
Измерение времени распространения ультразвука в бетоне конструкций следует проводить в направлении, перпендикулярном уплотнению бетона. Расстояние от края конструкции до места установки ультразвуковых преобразователей должно быть не менее 30 мм. Измерение времени распространения ультразвука в бетоне конструкций следует проводить в направлении, перпендикулярном направлению рабочей арматуры. Концентрация арматуры вдоль выбранной линии прозвучивания не должна превышать 5 %. Допускается прозвучивание вдоль линии, расположенной параллельно рабочей арматуре, если расстояние от этой линии до арматуры составляет не менее 0,6 длины базы.
Пульсар 1.2.
Рис. 2. Внешний вид прибора
Пульсар-1.2: 1 — вход приемника;
2 — выход излучателя
Прибор состоит из электронного блока (см. рис. 3.2) и ультразвуковых преобразователей — раздельных или объединенных в датчик поверхностного прозвучивания. На лицевой панели электронного блока расположены: 12-ти клавишная клавиатура и графический дисплей. В верхней торцевой части корпуса установлены разъёмы для подключения датчика поверхностного прозвучивания или отдельных УЗ преобразователей для сквозного прозвучивания. На правой торцевой части прибора расположен разъем USB интерфейса. Доступ к аккумуляторам осуществляется через крышку батарейного отсека на нижней стенке корпуса.
Работа прибора основана на измерении времени прохождения ультразвукового импульса в материале изделия от излучателя к приемнику. Скорость ультразвука вычисляется делением расстояния между излучателем и приемником на измеренное время. Для повышения достоверности в каждом измерительном цикле автоматически выполняется 6 измерений и результат формируется путем их статистической обработки с отбраковкой выбросов. Оператор выполняет серию измерений (от 1 до 10 измерений по его выбору), которая также подвергается математической обработке с определением среднего значения, коэффициента вариации, коэффициента неоднородности и с отбраковкой выбросов.
Скорость распространения ультразвуковой волны в материале зависит от его плотности и упругости, от наличия дефектов (трещин и пустот), определяющих прочность и качество. Следовательно, прозвучивая элементы изделий, конструкций и сооружений можно получать информацию о:
- прочности и однородности;
- модуле упругости и плотности;
- наличии дефектов и их локализации.
- форме А-сигнала
Возможны варианты прозвучивания со смазкой и сухим контактом (протекторы, конусные насадки), см. рис. 3.1.
Рис. 3. Варианты прозвучивания
Прибор осуществляет запись и визуализацию принимаемых УЗК, имеет встроенные цифровые и аналоговые фильтры, улучшающие соотношение «сигнал-помеха». Режим осциллографа позволяет просматривать сигналы на дисплее (в задаваемом масштабах времени и усиления), вручную устанавливать курсор в положение контрольной метки первого вступления. Пользователь имеет возможность вручную изменять усиление измерительного тракта и смещать ось времени для просмотра и анализа сигналов первого вступления и огибающей.
Оформление результатов для методов определения прочности неразрушающего контроля
Результаты испытаний прочности бетона заносят в журнал, в котором должно быть указано:
- наименование конструкции, номер партии;
- вид контролируемой прочности и ее требуемое значение;
- вид бетона;
- наименование неразрушающего метода, тип прибора и его заводской номер;
- среднее значение косвенной характеристики прочности и соответствующее значение прочности бетона;
- сведения об использовании поправочных коэффициентов;
- результаты оценки прочности бетона;
- фамилия и подпись лица, проводившего испытание, дата испытания.
Для ультразвукового метода определения прочности нужно воспользоваться формой журнала, установленной в приложениях №8-9, ГОСТ 17624-87 «Бетоны. Ультразвуковой метод определения прочности»
Определение и испытание прочности бетона на сжатие
Испытание бетона
НаверхВ лаборатории АБЗ Линт можно заказать большой перечень работ, связанных с испытанием бетонной смеси и бетона. Мы определяем марку бетона, прочность бетона на сжатие, влажность бетона и осуществляем другие испытания. Выполняем выезд на объект к заказчику для взятия образцов, обработку испытаний с составлением протокола.
Испытание образцов бетона на прочность и сжатие | Стоимость работ вкл. НДС (20%) руб |
---|---|
Определение прочности бетона на сжатие (серия из 6-ти образцов-кубов размером 10х10 см) по ГОСТ 10180-90, 1 серия | 2230 |
Определение прочности бетона на сжатие (серия из 6-ти образцов-кубов размером 15х15 см) по ГОСТ 10180-90, 1 серия | 2650 |
Определение прочности раствора на сжатие (серия из 6-ти образцов-кубов размером 7х7 см) по ГОСТ 10180-90, 1 серия | 1600 |
Определение водонепроницаемости бетона на образцах по ГОСТ 12730.0-78, ГОСТ 12730.5-84 1 образец | 530 |
Определение коэффициента вариации по ГОСТ 10180-90, 1экз | 5300 |
Удобоукладываемость бетонной смеси по ГОСТ 7473-2010, ГОСТ 10181-2000 , 1 партия | 1280 |
Обработка результатов испытаний с составлением протоколов, 1 экз | 3300 |
Определение прочности бетона в изделиях и конструкциях методом упругого отскока ГОСТ 22690, 1 участок | 450 |
Определение прочности бетона в изделиях и конструкциях методом ультразвука ГОСТ 17624–87 1 точка | 240 |
Определение прочности бетона в изделиях и конструкциях методом отрыва со скалыванием ГОСТ 22690, 1 точка | 500 |
Выезд на объект за образцами-кубами или на испытания по вызову Заказчика транспортом Исполнителя в пределах Пушкинского и Мытищинского районов, 1 выезд — до 30 км — до 50 км | 3200 |
Компания АБЗ Линт изготавливает высококачественные смеси и предлагает специальные лабораторные услуги. Они востребованы заказчиками, которым необходимо произвести испытания бетона на прочность в изделиях и конструкциях. Ряд лабораторных работ позволяет определить не только прочностные показатели, но и показатели влажности, объемного веса, и многое другое.
Как производится определение прочности бетона.
Существует несколько видов определения прочности. Они могут производиться различными методами, которые можно разделить на три категории:
- Механические.
- Ультразвуковые.
- Лабораторные испытания образцов (частей бетонных изделий или конструкций).
При проверках лаборанты используют различные устройства и приборы. Все испытания бетона проводятся в соответствии с ГОСТ. При необходимости осуществляется выезд на объект заказчика с целью взятия образцов из изделий или конструкций, определения их прочностных качеств на месте.
Мы обрабатываем результаты и составляем протокол. Услуги по определению прочности бетона позволяют испытывать конструкции и изделия, изготовленные из любой марки и сорта бетонной смеси.
Определение прочности бетона при обследовании зданий и сооружений
А. В. Улыбин, к. т. н.; С. Д. Федотов, Д. С. Тарасова (ПНИПКУ «Венчур», Санкт-Петербург)
В предлагаемой статье рассмотрены основные методы неразрушающего контроля прочности бетона, применяемые при обследовании конструкций зданий и сооружений. Приведены результаты экспериментов по сопоставлению данных, получаемых неразрушающими методами контроля и испытанием образцов. Показывается преимущество метода отрыва со скалыванием перед другими методами контроля прочности. Описываются мероприятия, без выполнения которых применение косвенных неразрушающих методов контроля недопустимо.
Прочность бетона на сжатие является одним из наиболее часто контролируемых параметров при строительстве и обследовании железобетонных конструкций. Имеется большое число методов контроля, применяемых на практике. Более достоверным, сточки зрения авторов, является определение прочности не по контрольным образцам (ГОСТ 10180–90), изготовляемым из бетонной смеси, а по испытанию бетона конструкции после набора им проектной прочности. Метод испытания контрольных образцов позволяет оценить качество бетонной смеси, но не прочность бетона конструкции. Это вызвано тем, что невозможно обеспечить идентичные условия набора прочности (вибрирование, прогрев и др.) для бетона в конструкции и бетонных кубиков образцов.
Методы контроля по классификации ГОСТ 18105–2010 («Бетоны. Правила контроля и оценки прочности») разделены на три группы:
- Разрушающие;
- Прямые неразрушающие;
- Косвенные неразрушающие.
Таблица 1. Характеристики методов неразрушающего контроля прочности бетона.
№ | Наименование метода | Диапазон применения*, МПа | Погрешность измерения** |
1 | Пластической деформации | 5 – 50 | ± 30 – 40% |
2 | Упругого отскока | 5 – 50 | ± 50% |
3 | Ударного импульса | 10 – 70 | ± 50% |
4 | Отрыва | 5 – 60 | Нет данных |
5 | Отрыва со скалыванием | 5 – 100 | Нет данных |
6 | Скалывания ребра | 5 – 70 | Нет данных |
7 | Ультразвуковой | 5 – 40 | ± 30 – 50% |
*По требованиям ГОСТ 17624–87 и ГОСТ 22690–88;
**По данным источника без построения частной градуировочной зависимости
К методам первой группы относится упомянутый метод контрольных образцов, а также метод определения прочности путем испытания образцов, отобранных из конструкций. Последний является базовым и считается наиболее точным и достоверным. Однако при обследовании к нему при бегают довольно редко. Основными причинами этого являются существенное нарушение целостности конструкций и высокая стоимость исследований.
Измерители прочности бетона на нашем сайте.
В основном применяются методы определения прочности бетона неразрушающим контролем. При этом большая часть работ выполняется косвенными методами. Среди них наиболее распространенными на сегодняшний день являются ультразвуковой метод по ГОСТ 17624–87, методы ударного импульса и упругого отскока по ГОСТ 22690–88. Однако при использовании указанных методов редко соблюдаются требования стандартов по построению частных градуировочных зависимостей. Некоторые исполнители не знают этих требований.
Другие знают, но не понимают, насколько велика ошибка результатов измерений при использовании зависимостей, заложенных или прилагаемых к прибору, вместо зависимости, построенной на конкретном исследуемом бетоне. Есть «специалисты», которые знают об указанных требованиях норм, но пренебрегают ими, ориентируясь на финансовую выгоду и неосведомленность заказчика в данном вопросе.
Про факторы, влияющие на ошибку измерения прочности без построения частных градуировочных зависимостей, написано много работ. В табл.1 представлены данные по максимальной погрешности измерений различными методами, приведенные в монографии по неразрушающему контролю бетона.
В дополнение к обозначенной проблеме использования несоответствующих («ложных») зависимостей обозначим еще одну, возникающую при обследовании. Согласно требованиям СП 13-102-2003 обеспечение выборки измерений (параллельных испытаний бетона косвенным и прямым методом) на более чем 30 участках является необходимым, но не достаточным для построения и использования градуировочной зависимости. Необходимо, чтобы полученная парным корреляционно регрессионным анализом зависимость имела высокий коэффициент корреляции (более 0,7) и низкое СКО (менее 15% от средней прочности). Чтобы данное условие выполнялось, точность измерений обоих контролируемых параметров (например, скорость ультразвуковых волн и прочность бетона) должна быть достаточно высокой, а прочность бетона, по которому строится зависимость, должна изменяться в широком диапазоне.
При обследовании конструкций указанные условия выполняются редко. Во-первых, даже базовый метод испытания образцов нередко сопровождается высокой погрешностью. Во-вторых, за счет неоднородности бетона и других факторов [4] прочность в поверхностном слое (исследуемая косвенным методом) может не соответствовать прочности того же участка на некоторой глубине (при использовании прямых методов). И наконец, при нормальном качестве бетонирования и соответствии класса бетона проектному в пределах одного объекта редко можно встретить однотипные конструкции с прочностью, изменяющейся в широком диапазоне (например, от В20 до В60). Таким образом, зависимость приходится строить по выборке измерений с малым изменением исследуемого параметра.
