Асинхронный двигатель с короткозамкнутым ротором: конструкция, принцип работы
Учитывая то, что электроснабжение традиционно осуществляется путём доставки потребителям переменного тока, понятно стремление к созданию электромашин, работающих на поставляемой электроэнергии. В частности, переменный ток активно используется в асинхронных электродвигателях, нашедших широкое применение во многих областях деятельности человека. Особого внимания заслуживает асинхронный двигатель с короткозамкнутым ротором, который в силу ряда причин занял прочные позиции в применении.
Секрет такой популярности состоит, прежде всего, в простоте конструкции и дешевизне его изготовления. У электромоторов на короткозамкнутых роторах есть и другие преимущества, о которых вы узнаете из данной статьи. А для начала рассмотрим конструктивные особенности этого типа электрических двигателей.
Конструкция
В каждом электромоторе есть две важных рабочих детали: ротор и статор. Они заключены в защитный кожух. Для охлаждения проводников обмотки на валу ротора установлен вентилятор. Это общий принцип строения всех типов электродвигателей.
Конструкции статоров рассматриваемых электродвигателей ничем не отличаются от строения этих деталей в других типах электромоторов, работающих в сетях переменного тока. Сердечники статора, предназначенного для работы при трехфазном напряжении, располагаются по кругу под углом 120º. На них устанавливаются обмотки из изолированной медной проволоки определённого сечения, которые соединяются треугольником или звездой. Конструкция магнитопровода статора жёстко крепится на стенках цилиндрического корпуса.
Строение электродвигателя понятно из рисунка 1. Обратите внимание на конструкцию обмоток без сердечника в короткозамкнутом роторе.
Рис. 1. Строение асинхронного двигателя с КЗ РоторомНемного по-другому устроен ротор. Конструкция его обмотки очень похожа на беличью клетку. Она состоит из алюминиевых стержней, концы которых замыкают короткозамыкающие кольца.
Конструктивно стержни расположены поверх сердечников ротора, которые состоят из трансформаторной стали. При изготовлении роторов сердечники монтируют на валу, а проводники обмотки впрессовывают (заливают) в пазы магнитопровода. При этом нет необходимости в изоляции пазов сердечника. На рисунке 2 показано фото ротора с КЗ обмотками.
Рис. 2. Ротор асинхронного двигателя с КЗ обмоткамиПластины магнитопроводов таких роторов не требуют лаковой изоляции поверхностей. Они очень просты в изготовлении, что удешевляет себестоимость асинхронных электродвигателей, доля которых составляет до 90% от общего числа электромоторов.
Ротор асинхронно вращается внутри статора. Между этими деталями устанавливаются минимальные расстояния в виде воздушных зазоров. Оптимальный зазор находится в пределах от 0,5 мм до 2 мм.
В зависимости от количества используемых фаз асинхронные электродвигатели можно разделить на три типа:
- однофазные;
- двухфазные;
- трёхфазные.
Они отличаются количеством и расположением обмоток статора. Модели с трехфазными обмотками отличаются высокой стабильностью работы при номинальной нагрузке. У них лучшие пусковые характеристики. Зачастую такие электродвигатели используют простую схему пуска.
Двухфазные двигатели имеют две перпендикулярно расположенных обмотки статора, на каждую из которых поступает переменный ток. Их часто используют в однофазных сетях – одну обмотку подключают напрямую к фазе, а для питания второй применяют фазосдвигающий конденсатор. Без этой детали вращение вала асинхронного электродвигателя самостоятельно не начнётся. В связи с тем, что конденсатор является неотъемлемой частью двухфазного электромотора, такие двигатели ещё называют конденсаторными.
В конструкции однофазного электродвигателя используют только одну рабочую обмотку. Для запуска вращения ротора применяют пусковую катушку индуктивности, которую через конденсатор кратковременно подключают к сети, либо замыкают накоротко. Эти маломощные моторчики используются в качестве электрических приводов некоторых бытовых приборов.
Принцип работы
Функционирование асинхронного двигателя осуществляется на основе свойства трёхфазного тока, способного создавать в обмотках статора вращающее магнитное поле. В рассматриваемых электродвигателях синхронная частота вращения электромагнитного поля связана прямо пропорциональной зависимостью с собственной частотой переменного тока.
Существует обратно пропорциональная зависимость частоты вращения от количества пар полюсов в обмотках статора. Учитывая то, что сдвиг фаз составляет 60º, зависимость частоты вращения ротора (в об/мин.) можно выразить формулой:
n1 = (f1*60) / p, где n1 – синхронная частота, f1 – частота переменного тока, а p – количество пар полюсов.
