ГОСТ 6009-74
ГОСТ 6009-74
Группа В24
ОКП 09 3500
Дата введения 1975-01-01
Постановлением Государственного комитета стандартов Совета Министров СССР от 17 января 1974 г. N 143 дата введения установлена 01.01.75
Ограничение срока действия снято по протоколу N 4-93 Межгосударственного Совета по стандартизации, метрологии и сертификации (ИУС 4-94)
ВЗАМЕН ГОСТ 6009-57
ИЗДАНИЕ с Изменением N 1, утвержденным в мае 1985 г. (ИУС 8-85).
Настоящий стандарт распространяется на стальную ленту шириной от 20 до 220 мм, толщиной от 1,2 до 5,0 мм, получаемую горячей прокаткой или продольной резкой горячекатаной листовой рулонной стали.
1. СОРТАМЕНТ
1.1. Ширина, толщина и масса 1 м ленты должны соответствовать указанным в табл.1.
Таблица 1
Ширина, мм | Масса 1 м ленты, кг, при толщине, мм | ||||||||||||
1,2 | 1,4 | 1,5 | 1,6 | 1,8 | 2,0 | 2,2 | 2,5 | 3,0 | 3,5 | 4,0 | 4,5 | 5,0 | |
20 | 0,188 | 0,220 | 0,236 | 0,251 | 0,283 | 0,314 | 0,345 | 0,393 | 0,471 | 0,550 | — | — | — |
22 | 0,207 | 0,242 | 0,259 | 0,276 | 0,311 | 0,345 | 0,380 | 0,432 | 0,518 | 0,604 | — | — | — |
25 | 0,236 | 0,275 | 0,294 | 0,314 | 0,353 | 0,393 | 0,432 | 0,491 | 0,589 | 0,687 | — | — | — |
28 | 0,264 | 0,308 | 0,327 | 0,352 | 0,396 | 0,440 | 0,484 | 0,550 | 0,659 | 0,769 | — | — | — |
30 | — | 0,330 | 0,353 | 0,377 | 0,424 | 0,471 | 0,518 | 0,589 | 0,707 | 0,824 | — | — | — |
32 | — | 0,352 | 0,377 | 0,402 | 0,452 | 0,502 | 0,553 | 0,628 | 0,754 | 0,879 | — | — | — |
36 | — | 0,396 | 0,424 | 0,452 | 0,509 | 0,565 | 0,622 | 0,707 | 0,848 | 0,989 | — | — | — |
40 | — | 0,440 | 0,471 | 0,502 | 0,565 | 0,628 | 0,691 | 0,785 | 0,942 | 1,099 | — | — | — |
45 | — | 0,495 | 0,530 | 0,565 | 0,636 | 0,707 | 0,777 | 0,883 | 1,060 | 1,236 | — | — | — |
50 | — | 0,550 | 0,589 | 0,628 | 0,707 | 0,785 | 0,864 | 0,981 | 1,178 | 1,374 | — | — | — |
60 | — | — | — | — | — | 0,942 | 1,036 | 1,178 | 1,413 | 1,649 | — | — | — |
63 | — | — | — | — | — | 0,989 | 1,088 | 1,236 | 1,484 | 1,731 | — | — | — |
65 | — | — | — | — | — | 1,021 | 1,123 | 1,276 | 1,531 | 1,786 | — | — | — |
70 | — | — | — | — | — | 1,072 | 1,209 | 1,374 | 1,649 | 1,923 | — | — | — |
75 | — | — | — | — | — | 1,178 | 1,295 | 1,472 | 1,766 | 2,061 | — | — | — |
80 | — | — | — | — | — | 1,256 | 1,382 | 1,570 | 1,884 | 2,198 | — | — | — |
85 | — | — | — | — | — | 1,334 | 1,468 | 1,668 | 2,002 | 2,335 | — | — | — |
90 | — | — | — | — | — | — | — | 1,766 | 2,120 | 2,473 | — | — | — |
100 | — | — | — | — | — | — | — | 1,963 | 2,355 | 2,748 | — | — | — |
110 | — | — | — | — | — | — | — | 2,159 | 2,591 | 3,022 | — | — | — |
120 | — | — | — | — | — | — | — | 2,355 | 2,826 | 3,297 | — | — | — |
130 | — | — | — | — | — | — | — | 2,551 | 3,062 | 3,572 | — | — | — |
150 | — | — | — | — | — | — | — | 2,944 | 3,533 | 4,121 | — | — | — |
160 | — | — | — | — | — | — | — | 3,136 | 3,768 | 4,396 | — | — | — |
170 | — | — | — | — | — | — | — | 3,332 | 4,004 | 4,671 | — | — | — |
175 | — | — | — | — | — | — | — | 3,434 | 4,121 | 4,808 | — | — | — |
190 | — | — | — | — | — | — | — | 3,724 | 4,475 | 5,220 | — | — | — |
200 | — | — | — | — | — | — | — | 3,920 | 4,710 | 5,495 | 6,280 | 7,065 | 7,850 |
215 | — | — | — | — | — | — | — | — | 5,063 | 5,907 | 6,751 | 7,595 | 8,439 |
220 | — | — | — | — | — | — | — | — | 5,181 | 6,045 | 6,908 | 7,772 | 8,635 |
Примечание. Площадь поперечного сечения ленты вычислена по номинальным размерам. При вычислении массы 1 м плотность стали принята равной 7,85 г/см.
1.2. Предельные отклонения по толщине ленты должны соответствовать:
для ленты с катаной кромкой — табл.2;
Таблица 2
мм | |
Ширина ленты | Предельное отклонение по толщине |
От 20 до 100 | +0,15 |
Св.100 » 150 | +0,20 |
» 160 » 220 | +0,25 |
для разрезной ленты — табл. 3.
