С 1-8. Дефектные инструменты, выявленные в партии, прошедшей приемочный контроль, должны быть заменены.
1.9. Результаты выборочного приемочного контроля распространяются на всю партию.
1.10. При приемочном контроле должны проводиться контроль внешнего вида, размерных параметров и параметров, характеризующих шероховатость поверхностей, качество термообработки и испытания на работоспособность в соответстпин с разд. 2. 3, 4 и 5 настоящего стандарта.
1.11. При периодических испытаниях должны проводиться испытания на стойкость инструмента.
1.12. Периодическим испытаниям подвергаются инструменты, прошедшие приемочный контроль.
1.13. Из всего объема инструментов, одинаковых по конструкции и технологии изготовления, периодические испытания проводятся на одном из наиболее распространенных типоразмеров инструмента.
1. 14. Порядок проведения периодических испытаний должен соответствовать ГОСТ 15.001-73.
2. КОНТРОЛЬ ИНСТРУМЕНТОВ ПО ВНЕШНЕМУ ВИДУ
2.1. Контроль соответствия внешнего вида требованиях стандартов должен быть выборочным.
Для партий менее 280 шт. должен проводиться сплошной контроль.
2.2. Дефекты внешнего вида инструментов разделяются на критические, значительные к малозначительные по ГОСТ 15467-79.
2.2.1. Классификация дефектов указана в табл. I
2.3. План контроля должен соответствовать указанному в табл. 2.
2.3.1. Критические дефекты не допускаются.
2.3.2. Допускается применять другие способы и планы выборочного контроля прн условии, что приемочный уровень качества не должен быть более:
для значительных дефектов — 1%,
для малозначительных дефектов — 4%.
2.4. Партия считается не прошедшей приемочный контроль, если число дефектных инструментов в выборке будет более приемочного числа, указанного в табл.
ГОСТ 23726-79 Инструмент металлорежущий и дереворежущий. Приемка
Текст ГОСТ 23726-79 Инструмент металлорежущий и дереворежущий. Приемка
Цена 3 коп.
ГОСУДАРСТВЕННЫЙ СТАНДАРТ
СОЮЗА ССР
ИНСТРУМЕНТ МЕТАЛЛОРЕЖУЩИЙ
ПРАВИЛА ПРИЕМКИ
ГОСТ 23726-79
Издание официальное
ГОСУДАРСТВЕННЫЙ КОМИТЕТ СССР ПО СТАНДАРТАМ
Москк
РАЗРАБОТАН Министерством станкостроительной и инструментальной промышленности
ИСПОЛНИТЕЛЬ ▲. Д. Мартынов
ВНЕСЕН Министерством станкостроительной и инструментальной промышленности
Член коллегии В. Л. Трефилов
УТВЕРЖДЕН И ВВЕДЕН В ДЕЙСТВИЕ Постановлением Государственного комитета СССР по стандартам от 28 июня 1979 г. N9 2331
УДК 621.9.02:006.354 Группа Г29
ГОСУДАРСТВЕННЫЙ СТАНДАРТ СОЮЗА ССР
ИНСТРУМЕНТ МЕТАЛЛОРЕЖУЩИЙ
Правила приемки
Metalcutting tools Acceptance rules
ГОСТ
23726-79
ОКП 39 0200
Постановлением Государственного комитета СССР по стандартам от 28 июня 1979 г. N9 2331 срок действия установлен
с 01.01. 1981 г. до 01.0Г 1Ш г
Несоблюдение стандарта преследуется по закону
1. ОБЩИЕ ПОЛОЖЕНИЯ
1 1 Для проверки соответствия металлорежущего инструмента требованиям стандартов и технических условий предприятие-изготовитель должно проводить приемочный контроль и периодические испытания
1.2 Приемочному контролю и периодическим испытаниям подлежат инструменты, выпускаемые в серийном и массовом производстве.
1 3 Инструмент к приемке должен предъявляться партиями
1 3 1 Партия должна состоять из инструментов одного типоразмера, изготовленных из одной марки инструментального материала в течение определенного промежутка времени по одному и тому же технологическому процессу.
1 4 Методы контроля и испытаний должны соответствовать указанным в стандартах и технических условиях на конкретные виды инструмента
1 5 При приемочном контроле и периодических испытаниях должен применяться выборочный и сплошной контроль в соответствии с требованиями настоящего стандарта
Контроль отдельных параметров должен быть сплошным при наличии соответствующих требований в стандартах на конкретные виды инструмента
Издание официальное ★
Перепечатка воспрещена © Издательство стандартов, 1979
1. 6. Правила отбора инструмента в выборку при выборочном контроле должны соответствовать ГОСТ 18321—73.
1.7. При применении статистического приемочного контроля порядок проведения контроля должен соответствовать ГОСТ 18242—72.
1.8. Дефектные инструменты, выявленные в партии, прошедшей приемочный контроль, должны быть заменены.
1.9. Результаты выборочного приемочного контроля распространяются на всю партию.
1.10. При приемочном контроле должны проводиться контроль внешнего вида, размерных параметров и параметров, характеризующих шероховатость поверхностей, качество термообработки и испытания на работоспособность в соответствии с разд. 2, 3, 4 и 5 настоящего стандарта.
1.11. При периодических испытаниях должны проводиться испытания на стойкость инструмента.
1.12. Периодическим испытаниям подвергаются инструменты, прошедшие приемочный контроль.
1.13. Из всего объема инструментов, одинаковых по конструкции и технологии изготовления, периодические испытания проводятся на одном из наиболее распространенных типоразмеров инструмента,
1. 14. Порядок проведения периодических испытаний должен соответствовать ГОСТ 15.001—73.
2. КОНТРОЛЬ ИНСТРУМЕНТОВ ПО ВНЕШНЕМУ ВИДУ
2.1. Контроль соответствия внешнего вида требованиям стандартов должен быть выборочным.
Для партий менее 260 шт. должен проводиться сплошной контроль.
2.2. Дефекты внешнего вида инструментов разделяются на критические, значительные и малозначительные по ГОСТ 15467—79.
2.2.1. Классификация дефектов указана в табл. 1
2.3. План контроля должен соответствовать указанному в табл. 2.
2.3.1. Критические дефекты не допускаются.
2.3.2. Допускается применять другие способы и планы выборочного контроля при условии, что приемочный уровень качества не должен быть более:
для значительных дефектов— 1%,
для малозначительных дефектов — 4%.
2.4. Партия считается не прошедшей приемочный контроль, если число дефектных инструментов в выборке будет более приемочного числа, указанного в табл. 2.
Таблица 1
Наименование класса дефектов внешнего вида инструментов | Примеры |
Критические дефекты | Отсутствие конструктивных элементов (например, отсутствие вставных ножей, заточки и т п), трещины, свищи в месте сварки, видимым разрыв слоя припоя более 50% общей длины по контуру пайки, отсутствие маркировки, неправильная маркировка и т п |
Значительные дефекты | Сколы, притупления и прижеги на режгущих кром ках, забоины, коррозия и другие повреждения на базирующих и рабочие поверхностях, существенно влияющие на использование инструмента, видимый разрыв слоя припоя в пределах 10—50% общей длины по контуру пайки, отсутствие защитных покрытий и г и |
Малозначительные дефекты | Нечеткая маркировка, нс нарушающие работоспособности инструмента забоины, коррозии и другие повреждения поверхностей, наплывы припоя и т п |
Таблица 2
Объем партии, шт | Объем выборки шт | Приемочные числа | |
Значите гьные де1| екты | Малотиачите тьные дефекты | ||
281 — 500 | 80 | 2 | 7 |
501 — 1200 | 125 | 3 | 10 |
1201 — 3200 | 200 | 5 | 14 |
3201 — 10000 | 315 | 7 | 21 |
10001 — 35000 | 500 | 10 | 21 |
3. КОНТРОЛЬ ИНСТРУМЕНТОВ ПО РАЗМЕРНЫМ ПАРАМЕТРАМ И
ПАРАМЕТРАМ, ХАРАКТЕРИЗУЮЩИМ ШЕРОХОВАТОСТЬ ПОВЕРХНОСТЕЙ
3.1 На соответствие размерных параметров и параметров, характеризующих шероховатость поверхностей следует проверять партии, прошедшие контроль по разд. 2 настоящего стандарта
3.1.1. Контроль должен быть выборочным.
3.1 2 Для партий менее 50 шт должен проводиться сплошной контроль.
3 2 Дефекты размерных параметров и параметров, характеризующих шероховатость поверхностей, разделяются па значительные и критические по ГОСТ 15467—79
3 2.1. Классификация значительных дефектов указана в табл. 3.
Табтица3
Группа | Наименование параметров | Значения предельных нарушении допустимых отклонений параметров |
1 | Диаметр рабочей части инстру ментов для обработки отверстий (кроме сверл общего назначения, разверток с припуском под довод ку и зенкеров под черновые раз вергки) и шпоночных пазов, элементы резьбы у метчиков резь бонарезных фрез этементы про фнля инструмента работающего по методу огибания Размеры посадочных цилиндри ческих отверстий, элементов кони ческих поверхностен хвостовиков и отверстий (угол, непрямолиней иость, некруглость конуса), разме ры, влияющие на взаимозамепяс мость деталей сборных инструментов | Для линейных размеров свыше 3 мм — величины допустимых погрешностей измерения по ГОС1 8 051—73 Для линейных размеров до 3 мм — 50% от допуска Для мгЛовых размеров концевого инструмента с диаметром рабочей части до 3 мм — 100% от допуска и для осталь ных угловых размеров — 35% от допуска |
2 | Цчаадетр рабочей части сверл общего назначения, разверток с припуском под доводку, зенкеров под черновые развертки Параметры, определяющие по грешности формы и расположения поверхностей инструмента | 50% от допуска |
Размеры цилиндрических хвое тоников, элементы конических хвостовиков не вошедшие в груп пу I размеры квадратов, повод ков лысок, посадочные размеры паз^в под вставные ножи разме ры центровых отверстий, шпоночных пазов, крепежных отверстий и пазов и т п | Для линейных размеров — 50% от допуска Для угловых размеров конне-вого инструмента с диаметром рабочей части до 3 мм — 100% от допуска Для остальных угчовых размеров — 35% от допуска | |
Шероховатость рабочих поверх ностея инструмента невосстанав ливаемых (непере^аччваемых) при эксп туатации поверхностей бази рующих элементов | 40% от наибольшего допус тимого значения | |
3 | Шероховатость остальных (поверхностен (не вошедших в труп пу 2) | 60% от наибольшего допустимого значения |
Размеры режущей части инст ру мечта, |
Продолжение табл. 5
Группа | Наименование параметров | Значения предельных нарушений допустимых отклонений параметров | |
3 | Размеры главных и вспомогательных углов, величины обратной конусности, величины затьг-лования, диаметр и утолщение сердцевины, размеры стружколо-маюших канавок и стружечных отверстий, размеры ленточек, поверхностей, образующих режущие кромки и т. п. | Для линейных размеров — 50% от допуска Для угловых размеров концевого инструмента с диаметром рабочей части до 3 мм— 100% от допуска. Для остальных угловых раз * меров — 30% от допуска. | |
4 | Размеры с неуказанными и большими допусками: габаритные раз-мсры, длина рабочей части, диаметр и длина шеек; размеры выточек, фасок; размеры, не влияющие на взаимозаменяемость деталей сборных инструментов и т. п. |
3 2.2. В случаях, когда нарушения допустимых отклонений превышают указанные в табл. 3, дефекты считаются критическими. Критические дефекты не допускаются.
3.3. План контроля должен соответствовать указанному в табл. 4.
Таблица 4
Объем партии, шт. | Объем выборки, шт | Приемочное число | |||
Группа дефектных параметров | |||||
1 | О | з | 4 | ||
51 — 90 | 13 | 0 | 0 | 1 | 1 |
91 — 150 | 20 | 0 | 1 | 1 | 2 |
151 — 280 | 32 | 1 | 1 | 2 | 2 |
281 — 500 | 50 | 1 | 2 | 3 | 5 |
501 — 1200 | 80 | 2 | 3 | 5 | 7 |
1201 — 3200 | 125 | 3 | 5 | 7 | 10 |
3201 — 10000 | 200 | 5 | 7 | 10 | 14 |
10001 — 35000 | 315 | 7 | 30 | 14 | 21 |
3. 3.1. Допускается применять другие планы выборочного контроля при условии, что приемочный уровень качества должен быть не более:
для группы дефектов 1 …. 1,0 то же 2 …. 1,5
3.4. Проверка должна производиться по каждому параметру в отдельности.
Проверка по каждому последующему параметру производится только при получении положительных результатов контроля по предыдущему параметру.
3.5. Партия считается не прошедшей контроль, если число дефектных инструментов в выборке будет более приемочного числа, указанного в табл. 4.
4. КОНТРОЛЬ ИНСТРУМЕНТОВ ПО ПАРАМЕТРАМ, ХАРАКТЕРИЗУЮЩИМ
КАЧЕСТВО ТЕРМООБРАБОТКИ
4.1. На соответствие параметров, характеризующих качество термообработки, требованиям стандартов следует проверять партии, прошедшие контроль по разделам 2 и 3 настоящего стандарта
4.2 1. Контроль должен быть выборочным.
4.2. От каждой партии инструмента проверяется случайная выборка.
Объем выборки должен соответствовать указанному в табл. 5.
Таблица 5
Объем партии, | ш г | ||
Контролируемые параметры | 20-500 | 501-1200 | Св 1200 |
Объем выборки, шт , не менее | |||
Параметры, при проверке которых нарушается целость инструмента | 2 | 3 | 5 |
Параметры, при проверке которых не нарушается целость инструмента | 1 % от партии, но не менее 5 и не более 20 инструментов |
П р имечание Если количество инструментов в партии менее 20 шт., то при проверке параметров, при которой не нарушается целость инструмента должен применяться сплошной контроль Проверки параметров, требующие нарушения целости инструмента в оюм случае допускается не проводить
4 3. Партия инструмента не принимается, если количество инструментов, не соответствующих требованиям стандарта, 2 и более.
4. 4. При обнаружении в первой выборке одного инструмента несоответствующего требованиям стандарта, из партии отбирается вторая выборка того же объема.
Если во второй выборке будет обнаружен хотя бы один инструмент, не соответствующий требованиям стандарта, партия не принимается
5. ИСПЫТАНИЯ НА РАБОТОСПОСОБНОСТЬ
5.1. Испытаниям на работоспособность следует подвергать партии инструментов, прошедшие контроль в соответствии с требованиями разделов 2, 3 и 4 настоящего стандарта.
5.2. От каждой партии инструмента испытывается случайная выборка. Объем выборки должен соответствовать указанному в табл. 7.
Таблица 7
Объем партии, шт. | Объем выборки, шг , не менее |
100 — 500 | 2 |
501 — 1200 | 3 |
1201 — 3200 | 4 |
Св. 3200 | 5 |
5.3. Партия считается не выдержавшей испытания, если количество инструментов, не выдержавших испытания, больше или равно двум.
5.3.1. При обнаружении в выборке одного инструмента, не выдержавшего испытаний, из партии извлекается вторая выборка того же объема.
В этом случае, партия считается не выдержавшей испытания, если во второй выборке хотя бы один инструмент не выдержит испытаний.
Редактор А Л. Владимиров Технический редактор Л. Б Семенова Корректор А. Г. Старостин
Сдано в набор 16 07 79 Подп в печ 13 09 79 0,5 п л 0,057 уч -изд л Доп тираж 19000 Цеча 3 коп
Ордена «Знак Почета» Издательство стандартов. 123557, Москва, Новопресненский пер 3 Калужская типография стандартов, ул. Московская 256. Зак. 198ь
Изменение № 1 ГОСТ 23726—79 Инструмент металлорежущий. Правила приемки
Постановлением Государственного комитета СССР по стандартам от 10.11.86 № 3406 срок введения установлен
с 01.10.86
Пункты 1.7, 1,8 исключить.
Пункт 1.10 дополнить абзацами: «Если при приемочном контроле установлено несоответствие стандарту более чем по одному из контролируемых параметров хотя бы одного инструмента или по одному параметру у двух и более инструментов, вся партия не принимается.
(Продолжение см. с. 146)
Если установлено несоответствие стандарту по одному из контролируемых параметров одного инструмента, контролю подвергается удвоенное количество инструмента из той же партии по всем контролируемым параметрам. Если в повторной выборке будет обнаружен хотя бы один инструмент, не соответствующий требованиям стандарта, вся партия не принимается».
Пункт 2,1 дополнить абзацем: «Для партии более 280 шт. должен проводиться выборочный контроль».
Пункты 2.2, 2.2.1 и таблицу 1 исключить.
Пункт 2.3 изложить в новой редакции: «2.3. Объем выборки должен соответствовать значениям, указанным в табл. 2,
(Продолжение см. с. 147)
Таблица 2
Объем партии, шт | Объем выборки, шт |
281—500 | 80 |
501—1200 | 125 |
1201—3200 | 200 |
3201—10000 | 315 |
10001—35000 | 500 |
Пункты 23 1, 23 2, 2 4, 3 2, 321,322 исключить
Пункт 3 3 изложить в новой редакции. «3 3 Объем выборки должен соответствовать значениям, указанным в табл 4
(Продолжение см с. 148)
(Продолжение изменения к ГОСТ 23726—79)
Таблица 4
Объем г ар гии, шт. | Объем выборки, шт. | Объем партии, шт. | Объем выборки, шт. |
51—90 | 13 | 501—1200 | 80 |
91—150 | 20 | 1201—3200 | 125 |
151—280 | 32 | 3201—10000 | 200 |
281—500 | 50 | Ю001—35000 | 315 |
Пункты 3.3.1, 3.5, 4.3, 4.4 исключить.
Пункт 5.2. Таблицу 7 дополнить показателями (перед значениями 100—500):
Объем партии, шт.
Объем выборки, шт.
До 100
Пункы 5.3, 5.3.1 исключить.
(ИУС № 2 1987 г.)
Изменение № 2 ГОСТ 23726—79 Инструмент металлорежущий. Правила приемки
Утверждено и введено в действие Постановлением Государственного комитета СССР по стандартам от 14 05.87 № 1595
Дата введения 01.11.87
Раздел 1 дополнить пунктами —1.7, 18 «1.7 При применении статистичес
кого приемочного контроля порядок проведения контроля должен соответствовать ГОСТ 18242—72
(Продолжение см. с. 154)
1.8. Дефектные инструменты, выявленные в партии, прошедшей приемочный контроль, должны быть заменены».
Пункт 1.10. Предпоследний, послед -шй абзацы исключить.
Пункт 1.11 дополнить словами и абзацем: «(на средний и установленный периоды стойкости или среднюю наработку на отказ и установленную безотказную наработку).
(Продолжение см. с. 155}
Объемы выборок и периодичность проведения испытаний указывают в нор-ыати1 чо-технической документации на инструменты конкретного вида»*
Пункт 2.1. Последний абзац исключить.
Раздел 2 дополнить пунктами — 2.2, 2,2.1: «2.2. Дефекты внешнего вида инструментов разделяются на критические и малозначительные по ГОСТ 15467—79. 2.2.1. Классификация дефектов указана в табл. К
Таблица 1 | |
Наименование класса дефектности внешнего вида инструментов | Виды дефектов |
Критические дефекты | Отсутствие конструктивных элементов, отсутствие заточки Трещины и свищи на сварном соединении Разрывы слоя припоя, на -0% превышающие допустимые в стандартах на инструмент Отсутствие маркировки или неправильная маркировка Сколы и притупления на режущих кромках величиной более нормативного износа Трещины Забоины на базирующих поверхностях, существенно влияющие на использование инструмента Зазор у сборного инструмента между нижней опорной поверхностью гнезда державки и опорной пластиной под вершиной Наплывы припоя, влияющие на работоспособность инструмента Качание сегментов на дисках пил и твердосплавных пластин в гнездах корпусов |
Малозначительные дефекты | Нечеткая и неровная маркировка Забоины, не нарушающие работоспособность инструмента Наплывы припоя, не нарушающие товарный вид и работоспособность инструмента Разрывы слоя припоя, не превышающие 50 % от допустимых в стандартах на инструмент Неоднородный цвет поверхностей износостойкого покрытия, нанесенного методом КИБ, поверхности, обработанной низкотемпературным отпуском и в атмосфере перегретого водяного пара или после промывки в горячем нитридно-содовом растворе Притупления режущей кромки не более 0,15 мм на 15 % длины режущей кромки Наличие черновин на нерабочих и небазовых поверхностях общей площадью не более 10 % указанных поверхностей |
Пункт 2. 3 излржить в новой редакция: «2,3* План контроля должен соот-ветствовать указанному в табл. 2*
Таблица 2
Приемочное число | |||
Объем партии, шт. | Объем вьборки, | ||
шт. | Критические | Малозначительные | |
дефекты | дефекты | ||
281—500 | 80 | 5 | |
501—1200 | 125 | 0 | 7 |
1201—3200 | 200 | Ю | |
31201—10000 | 315 | 14 | |
100 Э1—35000 | 50С | 21 |
Раздел 2 дополнить пунктом — 2.4:
«2.4. Партия считается прошедшей приемочный контроль, если число дефектов в выборке меньше или равно приемочному числу, указанному в табл, 2, и партия считается не прошедшей приемочный контроль, если число дефектов в выборке более приемочного числа».
Раздел 3 дополнить пунктами — 3.2, 3.2,1, 3.2.2: «3.2, Дефекты размерных параметров и параметров, характеризующих шероховатость поверхностей, разделяются на значительные и критические по ГОСТ 15467—79.
3.2. J. Классификация значительных дефектов указана в табл* 3.
3.2.2. В случае, когда нарушения допустимых отклонений превышают указанные в табл. 3, дефекты считают критическими.
Таблица 3
Группа | Наименование параметров | Значение допустимых отклонений |
1 | Диаметр рабочей части сверл класса | Для линейных разме- |
точности А и А1, разверток (кроме | ров до 3 мм — 60 % | |
разверток с припуском под доводку), зенкеров, шпоночный фрез | допуска | |
Толщина рабочей части прорезных | Для линейных разме- | |
фрез, фрез для сегментных шпонок и | ров свыше 3 мм — 35% | |
Т-образных пазов | допуска | |
Элементы резьбы метчиков, резьбовых | Для угловых разме- | |
фрез, плоских накатных плашек, гребенок и плашек к резьбонарезным головкам, накатных роликов Размеры посадочных цилиндрических отверстий, цилиндрического хвостовика сверл, разверток, концевых фрез н резцов для станков с ЧПУ, угла и большого диаметра конуса Морзе | ров — 35 % допуска | |
Радиальное и торцовое биение рабочей части сверл и прямолинейность сверл диаметром до 3 мм классов точности А и А1 и для станков с ЧПУ, биение режущей и калибрующей части метчиков и разверток, радиальное биение концевых фрез, торцовое биение чистовых торцовых фрез | 35 % допуска |
(Продолжение изменения к ГОСТ 28726—79)
Груява
Наименование параметра
Продолжение табл.

Значение допустимых отклонений
2
Диаметр рабочей части сверл классов точности В я BI и сверл с утолщенным хвостовиком, разверток с припуском под доводку, наружный диаметр круглых плашек
Ширина трехсторонних фрез
Высота вершины резца и расстояние от вершины резца до боковой поверхности
Обратная конусность рабочей части сверл
Угол наклона резьбы конических метчиков
Диаметр рабочей и зажимной части центровочных сверл
Размеры цилиндрических и элементы конических хвостовиков, не вошедшие в группу I, размеры квадратов поводков, лысок и лапок
Посадочные размеры пазов под вставные ножи, посадочные размеры ножей сборного инструмента, шпоночных пазов, крепежные отверстия для насадного инструмента, элементы крепления сменных неперетачиваемых пластин, размеры рифлений ножей и корпусов фрез
Радиальное и торцовое биение и прямолинейность сверл диаметром до 3 мм класса точности В и В1, сверл с утолщенным хвостовиком и сверл центровочных
Прямолинейность в поперечном направлении ножовочных полотен и прямолинейность линии вершин зубьев ножовочных полотен и ленточных пил, плоскостность опорных поверхностей ножей листовых ножниц
Радиальное и торцовое биение фрез дисковых, фасонных, угловых, отрезных и прорезных, цилиндрических, черновых торцовых и резьбовых
Радиальное и торцовое биение пил дисковых сегментных
50 % допуска
До 0,12 мм на 100 мм длины для сверл из инструментальных сталей и твердого сплава 100 °/о допуска на длине пластины твердого сплава
До 0,13 мм на 10 мм длины для сверл центровочных комбинированных
50 % допуска
10 % допуска
50 % допуска
50% допуска
50 % допуска
50 % допуска
(Продолжение изменения к ГОСТ 23726—79)
Продолжение табл. 3
Группа
2
3
Наименование параметров
Значение допустимых отклонений
Биение по нормали к профилю фрез дисковых модульных
Торцовое биение опорных торцов насадного инструмента, биение круглых плашек
Геометрические параметры режущих поверхностей, не восстанавливаемые при переточках (передние и задние углы, углы в плане, задние углы затылован-ного инструмента, углы поднутрения)
Шероховатость рабочих поверхностей инструмента, не восстанавливаемых при эксплуатации и посадочных (базирующих) поверхностей (поверхностей направляющих ленточек сверл, разверток, зенкеров, ленточек фрез отрезных, опорных поверхностей резцов и т. п.)