В результате действия магнитной индукции на сердечник ротора, в нём возникнет ЭДС, которая, в свою очередь, вызывает появление электрического тока в замкнутом проводнике. Возникнет сила Ампера, под действием которой замкнутый контур начнёт вращение вдогонку за магнитным полем. В номинальном режиме работы частота вращения ротора немного отстаёт от скорости вращения создаваемого в статоре магнитного поля. При совпадении частот происходит прекращение магнитного потока, ток исчезает в обмотках ротора, вследствие чего прекращается действие силы. Как только скорость вращения вала отстанет, переменными токами магнитных полей, возобновляется действие амперовой силы.
Разницу частот вращения магнитных полей называют частотой скольжения: ns=n1–n2, а относительную величину s, характеризующую отставание, называют скольжением.
s = 100% * ( ns / n1) = 100% * (n1 — n2) / n1 , где ns – частота скольжения; n1, n2 – частоты вращений статорных и роторных магнитных полей соответственно.
С целью уменьшения гармоник ЭДС и сглаживания пульсаций момента силы, стержни короткозамкнутых витков немного скашивают. Взгляните ещё раз на рис. 2 и обратите внимание на расположение стержней, выполняющих роль обмоток ротора, относительно оси вращения.
Скольжение зависит от того, какую механическую нагрузку приложено к валу двигателя. В асинхронных электромоторах изменение параметров скольжения происходит в диапазоне от 0 до 1. Причём в режиме холостого хода набравший обороты ротор почти не испытывает активного сопротивления. S приближается к нулю.
Увеличение нагрузки способствует увеличению скольжения, которое может достигнуть единицы, в момент остановки двигателя из-за перегрузки. Такое состояние равносильно режиму короткого замыкания и может вывести устройство из строя.
Относительная величина отставания соответствующая номинальной нагрузке электрической машины называется номинальным скольжением. Для маломощных электромоторов и двигателей средней мощности этот показатель изменяется в небольших пределах – от 8% до 2%. При неподвижности ротора электродвигателя скольжение стремится к 0, а при работе на холостом ходу оно приближается к 100%.
Во время запуска электромотора его обмотки испытывают нагрузку, что приводит к резкому увеличению пусковых токов. При достижении номинальных мощностей электрические двигатели с короткозамкнутыми витками самостоятельно восстанавливают номинальную частоту ротора.
Обратите внимание на кривую крутящего момента скольжения, изображённую на рис. 3.
Рис. 3. Кривая крутящего момента скольженияПри увеличении крутящего момента коэффициент s изменяется от 1 до 0 (см. отрезок «моторная область»). Возрастает также скорость вращения вала. Если скорость вращения вала превысит номинальную частоту, то крутящий момент станет отрицательным, а двигатель перейдёт в режим генерации (отрезок «генерирующая область»). В таком режиме ротор будет испытывать магнитное сопротивление, что приведёт к торможению мотора. Колебательный процесс будет повторяться, пока не стабилизируется крутящий момент, а скольжение не приблизится к номинальному значению.
Преимущества и недостатки
Повсеместное использование асинхронных двигателей с короткозамкнутыми роторами обусловлено их неоспоримыми преимуществами:
- стабильностью работы на оптимальных нагрузках;
- высокой надёжностью в эксплуатации;
- низкие эксплуатационные затраты;
- долговечностью функционирования без обслуживания;
- сравнительно высокими показателями КПД;
- невысокой стоимостью, по сравнению с моделями на основе фазных роторов и с другими типами электромоторов.
Из недостатков можно отметить:
- высокие пусковые токи;
- чувствительность к перепадам напряжений;
- низкие коэффициенты скольжений;
- необходимость в применении устройств, таких как преобразователи частоты, пусковые реостаты и др., для улучшения характеристик электромотора;
- ЭД с короткозамкнутым ротором нуждаются в дополнительных коммутационных управляющих устройствах, в случаях, когда возникает необходимость регулировать скорость.
Электродвигатели данного типа имеют приличную механическую характеристику. Несмотря на недостатки, они лидируют по показателям их применения.
Основные технические характеристики
В зависимости от класса электродвигателя, его технические характеристики меняются. В рамках данной статьи не ставится задача приведения параметров всех существующих классов двигателей. Мы остановимся на описании основных технических характеристик для электромоторов классов 56 А2 – 80 В2.
В этом небольшом промежутке на линейке моделей эелектромоторов с короткозамкнутыми роторами можно отметить следующее:
Мощность составляет от 0,18 кВт (класс 56 А2) до 2,2 кВт (класс 80 В2).
Ток при максимальном напряжении – от 0,55 А до 5А.
КПД от 66% до 83%.
Частота вращения вала для всех моделей из указанного промежутка составляет 3000 об./мин.