Таблица 3
мм | ||||
Толщина ленты | Предельное отклонение по толщине при ширине исходной ленты | |||
Св. 200 до 500 | Св. 500 до 750 | Св. 750 до 1100 | Св. 1100 до 1500 | |
1,2 | ±0,11 | ±0,12 | ±0,18 | — |
Св. 1,2 до 1,4 | ±0,12 | ±0,13 | ±0,16 | ±0,16 |
» 1,4 » 1,8 | ±0,14 | ±0,15 | ±0,16 | ±0,17 |
» 1,8 » 2,0 | +0,14 | +0,15 | +0,15 | +0,16 |
» 2,0 » 2,2 | +0,14 | +0,15 | +0,15 | +0,17 |
» 2,2 » 2,5 | +0,14 | +0,15 | +0,16 | +0,17 |
» 2,5 » 3,0 | +0,15 | +0,16 | +0,17 | +0,18 |
» 3,0 » 3,5 | +0,16 | +0,17 | +0,18 | +0,22 |
» 3,5 » 3,8 | +0,18 | +0,20 | +0,20 | +0,25 |
» 3,8 » 5,0 | +0,20 | +0,20 | +0,20 | +0,28 |
Для ленты, полученной путем продольной резки горячекатаной листовой рулонной стали (разрезная лента), разнотолщинность по поперечному сечению не должна превышать половины суммы предельных отклонений по толщине.
1.3. Предельные отклонения по ширине должны соответствовать:
мм — для ленты с катаной кромкой шириной до 60 мм;
% ширины — для ленты с катаной кромкой шириной свыше 60 мм;
+2,0 мм — для разрезной ленты.
Пример условного обозначения горячекатаной ленты толщиной 3,5 мм, шириной 50 мм из стали марки БСт2пс:
Лента 3,5х50 БСт2пс ГОСТ 6009-74
2. ТЕХНИЧЕСКИЕ ТРЕБОВАНИЯ
2.1. Лента должна изготовляться из углеродистой стали обыкновенного качества марок ВСт0-БСт5 первой или второй категории всех степеней раскисления по ГОСТ 380-94*
______________
* На территории Российской Федерации действует ГОСТ 380-2005. — Примечание изготовителя базы данных.
2.2. На поверхности ленты не допускаются дефекты, глубина или высота которых превышает предельные отклонения по толщине. Для разрезной ленты допускаются заусенцы на кромках высотой не более 1 мм.
Допускается пологая зачистка наружных дефектов поверхности ленты. Ширина зачистки должна быть не менее пятикратной глубины. Глубина зачистки не должна превышать минусового предельного отклонения по толщине ленты.
2.3. По согласованию изготовителя с потребителем концы ленты с катаной кромкой обрезаются.
2.4. Допускается телескопичность рулона в пределах ширины ленты, но не более 50 мм.
2.5. Серповидность (кривизна в горизонтальной плоскости) ленты с катаной кромкой должна составлять 0,6% от длины, разрезной ленты — устанавливается по согласованию изготовителя с потребителем.
3. ПРАВИЛА ПРИЕМКИ
3.1. Общие правила приемки — по ГОСТ 7566-94.
3.2. К приемке лента представляется партиями. Партия должна состоять из лент одной марки стали, одной плавки и одного размера. Допускаются сборные партии из стали одной марки разных плавок, но не более четырех.
3.3. Для проверки качества и размеров от партии отбирают 2% ленты, но не менее двух мотков.
(Измененная редакция, Изм. N 1).
3.4. (Исключен, Изм. N 1).
4. МЕТОДЫ ИСПЫТАНИЙ
4.1. Для определения химического состава стали пробы отбирают по ГОСТ 7565-81.
Химический состав разрезной ленты не контролируется, а указывается в сертификате по данным плавочного анализа.
4.2. Поверхность ленты проверяют без применения увеличительных приборов на длине не менее двух витков от конца рулона.
4.3. Проверка размера ленты производится микрометром или другим мерительным инструментом на расстоянии не менее длины одного витка от конца рулона. Толщину ленты шириной до 30 мм измеряют в середине ширины, свыше 30 мм — на расстоянии не менее 15 мм от кромки.
5. МАРКИРОВКА, УПАКОВКА, ТРАНСПОРТИРОВАНИЕ И ХРАНЕНИЕ
5.1. Маркировка, упаковка, транспортирование и хранение — по ГОСТ 7566-94.
Разд.5. (Измененная редакция, Изм.
Электронный текст документа
подготовлен АО «Кодекс» и сверен по:
официальное издание
Стальной прокат. Ленты: Сб. ГОСТов. —
М.: ИПК Издательство стандартов, 2003
Лента стальная горячекатаная ГОСТ 6009-74 цена
Лента стальная горячекатаная ГОСТ 6009-74 от производителя
Реализуемая в нашем каталоге лента стальная горячекатаная ГОСТ отличается высоким качеством продукции и является универсальным продуктом. Он так же универсален, как и множество приложений. Подробную информацию о горячекатаной стали можно найти на портале информации о продукции.
Горячекатаная стальная полоса на любой вкус
Мы поставляем полосы шириной до 1750 мм и толщиной до 20 мм. Наши продукты доступны как в маринованном, так и в несобранном виде, в виде разрезанных или широких полос, а также в виде нарезанных листов.
Марки стали:
- Мягкие стали.
- Конструкционные стали.
- Микролегированные стали.
- Цементационные и термообрабатываемые стали.
- Мартенситные стали.
- Сложнофазные стали.
- Двухфазные сталиФерритно-бейнитные стали.
- Стали для опор и ободьев.
- Стали для эмалирования.
- Стали для газовых баллонов.
- Погодостойкие конструкционные стали.
-
Износостойкие стали.
- Высокопрочные и сверхвысокопрочные стали.
И если вас интересует ГОСТ 6009 74 лента стальная горячекатаная купить, которую можно через сайт, тогда вы обратились по нужному адресу.
Лента стальная горячекатаная
Мягкие нелегированные стали для холодной штамповки:
- Эти стали обычно поставляются в соответствии ГОСТ. Они используются в приложениях, в которых формуемость важнее прочности.
Конструкционные стали
Одна из областей их применения — машиностроение. Стали характеризуются минимальным пределом текучести, запасом прочности на разрыв и минимальным удлинением разрушения. Они используются для легкого волочения, формовки и гибки.
Наша торговая марка подразделения металлургии, производящая горячекатаную мелкозернистую сталь с лучшими характеристиками холодной штамповки и отличной свариваемостью. Стали доступны в различных марках и классах прочности. Будь то термомеханическая или нормализованная прокатка, горячекатаная полоса или толстый лист, в рулонах, разрезанных полосах или нарезанных листах. Все из вышеуказанного является незаменимым материалом в машиностроении, автомобильном дизайне и в обрабатывающей промышленности.