В качестве наглядного примера вышеуказанной проблемы рассмотрим градуировочную зависимость, представленную на рис. 1. Линейная регрессионная зависимость построена по результатам ультразвуковых измерений и испытаний на прессе образцов бетона. Несмотря на большой разброс результатов измерений, зависимость имеет коэффициент корреляции 0,72, что допустимо по требованиям СП 13-102-2003. При аппроксимации функциями, отличными от линейной (степенной, логарифмической и пр.) коэффициент корреляции был менее указанного. Если бы диапазон исследуемой прочности бетона был меньше, например от 30 до 40 МПа (область, выделенная красным цветом), то совокупность результатов измерений превратилась бы в «облако», представленное в правой части рис. 1. Данное облако точек характеризуется отсутствием связи между измеряемым и искомым параметрами, что подтверждается максимальным коэффициентом корреляции 0,36. Иными словами, градуировочную зависимость здесь не построить.
РИС. 1. Зависимость между прочностью бетона и скоростью ультразвуковых волн
Также необходимо отметить, что на рядовых объектах количество участков измерения прочности для построения градуировочной зависимости сопоставимо с общим количеством измеряемых участков. В данном случае прочность бетона может быть определена по результатам только прямых измерений, а в градуировочной зависимости и использовании косвенных методов контроля уже не будет смысла.
Таким образом, без нарушения требований действующих норм для определения прочности бетона при обследовании в любом случае необходимо в том или ином объеме использовать прямые неразрушающие либо разрушающие методы контроля. Учитывая это, а также обозначенные выше проблемы, далее более подробно рас смотрим прямые методы контроля.
К данной группе по ГОСТ 22690–88 относится три метода:
- Метод отрыва.
- Метод отрыва со скалыванием.
- Метод скалывания ребра.
Метод отрыва
Метод отрыва основан на измерении максимального усилия, необходимого для отрыва фрагмента бетонной конструкции. Отрывающая нагрузка прилагается к ровной поверхности испытываемой конструкции за счет приклеивания стального диска (рис. 2), имеющего тягу для соединения с прибором. Для приклеивания могут использоваться различные клеи на эпоксидной основе. В ГОСТ 22690–88 рекомендуются клеи ЭД20 и ЭД16 с цементным наполнителем.
На сегодняшний день могут применяться современные двухкомпонентные клеи, производство которых хорошо налажено (POXIPOL, «Контакт», «Момент» И др.). В отечественной литературе по испытанию бетона методика испытания предполагает приклеивание диска к участку испытания без дополнительных мероприятий по ограничению зоны отрыва. В таких условиях площадь отрыва является непостоянной и должна определяться после каждого испытания. В зарубежной практике перед испытанием участок отрыва ограничивается бороздой, создаваемой кольцевыми сверлами (коронками). В данном случае площадь отрыва постоянна и известна, что увеличивает точность измерений.
После отрыва фрагмента и определения усилия определяется прочность бетона на растяжение (R(bt)) , по которой с помощью пересчета по эмпирической зависимости может быть определена прочность на сжатие (R). Для перевода можно воспользоваться выражением, указанным в пособии:
Для метода отрыва могут применяться различные приборы, используемые и для метода отрыва со скалыванием, такие как ПОС-50МГ4, ОНИКСОС, ПИБ, DYNA (рис. 2), а также старые аналоги: ГПНВ-5, ГПНС-5. Для проведения испытания необходимо наличие захватного устройства, соответствующего тяге, расположенной на диске.
Рис. 2. Прибор для метода отрыва с диском для приклеивания к бетону
В России метод отрыва не нашел широкого распространения. Об этом свидетельствует и отсутствие серийно выпускаемых приборов, приспособленных для крепления к дискам, а также самих дисков. В нормативных документах отсутствует зависимость для перехода от усилия вырыва к прочности на сжатие. В новом ГОСТ 18105–2010, а также предшествующем ГОСТ Р 53231–2008 метод отрыва не включен в перечень прямых методов неразрушающего контроля и вообще не упоминается. Причиной этому, по всей видимости, является ограниченный температурный диапазон применения метода, что связано с продолжительностью твердения и (или) невозможностью использования эпоксидных клеев при низкой температуре воздуха. Большая часть России расположена в более холодных климатических зонах, чем страны Европы, поэтому данный метод, широко при меняемый в европейских странах, в нашей стране не используется. Другим отрицательным фактором является необходимость сверления борозды, что дополнительно снижает производительность контроля.
Метод отрыва со скалыванием
Рис. 3. Испытание бетона методом отрыва со скалыванием
Данный метод имеет много общего с описанным выше методом отрыва. Основным отличием является способ крепления к бетону. Для приложения отрывающего усилия используются лепестковые анкеры различных размеров. При обследовании конструкций анкеры закладываются в шпур, пробуренный на участке измерения. Так же, как и при методе отрыва, измеряется разрушающее усилие (Р). Переход к прочности бетона на сжатие осуществляется по указанной в ГОСТ 22690 зависимости: R=m1•m2•P, где m1 — коэффициент, учитывающий максимальный размер крупного заполнителя, m2 — коэффициент перехода к прочности на сжатие, зависящий от вида бетона и условий твердения.
В нашей стране данный метод нашел, пожалуй, самое широкое распространение благодаря своей универсальности (табл.1), относительной простоте крепления к бетону, возможности испытания практически налюбом участке конструкции. Основными ограничениями для его применения являются густое армирование бетона и толщина испытываемой конструкции, которая должна быть больше, чем удвоенная длина анкера. Для выполнения испытаний могут использоваться приборы, указанные выше.
Таблица 2. Сравнительные характеристики прямых методов неразрушающего контроля
Преимущества | Метод | ||
Отрыв | Отрыв со скалыванием | Скалывание ребра | |
Определение прочности бетонов классом более В60 | – | + | – |
Возможность установки на неровную поверхность бетона (неровности более 5 мм) | – | + | – |
Возможность установки на плоский участок конструкции (без наличия ребра) | + | + | – |
Отсутствие потребности в источнике электроснабжения для установки | +* | – | + |
Быстрое время установки | – | + | + |
Работа при низких температурах воздуха | – | + | + |
Наличие в современных стандартах | – | + | + |
*Без сверления борозды, ограничивающей участок отрыва.
Помимо более простого и быстрого крепления к бетону конструкции по сравнению с методом отрыва, не требуется обязательное наличие ровной поверхности. Главным условием является необходимость того, чтобы кривизна поверхности была достаточной для установки прибора на тягу анкера. В качестве примера на рис. 3 представлен прибор ПОС-МГ4, установленный на деструктированную поверхность устоя гидротехнического сооружения.
Метод скалывания ребра
Последним прямым методом неразрушающего контроля является модификация метода отрыва — метод скалывания ребра. Основное отличие заключается в том, что прочность бетона определяют по усилию (Р), необходимому для скалывания участка конструкции, расположенному на внешнем ребре. В нашей стране долгое время выпускались приборы типа ГПНС-4 и ПОС-МГ4 Скол, конструкция которых предполагала обязательное наличие двух рядом расположенных внешних углов конструкции.
Захваты прибора подобно струбцине крепились на испытываемый элемент, после чего через захватывающее устройство прилагалось усилие к одному из ребер конструкции. Таким образом, испытание можно было проводить только на линейных элементах (колонны, ригели) или в проемах на краях плоских элементов (стены, перекрытия). Несколько лет назад была разработана конструкция прибора, которая позволяет устанавливать его на испытываемый элемент с наличием только одного внешнего ребра. Закрепление осуществляется к одной из поверхностей испытываемого элемента при помощи анкера с дюбелем. Данное изобретение несколько расширило диапазон применения прибора, но одновременно с этим уничтожило основное преимущество метода скалывания, которое заключалось в отсутствии необходимости сверления и потребности в источнике электроэнергии.
Прочность бетона на сжатие при использовании метода скалывания ребра определяется по нормированной зависимости: R=0,058•m•(30P+P2),
где m — коэффициент, учитывающий крупность заполнителя.
Для наглядности сравнения характеристики прямых методов контроля представлены в табл. 2.
По данным, приведенным в таблице, видно, что наибольшим числом преимуществ характеризуется метод отрыва со скалыванием.
Однако, несмотря на возможность применения данного метода по указаниям норм без построения частной градуировочной зависимости, у многих специалистов возникает вопрос о точности получаемых результатов и соответствии их прочности бетона, определяемой методом испытания образцов. Для исследования этого вопроса, а также сопоставления результатов измерений, полученных прямым методом, с результатами измерений косвенными методами проведен эксперимент, опиcанный далее.
Результаты сравнения методов
В лаборатории «Обследование и испытание зданий и сооружений» ФГБОУ ВПО «СПБГПУ» были проведены исследования при использовании различных методов контроля. В качестве объекта исследования использован фрагмент бетонной стены, выпиленный алмазным инструментом. Габариты бетонного образца — 2,0×1,О х 0,3 м.
Армирование выполнено двумя сетками арматуры диаметром 16 мм, расположенной с шагом 100 мм с величиной защитного слоя 15–60 мм. В исследуемом образце применен тяжелый бетон на заполнителе из гранитного щебня фракции 20–40.
Для определения прочности бетона использован базовый разрушающий метод контроля. Из образца с помощью установки алмазного сверления выбурены 11 кернов различной длины диаметром 80 мм. Из кернов изготов лены 29 образцов — цилиндров, удовлетворяющих по своим размерам требованиям ГОСТ 28570–90 («Бетоны. Методы определения прочности по образцам, отобранным из конструкций»). По результатам испытания образцов на сжатие выявлено, что среднее значение прочности бетона составило 49,0 МПа. Распределение значений прочности подчиняется нормальному закону (рис. 4). При этом прочность исследуемого бетона имеет высокую неоднородность с коэффициентом вариации 15,6% и СКО равным 7,6 МПа.
Для неразрушающего контроля применены методы отрыва, отрыва со скалыванием, упругого отскока и ударного импульса. Метод скалывания ребра не применялся по причине близкого расположения арматуры к ребрам образца иневозможности выполнения испытаний. Ультразву ковой метод не использован, так как прочность бетона выше допустимого диапазона для применения данного метода (табл.1). Выполнение измере ний всеми методами производилось на грани образца, срезанной алмазным инструментом, что обеспечива ло идеальные условия с точки зрения ровности поверхности. Для определе ния прочности косвенными методами контроля использовались градуиро вочные зависимости, имеющиеся в паспортах приборов, или заложен ные в них.
На рис. 5. представлен процесс измерения методом отрыва. Результаты измерений всеми методами представлены в табл. 3.
Таблица 3. Результаты измерения прочности различными методами
№ п/п |
Метод контроля (прибор) | Количество измерений, n | Среднее значение прочности бетона, Rm, МПа | Коэффициент вариации, V, % |
1 | Испытание на сжатие в прессе (ПГМ-1000МГ4) | 29 | 49,0 | 15,6 |
2 | Метод отрыва со скалыванием (ПОС-50МГ4) | 6 | 51,1 | 4,8 |
3 | Метод отрыва (DYNA) | 3 | 49,5 | – |
4 | Метод ударного импульса (Silver Schmidt) |
30 | 68,4 | 7,8 |
5 | Метод ударного импульса (ИПС-МГ4) |
7 (105)* | 78,2 | 5,2 |
6 | Метод упругого отскока (Beton Condtrol) |
30 | 67,8 | 7,27 |
*Семь участков по 15 измерений на каждом.
По данным, представленным в таблице, можно сделать следующие выводы:
среднее значение прочности, полученной испытанием на сжатие и прямыми методами неразрушающего контроля, различается не более чем 5%;
по результатам шести испытаний методом отрыва со скалыванием разброс прочности характеризуется низким значением коэффициента вариации 4,8%;
результаты, полученные всеми косвенными методами контроля, завышают прочность на 40–60%. Одним из факторов, приведших к данному завышению, является карбонизация бетона, глубина которой на исследуемой поверхности образца составила 7 мм.