Технические характеристики конкретного двигателя указаны в его паспорте.
Подключение
Статорные обмотки трёхфазного АДКР можно подключать по схеме «треугольник» либо «звезда». При этом для звёздочки требуется напряжение выше, чем для треугольника.
Обратите внимание на то, что электродвигатель, подключенный разными способами к одной и той же сети, потребляет разную мощность. Поэтому нельзя подключать электромотор, рассчитанный на схему «звезда» по принципу треугольника. Но с целью уменьшения пусковых токов можно коммутировать на время пуска контакты звезды в треугольник, но тогда уменьшится и пусковой момент.
Схемы включения понятны из рисунка 4.
Рис. 4. Схемы подключенияДля подключения трёхфазного электрического двигателя к однофазному току применяют фазосдвигающие элементы: конденсаторы, резисторы. Примеры таких подключений смотрите на рисунке 5. Можно использовать как звезду, так и треугольник.
Рис. 5. Примеры схем подключений в однофазную сетьС целью управления работой двигателя в электрическую цепь статора подключаются дополнительные устройства.
Асинхронный двигатель — принцип работы и устройство
Асинхронный двигатель
8 марта 1889 года величайший русский учёный и инженер Михаил Осипович Доливо-Добровольский изобрёл трёхфазный асинхронный двигатель с короткозамкнутым ротором.
Современные трёхфазные асинхронные двигатели являются преобразователями электрической энергии в механическую. Благодаря своей простоте, низкой стоимости и высокой надёжности асинхронные двигатели получили широкое применение. Они присутствуют повсюду, это самый распространённый тип двигателей, их выпускается 90% от общего числа двигателей в мире. Асинхронный электродвигатель поистине совершил технический переворот во всей мировой промышленности.
Огромная популярность асинхронных двигателей связана с простотой их эксплуатации, дешивизной и надежностью.
Асинхронный двигатель — это асинхронная машина, предназначенная для преобразования электрической энергии переменного тока в механическую энергию. Само слово “асинхронный” означает не одновременный. При этом имеется ввиду, что у асинхронных двигателей частота вращения магнитного поля статора всегда больше частоты вращения ротора. Работают асинхронные двигатели, как понятно из определения, от сети переменного тока.
Устройство
На рисунке: 1 — вал, 2,6 — подшипники, 3,8 — подшипниковые щиты, 4 — лапы, 5 — кожух вентилятора, 7 — крыльчатка вентилятора, 9 — короткозамкнутый ротор, 10 — статор, 11 — коробка выводов.
Основными частями асинхронного двигателя являются статор (10) и ротор (9).
Статор имеет цилиндрическую форму, и собирается из листов стали. В пазах сердечника статора уложены обмотки статора, которые выполнены из обмоточного провода. Оси обмоток сдвинуты в пространстве относительно друг друга на угол 120°. В зависимости от подаваемого напряжения концы обмоток соединяются треугольником или звездой.
Роторы асинхронного двигателя бывают двух видов: короткозамкнутый и фазный ротор.
Короткозамкнутый ротор представляет собой сердечник, набранный из листов стали. В пазы этого сердечника заливается расплавленный алюминий, в результате чего образуются стержни, которые замыкаются накоротко торцевыми кольцами. Эта конструкция называется «
Фазный ротор имеет трёхфазную обмотку, которая практически не отличается от обмотки статора. В большинстве случаев концы обмоток фазного ротора соединяются в звезду, а свободные концы подводятся к контактным кольцам. С помощью щёток, которые подключены к кольцам, в цепь обмотки ротора можно вводить добавочный резистор. Это нужно для того, чтобы можно было изменять активное сопротивление в цепи ротора, потому что это способствует уменьшению больших пусковых токов. Подробнее о фазном роторе можно прочитать в статье — асинхронный двигатель с фазным ротором.
Принцип работы
При подаче к обмотке статора напряжения, в каждой фазе создаётся магнитный поток, который изменяется с частотой подаваемого напряжения.
Результирующий магнитный поток статора вращается и тем самым создаёт в проводниках ротора ЭДС. Так как обмотка ротора, имеет замкнутую электрическую цепь, в ней возникает ток, который в свою очередь взаимодействуя с магнитным потоком статора, создаёт пусковой момент двигателя, стремящийся повернуть ротор в направлении вращения магнитного поля статора. Когда он достигает значения, тормозного момента ротора, а затем превышает его, ротор начинает вращаться. При этом возникает так называемое скольжение.
Скольжение s — это величина, которая показывает, насколько синхронная частота n1 магнитного поля статора больше, чем частота вращения ротора n2, в процентном соотношении.