Предлагаемые марки — это износостойкие стали с высокой твердостью, достигаемой за счет ускоренного охлаждения непосредственно за счет нагрева при прокатке. Они характеризуются высокой степенью износостойкости и особенно подходят для применений с высокими механическими нагрузками и высокими уровнями истирания
Цементационные и термообрабатываемые стали
Стали с цементацией и термообработкой в соответствии ГОСТ, а также стандартом качества выпуска используются для прямой обработки или используются для холодной прокатки. Эти стали обычно подвергаются термообработке для достижения желаемых технологических свойств и свойств компонентов. Они используются в приложениях, которые должны обеспечивать оптимальный баланс между твердостью и вязкостью.
Полюсные листы
Листы полюсов представляют собой термомеханически прокатанные стали с гарантированными магнитными свойствами. Стандартные сорта соответствуют определенным нормам. Поставляются также сверхвысокопрочные специальные марки, предлагаемые в нашем каталоге от производителя.
Горячекатаные эмалированные стали
Самые узкие допуски, высокое качество материалов и узкоспециализированный опыт применения гарантируют, что продукция соответствует любым требованиям. Комбинации толстых горячекатаных сталей и тонких холоднокатаных сталей, например, часто используются в промышленных конструкциях силосов. Кроме вышеуказанного, в каталоге вы найдете такой товар, как лента стальная горячекатаная цена, которой не высокая для потребителей. И сможете заказать её через телефон или сайт с оперативной доставкой по России и СНГ с отличными скидками и другими максимально выгодными предложениями.
Лента стальная горячекатаная ГОСТ 6009-74 цена
Лента стальная горячекатаная ГОСТ 6009-74 от производителя
Реализуемая в нашем каталоге лента стальная горячекатаная ГОСТ отличается высоким качеством продукции и является универсальным продуктом. Он так же универсален, как и множество приложений. Подробную информацию о горячекатаной стали можно найти на портале информации о продукции.
Горячекатаная стальная полоса на любой вкус
Мы поставляем полосы шириной до 1750 мм и толщиной до 20 мм. Наши продукты доступны как в маринованном, так и в несобранном виде, в виде разрезанных или широких полос, а также в виде нарезанных листов. Наше требование — неизменно высокое качество и производство с минимальными допусками. Лента стальная горячекатаная ГОСТ 6009-74 нашего производства доступна в широком ассортименте марок. Благодаря разнообразию различных сплавов и программ прокатки наши клиенты могут получить именно ту сталь, которая подходит для их конкретных применений.
Марки стали:
- Мягкие стали.
- Конструкционные стали.
- Микролегированные стали.
- Цементационные и термообрабатываемые стали.
-
Мартенситные стали.
- Сложнофазные стали.
- Двухфазные сталиФерритно-бейнитные стали.
- Стали для опор и ободьев.
- Стали для эмалирования.
- Стали для газовых баллонов.
- Погодостойкие конструкционные стали.
- Износостойкие стали.
- Высокопрочные и сверхвысокопрочные стали.
И если вас интересует ГОСТ 6009 74 лента стальная горячекатаная купить, которую можно через сайт, тогда вы обратились по нужному адресу.
Лента стальная горячекатаная
Мягкие нелегированные стали для холодной штамповки:
- Эти стали обычно поставляются в соответствии ГОСТ. Они используются в приложениях, в которых формуемость важнее прочности.
Конструкционные стали
Одна из областей их применения — машиностроение. Стали характеризуются минимальным пределом текучести, запасом прочности на разрыв и минимальным удлинением разрушения. Они используются для легкого волочения, формовки и гибки.
Наша торговая марка подразделения металлургии, производящая горячекатаную мелкозернистую сталь с лучшими характеристиками холодной штамповки и отличной свариваемостью. Стали доступны в различных марках и классах прочности. Будь то термомеханическая или нормализованная прокатка, горячекатаная полоса или толстый лист, в рулонах, разрезанных полосах или нарезанных листах. Все из вышеуказанного является незаменимым материалом в машиностроении, автомобильном дизайне и в обрабатывающей промышленности.
Предлагаемые марки — это износостойкие стали с высокой твердостью, достигаемой за счет ускоренного охлаждения непосредственно за счет нагрева при прокатке. Они характеризуются высокой степенью износостойкости и особенно подходят для применений с высокими механическими нагрузками и высокими уровнями истирания
Цементационные и термообрабатываемые стали
Стали с цементацией и термообработкой в соответствии ГОСТ, а также стандартом качества выпуска используются для прямой обработки или используются для холодной прокатки. Эти стали обычно подвергаются термообработке для достижения желаемых технологических свойств и свойств компонентов. Они используются в приложениях, которые должны обеспечивать оптимальный баланс между твердостью и вязкостью.
Полюсные листы
Листы полюсов представляют собой термомеханически прокатанные стали с гарантированными магнитными свойствами. Стандартные сорта соответствуют определенным нормам. Поставляются также сверхвысокопрочные специальные марки, предлагаемые в нашем каталоге от производителя.
Горячекатаные эмалированные стали
Самые узкие допуски, высокое качество материалов и узкоспециализированный опыт применения гарантируют, что продукция соответствует любым требованиям. Комбинации толстых горячекатаных сталей и тонких холоднокатаных сталей, например, часто используются в промышленных конструкциях силосов. Кроме вышеуказанного, в каталоге вы найдете такой товар, как лента стальная горячекатаная цена, которой не высокая для потребителей. И сможете заказать её через телефон или сайт с оперативной доставкой по России и СНГ с отличными скидками и другими максимально выгодными предложениями.
Лента стальная горячекатаная ГОСТ 6009-74 цена в Тюмени
Изготовленная согласно требованиям гост 6009 74 лента стальная горячекатаная находит применение в строительстве, машиностроении, металлообработке, производстве различного технологического оборудования, машин и механизмов. Изделие используется в транспортной отрасли для упаковки подготовленных для перевозки товаров, грузов и усиления прочностных характеристик различной тары. Оно также востребовано в изготовлении различных металлоконструкций, соединенных с применением сварки или болтов, гаек и другого крепежа.
Лента стальная отличается высокими показателями механических характеристик, в том числе хорошей прочностью, поверхностной твердостью, устойчивостью к износу, трению и к усилиям на растяжение и разрыв. Высокий уровень пластичности и технологичности позволяет обрабатывать изделие с применением традиционного металлорежущего оборудования. Из полуфабриката изготавливают продукцию сложной пространственной конфигурации с минимальными затратами финансовых средств и рабочего времени.
Выпускаемая нашим предприятием лента горячекатаная способна эффективно функционировать как при низких, так и при высоких температурах. При этом сохраняются все ее технологические и технические свойства.