Выводы
1. Мнимая простота и высокая производительность косвенных методов неразрушающего контроля теряются при выполнении требований построения градуировочной зависимости и учете (устранении) влияния факторов, искажающих результат. Без выполнения этих условий данные методы при обследовании конструкций можно при менять только для качественной оценки прочности по принципу «больше — меньше».
2. Результаты измерений прочности базовым методом разрушающего контроля путем сжатия отбираемых образцов также могут сопровождаться боль шим разбросом, вызванным как неоднородностью бетона, так и другими факторами.
3. Учитывая повышенную трудоем кость разрушающего метода и под твержденную достоверность результа тов, получаемых прямыми методами неразрушающего контроля, при обсле довании рекомендуется при менять по следние.
4. Среди прямых методов неразру шающего контроля оптимальным по большинству параметров является ме тод отрыва со скалыванием.
Рис. 4. Распределение значений прочности по результатам испытаний на сжатие.
Рис. 5. Измерение прочности методом отрыва.
А. В. Улыбин, к. т. н.; С. Д. Федотов, Д. С. Тарасова (ПНИПКУ «Венчур», Санкт-Петербург), журнал «Мир строительства и недвижимости, №47, 2013 г.
Все публикации
Архив по годам: 2006; 2008; 2013; 2015; 2016; 2018; 2019; 2020;
определение морозостойкости, прочности, определение удобоукладываемости
- Определение удобоукладываемости бетонной смеси по ГОСТ 10181-2000
- Определение подвижности строительного раствора по ГОСТ 5802-86
- Определение температуры смеси по ГОСТ 10181-2000
- Определение прочности бетона по контрольным образцам по ГОСТ 10180-2012
- Определение прочности на сжатие строительного раствора по ГОСТ 5802-86
- Определение плотности бетона по ГОСТ 12730.
1-78
- Определение плотности строительного раствора по ГОСТ 5802-86
- Подбор состава обычного бетона (без определения морозостойкости и водонепроницаемости)
- Подбор состава строительного раствора
- Морозостойкость ГОСТ 10060-2012 (метод №3, ускоренный)
- Водонепроницаемость W2 — W12 (ГОСТ 12730.5-84 Приложение 4)
- Разработка технологических карт (технологическая карта на прогрев бетона, технологическая карта)
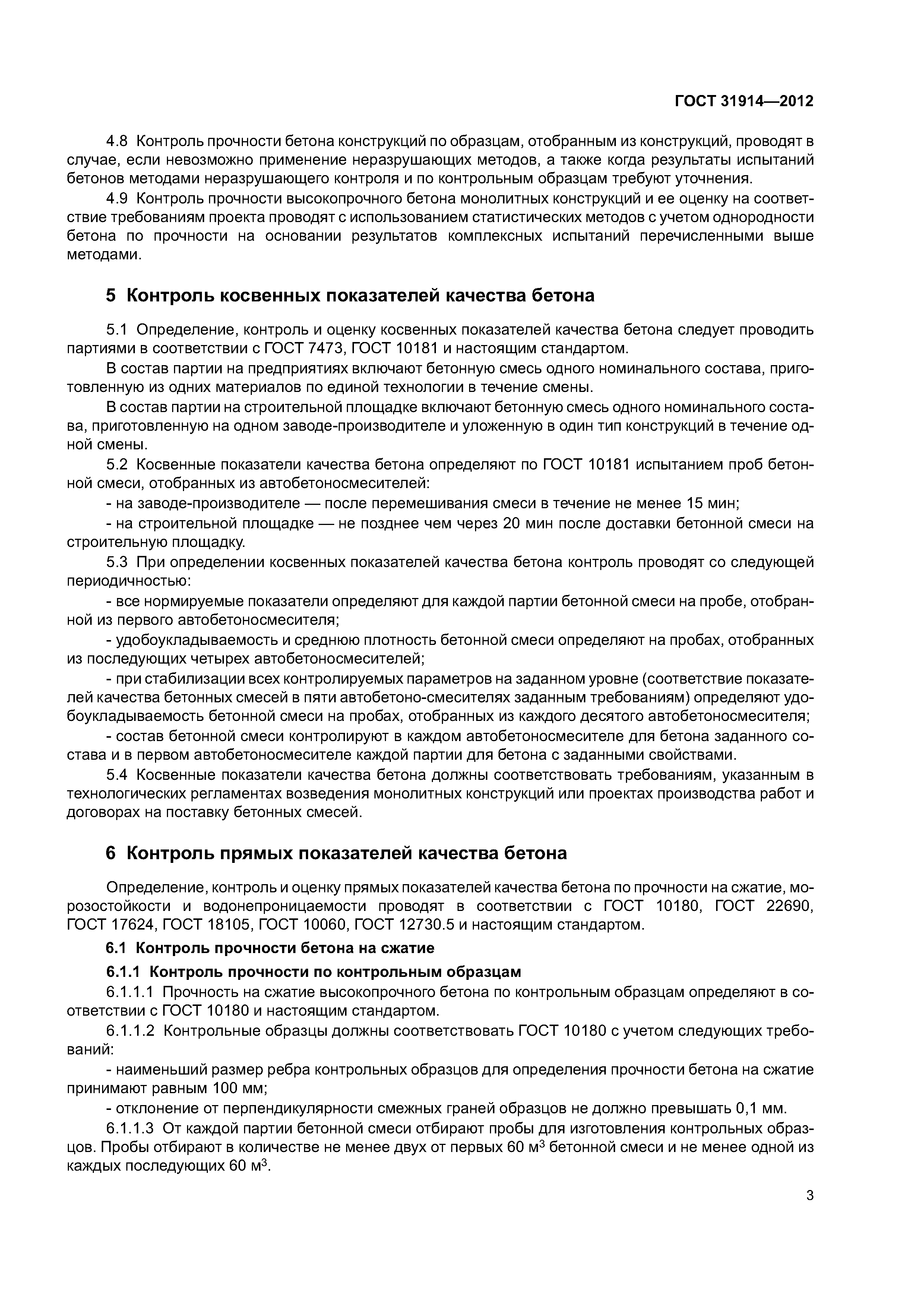
- Определение коэффициента уплотнения грунта
- Определение плотности грунта методом режущего кольца по ГОСТ 5180-84
- Определение влажности грунтов по ГОСТ 5180-84
- Определение влажности грунтов на границе текучести по ГОСТ 5180-84
- Определение влажности грунтов на границе текучести по ГОСТ 5180-84
- Определение коэффициента фильтрации грунтов по ГОСТ 25584-90
- Определение максимальной плотности грунтов по ГОСТ 22733-2002
- Определение гранулометрического состава по ГОСТ 12536-79
- Определение насыпной плотности грунта
- Определение температуры грунтов по ГОСТ 25358-2012
- Определение зернового состава и модуля крупности песка по ГОСТ 8735-88
- Определение зернового состава щебня по ГОСТ 8269.
0-97
- Определение содержания пылевидных и глинистых частиц по ГОСТ 8735-88
- Определение влажности песка по ГОСТ 8735-88
- Определение насыпной плотности песка по ГОСТ 8735-88
- Определение истинной плотности песка по ГОСТ 8735-88
- Определение насыпной плотности щебня по ГОСТ 8269.0-97
- Содержание в щебне зерен пластинчатой и игловатой формы щебня по ГОСТ 8269.0-97
- Содержание в щебне зерен слабых пород по ГОСТ 8269.0-97
- Определение марки по прочности (дробимость) по ГОСТ 8269.0-97

- Подбор состава жаропрочного бетона (карта подбора жаростойкого бетона)
- Остаточная прочность жаропрочного бетона по ГОСТ 20910-90
- Определение температуры грунтов по ГОСТ 25358-2012
- Определение остаточной прочность жаропрочного бетона по ГОСТ 20910-90
- Определение термостойкости жаропрочного бетона по ГОСТ 20910-90(определение количества теплосмен)
- Определение водонепроницаемости жаропрочного бетона по ГОСТ 12730.5-84
- Определение морозостойкости жаропрочного бетона по ГОСТ 26134-84
- Определение усадки жаропрочного бетона по ГОСТ 20910-90
- Определение активности цемента по ГОСТ 30744-20
- Определение активности цемента по ГОСТ 30744-2001
- Определение тонкости помола цемента по ГОСТ 30744-2001
- Определение сроков схватывания цемента по ГОСТ 30744-2001
- Определение нормальной густоты цементного теста по ГОСТ 30744-2001
- Определение прочности при сжатии и изгибе по ГОСТ 30744-2011
- Определение состава цементно-песчаной смеси
- Определение зернового состава смеси ПГС
- Определение насыпной плотности смеси

Бетон тяжелый: ГОСТ
Тяжелый бетон — это тип раствора, который используется в конструкции стального каркаса, в основном, для заливки фундамента большого здания. Свое название он получил благодаря входящим в его состав наполнителям. Эти наполнители самые прочные и надежные, поэтому их вес увеличивается. Отсюда и название — тяжелый бетон.
Как правило, состав бетона не меняется, будь он легкий или тяжелый. Можно менять только отдельные компоненты, которые задают тон раствору.Итак, в состав входят:
- Цемент — один из основных элементов смеси. Для изготовления тяжелого бетона добавляется цемент марки М200 или М300.
Чтобы раствор был максимально прочным, лучше всего добавить портландцемент.
- Вода. Обратите внимание, используйте только чистую воду, в ней не должно быть даже небольшой доли химических примесей и минеральных добавок. Чистая вода — залог хорошего бетона.
- Песок. Для качественного замеса раствора предпочтительнее покупать чистый песок.Клей и другие, оставляя его полностью отсутствовать, так как это может повлиять на прочность раствора.
- Наполнитель. Можно использовать щебень, гравий. Однако, чтобы тяжелый бетон был более прочным, лучше использовать гранит или другие породы, которые славятся своей крепостью. В качестве дополнительного связующего может добавляться раствор мраморной крошки. Этот наполнитель стоит недешево, но отлично держит.
- Дополнения. Используя изготовление раствора добавки, химической или минеральной, можно улучшить качество, увеличить прочность, срок службы, водостойкость, коррозионную стойкость и другие важные показатели.
Важно! Для изготовления тяжелого бетона приобретайте только чистые, не содержащие примеси компонентов, так как наличие примесей может негативно сказаться на свойствах раствора.
Обычно тяжелые и сверхтяжелые бетоны используются в строительстве промышленных масштабов. Например, такие решения используются при строительстве хранилищ банков, военных объектов и других стратегических объектов, станций технического обслуживания, парковок для большегрузных автомобилей, этажей в крупных торговых центрах, атомных электростанций и других объектов.Такое решение при правильной планировке способно выдерживать нагрузки до 3000кг / м Три .
Рассмотрим, что такое тяжелые бетоны:
- Обладая высокой прочностью. В состав этого в основном добавляют особое вещество, придающее раствору пластичность. Также для придания большей прочности его подвергают специальной процедуре — вибрации.
- Бетон. Этот вид используется при заливке арматурных конструкций в особо прочных перекрытиях, а также при изготовлении бетонных блоков.
- Быстро затвердевает. Он состоит из цемента, который быстро затвердевает и затвердевает.
Таким образом, раствор затвердевает быстрее, сокращая время до минимума без снижения качества.
- Гидравлический. Особый вид, позволяющий использовать его в местах с повышенной влажностью, а также при строительстве водных объектов.
- Дорога. Обычно этот вид используется для дорожного покрытия, но если вам нужен раствор, выдерживающий большие нагрузки, то обращайтесь за.