Скольжение это крайне важная величина. В начальный момент времени она равна единице, но по мере возрастания частоты вращения n2 ротора относительная разность частот n1-n2 становится меньше, вследствие чего уменьшаются ЭДС и ток в проводниках ротора, что влечёт за собой уменьшение вращающего момента. В режиме холостого хода, когда двигатель работает без нагрузки на валу, скольжение минимально, но с увеличением статического момента, оно возрастает до величины sкр — критического скольжения. Если двигатель превысит это значение, то может произойти так называемое опрокидывание двигателя, и привести в последствии к его нестабильной работе. Значения скольжения лежит в диапазоне от 0 до 1, для асинхронных двигателей общего назначения оно составляет в номинальном режиме — 1 — 8 %.
Как только наступит равновесие между электромагнитным моментом, вызывающим вращение ротора и тормозным моментом создаваемым нагрузкой на валу двигателя процессы изменения величин прекратятся.
Выходит, что принцип работы асинхронного двигателя заключается во взаимодействии вращающегося магнитного поля статора и токов, которые наводятся этим магнитным полем в роторе. Причём вращающий момент может возникнуть только в том случае, если существует разность частот вращения магнитных полей.
Рекомендуем к прочтению — однофазный асинхронный двигатель.
Как изготавливаются тормозные диски
Задумывались ли вы, как изготавливаются тормозные диски? Если да, то сегодня ваш счастливый день.
Процесс изготовления тормозного диска зависит от производителя. Тем не менее, основной обзор процесса остается одинаковым для всех твердотельных роторов. Тормозные роторы имеют простую конструкцию и не требуют большого количества инженерных и производственных ноу-хау. Наибольшую озабоченность у производителей тормозных дисков вызывает безопасность и контроль качества.
Из чего сделаны тормозные диски?
Изображение предоставлено AutoAction Большинство роторов изготовлены из чугуна. Это потому, что чугун дешев, обладает хорошими противоизносными свойствами и хорошо поглощает тепло. Роторы, разработанные для гонок, изготовлены из керамического композитного материала. Керамический композитный материал может работать при чрезвычайно высоких температурах. Если вы используете высококачественные роторы, вам не придется заменять их так часто.
Тормозные диски — довольно простые детали. Это круглые диски. Тем не менее, важно, чтобы производственный процесс каждый раз шел правильно. Ротор должен быть подходящего размера и толщины. Он также должен быть идеально круглым.
Оборудование, необходимое для производственного процесса, дорого и сложно в обслуживании. Это может объяснить, почему в мире всего несколько компаний производят качественные тормозные диски. Вот список наиболее распространенного оборудования, используемого в производстве роторов:
- Доменные печи
- Тигли
- Сверлильные станки с ЧПУ (для перфорированных и шлицевых роторов)
- Фрезы с ЧПУ, которые создают плоскую тормозную поверхность
Тормозной ротор Производственный процесс
Изображение предоставлено: Тодд Ласса Подводя итог, производственный процесс включает заливку горячего жидкого железа в форму и последующее охлаждение.
Первым этапом производственного процесса является создание пресс-формы. Обычно это делается с помощью фрезерного станка с ЧПУ, чтобы вырезать обратное изображение ротора из стального блока. Форма должна иметь точно правильные размеры, поэтому это важный шаг.
Далее расплавленный материал заливают в форму. Когда форма заполнена, верх смеси выравнивается. Затем форму накрывают и слегка прижимают, чтобы уплотнить всю деталь. Процесс изготовления цельных роторов обычно происходит в вакуумной печи. Далее ротор направляется в пресс, который оказывает на него давление около 20 тонн при нагревании примерно до 400 градусов. Этот процесс уплотняет ротор, что делает его намного прочнее.
Следующий шаг – прецизионное фрезерование и сверление. Тормозные поверхности фрезерованы плоско. Отверстия под гайки просверлены. Если ротор должен быть просверлен или прорезан, этот процесс также произойдет. Просверленные роторы имеют отверстия для отвода тепла и снижения веса. Роторы с прорезями обеспечивают лучшую вентиляцию во время тяжелых условий торможения, таких как гонки.
Когда ротор находится в своей окончательной форме, он полируется и проверяется на наличие структурных дефектов.
Последним этапом является очистка и упаковка роторов. Тормозной диск может потребовать дополнительной обработки, такой как пассивация хроматом цинка, прежде чем его можно будет упаковать и отправить.
В целом, создание качественного тормозного диска — это нечто большее, чем просто заливка металла в форму. Требуется точное оборудование и квалифицированный труд. Вот почему вы видите так много разных типов тормозных дисков. Основной производственный процесс одинаков, независимо от того, какой тип чугунного ротора вы покупаете.