Лента стальная горячекатаная является податливым к штамповке и прессованию изделием. Из неё изготавливают широкий ассортимент металлопродукции, применяемый в качестве запасных частей к автомобилям, сельскохозяйственной и строительной технике, технологическому оборудованию, различным машинам и механизмам. Продукция предназначена для длительного использования в режиме жесткой нагрузки.
У нашего предприятия можно купить на привлекательных условиях горячекатаную ленту всех типоразмеров. Отпускная цена изделия ниже средней по отрасли. Помогаем партнерам в организации доставки товара по месту назначения.
Лента стальная горячекатаная
Стальной Дивизион
Работа и карьера Покупка voestalpine AG EN Deutsch Сегменты Автоматизированная индустрия Промышленность коммерческого транспорта Машиностроение Кровля, обшивка, водоотвод Промышленность бытовой техники Бытовые системы Электротехническая промышленность Раздел промышленность Торговля сталью Сервисный центр стали Промышленность холодной прокатки Офшор Linepipe Аппаратебау Штальбау Продукты Тяжелые пластины Головы и шишки Аккорды Толстый лист из конструкционных сталей общего назначения Толстый лист из цементируемых и термообрабатываемых сталей Толстый лист из судостроительной стали Толстый лист из мелкозернистой конструкционной стали термомеханической прокатки.
Горячекатаная полоса из стали: изображения, фотографии и векторные изображения
В настоящее время вы используете более старую версию браузера, и ваши возможности могут быть не оптимальными.
PremiumBeat blogEnterprisePricingImageFootageMusicEditorialDev API
Вход
Зарегистрироваться
Меню
FiltersClear allAll изображений- Все изображения
- Фото
- Vectors
- Иллюстрации
- Editorial
- Видеоматериал
- Музыка
- Поиск по изображению
Горячекатаный полосовой прокат
Сортировать по
нержавеющая сталь.
микроструктура, текстура, тонкая полоса, прокатка, линейный, прочность, поверхность, зернистость, феррит, аустенит
Литье полосы обеспечивает некоторые основные металлургические и коммерческие улучшения по сравнению с традиционными методами обработки стального листа
- Во-первых, она поставляет ленту с той же геометрией , что и при горячей прокатке. Это позволяет избежать горячей прокатки.
- Во-вторых, обычно слабая первичная кристаллографическая текстура литой полосы снижает анизотропию.
- В-третьих, высокая скорость затвердевания приводит к улучшенным микроструктурам по сравнению с обычным литьем.
- В-четвертых, можно напрямую отливать стальные листы, которые не обладают достаточной собственной пластичностью для прокатки, например трансформаторные стали с высоким содержанием Si,
некоторые интерметаллические сплавы или стали с высоким содержанием углерода.
- В-пятых, неэкономично. производить небольшие количества высококачественной стали методом непрерывной разливки и горячей прокатки.Кроме того, капитальные затраты на синтез горячих прокат рулонов намного ниже, чем на обычных литейно-прокатных заводах. Во-вторых, значительно снижается общая энергия, необходимая для производства конечных продуктов, и соответственно снижаются затраты на энергию. Следовательно, технология полосового литья позволяет небольшим заводам по производству стали производить продукцию напрямую без необходимости передачи этого заключительного этапа другим компаниям, и, таким образом, имеет стратегическое значение. преимущество перед обычными технологиями литья.
Это был 1857 год, когда изобретатель сэр Генри Бессемер запатентовал основы двухвалкового литья металлов. Но весь спектр и потенциал этой новой идеи, сегодня называемой полосой
литье, и его влияние на производство стали не будет реализовано в течение нескольких поколений.
Последние достижения в технологии разливки полосы позволяют производить ферритную и аустенитную нержавеющую сталь с определенной геометрией и качеством, как и производимые обычной горячей прокаткой.Это позволяет обойти всю процедуру горячей прокатки. Случайное начальное распределение кристаллографической ориентации по толщине литой полосы. приводит к более однородным свойствам конечного стального листа. Последний эффект устраняет хорошо известный феноненон с выступами в ферритной нержавеющей стали, который часто ухудшает качество поверхности. изначально горячекатаной ленты. В данной статье представлена кристаллографическая текстура и микроструктура полосовой ферритной и аустенитной нержавеющей стали для различной толщины.В Результаты сравниваются с результатами для образцов, изготовленных традиционным способом, то есть одновременно литых и впоследствии горячекатаных образцов.
Листы из нержавеющей стали производятся промышленным способом путем непрерывного литья, горячей прокатки, холодной прокатки и перекристаллизации. Однако недавний прогресс в производстве
стальных листов на пилотных машинах для разливки полосы все больше стимулировал усилия по превращению таких устройств в промышленное производство [1-6]. Двухвалковые разливочные машины разного диаметра для
производство сталей сочетает в себе две операции: заливку жидкого металла между двумя валками и наложение небольшой деформации на затвердевшие металлические пленки в зазоре прокатки.
для производства наматываемых лент [1-4].Полосовое литье обеспечивает пять основных улучшений по сравнению с традиционными методами обработки. Во-первых, он поставляет стальную ленту с таким же
геометрия, полученная горячей прокаткой [1,2]. Это позволяет обойти процесс горячей прокатки. Во-вторых, слабая текстура литой полосы приводит к снижению анизотропии по сравнению с
до
горячекатаных листов [3,4, 7-10]. В-третьих, высокая скорость затвердевания приводит к улучшенной микроструктуре по сравнению с обычным литьем [II, 12]. В-четвертых, можно напрямую
литые стальные листы, которые t Текстуры рекристаллизации настоящего материала будут исследованы в следующей статье [25]. не наделены достаточным внутренним
пластичность для прокатки, например трансформаторных сталей с высоким содержанием Si [13,14]. В-пятых, неэкономично производить небольшие партии высоколегированных нержавеющих сталей.
методом непрерывной разливки и горячей прокатки.
Хотя многие начальные технические проблемы двухвалковых литейных машин были решены [1,2, 5,6, 13, 14], микроструктура и текстура, которые развиваются во время прокатки и отжига полосы
Литые аустенитные стали еще не исследованы. Из предыдущих исследований ферритных [10,15-18] и аустенитных [9,10,19-24] нержавеющих сталей, производимых традиционным способом, он
известно, что исходная морфология и текстура зерна могут существенно влиять на эволюцию текстуры в процессе холодной прокатки и отжига]: Помимо описания текстуры
и микроструктура, полученная в результате разливки полосы и последующей обработки, важен также второй, более фундаментальный момент
.Нестабильные аустенитные нержавеющие стали претерпевают фазовое превращение, вызванное деформацией, во время холодной прокатки. Этот механизм является строго кристаллографическим и
таким образом выступает за использование количественного анализа текстуры. Таким образом, нестабильные аустенитные стали можно рассматривать как модельное вещество для изучения деформационного поведения
f.c.c.-b.c.c. двухфазный сплав.