- Мелкозернистый. Свое название раствор получил из-за отсутствия в его составе горных пород и крупного щебня.Чаще всего используется, когда требуется мелкая работа, например, при кладке тонких стен. Производитель этого вида также регулируется ГОСТом. Раньше это был ГОСТ 26633-91, теперь это ГОСТ 26633-2012.
- Декоративный. Эта форма используется в тех случаях, когда вы хотите применить дизайнерское решение в парках. Из такого бетона делают красивые бордюры и оригинальные скульптурные решения, украшающие парки и набережные.
Видов бетона много, из-за чего область его применения практически безгранична.
Чтобы выбрать высококачественный бетон, оцените его по следующим критериям:
- Прочность. Обычно бетон проверяют на плотность сжатия. Жесткие решения в силу своего предназначения должны выдерживать большие нагрузки, сохраняя при этом свою целостность. Раствор имел максимальную прочность, он должен состоять из цемента марки М100-М800, а лучший портландцемент и чем выше соотношение цемента и воды, тем прочнее получается раствор.
- Класс бетона.Этот критерий говорит о прочности сжатого бетона и пределе его растяжения. Другими словами, чем больше прочность на сжатие, тем лучше. Что касается прочности на разрыв, то она меньше прочности на сжатие. Эти показатели обозначаются как: прочность на сжатие обозначается буквой b и измеряется в МПа, предел прочности обозначается индексом режима ВТ. Таким образом, чем выше эти показатели, тем лучше бетон.
- Мороз. Еще один важный показатель.Из-за высоких температур в бетоне скапливается вода, что существенно влияет на его качество и долговечность.
Раствор должен быть морозостойким. Эта функция позволяет сохранить его первоначальные свойства. Морозостойкость обозначается буквой F.
. - Водонепроницаемость. Чем выше это число, тем длиннее бетон. Обозначается эта цифра буквой W.
- Огнеупорность. Это свойство бетона особенно важно, когда здание или любой другой объект подвергаются воздействию высоких температур, например.грамм. пожар или взрыв.
Важно! Тяжелый бетон должен обладать высокими характеристиками по всем этим характеристикам, иначе качество не будет соответствовать условиям применения. Показатели измеряются либо в градусах Цельсия, либо в градусах Фаренгейта, в зависимости от страны-производителя.
Раствор, как и любой продукт, имеет свои стандартные справочные правила изготовления, характеристик, состава, которые нужно строго соблюдать. Итак, правила производства тяжелого бетона — это ГОСТ 26633-2012.Согласно ГОСТу раствор в стандарте имеет следующие характеристики:
- Устойчивость к замерзанию — F500.
- Водонепроницаемость — W6-W12.
- Усадка при схватывании — 0,15 мм на 1 метр.
- Предел прочности на разрыв — BT10-BT40.
Для получения раствора повышенной прочности и лучшего качества по другим характеристикам необходимо соединить компоненты, соблюдая следующие пропорции:
- 1 часть цемента.
- 2 части песка.Как правило, в тяжелых бетонах используют крупный песок. Необходимо увеличить прочность, так как в этом случае в качестве связующего компонента используется песок.
- 4 части наполнителя. Подходит к любому наполнителю, самому доступному.
- 0,8 части воды. Вода должна быть чистой и без примесей.
В целом в составе доля химических примесей составляет не более 4-5% от общей массы полученной массы.
Бетон полностью затвердевает, «становится взрослым» через 28 дней при условии, что температура в помещении была не ниже 16-18 ° C, а влажность не превышала 50-60%.
Важно! Не добавляйте в раствор много примесей, так как это может иметь противоположный эффект, и раствор не будет иметь даже исходных свойств.
Каждый сорт, так как каждый имеет свои особенности и качество. Согласно ГОСТу существует целый ряд классов решений, принятых в качестве мирового стандарта. В линейке продуктов представлены решения разного класса: B3,5; B5; B7,5; B10; B12,5; B15; B20; B25; B30; B35; C40; В45; B50; W55; B60; B70; B80; B90; 100.ГОСТ также допускает промежуточные классы, например, 27,5. Каждый из этих типов имеет свой набор свойств, на которые нужно обращать особое внимание при выборе типа бетона. Как правило, все характеристики этих видов перечислены в гостевой системе, которой руководствовались при создании решения указанные классы.
Тяжелый бетон — это тип, в состав которого входят дорогие и очень редкие компоненты, благодаря чему раствор является наиболее прочным и увеличивает его вес. Итак, данный вид предназначен исключительно для промышленного строительства, поэтому использовать его при строительстве обычных объектов не очень рентабельно.Поэтому нет необходимости заказывать особо тяжелый бетон для заливки фундамента на участке.
Цена решения зависит от стоимости его компонентов. Например, найти чистую воду, гравий или песок без примеси глины не проблема, но и добавки, улучшающие качество, не просто. Также цена зависит от его бренда. Например, решение марки М100 будет стоить 2400руб / м Три . Чем выше оценка, тем выше цена.
Сверхтяжелые бетоны в жилищном строительстве не используются из-за дороговизны комплектующих.Он состоит из элементов, которые сложно найти, из-за этого его стоимость увеличивается.
Чтобы у вас было четкое представление о твердом бетоне, предлагаем вам видео
Связанные с контентом
(PDF) Щебень в качестве заполнителя бетона при производстве железобетонных конструкций
4
Сеть конференций MATEC 193, 02005 (2018) https://doi.org/10.1051/matecconf/201819302005
ESCI 2018
ущерб, нанесенный выбросами при транспортировке), оказывается, что вторичный щебень
на 15-20% дешевле природного щебня.Более того, его использование в дорожных работах на нижележащем слое
оказалось эффективным. Расходы на обработку и качество вторичного щебня
зависят от способа сноса зданий и сооружений (снос, взрыв, демонтаж
), типа дробильных станций (шнековый, роторный, трубный и т. Д.), Разделяемости сортировка материала
перед дроблением и некоторые другие сложные факторы.
Щебень из щебня содержит значительное количество растворной составляющей,
при этом, зона контакта исходного зерна и раствора, которая является наименее жесткой и наибольшей
зерен пористого щебня, значительно снижает физико-механические свойства F Mp3
щебень от 200 до 15 циклов, дробимость от 12 до 24.
При этом бетон с вторичным щебнем имеет прочность более 200 кг / см2
, более 125 циклов морозостойкости. Это можно объяснить тем, что существующие методы и критерии оценки
для природного щебня не подходят для качественной оценки
щебня, качество которой должно оцениваться косвенно
по физико-механическим свойствам бетона. производится из вторичного щебня.Это
необходимо для разработки специальных нормативных документов, учитывающих специфические свойства щебня
.
Однако экологическая проблема остается актуальной не только на этапе производства стройматериалов
, но и на этапе утилизации отходов. Проблема утилизации строительного мусора
актуальна во всем цивилизованном мире. По данным международной организации
RILEM, годовой объем только бетонного лома составляет более 360 миллионов тонн
в странах ЕС, США и Японии.
Таким образом, сборные панельные дома общей площадью около 36 млн м 2 строились в
Москве; некоторые из этих зданий были построены из виброкатаного бетона и других панелей (здания К-
7, П-32, II-35). Эти постройки морально и морально морально и морально морально и
изношены и морально и поэтому практически снесены.
Экономически целесообразна переработка бетона и железобетона, оставшегося от снесенных
построек, и получение вторичного щебня. Строительный мусор
дешевле использовать, потому что, во-первых, транспортировка и хранение отходов бесплатны; во-вторых, строительные отходы
— это бесплатное и экологически чистое сырье; Ёмкости земельных участков
сохранены за счет отсутствия отходов на полигонах, что улучшило экологическую ситуацию
.
3 Выводы
Обобщая отечественные и зарубежные достижения, можно найти решение
проблемы обработки и удаления техногенных отходов путем создания интегрированной системы управления
для рационального использования материальных ресурсов.Его цель
— постоянное развитие ресурсосберегающих методов хозяйственной деятельности. Неотъемлемой частью этой системы
является интегрированная система управления рациональным использованием вторичного сырья,
включая бетонные отходы.
После анализа вторичного щебеночного бетона из дробленого бетона мы отобрали и испытали
различных смесей с различным соотношением цемент-вода и разными значениями текучести
(Таблица 3). По физическим свойствам бетон с вторичным щебнем равен
ГОСТ 25192, ГОСТ 26633-91.
Строительный мусор и отходы снесенных ветхих пятиэтажных домов — тема
, которую следует рассматривать отдельно, так как это проблема национального уровня, необходимо разработать единую схему учета захоронения отходов
, и его рациональное использование
в будущем как ресурсосберегающая технология при производстве строительных материалов
для изделий и конструкций.
Образцы легкого бетона | Скачать научную схему
В настоящее время различные типы легких бетонов имеют много преимуществ по сравнению с тяжелыми (уменьшение общей массы конструкции, повышенные теплофизические свойства, меньший расход материалов).Для повышения эффективности легких бетонов было предложено использование различных промышленных отходов, таких как летучая зола, шлак и зольный остаток. Это очень важно для производства зеленого бетона, так как очень важно получать новые виды экологически чистых материалов с использованием отходов. В статье обосновано использование и создание легкого бетона с органо-минеральными добавками на основе промышленных отходов, проведен анализ математической модели второго порядка, описывающей влияние количества зольного остатка (ЗШ) ТЭС Вунг Анг и пенополистирольных сфер (ППС) на свет. плотность бетона и прочность на сжатие в возрасте 28 суток нормального твердения.В данной работе количество БА и ЭПС варьировалось от 14,5 до 45,5% соответственно от веса цемента и от 24,5 до 55,5% от объема бетонной смеси. В данном исследовании исследовалось влияние пенополистирольных сфер (EPS) и зольного остатка (BA) ТЭС «Vung Ang» в качестве входных параметров на свойства полистиролбетона (PCP). С одной стороны, различные пропорции БА (14,5, 20, 30, 40 и 45,5%) были добавлены в бетонные смеси в качестве частичной замены портландцемента по весу. С другой стороны, количество пенополистирола было заменено объемом свежего бетона в диапазоне от 24.От 5% до 55,5%. Кроме того, центральный метод композитного проектирования Бокса-Уилсона для факторов второго порядка был использован для прогнозирования эффектов EPS и BA на свойства полистиролбетона.
Результаты показали, что предложенные уравнения регрессии этой математической модели достигли адекватной точности прогноза. Следовательно, влияние как зольного остатка, так и сфер из пенополистирола на сухую плотность и 28-дневную прочность на сжатие образцов PSC было значительным. В будущем должны быть проведены дальнейшие исследования для изучения прогноза качества бетона зеленого света, содержащего различные отходы.
бетон | Определение, состав, применение и факты
Бетон , в строительстве, конструкционный материал, состоящий из твердого, химически инертного вещества в виде частиц, известного как заполнитель (обычно песок и гравий), который скреплен между собой цементом и водой.
бетонСтроители заливают бетон.
© Дмитрий Калиновский / Shutterstock.comПодробнее по этой теме
Строительство: Ранние бетонные конструкции
Одним из самых ранних сохранившихся примеров этого бетонного сооружения является Храм Сибиллы (или Храм Весты) в Тиволи, построенный во время. ..
У древних ассирийцев и вавилонян в качестве связующего вещества чаще всего использовалась глина. Египтяне разработали вещество, более напоминающее современный бетон, используя известь и гипс в качестве связующих. Известь (оксид кальция), полученная из известняка, мела или (если возможно) раковин устриц, продолжала оставаться основным пуццолановым или цементирующим агентом до начала 1800-х годов. В 1824 году английский изобретатель Джозеф Аспдин сжег и измельчил смесь известняка и глины.Эта смесь, называемая портландцементом, остается основным вяжущим веществом, используемым в производстве бетона.