производство тормозных дисков
Новая технология для высокоэффективных двигателей
Применение меди в здравоохранении и окружающей среде
Дейл Т. Питерс и Джон Г. Коуи CDA Inc.
Введение | Литые медные роторы | Результаты | Резюме
Введение
Около 70% потребления меди происходит из-за высокой электро- и теплопроводности меди. Электрооборудование на основе меди, конечно, стало довольно продвинутым, но возможности для совершенствования все еще существуют. В этой статье рассматривается один такой пример: в нем описываются текущие исследования, направленные на использование преимущества высокой проводимости меди таким образом, чтобы сделать возможным создание электродвигателей со сверхвысоким КПД.
Ассоциация разработчиков меди (CDA) является членом отраслевого консорциума, который в настоящее время занимается разработкой усовершенствованных двигателей. Двигатели будут использовать медь, а не алюминий в роторе двигателя, что кажется элементарным изменением, но которое может привести к снижению электрических потерь в двигателе на 20%. Двигатели указанных в программе размеров потребляют 35% всей электроэнергии, вырабатываемой в США; следовательно, значительное повышение эффективности двигателя приведет к огромной экономии энергии по всей стране.
Сегодняшние алюминиевые роторы двигателей изготавливаются путем литья под давлением или литья под давлением, как этот процесс известен во многих странах. Типичный ротор асинхронного двигателя состоит из набора продольно ориентированных токопроводящих стержней, соединенных двумя концевыми кольцами. Устройство напоминает беличью клетку, и к этому типу конструкции часто применяется термин «двигатель с беличьей клеткой». Производственный процесс включает в себя литье под давлением металла внутри и вокруг пакета стальных пластин, составляющих магнитную часть ротора.
Новые медные роторы также будут отлиты под давлением. Основным препятствием, препятствующим литью под давлением меди для конструкции токопроводящего стержня/концевого кольца ротора, было отсутствие прочного высокотемпературного материала формы для штампов или форм, используемых в процессе литья под давлением. Таким образом, основной целью программы роторов двигателей является разработка подходящих материалов для штампов. Результаты программы на сегодняшний день показывают, что сочетание высокотемпературных материалов штампов и условий обработки при повышенных температурах может значительно увеличить срок службы пресс-формы по сравнению с тем, который наблюдается при использовании обычных штамповых сталей (используемых с алюминием) для литья под давлением меди.
Литые медные роторы
Фон
Сегодня алюминийповсеместно используется для изготовления литых роторов двигателей, поскольку литье металла под давлением является хорошо зарекомендовавшим себя и экономичным методом производства. Поскольку медь труднее отлить под давлением, медные двигатели, когда они требуются, должны изготавливаться путем ручной сборки механически обработанных компонентов. Этот процесс является трудоемким и дорогостоящим, поэтому он применяется только к очень большим роторам двигателей, для которых литье под давлением нецелесообразно. В результате литье под давлением является предпочтительным методом изготовления, а алюминий — предпочтительным проводником для большей части производимых сегодня электродвигателей.
Формы из инструментальной стали, используемые для литья алюминия под давлением, не подходят для литья таких металлов, как медь, поскольку они не выдерживают высокой температуры плавления металлов. Отсутствие прочного и экономичного материала пресс-формы до сих пор было техническим барьером, препятствующим массовому производству литых под давлением медных роторов.
Исследование, спонсируемое Министерством энергетики, показало, что двигатели мощностью более 1/6 л.с. потребляют около 60% электроэнергии, вырабатываемой в США 1 Двигатели средней мощности мощностью от 1 до 125 л.с. потребляют около 60% электроэнергии, потребляемой всеми двигателями, или около 36% всей вырабатываемой электроэнергии. Прогнозируется, что повышение эффективности двигателя, которое может быть результатом использования медных роторов, приведет к общей экономии энергии в 2010 году в размере 20,2 E+12 Btu/год, если новые двигатели получат лишь 10% проникновения на рынок. Экономия вырастет до 143 E+12 Btu/год при ожидаемом проникновении на рынок от 50 до 70%. (Цифры различаются, поскольку повышение эффективности зависит от размера двигателя.) Эти цифры эквивалентны годовой выработке соответственно от 0,5 до 3,5 электростанций мощностью 600 МВт, работающих на 75% мощности.
Участие CDA в исследовательском проекте финансируется Международной ассоциацией меди, ООО. Дополнительное финансирование проекта поступает от Министерства энергетики США в рамках программы NICE 3 , Института кондиционирования и охлаждения, Trex Enterprises и ряда производители моторов. Общий план состоит в том, чтобы определить подходящие материалы для штампов, а затем спроектировать, изготовить и продемонстрировать формы, которые будут выдерживать условия литья под давлением меди в течение экономически приемлемого количества циклов литья или «выстрелов».