Исследование текстуры нестабильных аустенитных сталей сложнее, чем стабильных. Сначала нестабильные стали подвергаются фазе частичной деформации
. Превращение аустенита в мартенсит при холодной прокатке.Во-вторых, преобразованная объемная доля мартенсита зависит от пути деформации. Этот факт представляет собой
существенное отличие настоящего материала от латуни 60/40, которая часто используется в качестве двухфазного модельного вещества [26,27]. В-третьих, в нестабильных аустенитах ГЦК. и b.c.c.
Фазы связаны не только за счет равновесия напряжений и совместимости деформаций, но и за счет строгих правил кристаллографического преобразования. В-четвертых, из-за
почти идентичный химический состав обеих фаз, угол Брэгга {III} аустенита перекрывает угол Брэгга {IIO} мартенсита. В этом документе рассматриваются
микроструктура и кристаллографическая текстура гильзы ленты и, впоследствии, холоднокатаной стали
с 18% Cr и 8,5% Ni по отношению к вышеупомянутым точкам. Результаты сравниваются с результатами для образцов, изготовленных традиционным способом. За это
Целевые идентичные эксперименты были проведены как на полосовых, так и на горячекатаных исходных образцах. Микроструктура и текстура изучались в различных толщинах.
слои. Экспериментально наблюдаемые текстуры аустенита
при холодной прокатке сравнивались с расчетами Тейлора с учетом взаимодействия зерен [28].Этот подход уже был успешно использован в
для описания текстуры прокатки алюминия [29,30]. В настоящем моделировании рассматриваются как <110), так и чистые (211) векторы скольжения (механизм скольжения карты
) [31, 32]. Текстура мартенсита моделировалась с использованием модели деформации типа Сакса с учетом систем скольжения {11O} (III) и {211} (III).
Более конкретно микроструктура и эволюция текстуры полосового литья и горячекатаного аустенитного
нержавеющая сталь (18% Cr, 8. 5% Ni) при холодной прокатке (максимальное уменьшение толщины Dd / d; =
80%). Микроструктура горячей полосы была однородной по толщине листа, за исключением
В центральном слое появилась небольшая объемная доля мартенсита. Текстура горячей полосы показала
градиент по толщине, который обсуждался с точки зрения распределения сдвига во время горячей прокатки. В
На микроструктуре литой полосы наблюдались глобулярные зерна с мартенситом в центральном слое и блоки
аустенитные дендриты в других слоях.Образование мартенсита связывали с деформацией
затвердевшие пленки в зазоре прокатки. Образец ленточного литья показал слабую текстуру волокна, близкую к
{OOI} (uvw), который интерпретировался с точки зрения выделения роста во время затвердевания. При холодной прокатке в обоих
В типах образцов объемная доля мартенсита увеличилась до ~ 50 об.% (уменьшение 80%). В
Текстура аустенита при холодной прокатке в обоих случаях характеризовалась {OIl} (211) и {OIl} (100). В
текстура холодной прокатки горячей полосы была сильнее, чем у образца из полосы, что
к
влияние исходной текстуры и размера зерна. Текстура холодной прокатки аустенита моделировалась с помощью модели типа Тейлора с учетом взаимодействия зерен и
так называемый механизм скольжения карты. Текстура мартенсита характеризовалась {211} (0 II) и {II I} 011). Первый компонент интерпретировался с точки зрения ослабления ограничений сдвига.
Последнее было приписано селективному фазовому превращению {OlI} OIl) (аустенита) в {332} (113) (мартенсит), который затем повернулся в сторону {JII} (112). Текстуры прокатки мартенсита
моделировались с использованием деформационной модели типа Сакса.
Микроструктура и текстура отлитой из полосы, а также горячекатаной аустенитной нержавеющей стали (18% Cr, 8,5% Ni) исследуются с помощью оптической металлографии и количественной
Рентгеновский текстурный анализ. В горячей полосе выявляется однородная микроструктура вместе с градиентом текстуры по толщине, состоящим из текстуры слабой холодной прокатки в центре.
слой и текстура сдвига близко к поверхностным слоям. Результат обсуждается с точки зрения профиля сдвига по толщине, который создается во время горячей прокатки. В материале полосового литья
случайное распределение ориентации, а также развитие мартенсита вблизи центрального слоя объясняется столкновением и деформацией пленок, которые затвердевают на поверхностях
литейные валки. Текстура, близкая к поверхности, объясняется селекцией роста зерен с ориентацией {001} (uvw).
горячекатаная сталь — Перевод на немецкий — примеры английский
Эти примеры могут содержать грубые слова на основании вашего поиска.
Эти примеры могут содержать разговорные слова, основанные на вашем поиске.
Площадь 30 м² была оборудована мебелью и элементами дизайна новой концепции магазина «Пионер», которые состоят в основном из древесины сосны и горячекатаной стали .
Умереть ок. Площадь 30 м², площадь Флэше, Мёбельн и дизайн, новый магазин «Пионер», Концерт, вид на Кифернхольц и теплый валец, Шталь лучший.
Тарелка клапана по одному из пп.1-3, отличающаяся тем, что она изготовлена из горячекатаной стали , твердость которой увеличена до указанной заданной твердости поверхности путем регулирования количества содержащихся в ней углеродных и марганцевых компонентов.
Ventilplatte nach einem der Ansprüche 1 bis 3, dadurch gekennzeichnet, daß diese aus warmgewalztem Stahl gefertigt ist, der eine Härte hat, die auf die vorbestimmte Oberflächenhärte erhödiemérte erhödiemétée endemete endeemete endemete endemete endemete endemete en de endeme.Гибкие листы из горячекатаной стали с повышенной глубокой вытяжкой.
Способ термомеханической обработки горячекатаного проката из стали .
Способ защиты горячекатаного изделия из стали .
Полки для европоддонов изготавливаются из цельного горячекатаного стального профиля марки .
Сборная конструкционная балка по п.1, отличающаяся тем, что центральный продольный элемент (76) представляет собой горячекатаный стальной профиль .