Заполнители обычно бывают мелкими (размером от 0,025 до 6,5 мм [0,001–0,25 дюйма]) или крупными (от 6,5 до 38 мм [0,25–1,5 дюйма] или более). Все заполнители должны быть чистыми и не содержать примесей с мягкими частицами или растительными веществами, потому что даже небольшие количества органических соединений почвы приводят к химическим реакциям, которые серьезно влияют на прочность бетона.
Бетон характеризуется типом используемого заполнителя или цемента, особыми качествами, которые он проявляет, или методами, используемыми для его производства. В обычном конструкционном бетоне характер бетона во многом определяется соотношением воды и цемента. Чем ниже содержание воды при прочих равных условиях, тем прочнее бетон. В смеси должно быть ровно столько воды, чтобы гарантировать, что каждая частица заполнителя полностью окружена цементным тестом, чтобы промежутки между заполнителем были заполнены, и чтобы бетон был достаточно жидким, чтобы его можно было заливать и эффективно растекать.Другой фактор долговечности — это количество цемента по отношению к заполнителю (выраженное в трехкомпонентном соотношении — цемент, мелкий заполнитель и крупный заполнитель). Там, где требуется особо прочный бетон, заполнителя будет относительно меньше.
Получите подписку Britannica Premium и получите доступ к эксклюзивному контенту. Подпишитесь сейчас Прочность бетона измеряется в фунтах на квадратный дюйм или килограммах на квадратный сантиметр силы, необходимой для раздавливания образца определенного возраста или твердости. На прочность бетона влияют факторы окружающей среды, особенно температура и влажность. Если позволить ему высохнуть преждевременно, он может испытывать неравные растягивающие напряжения, которым невозможно противостоять в недостаточно затвердевшем состоянии. В процессе, известном как отверждение, бетон остается влажным в течение некоторого времени после заливки, чтобы замедлить усадку, возникающую при затвердевании. Низкие температуры также отрицательно сказываются на его прочности. Чтобы компенсировать это, к цементу примешивают такую добавку, как хлорид кальция.Это ускоряет процесс схватывания, который, в свою очередь, выделяет тепло, достаточное для противодействия умеренно низким температурам. Большие бетонные формы, которые невозможно покрыть должным образом, не заливают при отрицательных температурах.
Рабочие, использующие мастерки для разглаживания свежеуложенного бетона.
Помощник фотографа 2-го класса Эрик Пауэлл / США. Navy Бетон, затвердевший на заделанном металле (обычно стали), называется железобетонным или железобетонным. Его изобретение обычно приписывают Жозефу Монье, парижскому садовнику, который сделал садовые горшки и кадки из бетона, армированного железной сеткой; он получил патент в 1867 году.Арматурная сталь, которая может иметь форму стержней, стержней или сетки, способствует прочности на разрыв. Обычный бетон с трудом выдерживает нагрузки, такие как воздействие ветра, землетрясения, вибрации и другие изгибающие силы, и поэтому не подходит для многих строительных конструкций. В железобетоне прочность на разрыв стали и прочность на сжатие бетона делают элемент способным выдерживать большие нагрузки всех видов на значительных пролетах. Текучесть бетонной смеси позволяет размещать сталь в точке или около того места, где ожидается наибольшая нагрузка.
Еще одно новшество в каменном строительстве — это использование предварительно напряженного бетона. Это достигается либо предварительным, либо последующим натяжением. При предварительном натяжении отрезки стальной проволоки, тросов или канатов укладываются в пустую форму, а затем растягиваются и закрепляются. После заливки и схватывания бетона анкеры освобождаются, и по мере того, как сталь стремится вернуться к своей исходной длине, она сжимает бетон. В процессе последующего натяжения сталь проходит через каналы, образованные в бетоне.Когда бетон затвердеет, сталь прикрепляется к внешней стороне элемента каким-либо захватным устройством. Приложив к стали отмеренное растягивающее усилие, можно тщательно отрегулировать степень сжатия, передаваемого бетону. Предварительно напряженный бетон нейтрализует растягивающие силы, которые могут привести к разрыву обычного бетона, сжимая область до точки, в которой не возникает никакого напряжения, пока не будет преодолена прочность сжатой секции. Поскольку он обеспечивает прочность без использования тяжелой стальной арматуры, он с большим успехом используется для строительства более легких, мелких и элегантных конструкций, таких как мосты и огромные крыши.: lI, Zs & + HQ (& = َ, A: J9QLphUt: aaKjwWa˪
I + Zaox9) tNc, 6IL>? {2 ߺ2 | XA&D; Mir>: `» / 0BxL; 8w
̤E0
o]) l) [d ޕ ƪ>: _x3endstream
эндобдж
2 0 obj
>
эндобдж
3 0 obj
>
эндобдж
4 0 obj
>
эндобдж
5 0 obj
>
эндобдж
6 0 obj
>
поток
конечный поток
эндобдж
7 0 объект
>
поток
x +
АВТОМАТИЗИРОВАННАЯ ЛИНИЯ ПО ПРОИЗВОДСТВУ ПОЛИСТИРОБЕТОННЫХ БЛОКОВ производительностью 100 м3 / смену
Технические характеристики линии
Вместимость | 100 м 3 / смену (200 м 3 / сутки) |
Потребляемая мощность | 81 кВт / ч |
Использование воды | ~ 15 тн / смену |
Утилизация цемента | ~ 33 тн / смену |
Утилизация полистирола | ~ 1 тонна / смену |
Производство | мелкие стеновые блоки по ГОСТ 21520-89, ГОСТ 51263-99 |
Требуемая площадь производственного помещения | не менее 1000 м 2 |
Высота потолка в зоне смешивания | не менее 6 м * |
Высота потолка в производственной зоне | не менее 3 м * |
Температура окружающей среды | не менее +15 o С |
Требуемый персонал | 12 рабочих, 1 начальник производства / прораб |
ПРЕИМУЩЕСТВА
Автоматизация управления процессами
На производственных линиях используются электронные системы для управления загрузкой и дозированием сырья в зоне смешивания. В системах управления предусмотрены функции регистрации и контроля сырья. Зона смешивания контролируется одним оператором. В зоне раскроя имеется отрезной станок, которым также управляет один оператор. Процесс демонтажа формы и укладки блоков автоматизирован.
Точность дозирования
Сырье подается на весы с тензодатчиками и весовым контроллером, который обеспечивает точное дозирование.
Высокая вместимость
Высокая производительность обеспечивается автоматизированной системой загрузки и дозирования сырья, а также высокой скоростью заполнения смесителя водой и сырьем.Высокопроизводительный отрезной станок обеспечивает высокую скорость резки монолита на блоки заданного размера.
Высокое качество
Система автоматизации процессов обеспечивает высокое качество продукции и гарантирует точность дозирования, а также стабильный и однородный состав, что позволяет нам выпускать качественную и конкурентоспособную продукцию.
СЫРЬЕ ДЛЯ ПРОИЗВОДСТВА ПОЛИСТИРОЛБЕТОНА
- Папка. В качестве вяжущего используется портландцемент или шлакопортландцемент марок М-400 и М-300 по ГОСТ 10178.
- Совокупный. Гранулированный полистирол, вспененный однократно или несколько раз, служит заполнителем.
- Вода для замешивания. Вода соответствует требованиям ГОСТ 23732.
- Смазка для форм. Смазки для форм SDF или другие антиадгезионные агенты используются для обеспечения эффективного удаления плесени.
- Кремнеземный компонент * Используется для производства полистиринового бетона высокой плотности.
- Химические добавки. Химические добавки (воздухововлекающие, пластифицирующие, регуляторы твердения) должны соответствовать требованиям ГОСТ 24211.
КРАТКОЕ ОПИСАНИЕ ТЕХНОЛОГИЧЕСКОГО ПРОЦЕССА
1. Приготовление полистирольной смеси
Пенополистирол
Сырье (гранулы полистирола) подается в приемную воронку устройства предварительного вспенивания, затем с помощью шнекового конвейера подается в камеру предварительного вспенивания.Впервые гранулы полистирола вспениваются в камере предварительного вспенивания с помощью водяного пара, образующегося в парогенераторе. После вспенивания полистирол отправляется на конвейер для сушки гранул для снижения их влажности и аэрации. После сушки гранулы транспортируются с помощью пневмотранспортера в бункеры выдержки. Второе или многократное (при необходимости) расширение гранул полистирола выполняется так же, как и первое расширение.
Добавление воды в смеситель
Вода дозируется с помощью электронного дозатора воды.Оператор смесительной секции устанавливает необходимое количество воды на панели управления и запускает цикл загрузки смесителя.
Загрузка смесителя сырьем
Весовые дозаторы загружаются сырьем (цемент и кремнистый компонент, если используется) с помощью весового регулятора, так же, как загрузка пенополистирола в объемный дозатор. Цемент загружается с помощью шнекового конвейера, а полистирола — с помощью пневматической конвейерной системы.Затем цемент выгружается из дозатора в смеситель, препарат перемешивается 2-3 минуты до однородности. Когда он готов, дозатор химических добавок дозирует воздухововлекающую добавку, затем полистирол загружается в смеситель и смесь перемешивается в течение 1-2 минут. В режиме реального времени оператор контролирует все процессы, происходящие в секции смешивания. При необходимости оператор может скорректировать или изменить производимую рецептуру, время перемешивания и другие технологические параметры на панели управления.Оборудование может работать как в автоматическом, так и в ручном режиме.
2. Формовочный блок
Готовая смесь сливается через кран смесителя в емкость объемом 0,85 куб. м плесень. Форма заполняется сразу. Форма состоит из основания и сменных сменных стенок. Перед отливкой форма смазывается и транспортируется в секцию смешивания, где происходит отливка.
3. Блок старения
После литья форма по железной дороге транспортируется к участку выдержки, где блок выдерживается до тех пор, пока не наберется прочности, достаточной для снятия стенок.Прочность, достаточная для снятия стен, достигается за 4-7 часов и зависит от плотности полистирола, активности цемента, температуры и т. Д.
4. Демонтаж форм и вырезание массивов
После того, как массив наберет необходимую прочность, форма, содержащая массив, по железным дорогам переносится на демонтажную машину, основание формы фиксируется на пути. Затем четыре стенки формы снимаются и поднимаются захватом. После демонтажа формы основание формы и массив переносятся в секцию резки.Затем свободные стены накладываются на свободное основание, которое находится на прилегающей железной дороге. Форма в кожухе отправляется на участок разливки. Массив разрезают на блоки заданных размеров режущим агрегатом АРК-004. На участке резки находятся два отдельных последовательных модуля для вертикальной и горизонтальной резки массива.
Основание пресс-формы фиксируется захватом на вертикальном модуле, в то время как оператор запускает вертикальный модуль. Двигаясь по направляющим, модуль разрезает массив в вертикальной плоскости и обрезает его с обоих концов.После вертикальной резки опалубка с массивом переносится в зону горизонтального модуля, фиксируется захватом, после чего разрезается в горизонтальной плоскости на блоки заданных размеров, а также нижний слой и верх срезан.
Пока горизонтальный модуль работает, следующий массив подается в зону вертикального модуля. Таким образом, одновременно производится резка двух массивов, что обеспечивает высокую пропускную способность линии.
5.Укладка блоков на поддоны, упаковка и хранение
Опалубка с вырезанным массивом переносится в блок штабелирования блоков. Основание пресс-формы закреплено на рельсе. Затем половину среза массива с помощью захвата укладывают на поддон. Для комплектации поддона вручную устанавливаются восемь блоков. Затем укладывается вторая половина массива, а также восемь блоков вручную (в зависимости от их размеров). Поддон с блоками обматывают стрейч-пленкой.