Диаметр отрезных н прорезных фрез и пил сегментных, толщина отрезных фрез и пил сегментных
Диаметр ступицы дисковых и отрезных фрез
Разность по высоте вершин смежных зубьев ножовочных полотен и ленточных
пил
Толщина круглых плашек
50 % допуска
Е 0 % допуска
4 0 % предельного пустимого значения
50 % допуска
до-
Толщина и утолщение сердцевины сверл, ширина пера сверл, метчиков н круглых плашек
Ширина ленточек сверл, ширина фасок трехсторонних фрез
Элементы заборного конуса, передний и задний угол круглых плашек
Прямолинейность режущих кромок сверл
Прямолинейность в продольном направлении ножовочных полотен
Размеры и расположение стружкоразделительных канавок для концевых обдирочных фрез
Обратная конусность инструмента, не вошедшего в группу 2, конусность рабочей части
Геометрические параметры режущих поверхностей, восстанавливаемых при переточках (передний н задний углы главной режущей кромки фрез отрезных и прорезных, пил сегментных н запасных сегментов)
Величина разводки зубьев ножовочных полотен и ленточных пил
50 % допуска
50 % допуска
Для инструмента диаметром до 3 мм—100% допуска,
для остальных — 30 % допуска
30 % допуска
Продолжение табл. 9
Группа | Наименование параметров | Значение допустимых отклонений |
3 | Расположение и диаметр поводковых отверстий. | 5 0 % допуска |
Симметричность осей отверстий* ножовочных полотен относительно оси, симметричность фиксирующего гнезда круглых плашек, симметричность торцовых кромок относительно торцов ступицы трехсторонних фрез | 50 % допуска | |
Габаритные размеры и размеры рабочих частей, кроме указанных в группах 1 н 2. | 50 % допуска | |
Шероховатость поверхностей, не во | 40 % предельного до* | |
шедших в группу 2 | пустимого значения |
Пункт 3.3 изложить в новой редакции: «3.3. План контроля должен соответ* ствовать указанному в табл 4.
Таблица 4
Объем партии, шт. | Объем выборки, шт. | Приемочное число | |||
Критические дефекты | Зна Группа 1 | ч и тельные дефе дефектных пар 2 | кты аметров 3 | ||
51—90 | 13 | 0 | 0 | 1 | |
91—150 | 20 | 0 | 1 | 1 | |
151 —2*80 | 32 | 1 | 1 | 2 | |
281—500 | 50 | 0 | 1 | 2 | 3 |
501—1200 | S0 | 2 | 3 | 5 | |
1201—3200 | 125 | 3 | 5 | 7 | |
3201—10000 | 200 | 5 | 7 | Ю | |
10001—35000 | 315 | 7 | 10 | 14 |
Раздел 3 дополнить пунктами — 3. 3.1, 3.5: <3.3.1, Переход на ослабленный или усиленный контроль следует осуществлять в случаях, предусмотренных ГОСТ 18242—72 при условии, что приемочный уровень качества должен быть не более:
1,0 ….. . для группы дефектов 1
1.5 » * > 2
2.5 …..* > » > 3.
3,5. Партия считается прошедшей приемочный контроль, если число дефектов в выборке меньше или равно приемочному числу, указанному в табл, 4, и партия считается не прошедшей приемочный контроль, если число дефектов в выборке более приемочного числа».
Пункт 4.2Л дополнить словами: «по двухступенчатому плану».
Пункт 4.2. Таблицу 5 изложить в новой редакции:
Таблица 5
Объем партии, шт. | Объем выборки, шт. | |
Параметры, при проверке которых нарушается целость инструмента | Параметры, при проверке которых не нарушается целость инструмента | |
26—50 | 2 | 3 |
51—90 | 2 | 3 |
91—150 | 2 | 5 |
151—280 | 3 | 8 |
281-500 | э | 8 |
501—1200 | 3 | 13 |
Св. | 8 | 20 |
примечание. Заменить значение: 20 на 26,
Раздел 4 дополнить пунктом —4.3:
«4.3. Партия считается прошедшей приемочный контроль, если в первой выборке нет дефектов. В случае, если в первой выборке обнаружен один дефект, из партии отбирается вторая выборка того же объема,.
Партия считается прошедшей приемочный контроль, если во второй выборке нет дефектов, зи партия считается не прошедшей приемочный контроль, если во второй выборке обнаружен хотя бы один дефект»,
Пункт 5.1 дополнить словами: «Контроль должен быть выборочным по двухступенчатому плану».
Пункт 5.2. Таблица 7. Графа «Объем выборки, шт., не менее». Заменить значение: 4 на 5;
дополнить примечанием:
«Примечание. При объеме партии менее 50 шт. испытания на работоспособность допускается не проводить».
Раздел 5 дополнить пунктом — 5 3: «5.3. Партия считается прошедшей приемочный контроль, если в первой выборке все инструменты выдержали испытания. В случае, если в первой выборке один инструмент не выдержал испытаний, из партии отбирается вторая выборка того же объема.
Партия считается прошедшей приемочный контроль, если во второй выборке все инструменты выдержали испытания, и г артия считается не прошедшей приемочный контроль, если во второй выборке хотя бы один инструмент не выдержал испытания».
(ИУС № 8 1987 г.)
Из мнение № 3 ГОСТ 23726—79 Инструмент металлорежущий. Правила приемки
Утверждено и введено в действие Постановлением Государственного комитета СССР по стандартам от 20.07.S8 № 2695
Дата введения 01.02.89
Наименование стандарта изложить в новой редакции: «Инструмент металлорежущий и дереворежущий. Приемка
Metalcutting and woodcutting. Acceptance».
Пункт 1.1 после слова «металлорежущего» дополнить словами: «и дереворежущего».
Пункт 1Л0 после слов «при приемочном контроле» дополнить словами: «металлорежущего инструмента»;
дополнить абзацем «При приемочном контроле дерево режущего инструмента должен проводиться контроль внешнего вида, размерных параметров, параметров шероховатости поверхностей, качества термообработки и прочности в соответствии с пп. 2, 3, 4 и б».
Пункт 1.11 после слов «установленную безотказную наработку» дополнить словами, «или средний и установленный ресурс».
Пункт 2 1 изложить в новой редакции: «2.1. Контроль соответствия внешнего вида требованиям стандартов должен быть выборочным.
Для партий мел аллорежущего инструмента менее 280 шт., а дереворежущего инструмента, напильников, надфилей и рашпилей менее 90 шт. проводят сплошной контроль».
Пункт 2.2.1. Таблица 1. Текст после слов «Сколы и притупления на режущих кромках» до слов «Забоины на базирующих поверхностях» изложить в новой редакции: «величиной более нормативного износа (кроме напильников, надфилей и рашпилей).
Прижоги на режущих кромках
Трещины
Волосовины, расслоения у дереворежущих пил и ножей
Наличие черновик и следов коррозии на рабочих поверхностях
Наличие выкрошенных зубьев у напильников, надфилей и рашпилей»;
текст после слов «нитридно-содовом растворе» изложить в новой редакции. «Нарушение оксидного покрытия на нерабочих поверхностях
Притупления режущей кромки не более 0,15 мм на 15 % длины режущей кромки металлорежущего инструмента
Наличие черновин и следов коррозии на нерабочих и небазовых поверхностях общей площадью не более 10 % указанных поверхностей
Наличие заусенцев на поверхностях хвостовиков напильников, надфилей и рашпилей
(Продолжение см, с. 132)
131
Наличие на рабочих поверхностях напильников, надфилей и рашпилей з/бь-ев, имеющих неполный профиль, общей площадью не более 1 % указанных по* верхностсй
Отсутствие перекрытия насечек на круглых и выпуклой стороне полукруг* лы\ напильников и надфилей общей площадью не более 1 % от площади насекаемой поверхности
Наличие скола одного зуба на торце носка напильников, надфилей и рашпилей»
Пункты 2 к 33 после слов «План контроля» дополнить словами: «металлорежущею инструмента».
Раздел 2 дополнить пунктом — 2.3а: «2 За, План контроля дереворежущею инструмента, напильников, надфилей и рашпилей должен соответствовать указанному в табл. 2а.
Таблица 2а
Объем партии, шт | Приемочное чисто | ||
С С ‘ см выборки, шт. | критические дефекты | Малое на ни тельные дефекты | |
93 — ’ «0 | 20 | 3 | |
151—28П | 32 | 5 | |
281—50 D | 50 | 0 | 4 |
501—3200 | 80 | V | 10 |
~j 1—3200 | 125 | 1 \ | |
Св. | 200 | 21 |
Пункт 3 12 изложить в новой редакции: «3.1 2. Для партий металлорежущего инструмента, напильников, надфилей и рашпилей менее 50 шт., а для депезоро ,ущею инсгру мента менее 25 шт. должен проводиться сплошной контроль
Пункт 3 2. Заменить слова- «значительные и критические» на «критические, значительные и малозначительные».
Пункт 3 2.1 после слов «Классификация значительных дефектов» дополнить словами: «металлорежущего инструмента».
Пункт 3.2.2. Заменить ссылку; «табл. 3» на «табл. 3, За и 36».
Таблица 3 Заменить наименование графы «Значение допустимых отклонений» на «Предельные значения допустимых отклонений».
Р, гол } дополнить пунктами — 3 2.1л, 3 За: «3.2.1а. Классификация дефектов напильников, рашпилей и надфилей указана в табл. За, дереворежущего инструмента — в табл 36.
(Продолжение см, с. 133)
Цена 3 коп
ОСНОВНЫЕ ЕДИНИЦЫ СИ
Величина | Единица | ||
Наименование | Обозначение | ||
русское | международное | ||
ДЛИНА | метр | X | m |
МАССА | килограмм | кг | kg |
ВРЕМЯ | секунда | с | s |
СИЛА ЭЛЕКТРИЧЕСКОГО ТОКА | ампер | А | А |
ТЕРМОДИНАМИЧЕСКАЯ | |||
ТЕМПЕРАТУРА | К | К | |
КОЛИЧЕСТВО ВЕЩЕСТВА | моль | моль | mol |
СИЛА СВЕТА | кандела | кд | cd. |
ДОПОЛ | НИТЕЛЬНЫЕ 1 | единицы си | |
Плоский угол | радиан | рад | rad |
Телесный угол | стерадиан | ср | sr |
ПРОИЗВОДНЫЕ ЕДИНИЦЫ С И,ИМЕЮЩИЕ СОБСТВЕННЫЕ НАИМЕНОВАНИЯ
Величина | Единица | Выражение производной единицы | ||
наименование | обозначение | через другие единицы СИ | через основные единицы СИ | |
Частота | герц | Гц | — | ©“* |
Сила | НЬЮТОН | Н | — | и-кгс*4 |
Давление | паскаль | Па | Н/м* | м-1 ‘КГ* O’—* |
Энергия, работа, количество теплоты | джоуль | Дж | Нм | м2-юг-с~* |
Мощность, поток энергии | ватт | Вт | Дж/с | мг-кг*с-^ |
Количество электричества, электрический заряд | пулом | Кл | Ас | с-А |
Электрическое напряжение, электрический потенциал | вольт | В | Вт/А | м* -юг-с -«. |
Световой поток | люмен | лм | ■— | кдср |
Освещенность | люкс | лк | — | м~2*кд ср J |
Активность нуклида | беккорель | Бк | —- | С-1 |
Доза излучения | грэй | Гр | — | м2-С“* |
* В эти два выражения входит, наравне с основными единицами СИ, донолшггелытя
единица—стерадиан
Законы :: Изменение N 3 ГОСТ 23726-79 Инструмент металлорежущий. Правила приемкиПостановление Госстандарта СССР от 20.07.1988 N 2695ГОСТ от 1988-07-20 N 23726-79
Группа Г29
ИЗМЕНЕНИЕ N 3
ГОСТ 23726-79 «Инструмент металлорежущий. Правила приемки»
Дата введения 1989-02-01
УТВЕРЖДЕНО И ВВЕДЕНО В ДЕЙСТВИЕ Постановлением Государственного комитета СССР по стандартам от 20. 07.88 N 2695
Наименование стандарта изложить в новой редакции: «Инструмент металлорежущий и дереворежущий. Приемка
Metalcutting and woodcutting. Acceptance».
Пункт 1.1 после слова «металлорежущего» дополнить словами: «и дереворежущего».
Пункт 1.10 после слов «при приемочном контроле» дополнить словами: «металлорежущего инструмента»;
дополнить абзацем: «При приемочном контроле дереворежущего инструмента должен проводиться контроль внешнего вида, размерных параметров, параметров шероховатости поверхностей, качества термообработки и прочности в соответствии с пп.2, 3, 4 и 6».
Пункт 1.11 после слов «установленную безотказную наработку» дополнить словами: «или средний и установленный ресурс».
Пункт 2.1 изложить в новой редакции: «2.1. Контроль соответствия внешнего вида требованиям стандартов должен быть выборочным.
Для партий металлорежущего инструмента менее 280 шт.

Пункт 2.2.1. Таблица 1. Текст после слов «Сколы и притупления на режущих кромках» до слов «Забоины на базирующих поверхностях» изложить в новой редакции: «величиной более нормативного износа (кроме напильников, надфилей и рашпилей).
Прижоги на режущих кромках
Трещины
Волосовины, расслоения у дереворежущих пил и ножей
Наличие черновин и следов коррозии на рабочих поверхностях
Наличие выкрошенных зубьев у напильников, надфилей и рашпилей»;
текст после слов «нитридно-содовом растворе» изложить в новой редакции: «Нарушение оксидного покрытия на нерабочих поверхностях
Притупления режущей кромки не более 0,15 мм на 15% длины режущей кромки металлорежущего инструмента
Наличие черновин и следов коррозии на нерабочих и небазовых поверхностях общей площадью не более 10% указанных поверхностей
Наличие заусенцев на поверхностях хвостовиков напильников, надфилей и рашпилей
Наличие на рабочих поверхностях напильников, надфилей и рашпилей зубьев, имеющих неполный профиль, общей площадью не более 1% указанных поверхностей
Отсутствие перекрытия насечек на круглых и выпуклой стороне полукруглых напильников и надфилей общей площадью не более 1% от площади насекаемой поверхности
Наличие скола одного зуба на торце носка напильников, надфилей и рашпилей».
Пункты 2.3, 3.3 после слов «План контроля» дополнить словами: «металлорежущего инструмента».
Раздел 2 дополнить пунктом — 2.3а: «2.3а. План контроля дереворежущего инструмента, напильников, надфилей и рашпилей должен соответствовать указанному в табл.2а.
Таблица 2а
Объем партии, шт. |
Объем выборки, шт. |
Приемочное число | |
Критические дефекты |
Малозначительные дефекты | ||
91-150 |
20 |
0 |
3 |
151-280 |
32 |
5 | |
281-500 |
50 |
7 | |
501-1200 |
80 |
10 | |
1201-3200 |
125 |
14 | |
Св. |
200 |
21 |
Пункт 3.1.2 изложить в новой редакции: «3.1.2. Для партий металлорежущего инструмента, напильников, надфилей и рашпилей менее 50 шт., а для дереворежущего инструмента менее 25 шт. должен проводиться сплошной контроль».
Пункт 3.2. Заменить слова «значительные и критические» на «критические, значительные и малозначительные».
Пункт 3.2.2 Заменить ссылку: «табл.3» на «табл.3, 3а и 3б».
Таблица 3. Заменить наименование графы «Значение допустимых отклонений» на «Предельные значения допустимых отклонений».
Раздел 3 дополнить пунктами — 3.2.1а, 3.3а: «3.2.1а. Классификация дефектов напильников, рашпилей и надфилей указана в табл.
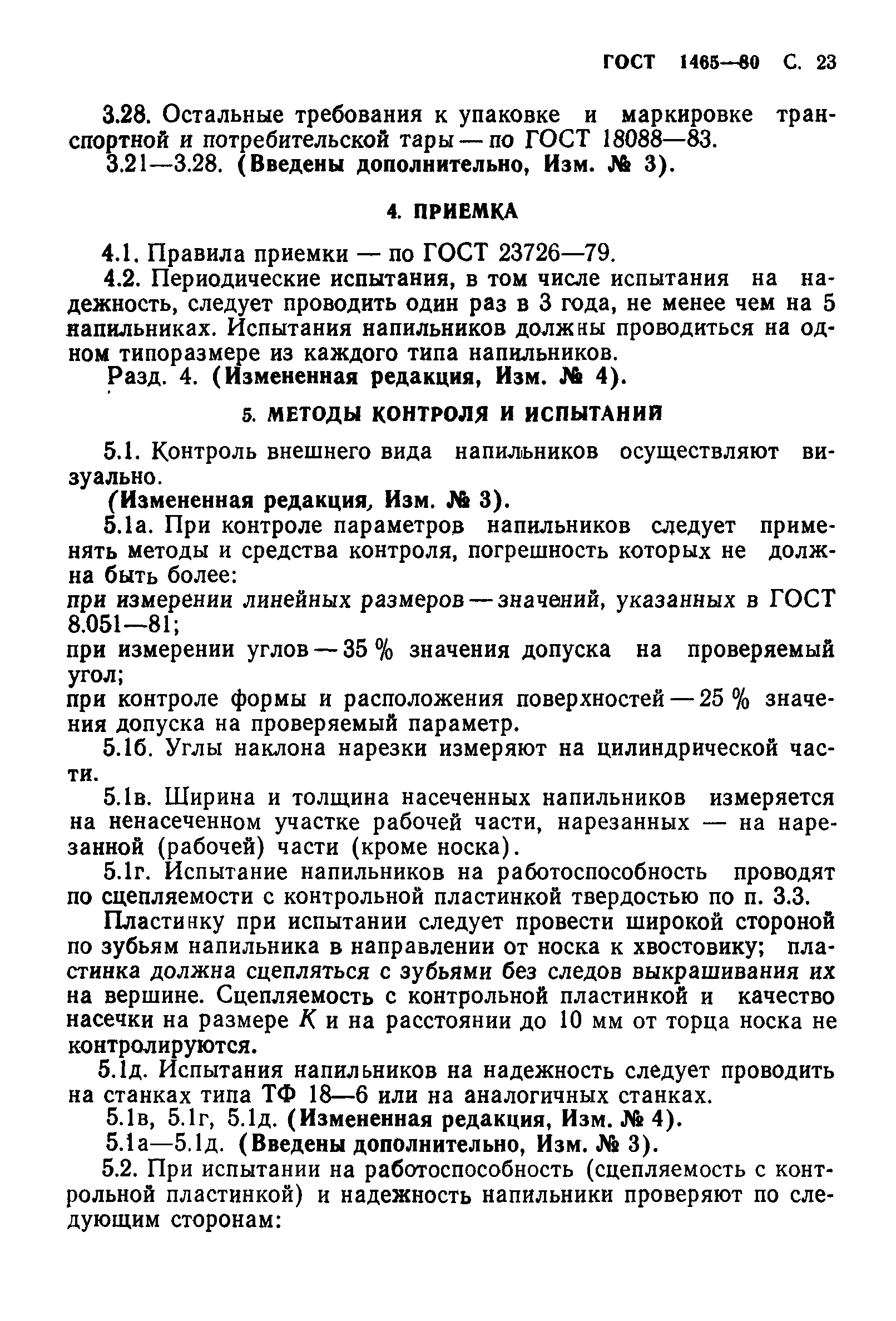
Таблица 3а
Вид дефектов |
Наименование параметров |
Предельные значения допустимых отклонений |
Значительные |
Прямолинейность сторон |
50% допуска |
Симметричность оси хвостовика относительно оси |
25% допуска | |
Передний угол зуба |
1° | |
Малозначительные |
Габаритные размеры и размеры рабочей части |
50% допуска |
Угол наклона нарезки или насечки |
50% допуска | |
Число основных нарезок или насечек на 10 мм длины при количестве насечек менее 14 |
1 насечка | |
Отношение высоты зуба к нормальному шагу основной насечки |
10% допустимого значения | |
Расстояние конца носка напильника до плоскости неоттянутой части |
25% допустимого значения | |
Разность между наибольшим и наименьшим значениями осевого шага основной или вспомогательной насечки |
50% допустимого значения | |
Размеры фасок на ребрах плоских, трехгранных, ромбических, полукруглых и квадратных слесарных напильников |
50% допустимого значения | |
|
50% допуска |
Таблица 3б
Вид дефектов |
Наименование параметров |
Предельные значения допустимых отклонений |
Значительные |
Диаметр посадочного отверстия насадных фрез, комбинированных, круглых, дисковых пил |
Для линейных размеров до 3 мм — 50% допуска; |
Диаметр рабочей части сверл и двузубых концевых фрез |
для линейных размеров свыше 3 мм — 35% допуска; | |
Диаметр цилиндрических хвостовиков сверл и концевых фрез |
||
Ширина режущей части пазовых, проушечных фрез, цепочек |
для угловых размеров — 35% допуска | |
Торцовое и радиальное биение зубьев насадных фрез, комбинированных и дисковых пил с твердосплавными пластинами, заточенных круглых пил Радиальное биение режущих кромок сверл и концевых фрез Торцовое биение опорных торцов насадных фрез Неравномерность толщины ножей, ленточных и круглых пил |
40% допуска | |
Значительные Группа 2 |
Разность двух любых шагов зубьев ленточных, рамных, круглых пил, звеньев цепочек Прямолинейность торцовых поверхностей круглых пил Прямолинейность режущей кромки и Величины вогнутости (выпуклости) поверхностей ленточных, рамных и круглых пил |
50% допуска |
Величины главных и вспомогательных углов |
35% допуска | |
Шероховатость режущих поверхностей фрез, сверл, пил, ножей, цепочек; посадочных отверстий насадных фрез, комбинированных, дисковых и круглых пил; опорных торцов насадных фрез; хвостовиков сверл и концевых фрез |
40% предельного допустимого значения | |
Малозначительные |
Шероховатость остальных поверхностей, не вошедших в группу 2 Следы ударов молотком круглых пил |
60% от наибольшего допустимого значения |
Наружный диаметр насадных и однозубых концевых фрез, комбинированных, дисковых, круглых пил Толщина ножей и круглых пил Величина затылования насадных затылованных фрез, величина обратной конусности сверл и концевых фрез, диаметр и утолщение сердцевины сверл, размеры ленточек, выточек, фасок, крепежных отверстий, шаг спирали сверл Величина выступов твердосплавных пластин над корпусом дисковых пил Размеры с допусками выше 11 квалитета Габаритные размеры рабочих частей, кроме указанных в группах 1 и 2 |
Для линейных размеров — 50% допуска; для угловых размеров — 35% допуска |
Пункт 3. 3а. План контроля напильников, надфилей и рашпилей должен соответствовать указанному в табл.4а, дереворежущего инструмента — в табл.4б.
Таблица 4а
Объем партии, шт. |
Объем выборки, шт. |
Приемочное число | ||
Критические дефекты |
Значительные дефекты |
Малозначительные дефекты | ||
51-90 |
5 |
0 |
0 |
1 |
91-150 |
8 |
0 |
1 | |
151-280 |
13 |
1 |
2 | |
281-500 |
20 |
1 |
3 | |
501-1200 |
32 |
2 |
5 | |
1201-3200 |
50 |
3 |
7 | |
Св. |
80 |
5 |
10 |
Таблица 4б
Объем партии, шт. |
Объем выборки, шт. |
Приемочное число | |||
Критические дефекты |
Значительные дефекты |
Малозначительные дефекты | |||
Группа |
|||||
1 |
2 |
||||
26-50 |
8 |
0 |
0 |
0 |
1 |
51-90 |
13 |
0 |
1 |
2 | |
91-150 |
20 |
1 |
2 |
3 | |
151-280 |
32 |
1 |
2 |
5 | |
281-500 |
50 |
2 |
3 |
7 | |
501-1200 |
80 |
3 |
5 |
10 | |
1201-3200 |
125 |
5 |
7 |
14 | |
3201-10000 |
200 |
7 |
10 |
21 |
Пункт 3. 3.1 изложить в новой редакции: «3.3.1. Допускается применять другие планы выборочного контроля при условии, что приемочный уровень дефектности должен быть не более указанного в табл.4в.
Переход на усиленный или ослабленный контроль осуществляют по ГОСТ 18242-72*.
_______________
* На территории Российской Федерации действует ГОСТ Р ИСО 2859-1-2007, здесь и далее по тексту. — Примечание изготовителя базы данных.
Таблица 4в
Вид инструмента |
Приемочный уровень дефектности | |||
Значительные дефекты для групп |
Малозначительные дефекты | |||
1 |
2 |
3 |
||
Металлорежущий инструмент |
1,0 |
1,5 |
2,5 |
— |
Напильники, надфили и рашпили |
2,5 |
6,5 | ||
Дереворежущий инструмент |
1,5 |
2,5 |
— |
6,5 |
Пункт 5. 1 после слова «работоспособность» дополнить словами: «металлорежущего инструмента, напильников, надфилей и рашпилей».