Очевидно, что чем дольше срок службы пресс-формы, тем большее количество двигателей можно произвести с меньшими затратами. Два американских производителя двигателей недавно провели анализ, который показывает, что экономика эксплуатации и производства двигателей благоприятствует использованию меди во всех классах двигателей, если срок службы может быть увеличен до 20 000 срабатываний.
Литые под давлением медные роторы могут обеспечить преимущества в производстве двигателей и/или производительности тремя способами:
- повышенная энергоэффективность двигателя во время работы
- снижение общих производственных затрат
- меньший вес мотора.
Как отмечалось ранее, основные проблемы при попытке отлить под давлением медные роторы двигателей заключаются в том, что материалы пресс-формы страдают от теплового удара и термической усталости. Обычные материалы для пресс-форм, в том числе инструментальные стали, используемые с алюминием, теряют прочность при высоких температурах, что требует проведения процесса при низких средних рабочих температурах (и температурах поверхности перед обжигом). Низкая начальная температура приводит к большому DT на поверхности штампа и, следовательно, к высокому напряжению в штампе при каждом выстреле. При литье меди под давлением высокая температура плавления металла, высокая теплота плавления, значительная скрытая теплота и высокая теплопроводность в совокупности обеспечивают максимальный тепловой удар.
Решение проблемы теплового удара заключается в использовании высокотемпературных материалов, обладающих тепловыми и термоупругими свойствами, способствующими минимизации термической деформации. Исследования, проведенные Международной ассоциацией исследований меди (INCRA) в 1970-х годах, подтверждают эти ожидания.
Проблемы теплового удара и усталости не ограничиваются медью, поскольку термоциклирование поверхности формы также ограничивает срок службы формы при литье алюминия под давлением. Циклические термические напряжения гораздо более серьезны для меди по причинам, указанным выше. По крайней мере, в одном недавнем случае плита литейной формы, изготовленная из высокопрочной стали (H-13, отраслевой стандарт литья под давлением), испытываемая с медью на предприятии производителя штамповочного оборудования, разрушилась всего после пяти литьевых выстрелов. Экономичные формы должны выдерживать тысячи циклов литья.
Результаты
Формы-кандидаты, разработанные для исследовательской программы, тестируются в исследовательском центре Formcast Corporation в Денвере, штат Колорадо. Плавильная печь Inductotherm питает 800-тонную машину для литья под давлением Buhler с компьютерным управлением в режиме реального времени, быстро расплавляя восемь фунтов меди с двухминутными интервалами, т. е. временем между последовательными штамповками. Тестовая форма, специально разработанная для проекта, имитирует условия, ожидаемые для одного литника промышленной пресс-формы с несколькими литниками. (Ворота — это точка, в которой расплавленный металл входит в полость формы.) Испытания по литью под давлением материалов-кандидатов для пресс-формы не включают пакет ламинированного железа из-за высокой стоимости ламинирующего материала, связанного с тысячами выстрелов, необходимых для программы испытаний. .
Создание базы
Рис. 1. Литье меди под давлением.
Чтобы установить базовый уровень для испытательной формы, было проведено первое испытание литья меди под давлением с использованием вставок штампа из стали H-13 (, рис. 1, ). Как и ожидалось, штампы обычно деградировали по мере увеличения использования. Весьма неожиданно, хотя очевидна некоторая тепловая проверка стальных вкладышей формы H-13 и дробеструйной гильзы, длительная прогонка меди по H-13 прошла успешно. Этот успех объясняется системой сухого извлечения из формы, коротким временем цикла (что сводит к минимуму тепловложение в форму) и использованием передового литейного оборудования с компьютерным управлением. С использованием одного комплекта штампов изготовлено более 800 отливок, превысив ожидания на порядок ( Рисунок 2 ).
Рис. 2. Набор инструментов для тестовых полостей из стали H-133 после первых нескольких выстрелов.
Металлографическое исследование показало, что макроструктуры литниковых и литниковых участков медных отливок под давлением демонстрируют внешнюю столбчатую зону закалки и смесь равноосных и столбчатых зерен в объеме. Микроструктуры этих областей также показали наличие междендритной фазы, скорее всего, медно-кислородной эвтектики. В секциях ворот обнаружены поверхностные трещины и надрывы; в целом их количество и глубина уменьшались с количеством выстрелов. Также были обнаружены внутренние дефекты в виде оксидных пленок, макроскопических пор и включений шлакового типа, и опять же их размеры и частота уменьшались с увеличением количества выстрелов. В отливках также присутствовала небольшая пористость, но в целом микроструктура здоровая (9).0105 Рисунок 3 ). Электропроводность отливок варьировалась от 95% до 101% IACS, в среднем 98% IACS. Химический анализ показал, что содержание железа варьировалось от 10 до 350 ppm, а кислорода от 0,06% до 0,15%.