6. Блок термовлагообработки
В зависимости от климатической зоны и типа производимого материала блоки, уложенные на поддоны, могут набирать марочную прочность на складе готовой продукции или при термовлагообработке. Для ускорения набора прочности блоков необходима термовлагообработка блоков. При термовлагообработке блоки выдерживаются в камере от 8 до 12 часов при температуре от +40 до 60оС.Режим термовлагообработки также зависит от плотности материала, активности цемента и определяется заказчиком для каждого конкретного вида выпускаемой продукции.
7. Переработка отходов резки
При резке блок обрезается с двух сторон и срезается верхняя корочка. Хорошая идея — разбить эту резку с помощью DG-1 Crasher. Crasher позволяет измельчать обрезки полистиролбетона размером от 0 до 30 мм. Грунт может быть использован как объемный утеплитель для утепления крыш, чердаков, полов и т. Д.Использование этого крашера сделает ваше производство практически безотходным.
ТЕХНИЧЕСКИЕ ХАРАКТЕРИСТИКИ ЛИНИЙ
N | Имя | Количество |
Участок хранения, подготовки и отгрузки сырья | ||
1 | Шнековый транспортер цемента (L = 6 м *, мотор-редуктор (Италия), N = 4 кВт) | 2 |
Площадь пенополистирола | ||
1 | Преддетандер ПНД-500 (Н — 3,3 кВт) | 1 |
2 | Парогенератор ПАР-50 (Н — 35 кВт, 50 кг / час) | 1 |
3 | Конвейер для сушки гранул пенополистирола (N — 3 кВт) | 1 |
4 | Бункер выдержки гранул пенополистирола 40 м 3 | 10 |
5 | Пневмотранспортная система (N — 6 кВт) | 1 |
Площадь смешения | ||
1 | Электронная система управления (включая дозатор воды + подкачивающий насос) | 2 |
2 | Весовой дозатор цемента (тензодатчики, пневмозатвор, диапазон взвешивания до 600 кг) | 2 |
3 | Дозатор объемный ППС 2,0 м 3 (датчик уровня, пневмозатвор) | 2 |
4 | Смеситель полистиролбетоносный РСГ-2000 (Н — 11 кВт, В — 2,0 м 3 ) | 2 |
5 | Компрессор C200LB40 (8-10 атм.![]() | 1 |
6 | Героторный насос ГН-10 (Н — 7,5 кВт) | 1 |
Участок раскроя блоков | ||
1 | АРК-004 Автомат раскройный комплекс для вертикального и горизонтального пиления массой (Н — 19,5 кВт) | 2 |
2 | Форма для заливки ФМ-0,91 м 3 (В — 0,91 м 3 ). | 110 |
3 | Транспортная тележка | 6 |
4 | Комплекс для демонтажа форм (N = 2,0 кВт) | 1 |
5 | Комплекс для укладки блоков на поддоны (N = 2,5 кВт) | 1 |
Участок вторичной переработки обрезных отходов | ||
1 | Дробилка ДГ-1 (Н — 4,5 кВт) | 1 |
РАСХОД МАТЕРИАЛА * НА 1 м
3 ПОЛИСТИРОЛБЕТОНА D-450Материал | Количество |
Цемент (М 400, М 300), кг | 330 |
EPS, кг | 10 |
Вода, л | 150 |
Воздухововлекающая добавка, кг | 0,2-1,0 |
Химическая добавка, кг | ** |
* Рецепты корректируются с учетом свойств сырья, выбранного заказчиком.
** Тип и количество добавок определяется на этапе проектирования бетона.
ОБЩАЯ ИНФОРМАЦИЯ
Для снижения затрат заказчика линия поставляется без силоса для цемента, бункера для песка и перил для транспортировки форм. Заказчику предоставляются чертежи раздельного изготовления этих узлов.
Кроме того, заказчик несет ответственность за подогрев воды до +35 … + 40 ° C и устройство камер пропаривания.Для работы линии в 2 смены требуются дополнительные опалубки.
Гарантийный срок на поставляемое оборудование — 12 месяцев. Компоненты каждой единицы оборудования указаны в контракте, паспорте оборудования и акте приема-передачи.
Специалисты ООО «Сибирские строительные технологии» (СКТ) разрабатывают компоновку оборудования на производственном объекте заказчика. Установка оборудования согласно схеме осуществляется заказчиком и за его счет.Заказчику предоставляется схема (чертежи) оборудования соответствующих помещений и подробная иллюстрированная инструкция по установке.
После того, как заказчик завершит установку и подключение оборудования, SCT выполняет следующие работы:
• пуско-наладка оборудования;• конструкция из полистиролбетона;
• оптимизация технологии производства;
• обучение персонала заказчика.
Заказчик несет ответственность за соблюдение всех правил техники безопасности, требований по охране труда и окружающей среды, а также других местных норм.
Все расходы по транспортировке и размещению персонала SCT на период проведения работ берет на себя заказчик. Оптимизация технологии включает оптимизацию состава бетона на основе сырья, предоставленного заказчиком. SCT предоставляет услуги поддержки.
После ввода оборудования в эксплуатацию заказчику предоставляется техническая документация, в том числе:
• технический регламент на производства;• Диаграмма процесса;
• описание вакансии;
• Инструкции по технике безопасности;
• ГОСТы.
УСЛОВИЯ ПОСТАВКИ
Стоимость указана для EXW-Новосибирск (Россия) и не включает стоимость растаможки и отгрузки.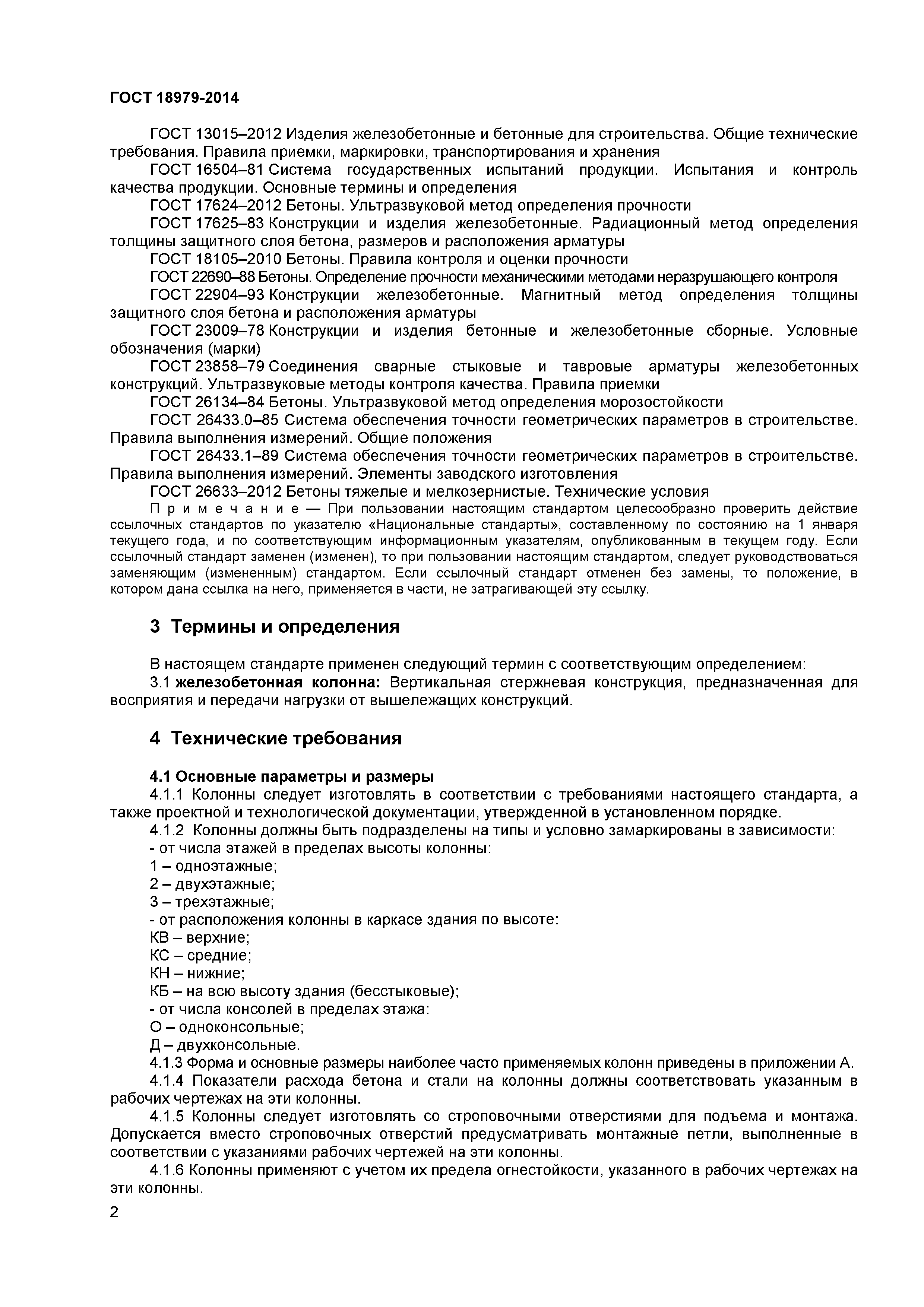
УСЛОВИЯ ОПЛАТЫ
Оплата 1—70% от стоимости контракта в течение 5 дней с момента подписания контракта.
Оплата 2–30% от стоимости контракта в течение 5 дней с момента получения подтверждения о готовности оборудования к отгрузке.
Сравнение DIN / ISO 8047 (Entwurf) с несколькими стандартами по определению скорости ультразвуковых импульсов в бетоне
Сравнение DIN / ISO 8047 (Entwurf) с несколькими стандартами по определению скорости ультразвуковых импульсов в бетоне NDTnet — апрель 1997 г., том 2, № 04Сравнение DIN / ISO 8047 (Entwurf) с несколькими стандартами по определению скорости ультразвукового импульса в бетоне
S. Popovics, K. Komlos *, J. Popovics **Университет Дрекселя, Филадельфия, Пенсильвания (США)
* Институт строительства и архитектуры, Бра тислава (Словакия)
** Северо-Западный университет, Эванстон, Иллинойс (США)
Ключевые слова: прочность на сжатие, бетон, стандарты, ультразвук
Этот документ был представлен на Международном симпозиуме по неразрушающим испытаниям в гражданском строительстве (NDT-CE) 26. -28.09.1995 г. в Берлине. NDT-CE, полная программа или ультразвуковая часть
- Введение
- Метод
- Факторы, влияющие на скорость импульса
- Общее сравнение стандартной скорости
- Возражения
- Выводы
Введение
- Неразрушающий контроль бетона быстро приобретает все большее значение из-за ухудшения инфраструктуры.Было предложено множество методов испытаний, но ни один из них не является удовлетворительным. Тем не менее метод, основанный на продольной скорости импульса, стал популярным благодаря своей простоте и экономической эффективности.
- DIN / ISO 8047 (Entwurf) «Закаленный бетон — определение скорости ультразвукового импульса» на немецком языке
- «Испытания бетона — рекомендации и комментарии» Н.
Burke in Deutscher Ausschuss fur Stahlbeton (DAfStb), Heft 422, 1991, как дополнение к DIN / ISO 1048 на немецком языке
- ASTM C 597-83 (91) «Стандартный метод испытания скорости импульса через бетон»
- BS 1881: Часть 203: 1986 «Испытания бетона — Рекомендации по измерению скорости ультразвуковых импульсов в бетоне»
- RILEM / NDT 1 1972 «Испытание бетона ультразвуковым импульсным методом»
- ГОСТ 17624-87 «Бетон. Ультразвуковой метод определения прочности» на русском языке.