Стандарт дополнять разделом — 6:
«6. Испытания дереворежущего инструмента на прочность
6.1. Испытаниям на прочность следует подвергать партии инструмента, прошедшие приемочный контроль в соответствии с требованиями пп.2-4.
6.2. Комбинированные пилы, насадные и сборные цилиндрические фрезы испытываются на прочность вращением. Контроль насадных фрез должен быть сплошным. План контроля комбинированных пил и сборных цилиндрических фрез должен соответствовать указанному в табл.8.
Таблица 8
Объем партии, шт. |
Объем выборки, шт. |
Приемочное число |
9-25 |
3 |
0 |
26-90 |
13 |
1 |
91-150 |
20 |
2 |
151-280 |
32 |
3 |
281-500 |
50 |
5 |
501-1200 |
80 |
7 |
1201-3200 |
125 |
10 |
3201-10000 |
200 |
14 |
Примечание. Для партий инструмента менее 9 шт. должен применяться сплошной контроль.
6.3. Фрезерные цепочки испытывают на разрыв при статическом нагружении под нагрузкой и на подвижность в шарнирах. Контроль должен быть сплошным.
6.4. Перед проведением испытаний на прочность вращением (п.6.2) должен быть проведен приемочный контроль остаточного дисбаланса.
Контроль должен быть выборочным.
План контроля должен соответствовать указанному в табл.8.
Партия считается прошедшей приемочный контроль, если число дефектных инструментов в выборке меньше или равно приемочному числу, указанному в табл.8, и партия считается не прошедшей приемочный контроль, если число дефектных инструментов в выборке более приемочного числа.
Переход на усиленный или ослабленный контроль осуществляют по ГОСТ 18242-72″.
Напильники для затачивания пил по дереву. Технические условия – РТС-тендер
ГОСТ 6476-80
Группа Г24
ОКП 39 2917
Дата введения 1981-01-01
в части разд. 2 — 1986-01-01
1. РАЗРАБОТАН И ВНЕСЕН Министерством станкостроительной и инструментальной промышленности СССР
РАЗРАБОТЧИКИ
Г.А.Астафьева, Н.И.Минаева, Т.А.Лавренова
2. УТВЕРЖДЕН И ВВЕДЕН В ДЕЙСТВИЕ Постановлением Государственного комитета СССР по стандартам от 25.01.80 N 353
3. Стандарт полностью соответствует СТ СЭВ 1298-78 и СТ СЭВ 1300-78
4. ВЗАМЕН ГОСТ 6476-67
5. ССЫЛОЧНЫЕ НОРМАТИВНО-ТЕХНИЧЕСКИЕ ДОКУМЕНТЫ
_______________
* На территории Российской Федерации действует ГОСТ Р ИСО 2859-1-2007. — Примечание изготовителя базы данных.
6. Ограничение срока действия снято по протоколу N 5-94 Межгосударственного Совета по стандартизации, метрологии и сертификации (ИУС 11-12-94)
7. ПЕРЕИЗДАНИЕ (август 1998 г.) с Изменениями N 1, 2, 3, утвержденными в ноябре 1984 г. , марте 1985 г., декабре 1990 г.* (ИУС 2-85, 8-88, 6-90*)
_______________
* Соответствует оригиналу. — Примечание изготовителя базы данных.
Вводная часть. (Исключена, Изм. N 2).
1. ТИПЫ
1.1. Напильники должны изготовляться типов:
трехгранные;
ромбические;
круглые;
плоские.
(Измененная редакция, Изм. N 2).
1.2. Напильники должны изготовляться следующих исполнений по твердости (сцепляемости с контрольной пластиной):
01 — 59;
02 — 62.
(Измененная редакция, Изм. N 1, 2).
2. ОСНОВНЫЕ ЭЛЕМЕНТЫ НАСЕЧЕК И РАЗМЕРЫ НАПИЛЬНИКОВ
2.1. Напильники должны изготовляться исполнений:
1 — с перекрестной (двойной) насечкой;
2 — с одинарной насечкой.
Насечки выполняются под углом 60° к оси напильника.
Расположение основной и вспомогательной насечек зубьев напильников должно соответствовать указанному на черт.1 и 2.
Черт.1, 2. Расположение основной и вспомогательной насечек зубьев напильников
Черт.1
Черт.2
2.2. Напильники с двойной насечкой должны иметь 24 основных и 20 вспомогательных насечек; с одинарной — 24 основные насечки на 10 мм длины.
По согласованию с потребителем допускается изготовление напильников с 17 основными и 13 вспомогательными насечками на 10 мм длины.
(Измененная редакция, Изм. N 1).
2.3. Круглые напильники и узкие стороны трехгранных, ромбических и плоских напильников должны иметь только одинарную насечку.
2.4. Размеры напильников должны соответствовать указанным на черт.3-7 и в табл.1-4.
Хвостовики напильников допускается выполнять с симметричным сечением любой формы, кроме круглой.
Черт.3. Трехгранные остроносые напильники
Трехгранные остроносые напильники
_______________
* Размеры для справок.
Черт.3
Таблица 1
Размеры в мм
Исполнение 1 | Исполнение 2 | , | ||||||||
Обозна- | Приме- | Обозна- | Приме- | |||||||
2833-0001 | 2833-0002 | 150 | 200 | 50 | 9 | 4,5 | 15 | 2,0 | ||
2833-0003 | 2833-0004 | 13* | 6,5 | 20 | 2,5 | |||||
2833-0023 | 2833-0024 | 200 | 255 | 55 | 16 | 8,0 | 3,0 |
_______________
* Допускается изготовление напильников с 12 мм.
Пример условного обозначения трехгранного остроносого напильника 9 мм исполнения 1:
Напильник 2833-0001 ГОСТ 6476-80
Черт.4. Трехгранные тупоносые напильники
Трехгранные тупоносые напильники
_______________
* Размеры для справок.
Черт.4
Таблица 2
Размеры в мм
Исполнение 1 | Исполнение 2 | , | |||||||
Обозна- | Приме- | Обозна- | Приме- | ||||||
2833-0005 | 2833-0006 | 150 | 200 | 50 | 9 | 15 | 2,0 | ||
2833-0007 | 2833-0008 | 13* | 20 | 2,5 | |||||
2833-0025 | 2833-0026 | 200 | 255 | 55 | 16 | 3,0 |
________________
* Допускается изготовление напильников с 12 мм.
Пример условного обозначения трехгранного тупоносого напильника 9 мм, исполнения 1:
Напильник 2833-0005 ГОСТ 6476-80
Четр.5 Ромбические напильники
Ромбические напильники
_______________
* Размеры для справок.
Черт.5
Таблица 3
Размеры в мм
Исполнение 1 | Исполнение 2 | , | |||||
Обозначение | Применяемость | Обозначение | Применяемость | ||||
2833-0009 | 2833-0010 | 19 | 5 | 15 | 2 | ||
2833-0011 | 2833-0012 | 24 | 7 | 20 | 2,5 |
Пример условного обозначения ромбического напильника 19 мм, исполнения 1:
Напильник 2833-0009 ГОСТ 6476-80
Черт.

Круглые напильники
________________
* Размеры для справок.
Примечание. Допускается по согласованию с потребителем изготовлять напильники без оттянутого участка.
Черт.6
Таблица 4
мм
Исполнение 2 | , | |||||||
Обозначение | Применяемость | |||||||
2833-0014 | 150 | 200 | 5,0 | 2,5 | 50 | 15 | 2,0 | |
2833-0020 | 7,5 | 4,0 | ||||||
2833-0022 | 200 | 255 | 9,5 | 5,0 | 55 | 20 | 3,0 |
Пример условного обозначения круглого напильника 5 мм, исполнения 2:
Напильник 2833-0014 ГОСТ 6476-80
Черт.

Плоские напильники
________________
* Размеры для справок.
Черт.7
Пример условного обозначения плоского напильника исполнения 1:
Напильник 2833-0015 ГОСТ 6476-80
То же, исполнения 2:
Напильник 2833-0016 ГОСТ 6476-80
Примечание. В напильниках всех типов для исполнения 02 по твердости к условному обозначению добавляется индекс 02.
(Измененная редакция, Изм. N 1, 2, 3).
3. ТЕХНИЧЕСКИЕ ТРЕБОВАНИЯ
3.1. Напильники должны изготовляться в соответствии с требованиями настоящего стандарта по рабочим чертежам, утвержденным в установленном порядке.
3.2. Напильники должны изготовляться из инструментальной углеродистой стали марок У13 или У13А по ГОСТ 1435* или из стали 13Х по ГОСТ 5950**, профилей номеров 3, 5, 8, 10 по ГОСТ 5210. Допускается изготовлять круглые напильники из стали по ГОСТ 14955.
_______________
* На территории Российской Федерации действует ГОСТ 1435-99, здесь и далее по тексту;
** На территории Российской Федерации действует ГОСТ 5950-2000. — Примечание изготовителя базы данных.
(Измененная редакция, Изм. N 3).
3.3. Твердость и острота зубьев напильника должны обеспечивать сцепляемость их с контрольной пластинкой, изготовленной из стали тех же марок, что и напильник, двух исполнений по твердости 59; 62.
(Измененная редакция, Изм. N 1, 2).
3.4, 3.5. (Исключены, Изм. N 2).
3.6. Твердость хвостовика напильника на участке от конца до середины его длины не должна превышать 36,5.
(Измененная редакция, Изм. N 1).
3.7. Отношение высоты зуба к нормальному шагу основной насечки должно быть не менее 0,5.
3.8. Передний угол зуба напильника, измеренный в сечении (по вершине зуба), перпендикулярном направлению основной насечки, может быть отрицательным, но не должен превышать минус 10°.
3.9. Предельные отклонения размеров напильников не должны превышать, мм:
длины рабочей части | ±5 | |
длины хвостовика | ±2,5 | |
ширины плоских напильников, большой диагонали ромбических и диаметра круглых | ±1,6 | |
ширины сторон трехгранных напильников | ||
толщины для плоских и малой диагонали для ромбических напильников | ±0,8 | |
ширины узкой стороны | ±0,2 | |
разности ширин двух смежных сторон при большом угле ромбического напильника | 1 |
(Измененная редакция, Изм. N 1, 2, 3).
3.10. Предельные отклонения: углов наклона насечки…±2°, числа основных и вспомогательных насечек на 10 мм длины напильника…±1 насечка.
(Измененная редакция, Изм. N 2).
3.11. Допуск прямолинейности неоттянутого участка рабочей части трехгранных и круглых напильников — 0,3 мм, ромбических и плоских напильников — 0,5 мм.
(Измененная редакция, Изм. N 1, 2).
3.12. Расстояние конца носка напильника от плоскости неоттянутой части соответствующей стороны напильника должно быть не менее 0,5 мм.
3.13. Отклонение от симметричности оси хвостовика относительно оси рабочей части напильника не должно превышать 0,8 мм.
3.14. На круглых напильниках и на овальной стороне плоских напильников, при насечке рядками, насечки соседних рядков должны перекрывать друг друга.
3.15. На поверхности напильника не должно быть трещин. На рабочей поверхности напильника не должно быть заусенцев, черновин и следов коррозии.
Торец носка напильника должен быть зачищен и не иметь сколов.
Острые кромки на хвостовике должны быть притуплены.
(Измененная редакция, Изм. N 1, 3).
3.16. Разность между наибольшим и наименьшим значениями осевого шага основной или вспомогательной насечки на любом участке рассматриваемой стороны не должна превышать 10% номинального значения осевого шага.
3.17. Смещение заплечиков относительно друг друга вдоль оси напильника не должно превышать 1 мм.
3.18. (Исключен, Изм. N 2).
3.19. Надежность напильников определяется полным 95%-ным ресурсом, равным 5000 рабочих ходов на одну сторону напильника, при условиях испытаний, указанных в разд.5.
Критерием предельного состояния напильников является потеря производительности, выраженная нормой съема металла за 5000 рабочих ходов менее, указанной в табл. 4а.
Таблица 4а
Тип напильников | Исполнение | Норма съема одной стороной, г |
Трехгранный | 1 | 4,5 |
2 | 4,1 | |
Ромбический | 1 | 3,7 |
2 | 3,2 | |
Плоский | 1 | 5,7 |
2 | 5,5 | |
Круглый | 2 | 3,7 |
Поправочный коэффициент на норму съема металла для напильников, изготовленных из стали 13Х, равен 1,4 по отношению к указанному в табл. 4а.
(Измененная редакция, Изм. N 3).
3.20. На ненасеченной части каждого напильника или на хвостовике около заплечиков должны быть четко нанесены:
товарный знак предприятия-изготовителя;
буква «П»;
марка стали 13Х (марки стали У13А, У13 не маркируют).
(Измененная редакция, Изм. N 2, 3).
3.21. При упаковывании напильников они должны быть отделены один от другого.
3.22. На потребительской таре должна быть указана твердость напильников.
3.23. Внутренняя упаковка напильников — ВУ-1 по ГОСТ 9.014.
3.24. Остальные требования к упаковке, маркировке транспортной и потребительской тары — по ГОСТ 18088.
3.21-3.24. (Введены дополнительно, Изм. N 2).
4. ПРИЕМКА
4.1. Правила приемки — по ГОСТ 23726.
(Измененная редакция, Изм. N 2).
4. 2. Периодические испытания, в том числе испытания на надежность, следует проводить один раз в 3 года не менее чем на 5 напильниках.
Испытания напильников должны проводиться на одном типоразмере из каждого типа напильников.
(Измененная редакция, Изм. N 3).
5. МЕТОДЫ КОНТРОЛЯ И ИСПЫТАНИЙ
5.1. Контроль внешнего вида осуществляют визуально.
5.2. При контроле параметров напильников должны применяться методы и средства контроля, погрешность которых должна быть не более:
при измерении линейных размеров — значений, указанных в ГОСТ 8.051;
при измерении углов — 35% значения допуска на проверяемый угол;
при контроле формы и расположения поверхностей — 25% значения допуска на проверяемый параметр.
5.3. Ширину и толщину напильника измеряют на ненасеченном участке рабочей части.
5.1-5.3. (Измененная редакция, Изм. N 2).
5. 4. При испытаниях на работоспособность (сцепляемость с контрольной пластинкой) и надежность напильники проверяют по следующим сторонам:
трехгранные — по трем широким сторонам;
ромбические — по четырем широким;
плоские — по двум широким;
круглые — по двум диаметрально противоположным поверхностям.
5.5. Испытания напильников на работоспособность проводят по сцепляемости с контрольной пластинкой твердостью, указанной в п.3.3.
Пластинку широкой стороной проводят по зубьям напильника от носка к хвостовику. При этом на зубьях напильника не должно быть следов смятия или выкрашивания их на вершинах. Сцепляемость с контрольной пластинкой и качество насечки на размере и на расстоянии до 10 мм от торца носка не контролируются.
5.6. Испытания напильников на надежность должны проводиться на специальных испытательных станках, которые должны соответствовать установленным для них нормам точности и жесткости.
5.4-5.6. (Измененная редакция, Изм. N 2, 3).
5.7. Насечка напильника, подвергаемого испытанию, должна быть сухой.
5.8. Напильники следует испытывать на образцах (брусках) из углеродистой стали марки У10 по ГОСТ 1435 твердостью 51-53.
Трехгранные, ромбические и плоские напильники испытывают на брусках сечением 1,5х8 мм, круглые напильники — на брусках сечением 1,5х4 мм.
Перед испытанием все стороны образца должны быть обработаны и иметь параметр шероховатости не более 10 мкм.
5.9. При испытании круглых напильников на торце опиливаемого образца должен быть сделан пропил, кривизна которого должна соответствовать кривизне поверхности испытываемого участка напильника.
5.10. У ромбических и плоских напильников испытанию должен подвергаться рабочий участок, равноудаленный от носка и заплечиков, а у трехгранных и круглых — неоттянутый участок рабочей части.
5.11. Напильники должны испытываться при следующем режиме испытательного станка:
число рабочих ходов — 55-60 в минуту;
длина рабочего хода — 65 мм;
прижимающее усилие подачи бруска 20 Н без учета сил трения в механизме подачи бруска и в механизме записи испытательного станка.
5.12. Опиливаемый образец при испытании напильников должен быть взвешен с точностью до 0,1 г.
5.7-5.12. (Измененная редакция, Изм. N 2).
5.13. Результаты испытаний следует считать удовлетворительными, если норма снятого металла каждой стороной напильника не менее значений, указанных в табл.4а.
(Измененная редакция, Изм. N 3).
6. ТРАНСПОРТИРОВАНИЕ И ХРАНЕНИЕ
Транспортирование и хранение напильников — по ГОСТ 18088.
(Измененная редакция, Изм. N 2).
Разд.7. (Исключен, Изм. N 2).
ПРИЛОЖЕНИЕ (справочное).

ПРИЛОЖЕНИЕ
Справочное
Твердость контрольной пластинки | Твердость затачиваемых пил по дереву |
| До 51 |
Электронный текст документа
подготовлен АО «Кодекс» и сверен по:
официальное издание
М.: ИПК Издательство стандартов, 1998
Фрезы цилиндрические насадные сборные — Морской флот
1.1. Фрезы должны изготовляться в соответствии с требованиями настоящего стандарта по рабочим чертежам, утвержденным в установленном порядке.
– корпуса фрез – из стали марки 40Х по ГОСТ 4543, стали марки 45 по ГОСТ 1050;
– корпуса ножей, оснащенных пластинами твердого сплава, – из стали марок 40Х, 35ХГСА по ГОСТ 4543, стали марки 45 по ГОСТ 1050;
– ножи фрез – из стали марок 8Х6НФТ, Х6ВФ по ГОСТ 5950;
– пластины ножей – из твердого сплава вольфрамовой группы по ГОСТ 3882;
– детали крепления и регулирования ножей – из стали марок 40Х и 45Х по ГОСТ 4543;
– цанги и упорные кольца – из стали марки 65Г по ГОСТ 14959.
(Измененная редакция, Изм. № 5).
1.2а. Фрезы, изготовленные из материалов, не указанных в п. 1.2, должны не уступать им по механическим свойствам и стойкости в соответствии с требованиями настоящего стандарта.
Детали крепления и регулирования ножей, изготовленные из материалов, не указанных в п. 1.2, должны обеспечивать прочность не ниже класса 4.8 по ГОСТ 1759.0, ГОСТ 1759.4, ГОСТ 1759.5.
(Введен дополнительно, Изм. № 5).
– корпусов – не менее 180 НВ;
– деталей крепления и регулирования ножей – 40 . 47 HRC э ;
– цанг и упорных колец – 43 . 49 HRC э ;
– твердость корпусов ножей – не менее 180 НВ.
Прочность деталей должна быть не ниже класса 4.8 по ГОСТ 1759.0, ГОСТ 1759.4, ГОСТ 1759.5.
(Измененная редакция, Изм. № 4).
(Измененная редакция, Изм. № 5).
1.4а. Пластины из твердого сплава, припаянные сплавом, не указанным в п. 1.4, должны не уступать им по прочности и надежности.
(Введен дополнительно, Изм. № 5).
при длине ножа до 40 мм. 0,3
» » » св. 40 до 90 мм. 0,4
Допускается утолщение слоя припоя до 0,4 мм по нижней опорной поверхности пластины. Разрыв слоя припоя по контуру пайки не должен быть более 5 % его общей длины.
1.8. Режущие кромки ножей не должны иметь трещин, завалов, выкрошенных мест и следов прижогов.
– передней поверхности ножей, оснащенных пластинами твердого
сплава (по пластине). Ra 0,32
– ленточки по задней поверхности ножей, оснащенных пластинами
твердого сплава (по пластине). Ra 0,16
– посадочного отверстия фрез, соприкасающихся поверхностей цанг
и корпусов фрез поверхностей укороченных цанг. Ra 1,25
– наружных поверхностей корпусов, опорных торцев корпусов для фрез с
непосредственной посадкой на шпиндель, опорных и торцевых
поверхностей ножей, оснащенных пластинами твердого сплава. Ra 2,5
– соприкасающихся поверхностей корпусов и клиньев с ножами. Rz 20
– остальных поверхностей. Rz 40
1.10. Предельные отклонения параметров фрез не должны быть более, мм:
– наружного диаметра фрез. js14
– диаметра посадочного отверстия. Н7
– диаметра корпуса и длины фрез. h24
1.5 – 1.10. (Измененная редакция, Изм. № 2).
от 90 до 130 мм. 0,08
св. 130 » 170 мм. 0,10
1.14. Допуск торцевого биения опорных поверхностей фрез с непосредственной посадкой на шпиндель относительно оси посадочного отверстия, измеренное на диаметре, превышающем на 30 мм диаметр посадочного отверстия, должен быть 0,03 мм.
1.12 – 1.14. (Измененная редакция, Изм. № 1).
1.15. Допуск прямолинейности режущих кромок ножей, оснащенных пластинами твердого сплава, должен быть, мм:
при длине до 60 мм. 0,02
1.16. Конусообразность по режущим кромкам ножей фрез должна быть не более значения допуска радиального биения фрезы.
1.17. Корпуса фрез должны быть уравновешены. Допустимый остаточный дисбаланс при массе должен быть, г ∙ мм:
св. 5 до 8 кг. 80
» 10 кг. 10 на каждые 1 кг массы
Фрезы, длина которых превышает половину диаметра, должны балансироваться динамически, остальные – статически.
При динамической балансировке значение допускаемого остаточного дисбаланса относится к каждой плоскости коррекции.
1.15 – 1.17. (Измененная редакция, Изм. № 2).
1.18. Разность в массе ножей, входящих в комплект фрезы, не должна быть более 0,1 г.
1.19. Разность в массе комплектов деталей для крепления и регулирования ножей фрезы должна быть не более, г, при массе:
св. 150 до 500 г. 0,2
1.20. Средний Т и установленный Ту периоды стойкости фрез при условиях испытаний, указанных в разд. 4 , должны быть не менее значений по табл. 1 . Критерием затупления фрез является увеличение шероховатости или значений сколов обработанных поверхностей, превышающих значения, указанные в табл. 1 .
шероховатости обработанных поверхностей по ГОСТ 7016 Rmmах , мкм
сколов облицовочного материала, мм
Фрезы с ножами из инструментальной стали марки Х6ВФ
Древесина хвойных пород по ГОСТ 8486 влажностью (12 ± 3) %
Фрезы с ножами, оснащенными пластинами твердого сплава марки ВК6
Древесностружечные плиты по ГОСТ 10632, облицованные синтетическим шпоном
Примечани е . Срок введения в действие требований пункта – с 01.06.90.
1.20. (Введен дополнительно, Изм. № 1; измененная редакция, Изм. № 3, 4).
– товарный знак предприятия-изготовителя;
– диаметр посадочного отверстия;
– предельная частота вращения.
1.22. Транспортная маркировка, маркировка потребительской тары и упаковка – по ГОСТ 18088.
1.21, 1.22. (Введены дополнительно, Изм. № 5).
от 80 до 100 мм. 12000
св. 100 » 125 мм. 9000
» 125 » 140 мм. 8000
» 140 » 180 мм. 6200
3.2. Приемочный контроль на соответствие требованиям пп. 1.12 , 1.13 и 1.16 проводят согласно плану контроля, указанному в табл. 4б ГОСТ 23726 , при этом количество фрез с установленными ножами должно соответствовать объему выборки.
3.3. Контроль прочности вращением на соответствие требованиям п. 4.6 проводят на фрезах, прошедших приемочный контроль согласно п. 3.2 . Объем выборки из этой партии должен соответствовать указанному в табл. 8 ГОСТ 23726 .
3.1 – 3.3. (Измененная редакция, Изм. № 2).
3.4. Периодические испытания, в том числе и испытания на средний период стойкости, следует проводить один раз в три года не менее чем на пяти фрезах.
Испытания на установленный период стойкости следует проводить один раз в год не менее чем на пяти фрезах.
Испытаниям следует подвергать фрезы любого диаметра, прошедшие приемочный контроль согласно пп. 3.1 – 3.3.
Примечани е. Срок введения в действие требований пункта – с 01.06.90.
(Измененная редакция, Изм. № 2, 3).
4.1. Поверхности фрез и комплектующих деталей (п. 1.6 ) контролируют визуально сравнением с образцами, утвержденными в установленном порядке, или с помощью лупы ЛП-1-5 ´ по ГОСТ 25706 .
4.2. Шероховатость поверхностей фрез должна проверяться сравнением с образцами шероховатости по ГОСТ 9378 или образцами-эталонами, имеющими значения параметров шероховатости не более указанных в п. 1.9 и утвержденными в установленном порядке.
Сравнение осуществляют визуально с применением лупы ЛП-1-5 ´ по ГОСТ 25706.
4.1, 4.2. (Измененная редакция, Изм. № 1, 2).
а) для линейных размеров – значений, указанных в ГОСТ 8.051;
б) для отклонения форм и расположения поверхностей – 25 % допуска на проверяемый параметр;
в) для угловых размеров – 35 % допуска на проверяемый угол.
(Измененная редакция, Изм. № 2).
4.4. Контроль твердости корпусов фрез – по ГОСТ 9012 , комплектующих деталей – по ГОСТ 9013 с помощью твердомеров ТБ и ТР по ГОСТ 23677 соответственно.