Рис. 3. Микрофотография медного литья под давлением.
Микропористость является распространенным дефектом, связанным с процессом литья под давлением. 50X
Суперсплавы на основе никеля
Вкладыши штампов были изготовлены из сплавов Inconel® 617, 718 и 754. Было выполнено более 250 литья под давлением с использованием наборов штампов, изготовленных из этих сплавов. Набор Inconel 754 начал трещать очень рано (50 выстрелов) на ходу. Это было несколько неожиданно, поскольку этот сплав показал самую высокую прочность при температуре из трех испытанных сплавов на основе никеля. С другой стороны, этот сплав также имеет очень низкую пластичность при повышенных температурах. Сплав Inconel� 718 с самой низкой температурной прочностью начал растрескиваться примерно после 100 выстрелов.
Лучшим сплавом стал сплав Inconel® 617, который демонстрирует наилучшее сочетание прочности и пластичности при повышенных температурах. На комплектах штампов, изготовленных из этого сплава, после 250 выстрелов было заметно лишь незначительное растрескивание. Эти данные дают важный ключ к решению металлургической проблемы, а именно, что высокая вязкость разрушения при рабочей температуре может помочь снизить склонность к растрескиванию и, в конечном счете, увеличить срок службы формы.
Три медных отливки были подвергнуты металлургическому, химическому и физическому анализу. Вновь были обнаружены следы железа, кислорода и, в данном случае, никеля. В отливках также присутствовала небольшая микропористость, но общая микроструктура была здоровой. Электропроводность отливок, составляющая почти 100 % IACS, была лучше, чем у отливок, изготовленных в стальных формах. Способность сохранять такую высокую проводимость после плавления меди на открытом воздухе, а затем отливки через стальную дробь в никелевые формы является очень многообещающей, поскольку такое поведение предполагает, что медный лом из процесса литья под давлением будет полностью перерабатываться в литейном производстве. .
TZM (сплав молибдена) и Anviloy (сплав вольфрама)
Эти сплавы рассматривались в ранних исследованиях INCRA по материалам форм для литья под давлением меди, но их высокие температуры вязко-хрупкого перехода предполагают, что целостность формы будет под угрозой, особенно при первых нескольких впрысках. Одним из решений этой проблемы является повышение температуры форм с помощью нагревателей электрического сопротивления.
Заготовки из сплавов TZM и Anviloy соответственно были обработаны в наборы штампов. Их нагревали примерно до 500°С (932 F) до и во время испытаний на литье под давлением. С этими наборами штампов было успешно произведено более 500 выстрелов. Ограниченная степень окисления развивалась как на штампах TZM, так и на штампах Anviloy; тем не менее, никакого растрескивания из-за теплового контроля не наблюдалось. Фактически, характеристики этих двух материалов для штампов были беспрецедентными (рис. 4). Опыт работы с этими штампами показал, что повышение рабочей температуры штампа уменьшает тепловое расширение и сжатие, тем самым снижая склонность к растрескиванию под воздействием термической усталости, более известному как «термическая проверка». Ожидается, что дальнейшее повышение рабочей температуры штампов значительно продлит срок их службы за счет ограничения количества циклических деформаций, связанных с нагревом и охлаждением. В частности, прогнозируется, что работа штампов при повышенных температурах (чуть ниже точки замерзания меди, 1085°С (1985 F) продлит срок службы штампов до тысяч циклов.
Подвижная половина набора штампов, содержащего материалы TZM и Anviloy.![]() | Крупный план смерти Анвилоя после 500 выстрелов. |
Растрескивания от термической усталости (термическая проверка) не наблюдалось.
Вольфрам CVD
Вольфрамовые вставки были изготовлены по технологии высокоскоростного химического осаждения из паровой фазы (CVD), разработанной компанией Trex Enterprises, Сан-Диего, Калифорния. Процесс CVD, который проводится на графитовой оправке, давал преимущество изготовления сетчатой формы или формы, близкой к сетчатой. Одним недостатком является то, что процесс приводит к относительно тонким структурам. Соответствующая основа для тонких вольфрамовых и вольфрам-рениевых изделий, изготовленных с использованием этой технологии, еще предстоит разработать. Однако для проверки этой концепции на обработанную молибденовую заготовку TZM нанесли вольфрамовые покрытия CVD. Медные отливки формы, показанной на рисунке 2, были изготовлены в Formcast с использованием этих композитных структур. Стойкость вольфрамовых форм CVD, которая на сегодняшний день была разочаровывающе короткой, по-видимому, ограничена столбчатой структурой зерна вольфрама. Последующие модификации были внесены в пресс-форму, установленную в Formcast, для повышения температуры инструмента. Ожидается, что эти модификации, а также усилия предприятий Trex по улучшению структуры зерна увеличат срок службы инструментов, изготовленных по этой технологии.