- STN 73 1371 «Метод ультразвукового импульсного контроля бетона» на словацком языке (идентичен чешскому CSN 73 1371)
- МИ 07-3318-94 «Испытания бетонных покрытий и бетонных конструкций отбойным молотком и ультразвуком», техническое руководство на венгерском языке.
В большинстве стран есть стандартизированные процедуры для выполнения этого теста (1). В данной статье анализируются следующие восемь из этих стандартов:
За сравнением и анализом методов испытаний следует критическая оценка. Это обязательно субъективно; тем не менее, есть надежда, что это поможет в улучшении использования метода скорости ультразвуковых импульсов и внесет вклад в улучшение будущих технических характеристик.
В некоторых стандартах используется термин «измерение» (Messung) или эквивалент скорости пульса. Это не совсем правильно, потому что напрямую измеряются только расстояние между двумя преобразователями и время прохождения.(Время прохождения — это время, необходимое для прохождения импульса через бетон.) Скорость импульса рассчитывается на основе этих двух значений. Тем не менее, это неправильное название не вызывает большого недоумения.
Для наглядности текст, касающийся спецификаций в стандарте DIN / ISO, выделен курсивом, все остальное написано как обычный текст.
Метод
- В основе сравнения лежит стандарт DIN / ISO 8047 (Entwurf).Он разделен на 7 глав и приложение. Каждая глава состоит из нескольких подразделов. Эти подглавы будут кратко описаны и сравнены с соответствующими главами других стандартов. В сравнениях подчеркиваются различия между методами испытаний. Если нет сравнения DIN с ASTM по какому-либо конкретному пункту, это означает, что два стандарта аналогичны в этом отношении.
- генератор импульсов должен производить повторяющиеся импульсы со скоростью не менее 10 импульсов в секунду и не более 150 импульсов в секунду;
- время измерения должно сено: точность 0,5%;
- напряжение, генерируемое преобразователем, должно быть усилено по мере необходимости для создания запускающих импульсов в цепи измерения времени;
- должно быть предусмотрено калибровочное устройство для проверки правильности работы схемы измерения времени.
- преобразователи расположены прямо напротив друг друга.Это самый чувствительный расположение, и называется прямым коробка передач;
- преобразователи расположены по диагонали относительно друг друга, то есть преобразователи расположены поперек углов. Это менее чувствительно, чем прямая передача, и называется диагональной передачей;
- Преобразователи прикреплены к одним и тем же боковым поверхностям.
Это наименее чувствительное устройство, называемое непрямой передачей.

Цель и использование
Сфера применения DIN / ISO ограничивается определением скорости продольных ультразвуковых волн в бетоне.Эта так называемая «скорость импульса» может использоваться для оценки однородности бетона в конструкции, измерения толщины слоя бетона низкого качества, отслеживания изменений бетона с течением времени и обнаружения дефектов и анизотропии. Также допустимо использовать его для оценки прочности бетона при наличии надежных калибровочных кривых. Однако следует отметить, что этот ультразвуковой тест не является приемлемой заменой стандартного определения разрушающей прочности.Определение упругих постоянных не упоминается в DIN.
Аналогичные ограничения и применения даны в других стандартах, особенно в стандартах ASTM и RILEM. Однако большинство из них позволяет оценить упругие постоянные по измерениям скорости импульса. BS также предлагает объяснения различных способов использования скорости пульса.
Основные принципы теста
Метод
Метод, указанный во всех стандартах, основан на том же принципе. Импульсы продольных ультразвуковых волн генерируются электроакустическим преобразователем, который удерживается в контакте с поверхностью испытуемого бетона. После прохождения через бетон импульсы принимаются и преобразуются в электрическую энергию вторым датчиком. Скорость v рассчитывается исходя из расстояния 1 между двумя преобразователями и измеренного электронным способом времени прохождения импульса t как v = l / t.
Аппарат
Обычно устройство состоит из генератора импульсов, пары преобразователей, усилителя и электронного устройства синхронизации для измерения времени прохождения. Согласно DIN, генератор должен иметь: точность измерения времени +/- 1%, короткое время нарастания, способность генерировать низкочастотную генерацию и пригодность для работы в полевых условиях. Для коротких путей рекомендуется использование преобразователя высокой частоты (от 60 до 200 кГц); для длинных путей рекомендуется использовать низкую частоту (от 10 до 40 кГц). В большинстве случаев приемлемы преобразователи с частотным диапазоном от 40 до 60 кГц. Устройство синхронизации должно быть достаточно чувствительным, чтобы запускаться импульсами малой амплитуды.
ASTM также указывает, что
Британский стандарт предлагает метод проверки точности транзита. измерение. Венгерская спецификация требует точности измерения времени 0,1 мкс.
Согласно ГОСТу, Пределы допускаемой абсолютной погрешности измерения времени пролета стандартных образцов не должны быть больше дельта = +/- (0,01t + 0,1), где t — время пролета в мкс. Кроме того, отклонение индивидуальных измерений переходного оттенка образца от среднего значения измерений того же образца не должно превышать 2%.
Согласно STN, точность испытательного устройства на эталонных стержнях должна быть +0.01 Как будто температура окружающей среды колеблется от -10 до + 45 ° C, а влажность не более 80%. RILEM предоставляет подробную информацию о характеристиках преобразователя.
Процедура
В стандарте DIN описаны три возможных варианта расположения датчиков для определения скорости. Эти:
По возможности следует использовать устройство прямой передачи и на поверхностях, которые контактировали с формой.
Важно обеспечить адекватную акустическую связь между бетоном и лицевой стороной каждого преобразователя. Для большей части бетона поверхности обычно достаточно гладкие, чтобы обеспечить хорошую передачу ультразвука, если нанести тонкий слой соответствующего связующего агента. Точность измерения времени прохождения следует проверять с помощью калибровочного устройства перед очень серия измерений. Расстояние между двумя преобразователями должно быть измерено с точностью +/- 1%, а время прохождения должно быть записано с точностью до трех значащих цифр.
Наиболее подробное описание измерений с любым из трех расположений датчиков представлено в BS. Подробности касаются калибровки, принадлежностей, таких как электронно-лучевой осциллограф, цифровых инструментов и т. Д. Согласно ASTM, повторные измерения следует проводить в одном и том же месте, чтобы минимизировать ошибочные показания из-за плохого контакта. В RILEM, а также в венгерской спецификации предлагается перед испытанием сгладить шероховатую бетонную поверхность.RILEM также предоставляет подробную информацию об измерениях времени прохождения с помощью осциллографа как методом максимальной амплитуды, так и методом фиксированной амплитуды. И BS, и STN предупреждают, что непрямая передача дает более низкие скорости импульсов, чем метод прямой передачи. В ГОСТе указано, что максимальная глубина и диаметр пустот в зоне контакта не должны превышать 3 мм и 6 мм соответственно, а максимальная высота любого выступа не должна превышать 0,5 мм.
Расчеты
Во всех стандартах указано, что скорость импульса v следует рассчитывать как
v = л / т (1)
В соответствии со словацким стандартом, скорость импульса, определенная в одномерном или двумерном образце, должна быть пересчитана на эквивалентную скорость импульса в трехмерном образце следующим образомv
l3 = k 3 v l1 (2)v
l3 = (k 3 / k 2 ) v l2 (3) гдеv l1 = скорость импульса в одномерном образце, таком как стержень
v l2 = скорость импульса в двумерном образце, например, пластине
v l3 = скорость импульса в трехмерном образце.
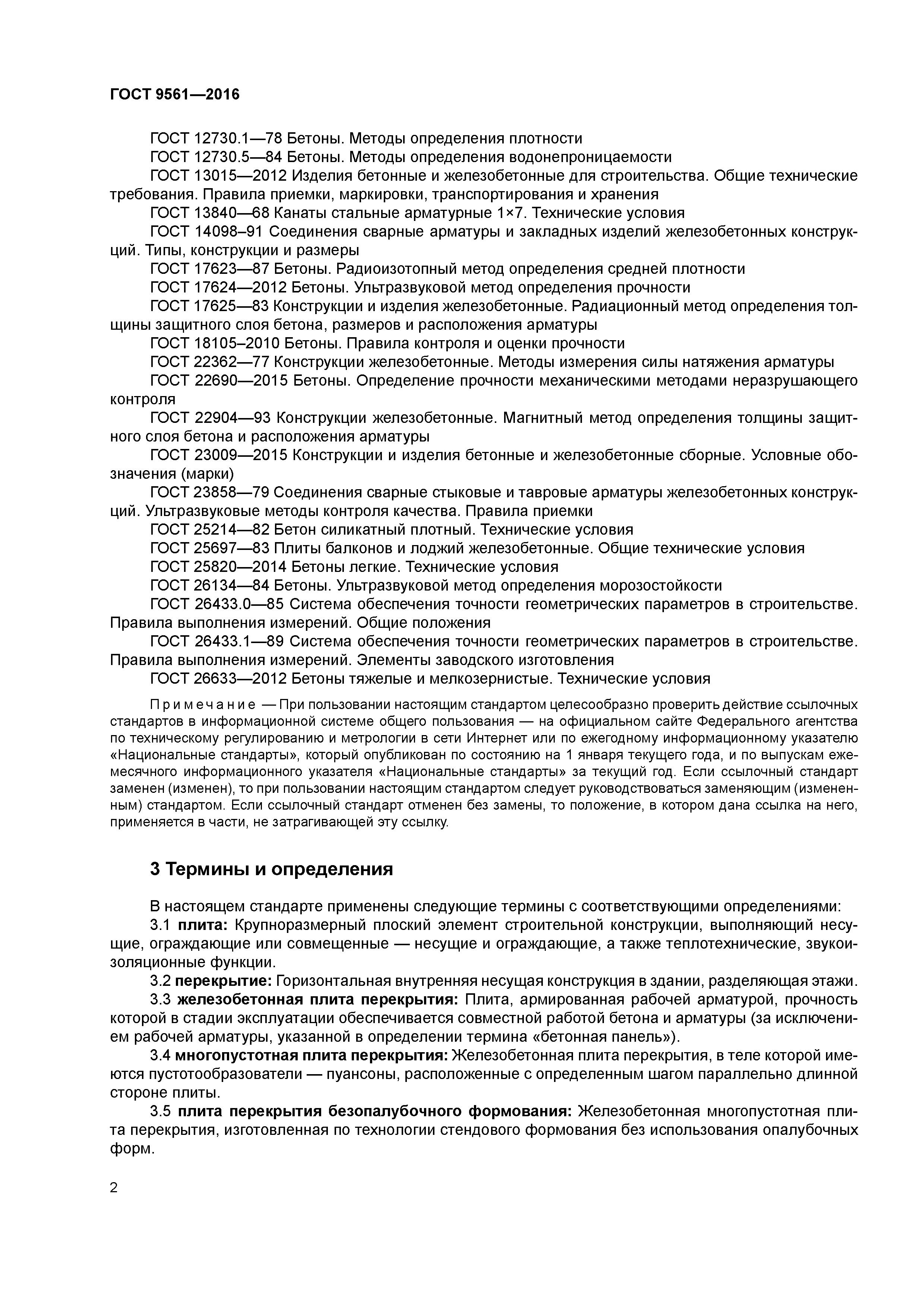
Значения коэффициентов k 2 и k 3 зависят от значения динамического коэффициента Пуассона pcu и могут быть получены следующим образом:
ГОСТ разрешает использовать время прохождения t вместо скорости, когда значение 1 остается постоянным.
Отчет
Стандарт DIN / ISO предоставляет подробные инструкции по составлению протокола испытаний. Это включает: описание испытанной конструкции или образца; спецификации на бетон; бетонный состав; состояние отверждения; и возраст; аппаратура и процедура тестирования; расположение преобразователей; расположение арматуры; свойства бетонной поверхности; расчетная влажность; длина пути; скорость импульса в разных направлениях; и другая значимая информация.