(Измененная редакция, Изм. № 3).
4.5. Толщину слоя припоя и допускаемый разрыв припоя (п. 1.5 ) контролируют на видимом контуре шва пайки по эталонам или с помощью лупы ЛП-1-5 ´ по ГОСТ 25706 .
(Измененная редакция, Изм. № 1).
до 140 мм. 13500
св. 140 до 160 мм. 12000
» 160 » 220 мм. 9300
(Измененная редакция, Изм. № 2).
При динамической балансировке и контроле фрезы устанавливают по риске, расположенной в плоскости, проходящей через ось стопорных винтов. Риска должна располагаться в верхнем вертикальном положении.
4.8. Испытания фрез должны проводиться на фрезерных станках по ГОСТ 6735 , нормы точности которых соответствуют ГОСТ 69 , или на четырехсторонних строгальных станках по ГОСТ 7315 , нормы точности и жесткости которых соответствуют ГОСТ 7315 , или на автоматических линиях, соответствующих установленным для них нормам точности.
Испытаниям на надежность следует подвергать фрезы с ножами из инструментальной стали марки Х6ВФ и фрезы с ножами, оснащенными пластинами твердого сплава ВК6, на режимах, указанных в табл. 2.
частота вращения шпинделя п, мин -1
подача на зуб t, мм/зуб
глубина фрезерования s, мм, не более
Фрезы с ножами из инструментальной стали марки Х6ВФ
Фрезы с ножами, оснащенными пластинами твердого сплава ВК6
(Измененная редакция, Изм. № 1, 4).
(Измененная редакция, Изм. № 4).
4.10. (Исключен, Изм. № 2).
Транспортирование и хранение фрез – по ГОСТ 18088.
Разд. 5. (Измененная редакция, Изм. № 5).
Разд. 6. (Исключен, Изм. № 1).
ПРИЛОЖЕНИЕ. (Исключено, Изм. № 1).
1. РАЗРАБОТАН И ВНЕСЕН Министерством станкостроительной и инструментальной промышленности СССР
B .C. Рыбалко, М.В. Лопачева
2. УТВЕРЖДЕН И ВВЕДЕН В ДЕЙСТВИЕ Постановлением Государственного комитета СССР по стандартам от 06.06.80 № 2631
3. Срок проверки – 1996 г., периодичность проверок – 5 лет
4. ВЗАМЕН ГОСТ 13932-68
5. ССЫЛОЧНЫЕ НОРМАТИВНО-ТЕХНИЧЕСКИЕ ДОКУМЕНТЫ
Купить ГОСТ 14956-79 — бумажный документ с голограммой и синими печатями. подробнее
Распространяем нормативную документацию с 1999 года. Пробиваем чеки, платим налоги, принимаем к оплате все законные формы платежей без дополнительных процентов. Наши клиенты защищены Законом. ООО «ЦНТИ Нормоконтроль».
Наши цены ниже, чем в других местах, потому что мы работаем напрямую с поставщиками документов.
Способы доставки
- Срочная курьерская доставка (1-3 дня)
- Курьерская доставка (7 дней)
- Самовывоз из московского офиса
- Почта РФ
Распространяется на насадные цилиндрические сборные фрезы, предназначенные для обработки древесины и древесных материалов на фрезерных и четырехсторонних строгальных станках. Фрезы должны изготовляться типов: 1 – с непосредственной посадкой на шпиндель; 2 – с креплением на двух цангах гайками; 3 – с креплением на двух цангах через промежуточные упорные кольца; 4 – с креплением на цанге; 5 – с креплением на патроне.
Ограничение срока действия снято: Протокол № 2-92 МГС от 05.10.92 (ИУС 2-93)
Оглавление
Приложение 1 Элементы конструкции и размеры деталей фрез
Приложение 2 Спецификация деталей фрез
×
Дата введения: | 01.01.1981 |
---|---|
Добавлен в базу: | 01.09.2013 |
Актуализация: | 01.01.2019 |
Этот ГОСТ находится в:
- Раздел: Экология
- Подраздел: 79 ТЕХНОЛОГИЯ ПЕРЕРАБОТКИ ДРЕВЕСИНЫ
- Подраздел: 79.
120 Деревообрабатывающее оборудование
- Подраздел: 79.120.20 Деревообрабатывающие инструменты
- Раздел: Электроэнергия
- Подраздел: 79 ТЕХНОЛОГИЯ ПЕРЕРАБОТКИ ДРЕВЕСИНЫ
- Подраздел: 79.120 Деревообрабатывающее оборудование
- Подраздел: 79.120.20 Деревообрабатывающие инструменты
Организации:
03.08.1979 | Утвержден | Госстандарт СССР | 2959 |
---|---|---|---|
Издан | Издательство стандартов | 1979 г. | |
Разработан | Министерство станкостроительной и инструментальной промышленности |
Shell type inserted beade circular cutterbloks for woodcutting. Types.

Чтобы бесплатно скачать этот документ в формате PDF, поддержите наш сайт и нажмите кнопку:
ГОСУДАРСТВЕННЫЙ СТАНДАРТ СОЮЗА ССР
ФРЕЗЫ ДЕРЕВОРЕЖУЩИЕ НАСАДНЫЕ ЦИЛИНДРИЧЕСКИЕ СБОРНЫЕ
ТИПЫ, ОСНОВНЫЕ ПАРАМЕТРЫ И РАЗМЕРЫ
ГОСУДАРСТВЕННЫЙ КОМИТЕТ СССР ПО СТАНДАРТАМ Москва
РАЗРАБОТАН Министерством станкостроительной и инструментальной промышленности
В. С. Рыбалко, канд. техн. наук; М. В. Лопачейа
ВНЕСЕН Министерством станкостроительной и инструментальной промышленности
Зам. министра А. Е. Прокопович
УТВЕРЖДЕН И ВВЕДЕН В ДЕЙСТВИЕ Постановлением Государственного комитета СССР по стандартам от 3 августа 1979 г. № 2959
Редактор Л- А. Владимиров Технический редактор О. Я. Никитина Корректор А. С. Черноусова
Сдано в набор 10.09,79 Подп. в печ. 16 10.79 1,75 п л. 1,12 уч. -изд. л. Тир. 16000 Цепи 5 коп
Ордена «Знак Почета» Издательство стандартов. 12355″, Москва, Новопреспенский пер., 3 Калужская типография стандартов, ул. Московская, 256. Зак. 2509
ПРИЛОЖЕНИЕ 1 Рекомендуемое
ЭЛЕМЕНТЫ КОНСТРУКЦИИ И РАЗМЕРЫ ДЕТАЛЕЙ ФРЕЗ
1. Элементы конструкции и размеры корпусов фрез указаны на черт, 1—6 и в табл. 1—5.
Количество отверстий в пазах п
Количество отверстий в пазах п
т 086 м 85×2-7 Н лед
ГОСТ 14956—79 Стр. 13
Обозначение ко рпуса
3210-0039/001 | 260 | 40 |
Количество отверстий в пазах п
Количество отверстий в пазах п
Пример условного обозначения корпуса для фрезы 3210-1708с D = 125 мм, d = 32 мм, L — 60 мм, типа 1, исполнения I:
Корпус 3210-17081001 2. Конструкция и основные размеры клиньев должны соответствовать указанным на черт, бив табл. 6.
Пример условного обозначения клина длиной L = 170 мм:
3. Конструкция и размеры винтов (поз. 4) указаны на черт. 7.
4. Конструкция и размеры регулировочных винтов (поз. 5) указаны на черт. 8 и в табл. 7.
Пример условного обозначения винта длиной / = 21 мм:
5. Конструкция и размеры винтов стопорных (поз. 6) указаны на черт. 9 и в табл. 8.
Пример условного обозначения винта длиной 7=20 мм:
6. Конструкция и размеры гаек (поз. 8 и 9) для крепления фрез типа 2 указаны на черт. 10.
Гайка должна изготовляться с правой или левой резьбой.
Пример условного обозначения гае к с ле вой резьбой:
Гайка М85Х2 лев
7. Конструкция и размеры гаек (поз. 8) для крепления фрез типа 4 указаны на черт. 11.
Гайка должна изготовляться с правой или левой резьбой.
Пример условного обозначения гайки с левой резьбой:
Гайкр M52XL5 лее
8. Конструкция и размеры укороченных цанг (поз. 8 и 10) для фрез типа 2, 3 и 4 указаны на черт. 12 и в табл. 9.
УДК 621.914.2:674.055:006.354 Группа Г23
ГОСУДАРСТВЕННЫЙ СТАНДАРТ СОЮЗА ССР
ФРЕЗЫ ДЕРЕВОРЕЖУЩИЕ НАСАДНЫЕ ЦИЛИНДРИЧЕСКИЕ СБОРНЫЕ Типыг основные параметры и размеры
Shell type inserted beade circular cutterbioks for woodcutting.
Types Mam parameter and dimensions
Постановлением Государственного комитета СССР по стандартам от 3 августа 1979 г. № 2959 срок действия установлен
с 01.01 1981 г. до 01.01 193$ г.
Несоблюдение стандарта преследуется по закону
1. Настоящий стандарт распространяется на насадные цилннд рические сборные фрезы, предназначенные для обработки древесины и древесных материалов па фрезерных и четырехсторонних строгальных станках.
2. Фрезы должны изготовляться типов:
1 — с непосредственной посадкой на шпиндель;
2 — с креплением на двух цангах гайками;
3 — с креплением на двух цангах через промежуточные упорные кольца;
4 — с креплением на цанге;
5 — с креплением па патроне.
Фрезы типа 1,4 п 5 изготовляются в двух исполнениях:
1 — со стальными ножами по ГОСТ 6567-75;
2— с ножами, оснащенными твердосплавными пластина!ми.
Фрезы типа 2 и 3 изготовляются со стальными ножами.
3. Конструкция и основные размеры фрез должны соответствовать указанным на черт. 1—5 и в табл. 1—5.
ГОСУДАРСТВЕННЫЙ СТАНДАРТ СОЮЗА ССР
ФРЕЗЫ ДЕРЕВОРЕЖУЩИЕ НАСАДНЫЕ ЦИЛИНДРИЧЕСКИЕ СБОРНЫЕ
Shell-type inserted bead circular cutter blocks for woodcutting.
Specifications
Дата введения 1982-01-01
1. РАЗРАБОТАН И ВНЕСЕН Министерством станкостроительной и инструментальной промышленности СССР
РАЗРАБОТЧИКИ
2. УТВЕРЖДЕН И ВВЕДЕН В ДЕЙСТВИЕ Постановлением Государственного комитета СССР по стандартам от 06.06.80 N 2631
3. Срок проверки – 1996 г., периодичность проверок – 5 лет
5. ССЫЛОЧНЫЕ НОРМАТИВНО-ТЕХНИЧЕСКИЕ ДОКУМЕНТЫ
Обозначение НТД,
на который дана ссылка
_______________
* Отменен. Действует ГОСТ 5950-2000, здесь и далее по тексту. – Примечание «КОДЕКС».
_______________
* Отменен. Действует ГОСТ 15527-2004, здесь и далее по тексту. – Примечание «КОДЕКС».
6. Снято ограничение срока действия Постановлением Госстандарта СССР от 30.05.91 N 766
7. ПЕРЕИЗДАНИЕ (январь 1998 г.) с Изменениями N 1, 2, 3, 4, 5, утвержденными в декабре 1986 г., ноябре 1988 г., марте 1989 г., мае 1991 г., феврале 1995 г. (ИУС 3-87, 2-89, 6-89, 8-91, 5-95)
Настоящий стандарт распространяется на сборные цилиндрические насадные дереворежущие фрезы по ГОСТ 14956 и другие насадные цилиндрические сборные фрезы для обработки древесины и древесных материалов на фрезерных, четырехсторонних строгальных станках и автоматических линиях, изготовляемые для нужд народного хозяйства и экспорта.
Требования стандарта являются обязательными, кроме пп.1.2, 1.4, 1.20, 1.21, 4.9.
Стандарт пригоден для целей сертификации по безопасности по пп.2.1 и 4.7.
(Измененная редакция, Изм. N 4, 5).
1. ТЕХНИЧЕСКИЕ ТРЕБОВАНИЯ
1. ТЕХНИЧЕСКИЕ ТРЕБОВАНИЯ
1.1. Фрезы должны изготовляться в соответствии с требованиями настоящего стандарта по рабочим чертежам, утвержденным в установленном порядке.
1.2. Фрезы изготовляют из следующих материалов:
– корпуса фрез – из стали марки 40Х по ГОСТ 4543, стали марки 45 по ГОСТ 1050;
– корпуса ножей, оснащенных пластинами твердого сплава, – из стали марок 40Х, 35ХГСА по ГОСТ 4543, стали марки 45 по ГОСТ 1050;
– ножи фрез – из стали марок 8Х6НФТ, Х6ВФ по ГОСТ 5950;
– пластины ножей – из твердого сплава вольфрамовой группы по ГОСТ 3882;
– детали крепления и регулирования ножей – из стали марок 40Х и 45Х по ГОСТ 4543;
– цанги и упорные кольца – из стали марки 65Г по ГОСТ 14959.
(Измененная редакция, Изм. N 5).
1.2а. Фрезы, изготовленные из материалов, не указанных в п.1.2, должны не уступать им по механическим свойствам и стойкости в соответствии с требованиями настоящего стандарта.
Детали крепления и регулирования ножей, изготовленные из материалов, не указанных в п.1.2, должны обеспечивать прочность не ниже класса 4.8 по ГОСТ 1759.0, ГОСТ 1759.4, ГОСТ 1759.5.
(Введен дополнительно, Изм. N 5).
1.4. Пластины из твердого сплава должны быть припаяны сплавом марки Л63 по ГОСТ 15527.
(Измененная редакция, Изм. N 5).
1.4а. Пластины из твердого сплава, припаянные сплавом, не указанным в п.1.4, должны не уступать им по прочности и надежности.
(Введен дополнительно, Изм. N 5).
1.5. Толщина слоя припоя между поверхностью корпуса ножа и пластиной должна быть не более, мм:
при длине ножа до 40 мм
Допускается утолщение слоя припоя до 0,4 мм по нижней опорной поверхности пластины. Разрыв слоя припоя по контуру пайки не должен быть более 5% его общей длины.
1.6. Корпуса фрез и комплектующие детали не должны иметь трещин и следов коррозии.
1.7. Корпуса фрез, детали крепления и регулирования ножей должны иметь защитное покрытие по ГОСТ 9.301.
1.18. Режущие кромки ножей не должны иметь трещин, завалов, выкрошенных мест и следов прижогов.
1.9. Параметры шероховатости поверхностей фрез по ГОСТ 2789 должны быть, мкм, не более:
– передней поверхности ножей, оснащенных пластинами твердого сплава (по пластине)
– ленточки по задней поверхности ножей, оснащенных пластинами твердого сплава (по пластине)
– посадочного отверстия фрез, соприкасающихся поверхностей цанг и корпусов фрез поверхностей укороченных цанг
– наружных поверхностей корпусов, опорных торцев корпусов для фрез с непосредственной посадкой на шпиндель, опорных и торцевых поверхностей ножей, оснащенных пластинами твердого сплава
– соприкасающихся поверхностей корпусов и клиньев с ножами
1.10. Предельные отклонения параметров фрез не должны быть более, мм:
– наружного диаметра фрез
– диаметра посадочного отверстия
– диаметра корпуса и длины фрез
1. 5-1.10. (Измененная редакция, Изм. N 2).
1.11. (Исключен, Изм. N 2).
1.12. Допуск радиального биения режущих кромок фрез с непосредственной посадкой на шпиндель, с посадкой на патроне и наружных поверхностей корпусов фрез относительно оси посадочного отверстия должен быть, мм, при диаметре фрез:
1.13. Допуск радиального биения режущих кромок фрезы с цанговым креплением относительно оси посадочных отверстий должен быть, мм, при длине фрез:
от 90 до 130 мм
1.14. Допуск торцевого биения опорных поверхностей фрез с непосредственной посадкой на шпиндель относительно оси посадочного отверстия, измеренное на диаметре, превышающем на 30 мм диаметр посадочного отверстия, должен быть 0,03 мм.
1.12-1.14. (Измененная редакция, Изм. N 1).
1.15. Допуск прямолинейности режущих кромок ножей, оснащенных пластинами твердого сплава, должен быть, мм:
при длине до 60 мм
1.16. Конусообразность по режущим кромкам ножей фрез должна быть не более значения допуска радиального биения фрезы.
1.17. Корпуса фрез должны быть уравновешены. Допустимый остаточный дисбаланс при массе должен быть, г·мм:
10 на каждые 1 кг массы
Фрезы, длина которых превышает половину диаметра, должны балансироваться динамически, остальные – статически.
При динамической балансировке значение допускаемого остаточного дисбаланса относится к каждой плоскости коррекции.
1.15-1.17. (Измененная редакция, Изм. N 2).
1.18. Разность в массе ножей, входящих в комплект фрезы, не должна быть более 0,1 г.
1.19. Разность в массе комплектов деталей для крепления и регулирования ножей фрезы должна быть не более, г, при массе:
св. 150 до 500 г
1.20. Средний и установленный периоды стойкости фрез при условиях испытаний, указанных в разд.4, должны быть не менее значений по табл.1. Критерием затупления фрез является увеличение шероховатости или значений сколов обработанных поверхностей, превышающих значения, указанные в табл.1.
Статическое испытание грунтов штампом по ГОСТ 20276
Статическое испытание грунтов штампом по ГОСТ 20276-2012 «Грунты. Методы полевого определения характеристик прочности и деформируемости» производится на стадии разработки котлована и уточнения полученных геологической организацией предоставленных данных изысканий. В зависимости от принятого конструктивного решения фундамента (фундаментная плита, железобетонный ростверк, отдельно-стоящие фундаменты и другие типы фундаментов), может назначаться определенная нагрузка при испытании и количество проверяемых участков.
В соответствии с методикой проведения работ по ГОСТ 20276-2012, существует 4 типа штампов, среди которых:
- штамп 1-го типа. С плоской подошвой и площадью 2500-5000 см2
- штамп 2-го типа. С плоской подошвой и площадью до 1000 см2, дополняющей штамп в 5000 м2
- штамп 3-го типа. С плоской подошвой, площадью 600 см2
- штамп 4-го типа. Винтовой штамп, площадью 600 см2
Назначение типа штампов производится в зависимости от данных геологической разведки в соответствии с таблице 5. 1. ГОСТ 20276-2012. В арсенале нашей лаборатории имеются штампы любых размеров, отвечающие самым нестандартным задачам и особенностям объекта исследования. За годы работы, инженеры нашей лаборатории способны решать самые нестандартные задачи и готовы изготовить штампы любого диаметра для выполнения самых сложных задач.
Алгоритм исследования:
- подготовка программы испытаний работ, согласование с Заказчиком
- установка штампа на дно котлована с предварительной подготовкой поверхности ( при штампе 4-го типа проводят завинчивание с синхронным вращением)
- подготовка пригруза и реперной измерительной системы;
- после монтажа всех устройств, производят снятия первичных показаний приборов;
- первичной нагружение, выдержка до стабилизации нагрузок и выравнивания основания;
- дальнейшее нагружение со снятием показаний давления «р» с необходимым количеством ступеней до достижения проектной нагрузки либо максимальной деформации грунта;
- снятие показаний с приборов, фиксирование в журнале работ, разбор стенда;
- камеральная обработка данных, подготовка Заключения.
Давайте поговорим о задаче, методике и цене проведения испытаний. Звоните +7(917) 588-26-22 (Александр).
Поделиться в соц. сетях
Испытания на герметичность изделий с замкнутой оболочкой ГОСТ РВ 20.57.416-98
Испытания на герметичность изделий с замкнутой оболочкой ГОСТ РВ 20.57.416-98, метод 401 – 2.1
Стенд контроля герметичности ВАКТРОН РМКГ-ГИРО предназначен для проверки малогабаритных микроэлектронных изделий. Метод работает следующим образом: изделие укладывается в опрессовочную камеру. Камера закрывается, и в неё с помощью системы и клапанов подается определённое тестовое давление гелия, например 3 атм.
Изделие выдерживается в атмосфере гелия определенное время, например в течение 10 минут. Затем изделие извлекается и выдерживается на воздухе несколько минут, для того чтобы гелий с поверхности улетучился.
Объект помещают в вакуумную камеру, которая соединяется с входом течеискателя. Гелий начнёт выходить из изделия под действием вакуумных насосов, в случае наличия течи, и индицироваться течеискателем. В данном случае изделие признается негодным. С помощью щупа течеискателя можно просканировать поверхность изделия и выделить точки нарушения герметичности для последующего устранения и ремонта.
Описание стенда контроля герметичности ВАКТРОН РМКГ-ГИРО
Установка РМКГ-ГИРО предназначена для контроля герметичности изделия (объект контроля – ОК), которое представляет собой металлический корпус из ковара с герметично приваренной крышкой. В корпусе имеется 3 металлостеклянных электрических вывода и 2 вывода оптического волокна.
Изделие имеет медный штенгель – трубка диаметром 3 мм с толщиной стенки 0,5 мм.
Объём внутрикорпусного пространства 4650 мм. куб. Срок эксплуатации изделия 20 лет.
Перед окончательной герметизацией устройства из него необходимо удалить остатки влаги. Делается это путем выдерживания корпуса под вакуумом при температуре 80-100 градусов Цельсия. Вакуумная печь, в которой осуществляется нагрев, одновременно является шлюзом атмосферной камеры, заполненной сухим азотом. После окончания сушки печь заполняется азотом, и корпус с крышкой переносится в атмосферную камеру. В камере осуществляется приварка крышки, создавая внутри изделия азотную среду.
Затем штенгель ОК обжимается, и проводится контроль герметичности.
К работам на стенде допускается персонал, владеющий навыками и знаниями в области основ вакуумной техники и течеискания.
КОНТРОЛЬ СПОСОБОМ ОПРЕССОВКИ ГЕЛИЕМ ЗАМКНУТЫХ ОБОЛОЧЕК
При контроле способом опрессовки замкнутых оболочек, ОК помещается в опрессовочную камеру, в которой создается давление гелия 1 – 3 атмосферы абс. При наличии течи в ОК, гелий проникает в замкнутый объем ОК. Проводится контроль ОК накоплением гелия в вакуумной камере, соединенной с течеискателем, в которую помещается ОК.
Контроль должен проводиться в такой последовательности:
- Объект контроля помещается в опрессовочную камеру.
Оператор включает вакуумный насос и плавно открывает ручной клапан VT1, удаляя воздух из опрессовочной камеры до достижения давления менее 0,1 атм., согласно манометру. Оператор закрывает клапан VT1 и отключает вакуумный насос.
- Далее обеспечивается подача заданного методикой испытаний давления гелия в опрессовочную камеру. Оператор открывает редуктор баллона с гелием, настроенный на 3 атм., и устанавливает заданное давление вентилем, следя за показаниями манометра. При превышении давления 3 атмосферы абс., сработает предохранительный клапан VP, сбросив избыточное давление для сохранения целостности изделия. После настройки испытательного давления оператор плавно открывает ручной клапан VT2, подавая в опрессовочную камеру гелий. ОК выдерживается под давлением гелия установленное методикой испытаний время.
- Оператор закрывает ручной клапан VT2, включает насос и плавно открывает ручной клапан VT1 для удаления гелия из камеры. Выпускная магистраль насоса должна быть выведена трубкой за пределы помещения контроля герметичности.
После удаления гелия оператор закрывает клапан VT1.
- Оператор вынимает ОК из камеры опрессовки, обдувает сжатым воздухом или азотом наружную поверхность ОК для очистки от сорбированного гелия и выдерживает ОК на воздухе в течение заданного методикой испытаний времени.
- Перед установкой ОК в вакуумную камеру, присоединенную к течеискателю, пустая вакуумная камера откачивается течеискателем до давления менее 100 Па в установленном методикой испытаний режиме чувствительности, например «Высокая чувствительность». Течеискатель предварительно калибруется в указанном режиме чувствительности в соответствии с инструкцией по эксплуатации. Затем оператор открывает ручной клапан VT3 между течеискателем и вакуумной камерой и только после этого включает режим измерения на течеискателе. Оператор дожидается стабилизации сигнала течеискателя и обнуляет фоновые показания выходного прибора течеискателя, нажимая кнопку ZERO в течение 3 секунд.
- Опрессованный гелием ОК (после его выдержки на воздухе) помещают в вакуумную камеру и откачивают камеру с ОК течеискателем до давления не более 100 Па.
Затем клапан VT3 перекрывают и накапливают гелий в камере в течение заданного методикой времени, после чего плавно открывают входной клапан VT3, следя за давлением и фиксируют показания течеискателя.
- Оператор измеряет и сравнивает величину показаний течеискателя с пороговым значением для режима накопления, заданным методикой испытаний, и принимает решение о наличии течи в ОК. Для определения соотношения между порогом герметичности в режиме накопления и порогом герметичности при измерениях в реальном времени нужно вместо ОК поместить в вакуумную камеру течь ГЕЛИТ и замерить её поток в режиме накопления с параметрами, указанными в методике испытаний.