Fabrizierter Konstruktionsträger nach Anspruch 1, dadurch gekennzeichnet, daß das zentrale Längsteil (76) ein warmgewalzter Stahlabschnitt ist.2. Способ по п.2, в котором горячекатаную стальную полосу подвергают дробеструйной очистке для очистки ее поверхностей перед цинкованием.
Verfahren gemäß Anspruch 2, bei dem der warmgewalzte Bandstahl zur Reinigung seiner Oberflächen vor dem Verzinken mit Stahlkies gestrahlt wird. Способ производства горячекатаного стального листа и устройство для него.
Узел по любому из предшествующих пунктов, в котором соединитель изготовлен из горячекатаной стали .
Aufbau nach einem der vorhergehenden Ansprüche, bei welchem der Verbinder aus warm gewalztem Stahl besteht.Vallourec & Mannesmann Tubes, входящая в группу Vallourec, является лидером на мировом рынке по производству бесшовных горячекатаных труб из стали для всех областей применения.
Vallourec & Mannesmann Tubes, ein Unternehmen der Vallourec Gruppe, является Weltmarktführer bei nahtlos warmgefertigten Stahlrohren für all Anwendungen.Для производства дисковых ножей Flai используется только горячекатаный прокат из стали .
Der für die Kreissägeblätter FLAI verwendete Stahl ist ausschließlich warmgewalzt .
Способ производства горячекатаного стального листа по п.1, включающий стадию теплоизоляции листов после первой или черновой прокатки.
Verfahren zum Erzeugen eines heißgewalzten Stahlblechs nach Anspruch 1, umfassend den Schritt des thermischen Isolierens der Streifen nach dem ersten Walzen oder Grobwalzen.Способ производства горячекатаного стального листа по п.1, включающий этап вторичного нагрева листа непосредственно перед дальнейшей или окончательной прокаткой.
Verfahren zum Erzeugen eines heißgewalzten Stahlblechs nach Anspruch 1, umfassend den Schritt des sekundären Erwärmens des Streifens unmittelbar vor einem weiteren Walzen oder einem Endwalzen. Способ по любому из пп. 13 — 22, отличающийся тем, что горячекатаную сталь подвергают холодной прокатке и отжигу в выбранном диапазоне температур.
Процесс производства горячекатаного стального листа с высокой прочностью на разрыв для формовки и особенно для глубокой вытяжки
Verfahren zur Herstellung von warmgewalztem, hochfestem Stahlblech zur Umformung und insbesondere zum TiefziehenУзел по любому из пп.1-9, в котором конструктивные элементы (1, 2) представляют собой колонны и балки из горячекатаной стали соответственно.
Aufbau nach einem der Ansprüche 1 bis 9, bei welchem die Strukturellen Bauteile (1, 2) warm gewalzte Stahlsäulen bzw. Stahlträger sind. Более чем вековой опыт и современное управление бизнесом сделали компанию ведущим производителем горячекатаного проката из стали .
Горячекатаный стальной лист по п.1 или 2, в котором упомянутый стальной лист имеет равномерное удлинение по меньшей мере 20%.
Warmgewalztes Stahlblech nach Anspruch 1 или 2, wobei das Stahlblech eine gleichförmige Dehnung von mindestens 20% aufweist.Способ по п.1, в котором стальная полоса включает горячекатаную полосу из стали марки .
Ключевая технология для получения качественной полосы
В настоящее время технология литья почти чистой формы является важной областью исследований в черной металлургии. Среди различных видов процесса литья, близкого к конечной, процесс двухвалкового литья привлек большое внимание исследователей. Двухвалковое литье (TRC) было предметом обширных исследований, направленных не только на развитие технологии, но и на понимание эволюции микроструктуры и производство качественных полос.Основными вопросами, касающимися конструкции и эксплуатации двухвалковых разливочных машин, являются теплопередача металла-формы, система подачи металла и их возможное влияние на формирование твердой оболочки и характеристики полос. Настоящий обзор дает представление о технологическом аспекте, моделировании и вопросах качества в процессе вертикального двухвалкового литья полосы и помогает улучшить конструкцию двухвалковой разливочной машины.
1. Введение
Процесс двухвалкового литья полосы — это технология литья почти чистой формы для производства тонких полос толщиной около 0.От 1 мм до 6,0 мм. Этот процесс позволяет получать тонкие полосы непосредственно из жидкого металла, сочетая разливку и прокатку за один этап. Этот процесс обеспечивает лучший контроль микроструктуры и механических свойств литой полосы. Процесс двухвалкового литья полосы очень прост, но в этом процессе участвует несколько сложных явлений, таких как поток жидкости, теплопередача и затвердевание. Процесс двухвалкового литья полосы динамичный и быстрый, происходит при высокой температуре. Успешный процесс двухвалкового литья полосы привел к исключению процесса горячей прокатки и сделал производство полос, которые трудно подвергать горячей прокатке [1].В зависимости от толщины полосы скорости затвердевания в этом процессе обычно варьируются от 10 2 К / с до 10 4 К / с, что значительно ниже диапазона быстрого затвердевания (от 10 5 К / с до 10 6 К / с). Литье полосы с использованием двухвалковой разливочной машины имеет много преимуществ, таких как низкая стоимость оборудования, низкие эксплуатационные расходы, экономия энергии, экономия места и т. Д. [2]. Однако у него есть и недостатки; один из основных недостатков — низкая производительность [3].
Контроль микроструктуры полосы имеет первостепенное значение в процессе двухвалкового литья полосы, поскольку дальнейшее существенное изменение микроструктуры, от которой зависят свойства полосы, может быть невозможно. Микроструктура полосы зависит от скорости охлаждения и скорости фронта затвердевания в различных местах стренги, что, в свою очередь, зависит от параметров литья, таких как скорость литья, зазор между валками, перегрев жидкого металла, усилие валков, материалы валков и т. Следовательно, необходимо определить конкретную комбинацию параметров конструкции и процесса, которая приведет к желаемой микроструктуре полосы.
2. Процесс разливки полосы и его классификация
Процесс литья почти чистой формы стимулировал увеличение усилий по производству плоских изделий с точки зрения как инвестиционных, так и эксплуатационных затрат, а также большей гибкости и возможности улучшения свойств материала по сравнению с традиционная технология непрерывного литья.С целью достижения хорошего качества поверхности и высокой производительности были разработаны различные типы процессов литья почти чистой формы (NNSC), которые также известны как процесс ленточного литья (SC).