Резюме
Литые под давлением медные роторы двигателя приведут к привлекательным улучшениям энергоэффективности электродвигателя. Делаются успехи в разработке прочных и экономичных материалов для пресс-форм, что сегодня является основным препятствием, препятствующим литью под давлением медных роторов. Продолжительный пробег меди по TZM и вольфрамовому сплаву Anviloy был выполнен без термоконтроля. Повышение рабочей температуры штампов продлило срок их службы за счет ограничения количества циклических деформаций, связанных с нагревом и охлаждением. Использование высокотемпературных материалов для штампов значительно увеличило срок службы формы, что сделало возможным литье под давлением меди и других материалов с высокой температурой плавления. Ожидается, что комплект пресс-форм, включающий комбинацию сплавов на основе никеля и тугоплавких сплавов (последние используются в самых горячих частях матрицы), позволит экономично производить отлитые под давлением медные роторы.
Текущие планы предусматривают завершение Фазы II исследовательской программы, а именно производство нескольких литых под давлением медных роторов для тестирования и оценки производителями электродвигателей. После завершения Фазы II акцент проекта сместится на передачу новой технологии литья под давлением производителям двигателей по всему миру.
Также в этом выпуске:
- Судьба меди, выпущенная из музея кораблей Васа
- Шведская программа долгосрочной изоляции высокоактивных ядерных отходов в медных контейнерах
- Медный ротор двигателя: новая технология для высокоэффективных двигателей
- Память формы и сверхэластичные сплавы
- Роль меди в захоронении радиоактивных отходов III – опыт США
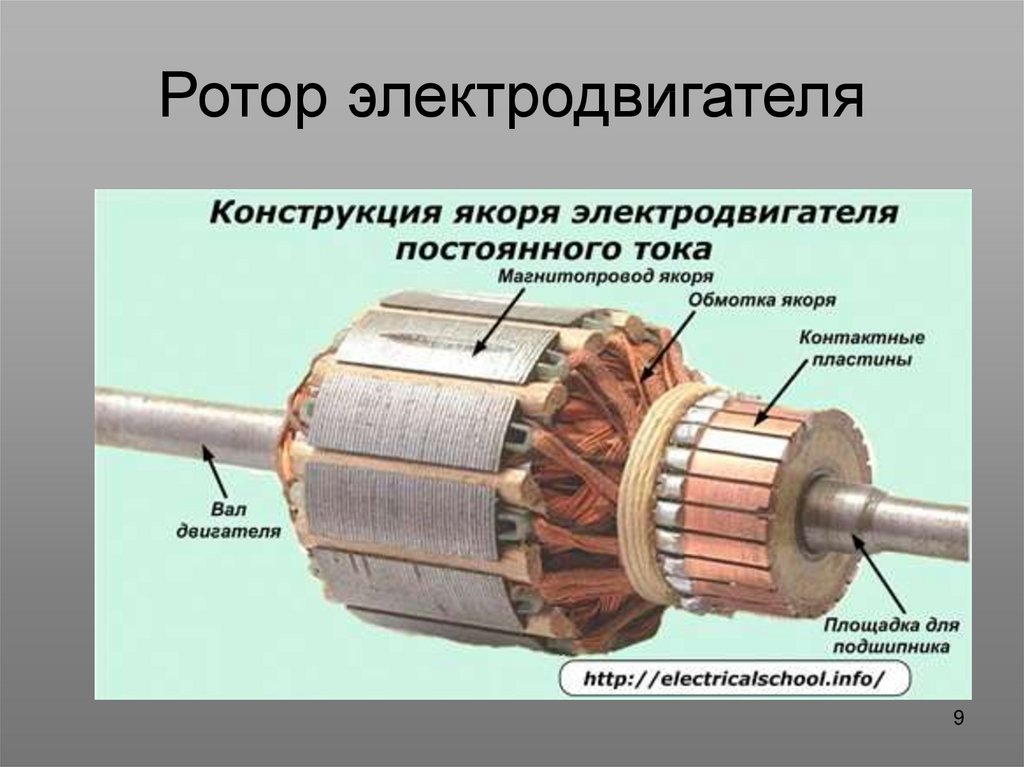