С целью исключения повышенного гелиевого фона в процессе испытаний запрещается использовать камеру, в которой проводилась опрессовка ОК гелием.
ЛОКАЛИЗАЦИЯ ТЕЧИ СПОСОБОМ ГЕЛИЕВОГО ЩУПА
При контроле способом гелиевого щупа объект контроля заполняется гелием до давления 1 – 3 атмосферы, после чего наружная поверхность ОК контролируется специальным щупом, соединенным с анализатором течеискателя. В результате перепада давления гелий проникает через имеющийся сквозной дефект и в месте течи улавливается щупом и индицируется анализатором течеискателя.
Контроль следует проводить в такой последовательности:
- Оператор устанавливает изделие через открытый штенгель на переходник на трубку 3 мм газового стенда. Оператор включает вакуумный насос и плавно открывает ручной клапан VT1, удаляя воздух из магистрали и изделия до достижения давления менее 0,1 атм., согласно манометру. Оператор закрывает клапан VT1 и отключает вакуумный насос.
- Далее обеспечивается подача заданного методикой испытаний давления гелия в изделие. Оператор открывает редуктор баллона с гелием, настроенный на 3 атм., и устанавливает заданное давление вентилем, следя за показаниями манометра. При превышении давления 3 атмосферы абс., сработает предохранительный клапан VP, сбросив избыточное давление для сохранения целостности изделия. После настройки испытательного давления оператор плавно открывает ручной клапан VT2, подавая в изделие гелий.
- Щуп устанавливается на вход течеискателя. Течеискатель калибруется в «режиме щупа» в соответствии с инструкцией по эксплуатации. Оператор включает режим измерений. Контроль осуществляется перемещением щупа по поверхности ОК с постоянной скоростью, равной 0,10 — 0,15 м/мин. При движении щуп должен находиться на удалении не более 5 мм от контролируемой поверхности. Удаление щупа от контролируемой поверхности более чем на 5 мм резко снижает выявляемость дефектов. Контроль следует начинать с нижних участков ОК с постепенным переходом к верхним.
- При увеличении сигнала течеискателя над пороговым значением отмечают места, где сигнал максимален, и фиксируют их дефектограмме.
- Оператор выявляет течи или устанавливает их отсутствие. При признании объекта годным, штенгель изделия герметизируется, сохраняя в ОК инертную атмосферу.
СПЕЦИФИКАЦИЯ НА УСТАНОВКУ
№ пп |
Наименование оборудования |
Ед. |
Кол-во |
1 |
Рабочее место контроля герметичности РМКГ-ГИРО в составе: |
шт. |
1 |
1.1 |
Течеискатель масс-спектрометрический ULVAC HELIOT 901W1 |
шт. |
1 |
1.2 |
Камера вакуумная испытательная для изделий с максимальным внутренним объемом 4,65 см3 |
шт. |
1 |
1.3 |
Щуп для течеискателя Ulvac Heliot 5 м |
шт. |
1 |
1.4 |
Мера потока (течь гелиевая) Гелит 1, №13133-09 СИ в гос. реестре |
шт. |
1 |
1.5 |
Комплект для подключения калибровочной течи |
комп. |
1 |
1.6 |
Газовый стенд для вакуумирования и подачи гелия 0-3 атм. абс. в составе: комплект вакуумных клапанов, манометр поверенный стрелочный, предохранительный клапан, ресивер для смешивания газов, редуктор баллонный гелиевый, комплект соединительных полимерных шлангов и фитингов |
комп. |
1 |
1. |
Насос вакуумный пластинчато-роторный ULVAC GHD-030 |
шт. |
1 |
1.8 |
Клещи пережимные для трубки Ø3 мм |
шт. |
1 |
1.9 |
Стол лабораторный |
шт. |
1 |
1.10 |
Камера опрессовочная 03PE100-300-1 ДУ100 |
шт. |
1 |
1.11 |
Поверка течеискателя масс-спектрометрического гелиевого Heliot900 |
шт. |
1 |
2 |
Пуско-наладка, ввод в эксплуатацию и инструктаж персонала специалистом, аттестованным по ПБ 03-440-02 |
усл. |
1 |
Купить стенд контроля герметичности ВАКТРОН
RussianGost | Официальная нормативная библиотека — ГОСТ 1465-80
Товар содержится в следующих классификаторах:
ПромЭксперт » РАЗДЕЛ I. ТЕХНИЧЕСКИЙ РЕГЛАМЕНТ » V Тестирование и контроль » 4 Тестирование и контроль продукции » 4.12 Испытания и контроль продукции металлургической промышленности » 4.12.6 Металлические изделия »
Классификатор ISO »
25 МАШИНОСТРОЕНИЕ »
25.100 режущих инструментов »
25. 100.60 Файлы »
Национальные стандарты » 25 МАШИНОСТРОЕНИЕ » 25.100 Режущие инструменты » 25.100.60 Файлы »
Национальные стандарты для сомов » Последнее издание » G Машины, оборудование и инструменты » G2 Промышленные инструменты и аксессуары » G24 Инструменты для рукоделия (слесарные, столярные и др.)) »
В качестве замены:
ГОСТ 1465-69 — Файлы
.ГОСТ 5.1625-72 — Выключатели автоматические однополюсные типа АК63-1. Требования к качеству сертифицированной продукции
ГОСТ 5.2237-74 — Напильники круглые. Требования к качеству сертифицированной продукции
ГОСТ 5.2309-76 — Тиски плоские острые. Требования к качеству сертифицированной продукции
Ссылки на документы:
ГОСТ 1435-90 — Прутки, полосы и рулоны из инструментальной стали нелегированной
.
ГОСТ 18088-83 — Инструмент металлорежущий, алмазный, дереворежущий и слесарный.Слесарь по упаковке, маркировке, транспортировке и вспомогательный
ГОСТ 23726-79 — Резка металлов и деревообработка. Приемка
ГОСТ 5210-82 — Сталь горячекатаный профилированный для напильников, напильников и долот
.ГОСТ 5950-73 — Прутки и полосы из инструментальной стали сплава
.ГОСТ 8.051-81 — Государственная система обеспечения единства измерений. Допустимые погрешности измерения линейных размеров до 500 мм
ГОСТ 9.014-78 — Единая система защиты от коррозии и старения.Временная защита изделий от коррозии. Общие требования
Ссылка на документ:
ГОСТ 13938.13-93 — Медь. Методы определения кислорода
ГОСТ 17261-2008 — Цинк. Методы атомно-эмиссионного спектрографического анализа.
ГОСТ 17261-77 — Цинк. Спектральный метод анализа
ГОСТ 17262.1-78 — Кадмий. Спектральный метод определения меди, никеля, свинца и таллия
ГОСТ 22598-93 — Сплавы на никелевой и малоникелевой основе. Метод определения кислорода
ГОСТ 23116.2-78 — Кадмий особой чистоты. Метод спектрографического определения ртути
ГОСТ 24941-81 — Камни. Методы определения механических свойств прессованием сферическими инденторами
ГОСТ 28052-97 — Титан и титановые сплавы. Методы определения кислорода
ГОСТ 3221-85 — Алюминий первичный. Методы спектрального анализа
ГОСТ 5170-73 — Ремкомплекты пневматических шин. Технические характеристики
ГОСТ 5726-2013 — Масла моторные.Метод определения моющих свойств
ГОСТ 9758-2012 — Заполнители неорганические пористые для строительных работ. Методы испытаний
ГОСТ Р 53542-2009 — Двигатели авиационные и их компоненты. Пайка высоколегированных сталей в вакууме. Общие требования к технологическому процессу
И 1.09-10: Инструкция по подключению изолированных жил проводов и кабелей
РД 15-13-2008 — Методические указания по экспертизе промышленной безопасности компрессорных установок угольных шахт и шахт
РД 15-14-2008 — Методические указания по экспертизе промышленной безопасности одноковшовых экскаваторов
.
РД 22-28-32-94 — Альбом карт типовых технологических процессов ремонта методами сварки и наплавки узлов грузоподъемных кранов
РД 34.10.102-91 — Предусмотренные количественные прибавки на средства механизации, специальные приспособления и инструмент для капитального ремонта основного энергетического оборудования ТЭЦ
РД 34.10.103 — Отраслевые нормы по инструментам, оборудованию, материалам и вспомогательным средствам для ремонта и восстановления газоочистного оборудования термоэлектрических мощностей
РД 34.20.261: Типовые инструкции по сварке неизолированных проводников с использованием термитных картриджей
РД 34.20.504-94 — Типовые методические указания по эксплуатации воздушных линий электропередачи напряжением 35-800 кВ
РД 34.39.201: Руководство по установке систем водяного пара и пара на тепловых электростанциях
РД 34.46.605 — Трансформаторы на напряжение 110-1150 кВ мощностью 80 МВxА и выше
СНиП 5.02.02-86: Нормы требований к строительному инструменту
СО 153-34.10.109-88 — Нормативные припуски на инструменты, приспособления и оборудование, электроинструменты, ручные инструменты и специальные принадлежности для ремонта и эксплуатации тепловых электростанций, гидроэлектростанций, электрических и трубопроводных тепловых сетей
VSN 003-88: Рекомендации по проектированию и установке пластиковых трубопроводов
Инструкция по СНиП 3.05.01-85: Пособие по изготовлению и приемке работ при установке систем вентиляции и кондиционирования
.РД 34.10.108-89: Таблицы комплектации предприятий электрических сетей Минэнерго СССР малой механизацией, приборами, такелажным оборудованием, ручным инструментом и приспособлениями для ремонта и обслуживания воздушных линий электропередачи напряжением 0,4 -750 кВ и кабельные линии 0,4-35 кВ
РД 34.47.602-75 — Методические указания по капитальному ремонту выключателя масляного ВМД-35
.РД 34.47.603-79: Методические указания по капитальному ремонту выключателей высоковольтных трехполюсных ВМПЭ-10
.РД 34.47.605-78 — Методические указания по капитальному ремонту масляного выключателя ВМГ-10-630-20 и ВМГ-10-1000-20
.РД 34.47.612-86 — Методические указания по капитальному ремонту масляных выключателей ВТ-35-630-10ВИ и ВТД-35-630-10ВИ
РД 34.47.613-74 — Методические рекомендации по капитальному ремонту выключателя масляного ВМП-10П
.РД-15-15-2008: Методические указания по порядку проведения экспертизы промышленной безопасности шахтных электровозов
Постановление 137 / 9-50: Типовые сводные нормы времени на ремонт сантехнического и канализационного оборудования
Клиенты, которые просматривали этот товар, также просматривали:
|
ВАШ ЗАКАЗ ПРОСТО!
Русский Гост.com — ведущая в отрасли компания со строгими стандартами контроля качества, и наша приверженность точности, надежности и аккуратности является одной из причин, почему некоторые из крупнейших мировых компаний доверяют нам обеспечение своей национальной нормативно-правовой базы и перевод критических, сложных и конфиденциальная информация.
Наша нишевая специализация — локализация национальных нормативных баз данных, включающих: технические нормы, стандарты и правила; государственные законы, кодексы и постановления; а также кодексы, требования и инструкции агентств РФ.
У нас есть база данных, содержащая более 220 000 нормативных документов на английском и других языках для следующих 12 стран: Армения, Азербайджан, Беларусь, Казахстан, Кыргызстан, Молдова, Монголия, Россия, Таджикистан, Туркменистан, Украина и Узбекистан.
Размещение заказа
Выберите выбранный вами документ, перейдите на «страницу оформления заказа» и выберите желаемую форму оплаты. Мы принимаем все основные кредитные карты и банковские переводы.Мы также принимаем PayPal и Google Checkout для вашего удобства. Пожалуйста, свяжитесь с нами для любых дополнительных договоренностей (договорные соглашения, заказ на поставку и т. Д.).
После размещения заказа он будет проверен и обработан в течение нескольких часов, но в редких случаях — максимум 24 часа.
Для товаров, имеющихся на складе, вам будет отправлена ссылка на документ / веб-сайт, чтобы вы могли загрузить и сохранить ее для своих записей.
Если товары отсутствуют на складе (поставка сторонних поставщиков), вы будете уведомлены о том, для выполнения каких товаров потребуется дополнительное время.Обычно мы поставляем такие товары менее чем за три дня.
Как только заказ будет размещен, вы получите квитанцию / счет, который можно будет заполнить для отчетности и бухгалтерского учета. Эту квитанцию можно легко сохранить и распечатать для ваших записей.
Гарантия лучшего качества и подлинности вашего заказа
Ваш заказ предоставляется в электронном формате (обычно это Adobe Acrobat или MS Word).
Мы всегда гарантируем лучшее качество всей нашей продукции.Если по какой-либо причине вы не удовлетворены, мы можем провести совершенно БЕСПЛАТНУЮ ревизию и редактирование приобретенных вами продуктов. Кроме того, мы предоставляем БЕСПЛАТНЫЕ обновления нормативных требований, если, например, документ имеет более новую версию на дату покупки.
Гарантируем подлинность. Каждый документ на английском языке сверяется с оригинальной и официальной версией. Мы используем только официальные нормативные источники, чтобы убедиться, что у вас самая последняя версия документа, причем все из надежных официальных источников.
RussianGost | Официальная нормативная библиотека — ГОСТ 6396-78
Товар содержится в следующих классификаторах:
ПромЭксперт » РАЗДЕЛ I. ТЕХНИЧЕСКИЙ РЕГЛАМЕНТ » V Тестирование и контроль » 4 Тестирование и контроль продукции » 4.12 Испытания и контроль продукции металлургической промышленности » 4.12.6 Металлические изделия »
Классификатор ISO » 25 МАШИНОСТРОЕНИЕ » 25.100 режущих инструментов » 25.100.20 Фрезы »
Национальные стандарты » 25 МАШИНОСТРОЕНИЕ » 25.100 Режущие инструменты » 25.100.20 Фрезы »
Национальные стандарты для сомов » Последнее издание » G Машины, оборудование и инструменты » G2 Промышленные инструменты и аксессуары » G23 Инструменты для механической обработки »
В качестве замены:
ГОСТ 6396-68 — Фрезы червячные, оснащенные твердым сплавом
.Ссылки на документы:
ГОСТ 1050-88 — Прокат калиброванный из углеродистой конструкционной качественной стали со специальной обработкой поверхности.Общие технические условия
ГОСТ 14034-74 — Отверстия центральные. Размеры
ГОСТ 1412-85 — Чугун с чешуйчатым графитом
.ГОСТ 15527-2004 — Сплавы медно-цинковые (латуни), обработанные давлением. Оценки
ГОСТ 15527-70 — Сплавы медные цинковые, обработанные давлением (латуни). Типы
ГОСТ 18088-83 — Инструмент металлорежущий, алмазный, дереворежущий и слесарный. Слесарь по упаковке, маркировке, транспортировке и вспомогательный
ГОСТ 23360-78 — Основные нормы взаимозаменяемости.Ключи муфты с призматическими ключами. Размеры ключей и сечения шпоночных пазов. Пределы и посадки
ГОСТ 23726-79 — Резка металлов и деревообработка. Приемка
ГОСТ 25334-94 — Хвостовики цилиндрические для фрез. Основные размеры
ГОСТ 25400-90 — Наконечники твердосплавные паяные типа 21. Конструкция и размеры
.ГОСТ 25557-2006 — Станки конические. Основные размеры
ГОСТ 25557-82 — Конические станки. Основные размеры
ГОСТ 25706-83 — Лупы
.ГОСТ 2789-73 — Шероховатость поверхности.Параметры и характеристики
ГОСТ 2848-75 — Конус инструментальный. Допуски. Методы и средства контроля
ГОСТ 3882-74 — Сплавы твердые спеченные. Типы
ГОСТ 4543-71 — Сталь конструкционная легированная
.ГОСТ 4872-75 — Изделия из твердых сплавов спеченные для режущего инструмента. Технические характеристики
ГОСТ 8.051-81 — Государственная система обеспечения единства измерений. Допустимые погрешности измерения линейных размеров до 500 мм
ГОСТ 9013-59 — Металлы.Метод измерения твердости по Роквеллу
ГОСТ 9378-93 — Образцы сравнения шероховатости
. Клиенты, которые просматривали этот товар, также просматривали:
|
ВАШ ЗАКАЗ ПРОСТО!
Русский Гост.com — ведущая в отрасли компания со строгими стандартами контроля качества, и наша приверженность точности, надежности и аккуратности является одной из причин, почему некоторые из крупнейших мировых компаний доверяют нам обеспечение своей национальной нормативно-правовой базы и перевод критических, сложных и конфиденциальная информация.
Наша нишевая специализация — локализация национальных нормативных баз данных, включающих: технические нормы, стандарты и правила; государственные законы, кодексы и постановления; а также кодексы, требования и инструкции агентств РФ.
У нас есть база данных, содержащая более 220 000 нормативных документов на английском и других языках для следующих 12 стран: Армения, Азербайджан, Беларусь, Казахстан, Кыргызстан, Молдова, Монголия, Россия, Таджикистан, Туркменистан, Украина и Узбекистан.
Размещение заказа
Выберите выбранный вами документ, перейдите на «страницу оформления заказа» и выберите желаемую форму оплаты. Мы принимаем все основные кредитные карты и банковские переводы.Мы также принимаем PayPal и Google Checkout для вашего удобства. Пожалуйста, свяжитесь с нами для любых дополнительных договоренностей (договорные соглашения, заказ на поставку и т. Д.).
После размещения заказа он будет проверен и обработан в течение нескольких часов, но в редких случаях — максимум 24 часа.
Для товаров, имеющихся на складе, вам будет отправлена ссылка на документ / веб-сайт, чтобы вы могли загрузить и сохранить ее для своих записей.
Если товары отсутствуют на складе (поставка сторонних поставщиков), вы будете уведомлены о том, для выполнения каких товаров потребуется дополнительное время.Обычно мы поставляем такие товары менее чем за три дня.
Как только заказ будет размещен, вы получите квитанцию / счет, который можно будет заполнить для отчетности и бухгалтерского учета. Эту квитанцию можно легко сохранить и распечатать для ваших записей.
Гарантия лучшего качества и подлинности вашего заказа
Ваш заказ предоставляется в электронном формате (обычно это Adobe Acrobat или MS Word).
Мы всегда гарантируем лучшее качество всей нашей продукции.Если по какой-либо причине вы не удовлетворены, мы можем провести совершенно БЕСПЛАТНУЮ ревизию и редактирование приобретенных вами продуктов. Кроме того, мы предоставляем БЕСПЛАТНЫЕ обновления нормативных требований, если, например, документ имеет более новую версию на дату покупки.
Гарантируем подлинность. Каждый документ на английском языке сверяется с оригинальной и официальной версией. Мы используем только официальные нормативные источники, чтобы убедиться, что у вас самая последняя версия документа, причем все из надежных официальных источников.
ВИДЕО: Скрытность заврженега Камна, ки je postal temelj!
16.04.2017, 15:35 Тон Gorjup
Na Trgu svetega Petra ki ga je danes krasil pravi cvetlični vrt iz 35 tisoč cvetov, je papež Frančišek opozoril, da Kristusovo vstajenje ni praznik z Veliko rožami.Ni to, je več. Je skrivnost zavrženega kamna, ki je postal temelj našega bivanja. Kristus je vstal. Помени к.
Papež Frančišek je na praznik Gospodovega vstajenja daroval slovesno sveto mašo na Trgu pred baziliko sv. Петра, ки со жо наполнили številni romarji z all koncev sveta. Чеправ при маши ни белая предвидена придига, е папеж франчишек по крайши тихоти по евангелии в бизантинскем богослужнем додатку спреговорил.Spomnil je na pot vere, ki sta jo na Veliko noč prehodila Peter in Janez. Od praznega groba sta srcem zaprtim zaradi žalosti poraza, kar je za njiju представлала smrt njihovega učitelja, ostala zaklenjena skupaj z другими апостоли до večera, čeprav sta angel. Sveti oče je spomnil, da Cerkev ne preneha ob naših porazih odgovarjati zaprtim in boječim srcem, da je Gospod vstal od mrtvih, saj ne gre za fantazijo.
«В те культури картиранья, кьер тисто, кар ни веч упорабно, гре по поти» упораби в заврзи «.Kjer je to, kar ni več uporabno, zavrženo. Ta zavrženi kamen je vir življenja. In mi? «Se je vprašal papež.
Туди ми, камни разрезы по земле, по тей земли болезни, трагедии. Z vero v vstalega Križanega imamo smisel sredi tolikih nesreč, smisel, da gledamo onkraj, smisel, da rečemo, da ni zidu, je obzorje, je življenje, je veselje, je križ svojo dvoumnostjo.Глей напрей, не запри се, ти каменчек, сай имаш смисел в живленю, сай си каменчек, ки га е спрейел камен, ки га е злоба греха завргла.
Kaj nam danes pravi Cerkev pred tolikimi tragedijami? To, preprosto to, da zavržen Kamen, ni zavržen Kamen. Kamenčki, ki verujejo in se držijo tega Kamna, niso zavrženi. Imajo smisel. S tem občutjem Cerkev ponavlja v notranjosti srca: »Kristus je vstal!«
Папеж Франчипшек © CTV
Malo pomislimo, vsak od nas, na vsakodnevne težave, na bolezni, ki smo jih preživeli, ki jih kdo od sorodnikov ima, na vojne, na človeške tragedije.Препросто с понижным гласом, брез рож, пред Богом, пред нами: «Не вэм како бо то, а сем готов, да е Кристус встал в на ставим». Bratje in sestre, mi prihaja, da vam rečem: «Ko se boste vračali domov, ponavljajte v svojih srcih:» Kristus je vstal! «
Slovesno tudi v bizantinskem duhu
Posebnost letošnje papeževe praznične maše je narekovalo sočasno praznovanje velike noči po gregorijanskem in julijanskem koledarju. Зато е евангелию следил спев стихов в стехер из бизантинскега богослужения.Praznična besedila, ki jih je ohranila vzhodna Cerkev, nekoliko spominjajo na našo hvalnico velikonočni sveči in razodevajo vesele nad Kristusovo zmago nad smrtjo.
Praznični sveti maši je sledil papežev tradicionalni nagovor oziroma velikonočno voščilo z blagoslovom Urbi et Orbi — место в свете. Prevedel ga je br. Миран Шпелич:
Драги брате в сестре!
Благословено велико ночь!
Датчане по всему свету Церкев обнаружила полностью спорочило првих учетцев: »Jezus je vstal!« — »Resnično je vstal, kakor je napovedal!«
Стародавни великоночни празник, спомин на освободитев юдовскега люди из суженства, доспе тукай до своего дополнения: Иезус Кристус нас е с своим вступлением освободил сужь в одиночестве греха.
Kadar pustimo, da nam zavlada greh, mi vsi zaidemo s prave poti in blodimo kot izgubljene ovce. Bog sam, naš Pastir, pa nas je prišel iskat; да би нас решил, сэ его склонил все до понижанья на крижу. В данес лахко ознаньямо: «Встал е добри пастир, ки е за свое чредо шел смрти напроти, алелуйя!» (Римски мисал, 4. великон. Нед., Обх. Спев).
Во всех часих Встали пастыр нейтрудно ище нас, свое брате, изгублено в пущах тега света. In nas z znamenji svojega trpljenja — z ranami svoje usmiljene ljubezni — priteguje na svojo pot, pot življenja.Tudi danes si zadaja na rame mnogo naših bratov in sester, ki jih stiska zlo v svojih raznih Oblikah.
Встали пастыр гре искат изгублене в лабиринтих самотэ в одриньености; напроти джим гре по братих в сестрах, ки сие знайо споштливо в нежно приближати тер дайо слишати тем льюдем ньегов глас, николи позаблжени глас, ки йи кличе к приятиям з Богом.
Na rame jemlje tiste, ki so žrtve old in novih suženjstev: nečloveškega dela, nedovoljenega trgovanja, izkoriščanja in diskriminacije, hudih odvisnosti.На раме jemlje отроке в младостнике, ки со jih prikrajšali za brezskrbnost, da jih lahko izkoriščajo; na rame jemlje tudi tiste, ки imajo ranjeno srce zaradi nasilja, ki so mu podvrženi znotraj zidov lastnega doma.
Встали пастыр спремля на поти тисте, ки так присланы пустити свое действие заради обороженых спопадов, терористических нападов, поманиканья, насильных режимов. Tem prisilno preseljenim pomaga, da srečajo brate pod slehernim nebom, da z njimi Delijo kruh in upanje na skupni poti.
В заплетеных в различных драматических меднарядных догодках на Встали Господ води кораке тистих, ки своего права в мире; in naj da odgovornim v politiki pogum, da se izognejo širjenju sporov in ustavijo trgovino z orožjem.
В тех часих най ше посебей подпира напоре тистих, ки се дейвно трудийо принашати олайшанье в толажбо гражданскому пребивалству в Сириджи, ки е жртев войне, ки не неха сеяти грозе в смрти. Naj nakloni mir vsemu Bližnjemu vzhodu od Svete dežele pa do Iraka в Джемне.
Naj bližina Dobrega pastirja ne umanjka prebivalcem Južnega Sudana, Sudana, Somalije in Demokratične republike Kongo, ki trpijo zaradi neskončnih sporov, ki jih otežuje še pomanjkanje afrišké jekéra.