Процесс литья полосы — это категория процесса NNSC, при котором тонкие полосы производятся непосредственно из жидкого металла. Принцип технологии ленточного литья заключается в затвердевании жидкого металла при его контакте с вращающейся формой и получении тонких полос желаемой толщины.Этот процесс был впервые разработан Бессемером [4]. Это стало одной из самых интересных технологий в черной и цветной металлургии за последнее десятилетие. Движущие силы для развития этой технологии следующие: (i) Сокращение ступеней . Сокращение шагов прокатки приводит к экономии труда и энергии по сравнению с обычным способом литья [2, 5]. (Ii) Более низкое потребление энергии . С сокращением производственных этапов потребность в энергии становится меньше.(iii) Снижение инвестиционных затрат . С уменьшением этапов обработки снижается стоимость производства [6].
С учетом вышеупомянутых преимуществ процесса качество продукта, получаемого в процессе разливки полосы, является важным вопросом, который необходимо учитывать. Choo et al. [7] и Ha et al. [8] обнаружили, что основной проблемой, связанной с качеством полосы, было наличие дефектов на поверхности полосы, таких как поперечные трещины, продольные трещины, складки и полости. В течение последних нескольких десятилетий было разработано множество способов разливки полосы, но все они имеют общий факт, что жидкий металл подается в литейное устройство, а затем затвердевает при прямом контакте с движущейся подложкой. Наконец, отливка выходит прямо из литейной машины в виде затвердевшей полосы. Были обнаружены два основных типа установок для разливки полосы: (i) установка для литья под давлением с одним валком. (Ii) установка для литья с двумя валками.
(i) Ролик с одинарным роликом . Одновалковая разливочная машина была впервые разработана в США на основе технологии литья аморфной полосы.Он основан на том принципе, что полосы производятся с использованием вращающейся подложки. Полосы, полученные этим способом, имеют две разные поверхности: поверхность со стороны валка и свободную поверхность. В этом методе скорость отвода тепла и контроля формы полосы недостаточны, что приводит к ухудшению формы и качества полосы.
(ii) Ролик с двумя роликами . Двухвалковая разливочная машина была основана на концепции Бессемера [4], в которой расплавленный металл подается в зазор между валками.У него более высокая теплоотдача, чем у однорядной разливки. В этой разливочной машине можно отливать более толстую полосу, и качество обеих сторон поверхности полосы одинаково.
Эти методы обработки были исследованы различными исследователями. Однако для производства тонких полос двухвалковое литье стало ведущей технологией, которой в настоящее время уделяется большое внимание.
3. Процесс двухвалковой разливки полосы
Процесс двухвалковой разливки полосы основан на концепции, первоначально предложенной английским инженером сэром Бессемером [4].Этот процесс включает подачу расплавленного металла между двумя вращающимися в противоположных направлениях валками, которые действуют как элементы охлаждения и деформации, для затвердевания расплавленного металла в лист. Характеристики процесса, которые делают его таким привлекательным, следующие: (i) Литье без трения . Валок и затвердевший металл движутся примерно с одинаковой скоростью. (Ii) Смазка шлака не требуется, что увеличивает тепловой поток на границе раздела металл-валок и приводит к более высокой скорости затвердевания. (Iii) Комбинация литья и прокатки находится в разовая операция.
Двухвалковые машины для разливки лент могут состоять из рулонов одинакового или неравного размера. Эти валки могут быть расположены горизонтально, вертикально или наклонно [9, 10]. В зависимости от направления разливки двухвалковая разливочная машина делится на два типа, которые показаны на рисунке 1. Это (1) двухвалковая разливочная машина для вертикальной разливки полосы (VTRSC), (2) горизонтальная двухвалковая разливочная машина ( HTRSC).
В вертикальной двухвалковой разливочной машине два валка выровнены по горизонтали и направление разливки находится в вертикальном направлении, тогда как в горизонтальной двухвалковой разливочной машине два валка выровнены вертикально, а направление разливки — в горизонтальном направлении. В таблице 1 показано сравнение горизонтальной двухвалковой разливочной машины и вертикальной двухвалковой разливочной машины [11].
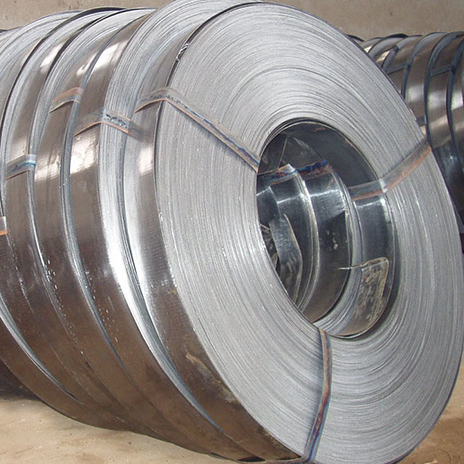
3.1. Принципы вертикальной двухвалковой разливочной машины
Вертикальная двухвалковая разливочная машина состоит из двух валков равного диаметра, вращающихся в противоположных направлениях. Валки обычно изготавливаются из сплавов медь / сталь с высокой теплопроводностью. Их оси вращения расположены в одной горизонтальной плоскости. Основное оборудование, используемое в этом процессе, — это тигель, промежуточный ковш, система подачи расплавленного металла (сопло) и валки.В этом процессе жидкий металл подается из промежуточного ковша через сопло в клиновидную область, образованную двумя валками, вращающимися в противоположных направлениях. Когда перегретый жидкий металл входит в контакт с движущимися валками, затвердевание начинается с отвода тепла от жидкого металла к поверхности валков, и на каждой из поверхностей валков образуется тонкая застывшая оболочка. При непрерывном отводе тепла через движущиеся валки толщина затвердевшей оболочки постепенно увеличивается. Наконец, две затвердевшие оболочки контактируют друг с другом и свариваются вместе в зазоре валков (минимальное расстояние между валками), и материал выходит из литейной машины в виде затвердевшей полосы [12].Более подробный схематический вид вертикальной двухвалковой машины для разливки полосы представлен на рисунке 2.