Требования других стандартов короче, но охватывают, по сути, те же вопросы для отчета. ASTM требует измеренного времени прохождения, а также скорректированного времени прохождения. В БС указываются дата, время и место расследования. Венгерская спецификация требует имени клиента, цели тестирования, имен исполнителей измерений, используемого оборудования, визуальных наблюдений и деталей отбора проб.
Точность
В приложении DIN / ISO указано, что следует проверять точность времени прохождения. Если эта проверка выполняется с помощью калибровочной шкалы, время прохождения должно быть известно с точностью +/- 0,2 с. Измеренные значения не должны отличаться более чем на +/- 0,5% от известного значения калибровочной шкалы.
Согласно заявлению о точности ASTM, испытания с участием трех испытательных приборов и пяти операторов показали, что для длины пути от 0.От 3 до 6 м через прочный бетон, разные операторы, использующие один и тот же инструмент, или один оператор, использующий разные инструменты, обеспечат воспроизводимость результатов временного испытания в пределах 2%. В случае изношенного бетона разброс результатов значительно увеличивается. Однако в таких случаях расчетные скорости будут достаточно низкими, чтобы четко указать на наличие повреждений в испытуемом бетоне.
Факторы, влияющие на скорость импульса
- В стандарте DIN обсуждается несколько факторов, которые могут влиять на измеренное время прохождения, помимо качества бетона.Эти:
- температура (в практических пределах эффект незначителен)
- слишком короткая длина пути (длина пути должна быть более 100-150 мм для прямой передачи и больше для непрямой передачи)
- микротрещин (можно уменьшить скорость)
- Влага в бетоне (может немного увеличить скорость).
- образец является одномерным, когда a и b L (стержни, призмы, цилиндры и балки),
- образец двумерный (плоский) при b L. Это тонкие пластины;
- в противном случае образец считается трехмерным (кубы, короткие призмы, цилиндры и балки).
В таких случаях критерий
a> 2 л L и b> 2 л L - a, b = размеры поперечного сечения перпендикулярно направлениям передачи.
- T = толщина плиты,
- l L = — длина волны в бетоне, определяемая из соотношения l L = v L / f u , где v L — скорость импульса ультразвуковой волны в бетоне, а f u — частота ультразвукового волнового движения в бетоне.
- v c = скорректированная скорость импульса в бетоне, км / с
- v с = скорость импульса в стальном стержне, км / с
- a = расстояние от поверхности стального стержня до линии, соединяющей ближайшую точку в два преобразователя, мм
- t = время прохождения, мс
- l = длина прямого пути между преобразователями, мм.
- d i = диаметры арматурных стержней
- n = количество арматурных стержней
- l = длина пути.
- Когда концентрация стали больше, влияние арматурных стержней перпендикулярно или наклонная к длине пути выражается следующим уравнением:
- v с = скорость импульса в стальном стержне, км / с
- v cs = скорость импульса в железобетоне при измерении в направлении, перпендикулярном или наклонном к направлению арматурных стержней, км / с.
Ниже обсуждается влияние двух дополнительных факторов.
Размер и форма образца
Размер образца бетона в направлении распространения импульса должен быть не менее 80 мм при испытании ультразвуком с частотой от 40 до 60 кГц.Меньшие образцы следует использовать с осторожностью.
STN регулирует длину ультразвуковой волны в соответствии с формой и размерами тестируемых элементов. Формы определены следующим образом:
Влияние стальной арматуры на скорость импульса
Стальная арматура увеличивает измеренную скорость импульса, когда она находится в непосредственной близости от пути прохождения импульса. Это влияние особенно сильно, когда арматура параллельна направлению распространения импульса. Однако увеличение незначительно, если расстояние между стальной поверхностью и траекторией больше одной шестой измеренной длины.Влияние стальной арматуры перпендикулярно направлению измерения очень мало, за исключением тяжелой арматуры.
Если невозможно избежать путей распространения волн, параллельных арматурным стержням, и путь находится поблизости (a / I
где
Уравнение 6 может быть изменен, чтобы дать следующее:
V
c = k v m (7) гдеV м = I / t = измеренная кажущаяся скорость импульса, км / с
k = поправочный коэффициент, определяемый как k = g + 2 (a / l) (1-g 2 ), в котором g = v c / v s .
Воздействием арматурных стержней, оси которых перпендикулярны направлению распространения волны и диаметр менее 20 мм, можно не учитывать.В ГОСТе также указано, что измерения времени пролета следует производить в направлении, перпендикулярном направлению стальной арматуры. Концентрация арматуры по пути распространения волны должна быть менее 5%. Допускаются измерения вдоль пути, параллельного направлению стальной арматуры, если расстояние между дорожкой и стальной поверхностью больше одной шестой измеренной длины.
В СТН также указано, что предпочтительны измерения, перпендикулярные направлению армирования.В этом случае влияние стальных стержней незначительно, если концентрация стали S не равна
где | |
где |
В спецификации RILEM представлены несколько разные формулы для эффектов параллельного и перпендикулярного армирования.
Словацкий стандарт строго ограничивает измерение скорости, если путь параллелен направлению армирования. В таких случаях преобразователи должны располагаться вне зоны влияния арматуры. Предполагаемая зона воздействия представляет собой цилиндрическую поверхность с приблизительным диаметром 1/6.
Общее сравнение стандартов скорости
- Большинство исследованных ультразвуковых эталонов были выпущены более десяти лет назад. Это может указывать на отсутствие прогресса в ультразвуковом испытании бетона.
Помимо общего сходства, общего сходства меньше. Например, DIN / ISO ближе к ASTM, чем к другим. Точно так же BS и RILEM очень похожи друг на друга, а STN и ГОСТ похожи.Причины такого сходства, вероятно, имеют географический и / или политический характер. Например, венгерская спецификация 1994 г. больше не показывает зависимости от российских спецификаций.
ASTM, DIN / ISO и венгерские спецификации довольно компактны. Они больше концентрируются на спецификации измерения времени прохождения. Другие стандарты также предоставляют подробные сведения для оценки прочности бетона по скорости импульса, а также для оценки других свойств бетона, таких как упругие постоянные, обнаружение дефектов и определение однородности бетона.Еще одна причина большой длины британского стандарта заключается в том, что многие формулы представлены и объяснены, как в учебнике.
Возражения
- Многие положения и спецификации в анализируемых стандартах поддерживаются литературой, но не все. Было бы слишком долго обсуждать это всесторонне, поэтому иллюстрация ограничена предыдущими работами авторов этой статьи.Например, было показано (2, 3), что допущение, что скорость импульса не зависит от размера и формы образца, длины пути, частоты и напряжений в бетоне, приемлемо, но только в первом приближении.
Гораздо важнее с инженерной точки зрения главное возражение авторов против анализируемых стандартов. Дело в том, что стандарты не предупреждают пользователя о подводных камнях. оценки свойств бетона по скорости продольного импульса.В большинстве стандартов перечислено около полдюжины возможных применений этого ультразвукового испытания, таких как оценка прочности, упругих констант, обнаружение дефектов и т. Д., Часто дополняемых формулами. Однако ни один из стандартов не оценивает эти применения по их надежности. Это прискорбно, потому что создается впечатление, что тест скорости импульса одинаково подходит для всех этих приложений, что не так (4,5). Фактически, лучшее и, возможно, единственное надежное применение скорости продольного импульса — это (а) проверка однородности бетона и (б) мониторинг изменений в бетоне с течением времени.Оценка прочности возможна только с точностью до 20%, и даже это может быть достигнуто только в строгих лабораторных условиях с установленной калибровочной кривой. Эта низкая точность не может быть улучшена путем дополнения измерения скорости импульса другими тестами, такими как испытание отбойным молотком (6). Другие предлагаемые применения скорости импульса (обнаружение дефектов, измерение глубины трещины и т. Д.) Еще менее надежны.
Очевидно, что нынешнее состояние ультразвукового контроля бетона требует улучшения.Первым шагом к этому может быть предупреждение в стандартах о неопределенностях использования метода стандартизированной скорости продольного импульса. Дальнейшее улучшение должно происходить от лучшего понимания теории распространения ультразвуковых импульсов в бетоне. Это может привести к использованию поверхностных и других направленных волн, а также передовых методов обработки сигналов (7,8). К сожалению, эти авторы не знают никаких стандартов, касающихся таких тестов.
Выводы
- Восемь проанализированных стандартов и спецификаций показывают значительное сходство в измерении времени прохождения ультразвуковых продольных импульсов в бетоне.Тем не менее. есть и отличия. Некоторые стандарты предоставляют более подробную информацию о приложениях скорости импульса, таких как оценка прочности, обнаружение дефектов и т. Д. Однако было установлено, что точность большинства этих приложений, включая оценку прочности, является неприемлемо низкой. Поэтому рекомендуется, чтобы будущие стандарты оценивали надежность приложений.
Отсюда также следует, что современное состояние ультразвукового контроля бетона нуждается в улучшении.Поскольку дальнейшее улучшение может быть достигнуто за счет использования поверхностных и других направленных волн, передовых методов обработки сигналов и т. Д., Разработка стандартов для них является своевременной.
Благодарность
Эта статья частично спонсировалась Американо-словацкой программой по науке и технологиям.
Список литературы
- Теодору, Г., Zerstorungsfreie Betonprufungen (неразрушающий контроль бетона), Beton-Verlag, Дюссельдорф, 1989.158 с.
- Поповикс С., Роуз Дж. Л. и Поповикс Дж. С. «Поведение ультразвуковых импульсов в бетоне», Cement annul Concrete Research, Vol. 20, No. 2, 1990. С. 259 — 270.
- Поповичс, С., Поповицс, Дж. С., «Влияние напряжений на скорость ультразвукового импульса в бетоне», Материалы и конструкции — Исследования и испытания, RILEM, Vol. 24, No. 139, Paris, January 1991. pp. 15–23.
- Поповичс, С., Поповикс, Дж. С., «Неправильное применение стандартного метода измерения скорости ультразвукового импульса для испытания бетона», Технология конструкционных материалов — конференция по неразрушающему контролю, Scancella, R.Дж., Каллахан, М. Э. (Редакторы), Technomic, Атлантик-Сити, Нью-Джерси, 23–25 февраля 1994 г., стр. 241–246.
- Popovics, S., и Popovics, J. S., «Критика метода измерения скорости ультразвукового импульса для испытания бетона», Неразрушающий контроль бетонных элементов и конструкций, F. Ansari and S. Strue, Editors, Proc. ASCE, Сан-Антонио, апрель 1992 г., стр. 94–103.
- Поповичс, С., «Статистическое определение дельты дельты сопротивления кальцеструццо медианте ла Велосита дельи Импульси в Америке» (Современное состояние определения бетона. Сила по скорости импульса в Америке), II Cemento, Anno 83 °, No.3, июль сентябрь 1986. С. 1 17-128.
- Поповичс С. и Поповикс Дж. С. «Потенциальные ультразвуковые методы, основанные на поверхностных волнах и затухании для оценки повреждений в бетоне — обзор», «Диагностика бетонных конструкций», Т. Явор, редактор, Proceeding of the International RILEM — IMEKO Конференция, Experteentrum, Братислава, 1991. С. 101–104.
- Поповикс, Дж. С., «Подходят ли передовые ультразвуковые методы для бетона? — Исследовательское исследование», Труды, неразрушающая оценка строительных конструкций и материалов, Б.А. Супренант и др., Редакторы, Университет Колорадо, Боулдер, Колорадо, октябрь 1990 г., стр. 327 — 339.
Ссылки на другие ресурсы в Интернете по ультразвуковому контролю гражданского / бетонного строительства
© Авторское право 1.