Папеж Франчишек по Благослову Урби и Орби © стр. доктор Роберт Бахчич
Встали Jezus naj podpira napore all, ki se še posbej v Latinski Ameriki zavzemajo za zagotavljanje skupnega dobrega v družbi, ki je pogosto zaznamovana s policyičnimi in družbenimi kis.О да би могли зградити мостове диалог во взятии в бою зопер рано корупция в исканю занесливых миролюбних решитев за споре. Tako bodo napredovale in se utrdile demokratične ustanove ob polnem spoštovanju pravne države.
Добри пастыр най помага украини, ки йо ше ведно пести крвави спор, да бо нашла лозунг, в най спремля побуде, ки со усмерьене к олайшанью драме тистих, ки трпийо последице ле-тега.
Встали Господ, ки не неха обсипати европейске селин со своим благословом, най подели упанье тистим, ки преживляйо тренутке кризе в тежав, зласти заради великега поманьканья дела ше посебей за младенцем.
Dragi bratje in sestre, letos kristjani all veroizpovedi skupaj praznujemo veliko noč. Naj tako enoglasno odmeva po all koncih zemlje najlepše oznanilo: »Gospod je resnično vstal, kakor je napovedal!« On, ki je premagal temo greha in smrti, naj da mir našim dnem.
Благословено велико ночь!
مطحنة تي أبعاد معدنية. رق التحكم والاختبار
معيار الدولة
Обновить Ssr.
القرار لجنة الدولة معايير مجلس وزراء الاتحاد السوفياتي مؤرخ ي 21 سطس 1972 مم 1637 تلسليس الدولة لاتحاد السوفياتي مؤرخ ي 21 سطس 1972 год 1637 تلسليس الدولة للالة الل الل علي وسلم
رار الدولة المعيار من 04.06.85 1574
تمتد الخبرة إلى 01.01.87
ن الفشل ي الامتثال للمعيار محاكمته بموجب القانون.
ينطبق ا المعيار على واطع فولاذية عالية السرعة لتعامل مع الأخاديد على ل حرف T وفقا لتحقيار ГОСТ 1574-75.
يتوافق المعيار بالكامل مع ST SEV 115-79 و St SEV 4632-84 من حيث القواطع لمعالجة الأخاديد على لفيرف الاديد على ليرف الاديد عل ليرف الاديد عل ليرف الاديد عل لير الاديد عل لير اللاديد عل لير اللاديد عل لير اللاديد عل لير اللالم
1. نواع ، التصميم والأحجام
1.1. Текущий рейтинг:
1 — القواطع مع عرقوب سطواني للأخادير ات الأبعاد ومن 5 لى 36 месяцев بزاوية ميل من اهتز الأخدود د
2 — القواطع مع عروب مخروطي لأخاديد بالأبعاد ومن 6 لى 54 чел. من نسختين:
1 — مع سنان طبيعية مع زاوية ميل من هز الأخدود (O = 10 ° ؛
2 — مع سنان كبيرة مع اوية ميل من هز الأخدود (O = 15… 25 درجة.
الطبعة الرسمية
ب) النوع 2 الإعدام 2 (لعنة 2 الجدول 2)
■ ب ي A-A 3
الجدول 2 الأبعاد في مم. |
الملحق 2 لزامي
الأبعاد الرئيسية للمجلدات النوع 1 المصنعة بناء على لب16
9018
اسمى ، صورى شكلى ، بالاسم فقط т.ttlgp | ||||||||
الملحق 3 لزامي
روط ع التشغيل لمعالجة الأخاديد على ل حرف T
1.مصممة القواطع لمعالجة الأخاديد على شكل حرف T على الآلات ، الدقة المقابلة والصلابة المنشأة لهم.
2. يجب أن تلبي الأداة المساعدة معايير الدقة.
3. المواد المعالجة:
ب 2 »
للحصول على واطع من ولنوع 2 التنفيذ 2 — الصلب 45 وفقا ل GOST 1050-74 لابة لا ر من HB 197.
.4. يجب ن تتوافق وضاع القطع تلك المحددة ي الفقرة 4.4 وفي الجدول. 3 من هذا المعيار.
5. يتم استخدام حل Эмульсол 5% في الماء (بالوزن) بمعدل تدفق من 6-8 لتر / دقيقة كمادة سائلة سائل تبريد التشحيم.
لقطع القطع 1 يتم التبريد بواسطة طائرة من الهواء.
6. ي قطع الشغل تم الحصول على الأخدود المستطيل بشكل مسبق ، يساوي عرض قطر الرقبة دي + 2 الحول على الأخدود المستطيل بشكل مسبق ، يساوي عرض قطر الرقبة دي + 2 الحول عل الدود.
7. يتم احتساب روف التشغيل هذه على مقاومة الضمان بين التدفقات — 60 دقيقة.
(دم بالإضافة إلى ذلك ، itch. رقم 3).
м.»ن قبول رضات حواف القطع الرئيسية لقطع الأسنان بالنسبة لمحور عرقوب يجب ن يكون:»
الفقرة 2L4. يتم تحديد الفقرة الأولى ي محرر NBVYI.
يجب أن يتم ذكر الفقرة 2,15 في الطبعة الجديدة:.. «2L5 متوسط \ u200b \ u200b ومحدد فترات المقاومة لجميع أقطار القطع Cut-1 و Тип 2 أثناء معالجة الرقم الهيدروجيني الحديد الزهر والصلب ST45 تحت ظروف الاختبارات المثبتة في القسم 4, يجب أن يكون : G CF * = 60 دقيقة ، TU = 25 دقيقة «:
القسم 2 تكمل البند — 2.16: «2.16. يتمثل معيار القواطع المنتفخة في تحقيق ارتداء مسموح به على السطح الخلفي يساوي المرلء اللي يساوي المرلء اليمحدد 9.
الجدول 3. | |||||||||||||||||||||||||||||||||||||||||
|
الأقسام 3 ، 4 قف في الطبعة الجديدة:
«3.قواعد القبول —
3.2. يتم راء اتبارات واطع لتحديد مؤشرات الموثوقية على الأقل 5 مطاحن.
للسيطرة على متوسط \ u200b \ u200b ترة الاختبار يتم راء الاختبار مرة واحدة ل لاث سناتات الاتبار مرة واحدة.
يجب ن تعرض الاختبارات للقواطع بقطر 18-25 и 50 минут.
يسمح له بمزيد من اختبار قواطع ار أخرى.
4. رق الرصد
4.1. يجب راء القواطع الاختبارات في آلات طحن إجمالية ومحددة للأغراض الخاصة المطابقة للدقة والصلناة الللية الللناشأة الللية ومحددة للراض الخاصة الم ابقة للدقة والصلنااة املللنابشأة الللية.
4.2. يجب اختبار نواع الأنواع 1 و 2 من عدام 1 على مقاتلي الحديد الزهر المشيك CZ Mak 18 وفقا ل ГОСТ 1412! -85 لابة 180 … 220 HV • • • »
Добавить в избранное
4.3. يجب.
الانحراف المسموح به لقيمة سرعة القطع من الجدول المشار إليها في الجدول. يجب ن يكون 4 من حدود التغيير في قيمة V * S ي ون 10.
4.4. يجب ن يكون ول الطحن الكلي عند اختبار الأداء 500 ملم على الأقل.
4.5. بعد الاختبار على الأداء على حواف القطع ، يجب ألا تكون القواطع رقائق وعيوب أخرى. يجب أن تكون القواطع بعد الاختبار مناسبة لمزيد من العمل.
4.6. يجب ن تكون يم القبول ي متوسط \ u200b وفترات المقاومة التي تم نشاؤها أقل: لها -68 دقيقة ، TU -28.
4.7. عند العمل على الصلب باعتبارها البنود CM LSH و YU
يجب تطبيق حل Emulsol 5 ي الماء (بالوزن) بمعدل تدفق من 6-8 لتر / دقيقة ؛ عند العمل على الحديد الزهر — تبريد طائرة من الهواء إزالة الرقائق من منطقة القطع. وبعد
(تابع انظر ص 132)
(استمرار التغيير إلى G01T 7063-72) الجدول 4. | |||||||||||||||||||||||||||||||||
|
4.9. يتم التحكم في المظهر بصريا.
4.10. يجب التحقق من معلمات خشونة السطح للأسطح بالمقارنة مع عينات خشونة السطح وفقا ل ГОСТ 9378-75 أو مع أدوات مثالية لها قيم خشونة الأسطح من الأسطح غير المحددة في Л. 2.10.
يتم تنفيذ المقارنة بصريا بمساعدة اج مكبرة 2 X وفقا ل GOST 2 & 7 | 0В-Ср.
4 مهورية 1. يجب ألا يكون خطأ ياس القاطع المعلمات الهندسية ر:
عند قياس الأبعاد الخطية للقيم المحددة ي ГОСТ 8.051-81 ؛
عند قياس الزوايا — 35 يمة القبول في الزاوية التي تم التحقق منها ؛
عند مراقبة ل وموقع الأسطح — 25 лет назад العبول في المعلمة التي تم التحقق منها.
الملحق 3 استبعاد.
(IUS № 2 1987 г.)
الفقرة 2.15. استبدال التعييين: SCh28 على «SCH 18 وفقا ل GOST 1412-85» ،
القسم 3 (الاسم) الفقرة 3.1. استبدل الكلمات: «واعد القبول» على «القبول».
يتم ذكر الفقرة 3.2 في الطبعة الجديدة:.. «3.2 ينبغي إجراء اختبارات دورية, بما في ذلك قواطع الاختبار لمتوسط \ u200b \ u200b فترة المقاومة, مرة واحدة كل ثلاث سنوات, لفترة مقاومة بنسبة 95% مرة واحدة سنويا على الأقل 5 مطاحن
يجب إجراء تخفيضات الاختبار على أي أحجام لطحن النطاق المشار إليه في الجدول.أربعة «.
الفقرات 4.3 ، 4.6. استبدل الكلمة: «تعيين» إلى «95 ٪».
الجدول 4. عدد «ر الطاطع D». استبدال الحجم: 12.5 لى 11.0 12.5.
يتم ر القسم 5 ي الطبعة الجديدة:
«مسة. النقل والتخزين
النقل والتخزين — по ГОСТ 18088-83. «
الملحق 1. الجدول 1 افة أح.0ام ر D 11.0 50.0 ؛ 60 ملم والقيم المقابلة: ____
1.2. يجب ن يتطابق التصميم والأبعاد الرئيسية من واطع النوع النوع 1 المحدد. 1 والجدول. 1 واطع القاطع — المشار إليها في الجحيم.2 والجدول. 2.
|
Размер عل التعيين الرطي من القاطع الري من الطاطع من ري من القاع النوع 1 باستخدام حجم اسمي Groove A = 14 Размер:
العلاقات العامة.يتم تحديد الأبعاد الرئيسية من النوع 1 المصنعة بناء على طلب العميل ، ي التطبيق المطلوب 2.
الجدول 2 | ||||||||||||||||||||||||||||||||||||||||||||||||||||||||||||||||||||||||||||||||||||||||||||||||||||||||||||||||||||||||||||||||||||||||||||||||||
|
مثال على التعيين الشرطي للقاطع من النوع 2 من الإصدار 1 مع حجم اسمي من Паз О \ u003d 6 مم;
(الطبعة المعدلة ، تغيير رقم 2 3).
1,2 А ، 1.26. (مستبعد ، التغيير رقم 3).
1,4. يتم إجراء أبعاد نصف قطر الأقارب والشامدات غير المحددة في هذا المعيار على أسباب تكنولوجية.
1,5. يشار إلى عناصر التصميم ومعلمات ع هندسية في التطبيق الموصى به.
2. المتطلبات الفنية
2.1. (مستبعد ، التغيير رقم 2).
2.2. يجب ن تكون القواطع مصنوعة من الفولاذ العالي السرعة وفقا ل ГОСТ 19265-73.
(الطبعة المعدلة ، التغيير رقم 2).
2.3. يجب ن تصنع القواطع ملحومة. في مكان اللحام غير مسموح به المصارف والدخل والحرقة والمعادن تواجه الشقوق الدائري.
النوع 1 واطع لأخاديده بحجم اسمي يصل لى 12 ملم لاملة يمكن ن تكون معنوعة لبة.
2.4. يجب ن تكون مقاطعات السحاب مصنوعة من ال ولاذ ال 45 ولا ل GOST 1050-74 و من ولاذ ال 40X وا لوست 4543-71.
2,5. يجب ن يكون القاطع صلابة:
ع من الصلب عالية السرعة HRC 62 … 65 ؛
ع ل »» »
عرقوب أسطواني.
واطع املة — HRC 35… 55 ؛
الواطع الملحومة — HRC 30 … 50 عل عة واحدة عل عة واحدة عل الأقل واحدة عل الأقل واحدة عل الأقل 1/2 ول من ناية عرقوب
علة عرقوب مخروطي — HRC 30 … 50.
2.6. على سطح العمل ، يجب ألا يكون القاطع طبقة ومؤنفة ديكوتشلترا وأماكن ذات صلابة منخفضة.
2.7. على سطح القاطع ، لا ينبغي أن تكون هناك حاجة لى سطح القاطع ، الشقوق ، الأزيز ، تشيرنوفين ، ماين م
2.8. لا يسمح بالدوائف في حواف القطع من واطع الأسنان.
2.9. لا ينبغي أن يكون تخفيضات القواطع المركزية أماكن رعاية وتطويرها..3.2 ؛
بالنسبة لى القاطع بقطر 12,5 لى 40 месяцев:
0,02 мм — انين من الأسنان المجاورة ، 0,04 мм — على الطاحونة بأكملها ؛ للقواطع بقطر من 50 ل 95 Просмотров:
0,03 ملم — انين من الأسنان المجاورة ؛ 0,05 мм — وال المطحنة.
2.14. يجب ألا يتجاوز الضرب الميكانيكي لخفض جزء العمل:
руб. 12,5 чел. 40 чел. — 0,04 чел. بالنسبة لى القاطع بقطر من 50 لى 95 ملم — 0,05 млн.
2.15. متوسط ترة واطع المقاومة يجب ن تمتثل للتطبيق المطلوب 3.
3. واعد القبول
(الطبعة المعدلة ، التغيير رقم 1).
3.2. (مستبعد ، التغيير رقم 1).
3.3. يجب راء اختبارات دورية مرة واحدة على الأقل كل ثلاث سنوات على الأقل за 10 месяцев.
3,4–3,6. (مستبعد ، التغيير رقم 3).
3,7. يسمح باختبار مقاومة القواطع ي المستهلكين في ظل ظروف الإنتاج.
4. رق الاختبار
4.1. يجب إجراء قطع اختبار الأداء على آلات الطحن. لات الطحن والمساعد
يجب ن تمتثل الأدوات المستخدمة ي الاختبار الدقة والصلابة المنشأة لهم.
(الطبعة المعدلة ، التغيير رقم 3).
4.2. يتم استخدام 5 дюймов (حسب الوزن) حل تشحيم وبريد (حسب الوزن)
(الطبعة المعدلة ، التغيير رقم 4).
4.3. يتم إجراء اختبار المطاحن من أنواع 1 و 2 من الإصدارات 1 على القوالب من الحديد الزهر الرمادي SCh28 وفقا ل ГОСТ 1412-79 HT هنا 170-200, قواطع من النوع 2 من الإصدار 2 — على ثلاجات الصلب الصف 45 في وفقا ل ГОСТ 1050- 74. صلابة HB 184-217.
يتم تقدير القرار من بل الأخدود المستطيل يساوي عرض ر عنق الرحم دي + 2 مم مع بلدل دلبل سفيل دللبل سفيل دللبل سفيل دللبل سفيل يساوي عرض ر عنق الرحم ح
4.4. يجب ن تكون وسائط القطع ناء الاختبار متسقة مع الجدول المحدد ي الجدول. 3.
الجدول 3. | ||||||||||||||||||||||||||
|
(الطبعة المعدلة ، تغيير رقم 2 3).
4.5. يجب ن يكون ول الطحن الكلي عند اختبار الأداء 500 ملم على الأقل.
4.6. بعد الاختبار على حواف القطع ، يجب ألا تكون القواطع رقائق وعيوب أخرى. يجب أن تكون القواطع بعد الاختبار مناسبة لمزيد من العمل.
(الطبعة المعدلة ، التغيير رقم 2).
4.7. يجب مراقبة الأحجام الخطية والأندية والأخبذ الرصم والميكانيكية من لال وسائل القياس العالمية واياس العالمية وااا.
4.8. يجب فحص القاطع الصلابع وفقا لجوست 9013-59 أو ГОСТ 2999-75.
4.9. يجب فحص ونة سطح القاطع لعينات ونة الأسطح وفقا ل ГОСТ 9378-75.
4.10. مظهر القواطع السيطرة بصريا.
5. وضع علامات ، التعبئة والتغليف والنقل والتخزين
5.1. على سطح عنق ل قطع ، يجب تطبيق العلامات التالية بوضوح:
) علامة تجارية الشركة المصنعة ؛
ب) القاطع التعيين ؛
ج) الحجم الاسمي паз а ؛
د) جزء ع الصلب العلامة التجارية.
يسمح بالقطع لى حجم Groove A = 18 مم م بتسمية الأرقام الأربعة الأخيرة من التعيين.
يسمح بوضع علامة على القواطع لتطبيقها على عرقوب تحت حالة الحفاظ على أشكاله الندسية علامة عل القواطع لتطبيقها على عرقوب تحت حالة الحفاظ على اله الندسية ولالك الملعلية ولالك الملعلتلام العلتل الملعلية
5.2. واطع التعبئة الداخلية — WU-1 وفقا لجوست 9.014-78.
(الطبعة المعدلة ، التغيير رقم 4).
5,2 أ. المتطلبات المتبقية لوضع العلامات والتعبئة والتغليف والنقل والتخزين — وفقا ل ГОСТ 18088-83.
(دم بالإضافة إلى ذلك ، itch. رقم 4).
5.3. (مستبعد ، التغيير رقم 3).
5.4-5.9. (مستبعد ، التغيير رقم 2).
القطاع الثامن. 6. (مستبعد ، التغيير رقم 4).
عناصر التصميم والقواطع الهندسية
* السطح الخلفي للقواطع القاطع يمكن ن يكون مصنوعا من ل هكتار أو منحلي.
الجدول 1 الأبعاد في مم. |
عادة بع محظور
عادة بع (سطس 1985) عادة لبع (سطس 1985) مع التعديلات ر،م 2 ، 3 و 4 المعتمدة ي يونيو 1977 براير 1981 ، يونيو 1985 (IUS 7-77، 8-85–81)
يمكن ن تكون السطح الخلفي للقاطع القاطع من ل هكتار و منحلي.
وصف:
تعيين: gst 7063-72.
Обновления: الدخول ي الاتحاد الروسي
الروسي: واطع لمعالجة اللاديد عرى ى.الروف التقنية
العنوان باللغة الإنجليزية: القواطع T- تحة. تحديد.
تاريخ النشر: 01.08.1985
تاريخ مقدمة: 21.08.1972
تاريخ الانتهاء: 01.01.2010
اري اريخ الانتهاء: 01.01.2010 اري 2.منطقة وشروط التطبيق: + ينطبق هذا المعيار على قواطع الفولاذ عالية السرعة لمعالجة الأخاديد على شكل حرف Т.
في حين أن: + ГОСТ 7063-63.
ائمة التغييرات: №0 من (ريج) «تغيير التعديل»
№2 من (рег.) «ترة عرب»
№3 من (рег.) «حة التعبير»
№4 من (рег.) «ترة أعرب»
№5 من (ريج) «ترة أعرب «ن
ر6 معرب «
по ГОСТ 7063-72.
الملاحق إلى gst.
Источник: Соответствует ГОСТ 7063-72. الدخول ي الاتحاد الروسي
تاريخ مقدمة: 01.01.2010
تغيير رقم 2 إل- GOST 7063-72
:01.1978
يتم دمج نص التعديل ي نص أو وصف المعيار.
تيير رقم 3 ل GOST 7063-72
تيير رقم 3 لى ГОСТ 7063-72
تاريخ م000دما:
معيار الدولة
Обновить Ssr.
واطع لمعالجة الأخاديد على شكل T
الظروف التقنية
gst 7063-72.
| СЭ СЭВ 115-79 ، СЭ СЭВ 4632-84)
الطبعة الرسمية
لنة الدولة في الاتحاد السوفياتي بشأن المعايير
УДК 621.914.22: 006.354 ГРУППА G23
معايير الدولة لاتحاد SSR
واطع لمعالجة الأخاديد على شكل حرف T الشروط الفنية
القواطع T- تحة. تحديد.
(СЭ СЭВ 115-79 ، СТ СЭВ 4632-84)
ГОСТ 7063-63.
رار لنة الدولة بمعايير مجلس وزراء الاتحاد السوفياتي في 21 августа 1972 г. 1637 чел.
الدولة المعيار от 04.06.85 N9 1574
تمتد الخبرة إلى 01.01.87
ن الفشل ي الامتثال للمعيار محاكمته بموجب القانون.
ينطبق ا المعيار على واطع فولاذية عالية السرعة لتعامل مع الأخاديد على ل حرف T وفقا لتحقيار ГОСТ 1574-75.
يتوافق المعيار بالكامل مع ST SEV 115-79 و St SEV 4632-84 من حيث القواطع لمعالجة الأخاديد على لفيرف الاديد على ليرف الاديد عل ليرف الاديد عل ليرف الاديد عل لير الاديد عل لير اللاديد عل لير اللاديد عل لير اللاديد عل لير اللالم
1. نواع ، التصميم والأحجام
1.1. Текущий рейтинг:
1 — القواطع مع عرقوب سطواني للأخادير ات الأبعاد ومن 5 لى 36 месяцев بزاوية ميل من هزة الأخدود و 10 °) \ u003d
2 — القواطع مع عروب مخروطي لأخاديد بالأبعاد ومن 6 لى 54 чел. من نسختين:
1 — مع سنان طبيعية مع زاوية ميل من ارك يهز الأخدود = 10 درجة ؛
2 — مع سنان كبيرة مع اوية ميل من هز الأخدود (O = 15… 25 درجة.
الطبعة الرسمية
عادة بع محظور
* عادة بع (سطس 1985) عادة بع (سطس 1985) التعديلات رقم 2 ف 3 ، 4 المعتمدة ي يونيو 1977 براير 1981 ، يونيو 1985 (
1.2. يجب ن يتطابق التصميم والأبعاد الرئيسية من واطع النوع النوع 1 المحدد. 1 والجدول. 1 واطع القاطع — المشار إليها في الجحيم. 2 والجدول. 2.
до | ير طبيعي | حجم الاسمي T- ل أخدود أ | и لا أكثر | لا أكثر | |||||||
Размер عل التعيين الشرطي من اع من النوع 1 باستخدام حجم اسمي Groove A = 14 Размер:
Версия 2252-0305 ГОСТ 7063-72
ملحوظة.يتم تحديد الأبعاد الرئيسية من النوع 1 المصنعة بناء على طلب العميل ، ي التطبيق المطلوب 2.
الجدول 2
الأداء 1. | الأداء 2. | 1 حجم الاسمي Т-образный паз | и لا أكثر | لا أكثر | Месяц | عدد الأسنان G | |||||||
до | до | ||||||||||||
LLGL A. | |||||||||||||
مثال على التعيين الشرطي للقاطع من النوع 2 من الإصدار 1 مع حجم اسمي من канавкой \ u003d \ u003d 6 مم;
Младенец 2252-0151 ГОСТ 7063-72 Носитель 2-х звеньев A = 14 Мгновенный: Мгновенный 2252-0158 ГОСТ 7063-72. ВНИМАНИЕ !!!!!!!!!!!!!!!!!!!!!!!!!!!!!!!!!!!!!!!!!!!!!!!!!!!!!!!!!!!!!!!!!!!!!!!!!!!!!!!!!!!!!!!!!!!!!!!!!!!!!!!!!!!!!!!!!!!!!!!!!!!!!!!!!!!!!!!!!!!!!!!!!!!!!!!!!!!!!!!!!!!!!!!!!!!!!!!!!!!!!!!!!!!!!!!!!!!!!!!!!!!!!!!!!!!!!!!!!!!!!!!!!!!!!!!!!!!!!!!!!!!!!!!!!
(الطبعة المعدلة ، تغيير رقم 2 3).
1,2 A 1,26. (مستبعد ، التغيير رقم 3).
1.3. ثقوب المركز — وفقا لجوست 14034-74.
1,4. يتم إجراء أبعاد نصف قطر الأقارب والشامدات غير المحددة في هذا المعيار على أسباب تكنولوجية.
1,5. يشار إلى عناصر التصميم ومعلمات ع هندسية في التطبيق الموصى به.
2. المتطلبات الفنية
2.1. (مستبعد ، التغيير رقم 2).
2.2. يجب ن تكون القواطع مصنوعة من الفولاذ العالي السرعة وفقا ل ГОСТ 19265-73.
2.3. يجب ن تصنع القواطع ملحومة. في مكان اللحام غير مسموح به المصارف والدخل والحرقة والمعادن تواجه الشقوق الدائري.
النوع 1 واطع لأخاديده بحجم اسمي يصل لى 12 ملم لاملة يمكن ن تكون معنوعة لبة.
2.4. يجب ن تكون مقاطعات السحاب مصنوعة من ال ولاذ ال 45 ولا ل GOST 1050-74 و من ولاذ ال 40X وا لوست 4543-71.
2,5. يجب ن يكون القاطع صلابة:
ع من الصلب عالية السرعة HRC 62 … 65 ؛
ع ل »» »
عرقوب أسطواني.
واطع املة — HRC 35 … 55
الواطع الملحومة — HRC 30 … 50 عل عة واحدة عل عة واحدة عل الأقل واحدة عل الأقل واحدة عل الأقل 1/2 ول من ناية عرقوب
نهاية عرقوب المخروطية — HRC 30 … 50.
2.6. على سطح العمل ، يجب ألا يكون القاطع طبقة ومؤنفة ديكوتشلترا وأماكن ذات صلابة منخفضة.
2.7. على سطح القاطع ، لا ينبغي أن تكون هناك حاجة لى سطح القاطع ، الشقوق ، الأزيز ، تشيرنوفين ، ماين م
2.8. لا يسمح بالدوائف في حواف القطع من واطع الأسنان.. عرون.
(الطبعة المعدلة ، التغيير رقم 2).
2.11. على السطح الخلفي ، على ول حواف القطع ، يسمح بشريط أسطواني بعرض لا يزيد عن 0,05 мес.
2.12. يجب ألا يتجاوز الحد الأقصى للانحرافات لخفض القاطع:
القطر الخارجي ل D-L12 по ГОСТ 25347-82 ؛ ر انك سطواني DZ-L8 ГОСТ 25347-82 ؛ I-HI2 عرض وفقا لجو st 25347-82 ؛ ر العر عنق الرحم DI-HI4 ولا ل GOST 25347-82 ؛
ط 9 »
يتسامح مورس المخاريط — ا لدرجة دقة AT8 وفقا ل ГОСТ 2848-75.
(الطبعة المعدلة ، التغيير رقم 2).
2.13. يجب ألا يتجاوز الضرب الشعاعي للحواف الرئيسية للقطع من واطع الأسنان بالنسبة لمحور عرقوب:
بالنسبة لى القاطع بقطر 12,5 لى 40 месяцев:
0,02 мм — انين من الأسنان المجاورة ، 0,04 мм — على الطاحونة بأكملها ؛ للقواطع بقطر من 50 ل 95 Просмотров:
0,03 ملم — انين من الأسنان المجاورة ؛ 0,05 мм — وال المطحنة.
2.14. يجب ألا يتجاوز الضرب الميكانيكي لخفض جزء العمل:
чел. 12,5 чел. 40 чел. — 0.04 года بالنسبة لى القاطع بقطر من 50 لى 95 ملم — 0,05 млн.
2.15. متوسط ترة واطع المقاومة يجب ن تمتثل للتطبيق المطلوب 3.
3. واعد القبول
3.1. واعد القبول — وا ل ГОСТ 23726-79.
(الطبعة المعدلة ، التغيير رقم 1).
3.2. (مستبعد ، التغيير رقم 1).
3.3. يجب راء اختبارات دورية مرة واحدة على الأقل كل ثلاث سنوات على الأقل за 10 месяцев.
3,4–3,6. (مستبعد ، التغيير رقم 3).
3,7. يسمح باختبار مقاومة القواطع ي المستهلكين في ظل ظروف الإنتاج.
4. رق الاختبار
4.1. يجب إجراء قطع اختبار الأداء على آلات الطحن. لات الطحن والمساعد
يجب ن تمتثل الأدوات المستخدمة ي الاختبار الدقة والصلابة المنشأة لهم.
(الطبعة المعدلة ، التغيير رقم 3).
4.2. يتم استخدام 5 дюймов (حسب الوزن) حل تشحيم وبريد (حسب الوزن)
4.3. يتم إجراء اختبار المطاحن من أنواع 1 و 2 من الإصدارات 1 على القوالب من الحديد الزهر الرمادي SCh28 وفقا ل ГОСТ 1412-79 HT هنا 170-200, قواطع من النوع 2 من الإصدار 2 — على ثلاجات الصلب الصف 45 في وفقا ل ГОСТ 1050- 74.صلابة HB 184-217.
يتم تقدير القرار من بل الأخدود المستطيل يساوي عرض ر عنق الرحم دي + 2 مم مع بلدل دلبل سفيل دللبل سفيل دللبل سفيل دللبل سفيل يساوي عرض ر عنق الرحم ح
4.4. يجب ن تكون وسائط القطع ناء الاختبار متسقة مع الجدول المحدد ي الجدول. 3.
الجدول 3.
(الطبعة المعدلة ، تغيير رقم 2 3).
4.5. يجب ن يكون ول الطحن الكلي عند اختبار الأداء 500 ملم على الأقل.
4.6. بعد الاختبار على حواف القطع ، يجب ألا تكون القواطع رقائق وعيوب أخرى. يجب أن تكون القواطع بعد الاختبار مناسبة لمزيد من العمل.
(الطبعة المعدلة ، التغيير رقم 2).
4.7. يجب مراقبة الأحجام الخطية والأندية والأخبذ الرصم والميكانيكية من لال وسائل القياس العالمية واياس العالمية وااا.
4.8. يجب فحص القاطع الصلابع وفقا لجوست 9013-59 أو ГОСТ 2999-75.
4.9. يجب فحص ونة سطح القاطع لعينات ونة الأسطح وفقا ل ГОСТ 9378-75.
4.10. يتم مراقبة ظهور القاطع بصريا.
5. وضع علامات ، التعبئة والتغليف والنقل والتخزين
5.1. على سطح عنق ل قطع ، يجب تطبيق العلامات التالية بوضوح:
) علامة تجارية الشركة المصنعة ؛
ب) القاطع التعيين ؛
ج) الحجم الاسمي паз а ؛
د) جزء ع الصلب العلامة التجارية.
يسمح بالقطع لى حجم Groove A = 18 مم م بتسمية الأرقام الأربعة الأخيرة من التعيين.
5.2. واطع التعبئة الداخلية — WU-1 وفقا لجوست 9.014-78.
(الطبعة المعدلة ، التغيير رقم 4).
5,2 أ. المتطلبات المتبقية لوضع العلامات والتعبئة والتغليف والنقل والتخزين — وفقا ل ГОСТ 18088-83.
(دم بالإضافة إلى ذلك ، itch. رقم 4).
5.3. (مستبعد ، التغيير رقم 3).
5.4-5.9. (مستبعد ، التغيير رقم 2).
القطاع الثامن.6. (مستبعد ، التغيير رقم 4).
عناصر التصميم والقواطع الهندسية
a) نواع 1 و 2 عدام 1 (لعنة 1 الدول 1)
الدول 1
الأبعاد في مم.
ب) النوع 2 الدعدام 2 (لعنة 2 الودول 2)
* السطح الخلفي للقواطع اللح للقواطع اعطن
الجدول 2
الأبعاد في مم.
(الطبعة المعدلة ، التغيير رقم 2).
الملحق 2 لزامي
الأبعاد الرئيسية للمجلدات من النوع 1 المصنعة بناء على لب العميل
الملحق 3 لزامي
روط ع التشغيل لمعالجة الأخاديد على ل حرف T
1.مصممة القواطع لمعالجة الأخاديد على شكل حرف T على الأجهزة المقابلة للدقة والصلابة المنشأة لهم.
2. يجب أن تلبي الأداة المساعدة معايير الدقة.
3. المواد المعالجة:
لنواع الواطع النواع النواع النواع 1 و 2 عروض 1 — رمادي من الحديد الزهر SCH 18 по ГОСТ 1412-79 HD 170 … 200 لابة ؛
للحصول على واطع من ولنوع 2 التنفيذ 2 — الصلب 45 وفقا ل GOST 1050-74 لابة لا ر من HB 197.
.4. يجب ن تتوافق وضاع القطع تل المحددة ي الفقرة 4.4 وفي الجدول.3 من هذا المعيار.
5. يتم استخدام حل Эмульсол 5% في الماء (بالوزن) بمعدل تدفق من 6-8 لتر / دقيقة كمادة سائلة سائل تبريد التشحيم.
لقطع القطع 1 يتم التبريد بواسطة طائرة من الهواء.
(الطبعة المعدلة ، التغيير رقم 4).
6. ي قطع الشغل تم الحصول على الأخدود المستطيل بشكل مسبق ، يساوي عرض قطر الرقبة دي + 2 الحول على الأخدود المستطيل بشكل مسبق ، يساوي عرض قطر الرقبة دي + 2 الحول عل الدود.
7. يتم احتساب روف التشغيل هذه على مقاومة الضمان بين التدفقات — 60 دقيقة.
(دم بالإضافة إلى ذلك ، зуд.»ن قبول رضات حواف القطع الرئيسية لقطع الأسنان بالنسبة لمحور عرقوب يجب ن يكون:»
الفقرة 2L4. تنشئ الفقرة الأولى في طبعة جديدة: «يجب أن يكون التسامح من الضرب الميكانيكي للجزء العامل من النقاع بعة»
يجب أن يتم ذكر الفقرة 2.15 في الطبعة الجديدة: «2L5 فترات المقاومة المتوسطة والمثبتة لجميع أقطار TYA 1 و Тип 2 Cutter أثناء معالجة الحديد الزهر СМ 18 والصلب ST45 تحت ظروف الاختبارات المثبتة في القسم 4..» يجب أن يكون: 7 CF \ u003d 60 دقيقة ، تو = 25 دقيقة «:
القسم 2 تكمل البند — 2.16:.. «2L6 يتمثل معيار القواطع المنتفخة في تحقيق ارتداء مسموح به على السطح الخلفي يساوي المرء المحدد في الجدول 3.
الأقسام 3 ، 4 قف في الطبعة الجديدة:
«3. واعد القبول —
3.1. واعد القبول — وا ل ГОСТ 23726-79 1.
3.2. يتم راء اتبارات واطع لتحديد مؤشرات الموثوقية على الأقل 5 مطاحن.
للسيطرة على متوسط \ u200b \ u200b ترة الاختبار يتم راء الاختبار مرة واحدة ل لاث سناتات الاتبار مرة واحدة.
يجب ن تعرض الاختبارات للقواطع بقطر 18-25 и 50 минут.
يسمح له بمزيد من اختبار قواطع ار أخرى.
4. رق الرصد
4.1. يجب راء القواطع الاختبارات في آلات طحن إجمالية ومحددة للأغراض الخاصة المطابقة للدقة والصلناة الللية الللناشأة الللية ومحددة للراض الخاصة الم ابقة للدقة والصلنااة املللنابشأة الللية.
4.2. يجب اختبار نواع النواع 1 و 2 الدارات 1 على القوالب الحديد الزهر الرمادي MOX 18 وفقا ل ГОСТ 1412! -85 صلابة 180 … 220 HV, نوع القواطع 2 — على ثلاجات الصلب الصف 415 وفقا لجوست 1050-74 صلابة 197 … 207 НВ.
ي قطع الشغل يتم الحصول على الأخدود المستطيل مسبقا في عرض ر الرقبة (DJ + 2) MM تر بدل Groove DNA 1-2 مم.
4.3. يمكن تنفيذ واطع اختبار الأداء ، ي المتوسط في فترات المقاومة الثابتة (الماومة الثابتة (الماومة الثابتة) (الماومة الابتة) (الواومة الابتة (الواومة الابتة) (الاومة الابتة) 4.
الانحراف المسموح به لقيمة سرعة القطع من الجدول المشار إليها في الجدول. يجب ن يكون 4 من حدود التغيير في قيمة V * S ي ون 10.
4.4. يجب ن يكون ول الطحن الكلي ل P ، أعمال الأطيومة للأداء ما لا يقل عن 500 млн.
4.5. بعد الاختبار على الأداء على حواف القطع ، لا ينبغي رسم القواطع الرسوم المتحركة والعيوب الأخرى. يجب ن تون القواطع P OS LED مناسبة لمزيد من العمل.
4.6. يجب ن تكون يم القبول ي فترات المقاومة المتوسطة والمثبتة ل: T CF -68 دقيقة ، T Y -28 دقيقة.
4.7. ع ع. عند العمل على الحديد الزهر — تبريد طائرة من الهواء إزالة الرقائق من منطقة القطع.
(تابع انظر ص 132)
4.8. قواطع صلابة — وفقا لجوست 9013-59.
4.9. يتم تنفيذ التحكم في المظهر. بصريا.
4.10. يجب التحقق من معلمات خشونة السطح من الأسطح بالمقارنة مع عينات خشونة السطح وفقا ل ГОСТ 9378-75 أو مع أدوات مثالية لها قيم معلمات خشونة من الأسطح غير المحددة أكثر في و.2.10.
يتم راء المقارنة بصريا باستخدام عدسة مكبرة 2 X وفقا ل ГОСТ 2 * 57106-83.
4L * لى مستوى قياس المعلمات الهندسية ، يجب ألا يكون القواطع ر:
عند قياس الأبعاد الخطية للقيم المحددة ي ГОСТ 8.051 — 81 ؛
oRI ياس الزوايا — 35 من القيمة المسموح بها للزاوية التي تم التحقق منها ؛
عند مراقبة ل وموقع الأسطح — 25 من يمة ما يصل إلى * تبدأ ي التحقق من المعلمة. «
الملحق 3 استبعاد.
(IUS № 2 1987 г.)
التغيير رقم 6 GOST 7063-72 واطع لمعالجة الأخاديد على ل حرف T.الظروف التقنية
وافق وضع حيز التنفيذ لال حل لجنة دولة الاتحاد السوفياتي لإدارة جودة المنتجات ومعايير 12,05,903
تاريخ مقدمة 01.12.96
القسم 1. اسم الحاضر ي الطبعة الجديدة: «1. نواع وأحجام». الفقرة 1.2. استبدل الكلمات: «التصميم والأبعاد الرئيسية» على «الأبعاد» ؛
الجدول 1 ي الطبعة الجديدة (ملاحظة لاستبعاد):
الجدول 1
до | تطبيق | حجم الاسمية T-E-Groove مختلفة | и لا أكثر | لا أكثر | عدد الأسنان 2XZ | ||||||
استكمال الداول 1 و 2 ملاحة: «ملاحظة لى الجدول 1 و 2.يسمح باستبدال Chammere Q و F Радиусы R = G و /؟ — Ф ».
الجدول 2. في العمود «عدد الأسنان R \ u003e استبدال القيم:. Z على 2xz; 6 لمدة 2 × 3; 8 ل 2×4; 4 على 2×2
يتم ذكر الفقرة 2,7 في الطبعة الجديدة: «. 21,7 على سطح القاطع, يجب ألا تكون هناك تشققات, آثار التآكل, على أسطح الطحن — مسودة, أماكن مصبوغة, على حواف القطع — مجموعات الإيدز, على عرقوب ومراكز — نغمات»
الفقرات 2.8 2.9 القضاء.
الفقرة 2L5. استبدال التعيين ؛ СЧ28 عل «СЧ 18 согласно ГОСТ 1412-85» ، СТ45 عل «Арт 45 согласно ГОСТ 1050-88» ؛ «شنت» إلى «95 ٪».
الجدول 3 رها ؛ 11.0 Рейтинг: 0.40 (عند معالجة الحديد الزهر) ؛ «-» (عند معالجة الصلب).
النقاط 2 تكمل النقاط — 2.17–2.19: «2.17. على سطح عنق الرحم في ل اطع يجب تطبيقه بوضوح:
العلامة التجارية للشركة المصنعة ؛
تعيين القاطع ؛
حجم الاسمي паз а ؛
ع الصلب العلامة التجارية ؛
ورة لعلامة الدولة على جودة عند تعيينها بالطريقة المنصوص عليها في معيار الدولة USSR.
يسمح بتطبيق علامة جودة الدولة فقط على الملصقات.
يسمح به على القاطع لمعالجة Groove Not من A = 18 ملم تميز فقط الأرقام الأربعة الأخيرة من التعيين.
يسمح بوضع علامة على القواطع لتطبيقها على عرقوب تحت حالة الحفاظ على أشكاله الندسية علامة عل القواطع لتطبيقها على عرقوب تحت حالة الحفاظ على اله الندسية ولالك الملعلية ولالك الملعلتلام العلتل الملعلية
2.18. علامات النقل ووضع علامات التعبئة والتغليف المستهلك — Условия использования ГОСТ 18088-83.
2.19. التعبئة والتغليف — согласно ГОСТ 18088-83I. «
القسم 3 (الاسم) ، الفقرة 3.L استبدال الكلمات: «واعد القبول» إلى «القبول».
يتم ر الفقرة 3.2 في الطبعة الجديدة:.. «3.2 ينبغي إجراء اختبارات دورية, بما في ذلك قواطع الاختبار لمتوسط \ u200b \ u200b فترة المقاومة, مرة واحدة كل ثلاث سنوات, لفترة مقاومة بنسبة 95% مرة واحدة سنويا على الأقل 5 مطاحن
يجب إجراء تخفيضات الاختبار على أي أحجام لطحن النطاق المشار إليه في الجدول. أربعة «.
الفقرات 4.3 ، 4.6. استبدل الكلمة: «تعيين» إلى «95 ٪».
الجدول 4. عدد «ر الطاطع D». استبدال الحجم: 12.5 لى 11.0 12.5.
يتم ر القسم 5 ي الطبعة الجديدة:
«خمسة.النقل والتخزين
النقل والتخزين — по ГОСТ 18088-83. «
الملحق 1. الجدول 1 اة حجام ر D 11.0 50,0 ؛ 60 чел. والقيم المقابلة: ____
الوكالة الفيدرالية للتنظيم الفني والمقاييس
وطني
اساسي
الروسية
Обновить
Обновить
2008
(ISO 3337: 2000)
واطع لمعالجة الأخاديد على شكل T
الظروف التقنية
ISO 3337: 2000
T- تحة القواطع السيقان الأسطوانية ومورس تفتق السيقان بعد استغلال حفرة
الطبعة الرسمية
stacdartiiform.
ГОСТ Р 53004-2008.
مقدمة
أهداف ومبادئ التوحيد الاتحاد الروسي تم تثبيته بموجب القانون الفيدرالي في 27 ديسمبر 2002 رقم 184-ФЗ «بشأن التنظيم الفني», وقواعد تطبيق المعايير الوطنية للاتحاد الروسي — ГОСТ Р 1.0-2004 «التوحيد في الاتحاد الروسي الأحكام الأساسية»
Место проведения
1 عدت مفتوحة ركة مساهمة ОАО «Вниинчанум»
2 المقدم من اللجنة الفنية المعنية بالتوحيد TC 95 «داة»
3 المعتمدة وسنها من ل الوكالة الفيدرالية لإعادة صياغة التقنية ومقاييس التواصل المؤاييس التواصل وسنا من ل الوكالة الخيدرالية لعادة ياغة التقنية ومقاييس التواصل المؤاييس التواصل المؤرخبة 11 января 2008 г.
4 يشمل ا المعيار اللوائح الأساسية المعدلة.المعيار الدولي ИСО 3337: 2000 «مطاحن مع سحاب أسطواني ومع السيقان المخروطية مورس مع حفرة خيوط للأخاديد على شكل حرف Т» (ISO 3337: 2000 Т-образный паз القواطع مع السيقان الأسطوانية والسيقان مورس تفتق بعد أن تم استغلالها حفرة », وزارة الدفاع).
معلومات عن امتثال المعايير الوطنية المرجعية مع المعايير الدولية المرجعية المستخدمة في هذا المعيار كمراجع تنظيمية مقدمة في الملحق أ.
ي الوقت نفسه ، يتم تقديم أحكام إضافية تأخذ ي الاعتبار احتياجات التقييس الوطني ي الأقسام 1.2.4. 5.6. الفقرات 3.1.5 — 3.1.8. ي القسم الفرعي 3.2 ومخصص في مائل.
تم تغيير اسم ا المعيار نسبا إلى اسم المعيار الوطني المحدد بين * لتحقيل التوافق اسم R 1.5-2004 (3.5).
5 دم لأول مرة
يتم نر معلومات حول التغييرات التي تحدث ي هذا المعيار ه مؤشر المعلوماالمنشور سنويا «نيريريا» نياريريات. ونص التغييرات والتعديلات — ي علامات المعلومات الشهرية الصادرة «المعايير الوطنية». في حالة المراجعة (استبدال) أو إلغاء هذا المعيار, سيتم نشر الإشعار المناسب في المعايير الوطنية المصدرة مؤشر المعلومات الشهرية.يتم نشر المعلومات ذات الصلة والإخطار والنصوص أيضا في نظام المعلومات العامة — على الموقع الرسمي للوكالة الاتحادية للتنظيم الفني والمقاييس على الإنترنت
© الحوادي. 2009.
لا يمكن إعادة إنتاج هذه المواصفة المعيارية بالكامل أو جزئيا, يتم نسخها وتكرارها وأسباق * بمثابة منشور رسمي دون إذن من الوكالة الفيدرالية للتنظيم والتقسيط الفني
ГОСТ Р 53004-2008.
المعيار الوطني للاتحاد الروسي
مطاحن لمعالجة الأخاديد على شكل حرف T الشروط الفنية T- فتحة القواطع.تحديد.
تاريخ الدارة — 2010 — 01 — 01
1 الاستخدام
ينطبق ا المعيار على واطع الفولاذ عالية السرعة لمعالجة الأخاديد على ل حرف T وفقا لمعيار على واطع الفولاذ عالية السرعة لمعالجة الأخاديد على ل حرف T وفقا للمعيار T وا للالمعيار
متالل8 يستخدم ا المعيار المراجع التنظيمية لى المعايير التالية:
ГОСТ Р 52965-2008 السيقان الأسطوانية للقواطع. الأبعاد الرئيسية GOST 8.051-81 نظام الدولة لضمان وحدة القياسات. الأخطاء المسموح بها عند قياس الأبعاد الخطية تصل إلى 500 шт.
ГОСТ 1050-88 Аренда сортовой ، معايرة مع سطح خاص من الصلب الهيكلي ذات الجودة العالية الكربون.الشروط الفنية العامة GOST 1412-85 الحديد الزهر مع الجرافيت Lamellar للبولينج. ГОСТ 1574-91 ГОСТ 1574-91 Тапочки Т-образные الأخاديد المصنعة. حجام ГОСТ 2789-73 ونة السطح. معلمات وخصائص ГОСТ 2848-75 مخاريط من الأدوات. التسامح رق وسائل السيطرة على GOST 4543-71 استئجار الصلب الهيكلية المدبرة. مواصفات GOST 9013-59 المعادن. ر قياس صلابة لو روكويل ГОСТ 9378-93 عينات من ونة السطح (المقارنة). الظروف التقنية العامة
ГОСТ 18088-83 داة قطع المعادن ، الماس ، ع الخشب ، المناسب والمساعد. التعبئة والتغليف والمنشحات والنقل والتخزين
ГОСТ 19265-73 بان وشرائط الصلب عالية السرعة.مواصفات ГОСТ 23726-79 داة القطع المعدنية وقطع الخشب. بول ГОСТ 25706-83 المكبر. أنواع ، المعلمات الأساسية. المتطلبات الفنية العامة
التطبيق — عند استخدام هذا المعيار, من المستحسن التحقق من إجراء المعايير المرجعية في نظام المعلومات العامة — على الموقع الرسمي للوكالة الفيدرالية للتنظيم الفني والتقسيط على الإنترنت أو LO, المعايير الوطنية * مؤشرات المعلومات المنشورة المنشورة اعتبارا من 1 يناير من العام الحالي, وفقا لمؤشرات المعلومات الشهرية المقابلة المنشورة في العام الحالي. ا تم استبدال المعيار المرجعي (تم تغييره) ، ينبغي أن تسترشد استخدام هذا المعيار عين طريق استعدار عن ريق استعدارإذا تم إلغاء المعيار المرجعي دون استبدال. الموقع الذي يتم فيه تقديم المرجع يتم تطبيقه في جزء لا يؤثر على رابط الارتباط.
الطبعة الرسمية
ГОСТ Р 53004-2008.
3 المتطلبات الفنية
3,1 والأحجام الرئيسية
3.1.1 يجب تصنيع القواطع:
1 — السنان الطبيعية:
2 — مع أسنان كبيرة.
3.1.2 Последний срок службы:
1 — مع عرقوب أسطواني ناعم ؛
2 — عروب سطواني مع عروب سطواني مع عروب سواني مع عروب:
3 — مع عرقوب أسطواني مع الخيط ؛
4 — مع عرقوب مخروطي مورس.
اتب 2 مطاحن تصنيع 4 — عرقوب مخروطي مورس.
3.1.3 يجب ن تتوافق الأبعاد الرئيسية للقواطع 1.2.3 المحدد ي الشكل 1 وفي الجدول 1.
الصوردول 1
ГОСТ Р 53004-2008.
الجدول 1
بعاد ملليمترات
اسمى ، صورى شكلى ، بالاسم فقط T- نموذج | ||||||||
3.1.4 يجب ن تتوافق الأبعاد الرئيسية للقاطع 4 المحدد ي الشكل 2 وفي الجدول 2.
المحدول 2
الأبعاد في ملليمتر
ГОСТ Р 53004-2008.
نهاية الجدول 2.
بعاد ملليمترات
اسمى ، صورى شكلى ، بالاسم فقط T- نموذج | عدد الأسنان لقواطع القاطع | ||||||||
مثال على التعييين التقليدي للنوع القاطع 1.الأداء 1. مع حجم اسمي من الأخدود من 6 ومم:
Мембраны 1 — 1 — 6 ГОСТ Р 53004-2006
أيضا. الأداء 2:
حن القاطع 1-2-6 gostper53004-2008
أيضا. الأداء 3:
حن القاطع 1-3-6 gostper53004-2008.
أيضا. الأداء 4:
Мембраны 1 — 4 — 6 ГОСТ Р 53004-2008
أيضا. اتب 2 ميلز 4. مع حجم الأخدود الاسمي من 12 ميلز:
حن القاطع 2 — 4-12GOSTR53004-2008
3.1.5 اصات السيقان 1.2.3 — وفقا لجوست ص 52965.
3.1.6 حجام مورس مورس — وفقا لجو st 25557.
3.1.7 وب المركز — وفقا لجوست 14034.
3.1.8 Версия 1 на сайте Shake Groove Co.
3,2 الخصائص
3.2.1 السرعة وفقا لجو st 19265.
3.2.2 يجب تنع القواطع الملحومة. في مكان اللحام غير مسموح به المصارف والدخل. مضاءة ومواجهة المعادن ، وشقوق الدائري وخراوضات.
واطع العروض 1. 2.3 للأخادير بحجم اسمي يصل إلى 12 ملم شاملة ، يسمح له بجعله ممكنا.
3.2.3 يب ن تكون ساقيات القواطع الملحومة مصنوعة درجات الصلب 40x وفقا لجو st 4543 و من الولاذ3 ت 45. 45.
3.2.4 يجب ن يكون صلابة القاطع الجزء العامل 63 ..66 HRC.
إن صلابة قطع جزء العمل من الصلب عالي السرعة مع محتوى الفاناديوم لا يقل عن 3% والكوبالت يجب أن يكون ما لا يقل عن 5% على الأقل أعلى في 1 إلى 2 وحدات HRC.
يجب ن يكون صلابة عرقوب أسطواني من المطاحن الصلبة (غير المشروبات) 37..57 HRC.
ن لابة عرقوب سطوانية للقواطع الملحومة على عة أرض لا تقل за 2 على الأقل من ناية عروب سطوانية للقواطع الملحومة على عة رض لا تقل عن 2 على الأقل من ناية عرقوب
3.2.5 على سطح العمل ، يجب لا يكون القاطع بقة متضغة وأماكن ات صلابة منخفضة.
ГОСТ Р 53004-2008.
3.2.6 على سطح القاطع يجب ألا يكون هناك تشققات, آثار التآكل: على أسطح الطحن — مسودة, أماكن متنوعة: على حواف القطع — الزبين, المناسب: على عرقوب ومراكز — الأزيز.
3.2.7 يب تكون معايير الأسطح المخيطية للقواطع وفقا ل GOST 2789 MKM وليس فقر من:
RZ 3.2- للأسطح الأمامية والخلفية للأسنان:
RA 0.63 — Дата публикации:
RZ 10 — لسطح ور سنان الأسنان والرقبة وأخاديد الصاح:
RZ 20 — للحصول على أسطح أخرى.
3.2.6 على السطح الخلفي للأسنان ، يسمح بعرض ريط أسطواني على ول حواف القطع.
3.2.9 يجب يكون الحد من الانحرافات القواطع. مم. لا ر:
± JT16 / 2 — القاطع L ؛
الدقة الحادة ي AT8 وفقا ل GOST 2848 — لمخروط مورس.
3.2.10 ن بول الضرب الشعاعي على حواف القطع الرئيسية لقطع الأسنان بالنسبة إلى محور عرقوب يجبن يكور.مم. لا ر:
0,02 — عل انين من الأسنان المجاورة — للقاطع بقطر ما يصل إلى 40 млн SCUCK:
0,04 — على احونة املة «» »» 40 »»:
0,03 — على انين من الأسنان المجاورة — للقاطع بقطر القديس 40 Количество:
0,05 — على القاطع بأكمله P »P» 40 ص.
3.2.11 يجب يكون التسامح مع التزلج من الجزء العامل من القاطع النسبي إلم محور عرقوب. مم. لا ر:
0,04 — للقواطع التي يبلغ رها ما يصل إلى 40 мин
0,05 цена. 40 чел.
3.2.12 منتصف 7 وأسس في فترات قاطع المقاومة أثناء معالجة المعالجة الحديد الزهر الجزء من ГОСТ من ГОСТ 1412 والصلب الصف 45 وفقا ل ГОСТ 1050 بموجب شروط الاختبارات الواردة في القسم 5. يجب أن تكون: Т-60 دقيقة. T G — 25 месяцев.
3.2.13. المحدد في الجدول 3.
الجدول 3.
ي ملليمتر
القاطع القطر D. | ارتداء حيح | |
عند معالجة الحديد الزهر | عند معالجة السهوب | |
ГОСТ Р 53004-2008.
3.2.14 بمناسبة
ي عبارة العنق يجب تطبيقها بوضوح:
العلامة التجارية للشركة المصنعة ؛
حجم الاسمي канавка ؛
العلامة التجارية الصلب العمل جزء.
يسمح بتطبيق وضع العلامات على عرقوب تحت حالة الحفاظ على اله الهندسية ، وكذلك المصنعلة عل عرول.
3.2.15 علامات النقل ووضع علامات حاويات المستهلكين — Условия использования ГОСТ 18088.
3.2.16 التعبئة والتغليف — وفقا لجو st 18088.
4 واعد بول
4.1 واطع القبول — وفقا لجو st 23726.
4.2. اختبارات تنفذ ما لا يقل عن خمسة مطاحن من ي sizzy.
4.3 يسمح باختبار المستهلك.
5 ر التحكم والاختبار
5.1 Последние данные по запросу LP-1-4 LPOST 25706.
5,2 يتم مراقبة لابة القاطع وفقا لجوست 9013.
5.3.
القيم المحددة ي ГОСТ 8.051 — عند قياس الأبعاد الخطية:
35 التسامح لزاوية ابلة للتحقق من «RALE RALE»
25 человек.
5,4 ت.
5.5 يجب راء تخفيضات الاختبار على آلات طحن الآلات المجموع والخاصة. الدقة المناسبة والصلابة المنشأة لهم.
5,6 نواع نواع 1. 2. عمليات الإعدام 1 2.3 يجب أن تكون من ذوي الخبرة على القوالب من الحديد الزهر الرمادي من الصف SCh28 وفقا ل ГОСТ 1412 صلابة 180 … 220 HV: أنواع القواطع 2 — على الثلانات من العلامة التجارية الصلب 45 وفقا ل ГОСТ 1050 Твердость 197 … 207 Н.В. . في الفراغات ، ن الأخاديد المستطيلة هي إعادة التقدير. متساوية ي عرض ر الرقبة (D T * 2) MM مع حفنة على ول الجزء السفلي من الأخدود 1–2 чел.
5,7 يتم استخدام حل 5% (الوزن) من الانبعاثات في الماء بمعدل تدفق من 6 إلى 8 لتر / دقيقة كمويد تشحيم وتبريد أثناء تشغيل الصلب: عندما يمكن تبريد الحديد الزهر بنفاوعة من عمليات إزالة الهواء الرقائق من منطقة القطع.
5,8 يجب راء اختبارات القواطع للأداء ، وينبغي أن تنفذ فترات المقاومة المتوسطة والمثبتة اتبارات الواطع للأداء وينبغي ن تنفذ فترات المقاومة المتوسطة والمثبتة علاتبارات المثبتة علاارات المبتة علاارات البتة علا 9 الوللى
الجدول 4.
ГОСТ Р 53004-2008.
نهاية tvbpitsa 4.
5.9 ول الطحن الكلي عند اختبار الأداء يجب ن يكون 500 млн. _
5.10. يجب. T G — 28 دقيقة.
5.11.
6 звезд
6.1 النقل والتخزين — وفقا لجو st 18088.
ГОСТ Р 53004-2008.
الملحق أ (إلزامي)
معلومات عن امتثال مرجع المعايير الوطنية المرجعية
المعايير الدولية
الجدول A.1.
تعلم التعيين المعياري الوطني | التعيين والاسم الإحالة لى المعايير الدولية والتعيين الشرطي لدرجة الامتثال للميايير الوايية |
ГОСТ Р 52965-2008. | ISO 3336-1: 1996 «السيقان الأسطوانية للقواطع. رف 1. بعاد السيقان الأسطوانية السلسة» (مو) ISO 3336-2: 2007 «السيقان الأسطوانية للقواطع. رف 2. بعاد السيقان الأسطوانية مع Lyscamn * (وزارة الدفاع) ISO 3336-3: 1996 «السيقان الأسطوانية للقواطع. الشرف 3. حجام السيقان مع نهاية خيوط» (مو) |
ГОСТ 1574-91. | ISO 299: 1987 «داول من دوات الآلات. على ل حرف T والبراغي المقابلة» (NEO) |
ГОСТ 9378-93. | ISO 2632-1: 1985 «عينات لمقارنة الخشونة. الجزء 1. Sampleshatopny. ISO 2632-2: 1985 «عينات لمقارنة الخشونة. الجزء 2. |
ГОСТ Р 53004-2008.
УДК 621.914.22: 006.354 الثور 25.100.20 G23 OKP 39 1828
الكلمات المفتاحية: القواطع. الأخاديد على شكل حرف T ، عرقوب أسطوانية ناعمة عرقوب مع ليكي ، اق الخيط ، مخروط مورس
محرر R.Г. Гудеро * Редактор Hell Edgine В.И. Прусакова корректор уб. تخطيط الكمبيوتر الأبيض السادس grishchenlo.
تسليمها وتعيين 11.12.2006. الموقع والطباعة 16.01.2009. التنسيق $ 0x84 «/ |
ФГУП «Стэндинформ». 123995 موسكو. الرمان لير .. 4. نيو استرليني Gostinfo.ru س ل OO ФГУП «Стэндинформ» عل PEVM
» «طابعة موسكو». 105062 موسكو. لينالين لين ، ب
الوكالة الفيدرالية
على التنظيم الفني والمعلومات
مقدمة
يتم إنشاء أهداف ومبادئ التقييس في الاتحاد الروسي من قبل القانون الفيدرالي للفترة 27 ديسمبر 2002 رقم 184-ФЗ «بشأن التنظيم الفني», وقواعد تطبيق المعايير الوطنية للاتحاد الروسي — ГОСТ Р 1.0- 2004 «توحيد في الاتحاد الروسي. الأحكام الأساسية»
Место нахождения
1 عدها شركة المساهمة المفتوحة JSC VNIIIINCH
2 المقدم من اللجنة الفنية المعنية بالتوحيد TC 95 «داة»
3 المعتمدة وتقديمها بنظام الوكالة الفيدرالية للتنظيم الفني ومقاييس 11 января 2008 г. 297
4 يشمل هذا المعيار لوائح أساسية معدلة من المعايير الدولية ИСО 3337: 2000 «مع سحاب أسطواني ومع السيقان المخروطية مورس مع حفرة خيوط للأخاديد على شكل حرف Т» (ISO 3337: 2000 Т-образный паз القواطع مع عرقوب أسطوانية ومورس تفتق السيقان بعد أن تم استغلالها حفرة »وزارة الدفاع).
معلومات عن امتثال المعايير الوطنية المرجعية مع المعايير الدولية المرجعية المستخدمة في هذا المعيار مثل المراجع التنظيمية مقدمة في المرفق.
.
يتم تغيير اسم ا المعيار نسبة إلى اسم المعاير الدولية المحددة لتحقيق التوافق المعيار نسبة ل اسم المعاير الدولية المحددة لتحقيق التوافق المعيار نسبة الدولية المحددة لتحقيق التوافق по ГОСТ Р 1.5-2004 (3.5).
5 دم لأول مرة
يتم نشر معلومات حول التغييرات التي تحدث في هذا المعيار في المؤشر المعلوماتي «المعايير الوطنية» سنويا ونص التغييرات والتعديلات — مؤشرات المعلومات الشهرية المنشورة «المعايير الوطنية».في حالة المراجعة (استبدال) أو إلغاء هذا المعيار, سيتم نشر الإشعار المناسب في المعايير الوطنية المصدرة مؤشر المعلومات الشهرية. كما يتم نشر المعلومات ذات الصلة والإشعار والنصوص أيضا في نظام المعلومات العامة — على الموقع الرسمي للوكالة الاتحادية للتنظيم الفني والمقاييس على الإنترنت
ГОСТ Р 53004-2008.
المعيار الوطني للاتحاد الروسي
تاريخ الإدارة — 2010-01-01
ينطبق ا المعيار على واطع الفولاذ عالية السرعة لمعالجة الأخاديد على شكل حرف T وفقا ل ГОСТ 1574.
يستخدم المعيار المراجع التنظيمية بالمعايير التالية:
اتب 2 مطاحن تصنيع 4 — عرقوب مخروطي مورس.
3.1.3 يجب ن تتطابق الأبعاد الرئيسية للقواطع 1 ، 2 ، 3 على المحدد ي الشكل وفي الجدول.
الصورة 1
الجدول 1
الأبعاد في ملليمتر
د. | د. 1 , | د. 2 | л. | л. | f | q | عدد | |
11,0 | 53,5 | |||||||
12,5 | 57,0 | |||||||
16,0 | 62,0 | |||||||
18,0 | 70,0 | |||||||
21,0 | 74,0 | |||||||
25,0 | 11,0 | 82,0 | ||||||
32,0 | 14,0 | 90,0 | ||||||
40,0 | 18,0 | 108,0 | ||||||
50,0 | 22,0 | 124,0 | ||||||
60,0 | 28,0 | 139,0 |
3.1.4 يجب ن تتطابق الأبعاد الرئيسية لقاطع القطع 4 مع المحدد في الشكل وفي الجدول.
الشكل 2.
الجدول 2
الأبعاد في ملليمتر
دود على ل حرف | د. ح 12. | د. 1 لا ر | л. | л. | f ، لا ر | q ، لا ر | до до | عدد الأسنان ل نواع الحجم | |
12,5 | |||||||||
16,0 | |||||||||
18,0 | |||||||||
21,0 | |||||||||
25,0 | |||||||||
32,0 | |||||||||
40,0 | |||||||||
50,0 | |||||||||
60,0 | |||||||||
72,0 | |||||||||
85,0 | |||||||||
95,0 |
عل التعيين الشرطي للقاطع النوع 1 الإعدام 1 مع حجم الأخدود الاسمي من 6
:Мембраны 1 — 1 — 6 ГОСТ Р 53004-2008
الإعدام 2:
Мембраны 1-2-6 ГОСТ Р 53004-2008
الإعدام 3:
Мембраны 1 — 3 — 6 ГОСТ Р 53004-2008
الإعدام 4:
Мембраны 1 — 4 — 6 ГОСТ Р 53004-2008
نفس, قواطع من النوع 2, 4 الإعدام, بحجم رمزي من الأخدود من 12 ملم:
محنة 2 — 4 — 12 ГОСТ Р 53004-2008
3.1.6 بعاد مورس المخاريط — وفقا لجو st 25557.
3.1.7 وب المركز — وفقا لجوست 14034.
3.2.2 يجب نع القواطع ملحومة. بدلا من اللحام غير مسموح به المصارف والدخل والحرقة والمعادن المواجهة والشقوق الحلقية وخراوضات.
يسمح مصانع العروض 1 ، 2 ، 3 للأخادير بحجم اسمي يصل إلى 12 ملم املة من قبل قطعة واحدة.
3.2.3 يب ن تكون عرقوب الملحومة الواطع الملحومة منوعة من GOST4543 الولاذ 40HPU و الولاذ ال 45 GOST.
3.2.4 يجب ن يكون صلابة الجزء العام القاطع 63 .. .66 HRC.
إن صلابة قطع جزء العمل من الصلب عالي السرعة مع محتوى الفاناديوم لا يقل عن 3% والكوبالت يجب أن يكون ما لا يقل عن 5% على الأقل أعلى في 1 إلى 2 وحدات HRC.
يجب ن يكون صلابة عرقوب الأسطوانية من المطاحن الصلبة (ير المنتجعات الصلبة) 37. .57HRC.
يجب ن تكون لابة عرقوب الأسطوانية للقواطع الملحومة على عة رض واحدة على الأقلليون لابة عرقوب السطوانية للقواطع الملحومة على عة رض واحدة عل الأقلليلية من ابة اللللية من ريوة من ريوة.. .52 HRC.
3.2.5 على سطح العمل ، يجب ألا يكون القاطع طبقة مرفجة وأماكن مع صلابة مخفضة.
3.2.6 لا ينبغي أن يكون ناك شقوق على سطح القاطع ، ار التآكل ؛ على الأسطح الطحن — تشيرنوفين ، أماكن مصبوغة ؛ على حواف القطع — ابين ، الإيدز ؛ على عرقوب وثقائق المركز — الأزيز.
الجدول 3.
مي ملليمتر
5,5 يجب راء تخفيضات الاختبار في آلات حن للأغراض العامة والخاصة التي تووافق مع اة والتوافق الدقة والصلانة الملللة واللات حن للأغراض العامة. 5.6 أنواع الأنواع 1, 2, الإصدارات 1, 2, 3 يجب أن تكون من ذوي الخبرة على القوالب من الحديد الزهر الرمادي من МОХ 18 وفقا ل ГОСТ 1412 Твердость 180. .. 220 HV; مطاحن نوع 2 العدام 4 — عل راغات العلامة التجارية الصلب 45 وا ل GOST 1050 لابة 197 … 207 NV. ي الفراغات ، ن الأخاديد المستطيلة أولية ي عرض ر الرقبة ( د. 1 + 2) مم بدل لأسفلة ولية عر ر الرقبة ( د. 1 + 2) مم بدل لأسفل 5,7 كوسائل تشحيم وتبريد, يتم استخدام 5% (حسب الوزن) بالنسبة للصلب الانبعاد في الماء مع الاستهلاك 6 — 8 لتر / دقيقة عندما يجب تبريد عمل الحديد الزهر النفاث من الهواء بإزالة الرقائق من منطقة القطع. 5,8 يجب راء اختبارات القاطع على سعة العمل وينبغي تنفيذ فترات المقاومة ترات الماومة المتوسطة الماومة ترات المقاومة تترات المقاومة ترات الماومة ترات الماومة ترات الماومة المتوسطة والمثية دلوليلولة اللولالبلة الوللولالولة اللولالالبلة اللوليلول الوللول اللم الجداول 4.
|
2005 твердосплавным оболочкового типа ФРЕЗЫ ДЛЯ
ГОСТ 23726: 1979 драм 3 1989 г. | РЕЗКА И ДЕРЕВО — ПРИЕМКА |
ГОСТ 8051: 1983 5 драм 1992 г. | БЫТОВЫЕ СТИРАЛЬНЫЕ МАШИНЫ — ТЕХНИЧЕСКИЕ ХАРАКТЕРИСТИКИ |
ГОСТ 12.1.012: 2009 | СИСТЕМА СТАНДАРТОВ ТЕХНИКИ БЕЗОПАСНОСТИ — ВИБРАЦИОННАЯ БЕЗОПАСНОСТЬ — ОБЩИЕ ТРЕБОВАНИЯ |
ГОСТ 3882: 1974 ОШИБКА 2002 | СПЛАВЫ ТВЕРДЫЕ СПЛАВНЫЕ — ТИПЫ |
ГОСТ 4543: 2016. | ТЕХНИЧЕСКИЕ ХАРАКТЕРИСТИКИ ИЗДЕЛИЙ ИЗ СПЛАВНЫХ СТАЛЬНЫХ КОНСТРУКЦИЙ |
ГОСТ 1050: 2013 | МЕТАЛЛИЧЕСКИЕ ИЗДЕЛИЯ ИЗ БЕЗ ЛЕГКИХ КОНСТРУКТИВНЫХ СТАЛЕЙ И СПЕЦИАЛЬНЫХ СТАЛЕЙ — ОБЩИЕ ХАРАКТЕРИСТИКИ |
ГОСТ 9012: 1959 ОШИБКА 2003 | МЕТАЛЛЫ — МЕТОД ИЗМЕРЕНИЯ ТВЕРДОСТИ БРИНЕЛЛЯ |
ГОСТ 23677: 1979 AMD 2 1988 г. | МАШИНЫ ДЛЯ ИСПЫТАНИЯ ЖЕСТКОСТИ МЕТАЛЛОВ — ОБЩИЕ ТЕХНИЧЕСКИЕ ТРЕБОВАНИЯ |
ГОСТ 25706: 1983 AMD 1 1989. | УВЕЛИЧИТЕЛИ — ТИПЫ, ОСНОВНЫЕ ПАРАМЕТРЫ — ОБЩИЕ ТЕХНИЧЕСКИЕ ТРЕБОВАНИЯ |
ГОСТ 577: 1968 5 драм 1988 г. | ЧАСОВЫЕ ИНДИКАТОРЫ НАБОРНОГО ДИАПАЗОНА, ВЫПУЩЕННЫЕ В РАЗДЕЛАХ 0,01 ММ — ТЕХНИЧЕСКИЕ ХАРАКТЕРИСТИКИ |
ГОСТ 18088: 1983 AMD 1 1990 | ИНСТРУМЕНТ ДЛЯ РЕЗКИ МЕТАЛЛОВ, АЛМАЗНЫХ, ДЕРЕВЯННЫХ И МОНТАЖНЫХ СБОРОВ — УПАКОВКА, МАРКИРОВКА, ТРАНСПОРТНЫЙ СМЕСИТЕЛЬ И ДОПОЛНИТЕЛЬНОЕ ОБОРУДОВАНИЕ |
ГОСТ Р 52401: 2005 | ДЕРЕВЯННЫЙ ИНСТРУМЕНТ ДЛЯ РУЧНЫХ СТАНКОВ — ТРЕБОВАНИЯ БЕЗОПАСНОСТИ |
ГОСТ 2789: 1973 драм 1 1981 г. | ШЕРОХОВАТОСТЬ ПОВЕРХНОСТИ — ПАРАМЕТРЫ И ХАРАКТЕРИСТИКИ |
ГОСТ 9378: 1993. | ОБРАЗЦЫ ДЛЯ СРАВНЕНИЯ ШЕРОХОВАТОСТИ — ОБЩИЕ ХАРАКТЕРИСТИКИ |
ГОСТ 69: 1975 AMD 2 1989 г. | ДЕРЕВООБРАБАТЫВАЮЩЕЕ ОБОРУДОВАНИЕ — ФОРМАТОР С НИЖНИМ ШПИНДЕЛЕМ — СТАНДАРТЫ ТОЧНОСТИ И ЖЕСТКОСТИ |
Баллад онлайн
Выходные данные Имена: Наджент, Дж.Ф. и Ко.
Расположение выходных данных: Дублин?
Дата между 1850 и 1899 гг.
Идентификатор серии: 26
1-я баллада
Название: Песня о Джеймсе МакДональде, казненном в Лонгфорде за убийство Анны О’Брайен
Первая линия: О! Молодые люди и старые, теперь я смел, молитесь, дайте мне ухо
Темы: Убийство
2-я баллада — номер Roud: 148
Название: Банки сладких Данди
Первая линия: Это дочь фермера, такая красивая, как мне сказали
3-я баллада — Номер рада: 12825
Название: Барни Бантлинг
Первая линия: Однажды ночью пришел ураган
Темы: Моряки
4-я баллада — Номер рада: 820
Название: Бернс и его Хайленд Мэри
Первая линия: В зеленой Каледонии никогда не было двух влюбленных
5-я баллада — номер строки: 3329
Название: Связать и идти
Первая линия: Прекрасные берега Клайда, где цветет вереск
Шестая баллада — Номер Roud: 2419
Название: Деяния Наполеона
Первая линия: Вы, герои дня, веселые, смелые и веселые
Тем: Наполеон I, император Франции, 1769-1821 гг.
7-я баллада — номер Roud: V30579
Название: Новая песня о Майкле Давитте
Первая линия: Затем вверх с флагом, поднятым Давиттом, наша голова
Мелодия: Garryowen
Тем: Давит, Майкл, 1846-1906 гг.
8-я баллада — номер строки: V2856
Заголовок: Зеркало пьяницы
Первая линия: Что пьяница сделает с элем?
Примечания: Предшественник: Катехизис пьяницы
Темы: Пьянство
9-я баллада — номер Roud: V1153
Название: Прощание с глупостью
Первая линия: Прощай, домовладельцы, прощай, Джерри
Темы: Пьянство
10-я баллада — номер строки: V3706
Название: Луна на водах
Первая линия: Когда луна в воде
11-я баллада — номер строки: V8189
Название: Она умерла за любовь, а он за славу
Первая линия: Молодой Генри был таким же храбрым, как юноша
Авторов: Дибдин, Томас, 1771-1841 гг.