3.2. Параметры процесса и их влияние на характеристики полосы
Микроструктура и механические свойства затвердевших материалов зависят от характеристик затвердевания. Механизм затвердевания в двухвалковой машине для разливки полосы может управляться различными параметрами процесса. Когда жидкий металл выходит из сопла и касается поверхности валка, обычно начинается отверждение двух валков за счет потери тепла от жидкого металла к поверхности валка, и в результате образование двух оболочек увеличивается по толщине, и они продолжают двигаться. продвигаются через ванну расплава и, наконец, контактируют друг с другом в зазоре между валками (минимальное расстояние между двумя валками) [2].Преобразование из жидкости в твердое включает полутвердую область, то есть мягкую зону. Когда затвердевающий металл достигает достаточной прочности, материал подвергается горячей обработке перед тем, как покинуть зону захвата валка, что позволяет изменять геометрические свойства и микроструктуру полосы. Это обеспечивает лучшее сцепление двух оболочек друг с другом, избегая пустот и пористости в центре полосы. Таким образом, процесс двухвалкового литья полосы объединяет затвердевание и деформацию в один процесс.Явление затвердевания в процессе двухвалковой разливки полосы зависит от следующих параметров процесса двухвалковой разливки полосы: (i) Диаметр валка. (Ii) Материал валка. (Iii) Скорость разливки. (Iv) Зазор между валками. ( v) Система подачи металла. (vi) Коэффициент теплопередачи металлопроката.
3.2.1. Материал рулона
На поверхности валков образуется твердая оболочка, и теплопередача между валками и жидким металлом в основном зависит от материала валка. Для увеличения скорости затвердевания используется рулонный материал с более высокой теплопроводностью, что позволяет повысить скорость охлаждения и снизить температуру поверхности [11, 13].Обычно валки изготавливают из стали или меди. Материал валков оказывает значительное влияние на скорость валков, которая может быть достигнута благодаря тому факту, что материал валка определяет коэффициент теплопередачи на границе раздела между расплавленным металлом и поверхностью валка. Чем выше коэффициент теплопередачи, тем больше тепла может быть извлечено за более короткий период времени, что, в свою очередь, дает возможность разливки с более высокими скоростями [14]. Таким образом, рулонный материал напрямую влияет на производительность литой полосы в процессе двухвалковой разливки полосы.Haga et al. [11] обнаружили, что, используя медный валок в двухвалковой разливочной машине в качестве рулонного материала, двухвалковая разливочная машина смогла разливать со скоростью в 10 раз более высокой и уменьшила толщину полосы вдвое по сравнению с полосой, приготовленной непрерывное литье.
Микроструктура полоски также была лучше.
3.2.2. Диаметр валка
С увеличением диаметра валка длина контакта между валками и жидким металлом увеличивается. Это увеличит скорость теплопередачи и ускорится отверждение.Процесс вертикального двухвалкового литья полосы может достигать скорости охлаждения в диапазоне от 100 ° C / с до 1000 ° C / с [15]. Скорость охлаждения сильно зависит от скорости вращения валков и материала валков.
3.2.3. Скорость литья
Контроль скорости разливки необходим для управления входящим потоком жидкого металла, чтобы обеспечить стабильную операцию разливки в двухвалковой разливочной машине, что повлияет на явления затвердевания. Скорость литья напрямую влияет на положение конечной точки затвердевания и силу разделения валков.Если конечная точка затвердевания смещается ниже точки захвата двухвалковой разливочной машины, это приводит к вздутию, трещинам и уменьшению толщины полосы [16]. Sahoo et al. [17] исследовали влияние скорости разливки на микроструктуру сплава Al-33Cu и обнаружили, что с увеличением скорости разливки микроструктура полосы становится более мелкой и расстояние между пластинами в эвтектической структуре Al-33Cu уменьшается.
3.2.4. Система доставки металла
Система доставки металла напрямую влияет на процесс затвердевания.Система подачи металла состоит из ковша, устройства регулирования расхода и сопел. Для сохранения массы система подачи металла должна подавать количество жидкости, которое будет соответствовать количеству жидкости, выходящей из зазора между валками. Другими словами, подача жидкого металла должна быть такой, чтобы массовые расходы на входе и выходе совпадали. Если система подачи металла не спроектирована должным образом, это влияет на характеристики потока жидкого металла в ванне расплава, что вызывает колебания свободной поверхности [18], чрезмерную рециркуляцию жидкого металла в ванне расплава [19] и т. Д. .Колебания свободной поверхности на поверхности ванны и рециркуляция в ванне расплава будут влиять на явления затвердевания, что приводит к дефектам на поверхности полосы, таким как (i) отклонение толщины, вызванное колебанием уровня ванны [20] и (ii) шероховатость полосы, которая может усугубляться нестабильностью формы мениска и т. д. [12].
3.2.5. Коэффициент теплопередачи между валками
Коэффициент межфазной теплопередачи между валками и жидким металлом играет решающую роль в определении общей производительности процесса TRSC и качества продукта.Коэффициент межфазной теплоотдачи зависит от нескольких параметров, а именно от скорости литья, проводимости материала валка, шероховатости поверхности валков, типа сплава, используемого при отливке, и использования смазки на поверхности валков [ 21, 22]. Желательно, чтобы валки имели высокое значение теплопроводности, чтобы как можно быстрее отводить тепло от расплавленного металла. Поверхность валков должна быть как можно более гладкой, чтобы минимизировать образование воздушного зазора между первоначально затвердевшей полосой и поверхностью валка, что увеличит теплопередачу от жидкого металла к поверхности валка.
Поскольку процесс включает в себя как затвердевание, так и деформацию, контроль процесса по своей сути затруднен. Есть много параметров процесса, которые взаимодействуют друг с другом. Контроль состояния затвердевания путем управления параметрами процесса является фундаментальным требованием для предотвращения или значительного замедления появления макро- и микроструктурных дефектов в материалах полосы.
4. Исследование процесса вертикального двухвалкового литья полосы
Анализ процессов двухвалкового литья полосы требует решения тепловых характеристик и режимов потока, где затвердевание является важной операционной переменной, которая влияет на качество конечной продукции .
4.1. Численное исследование
Первая попытка моделирования теплопередачи и потока жидкости и твердого тела в двухвалковой разливочной машине была сделана Миядзавой и Секели [23]. Эти авторы сообщили о результатах двухмерного несвязанного потока жидкости и теплопередачи для системы из чистого алюминия, сделав ряд упрощающих предположений. В ванне с жидкостью учитывалось ламинарное течение, а в твердой оболочке предполагалось пластическое течение, когда затвердевание происходило до зазора между валками. Модель применялась для литья чистого алюминия, где не учитывалось наличие мягких зон. На основе этих предположений был получен стационарный двумерный профиль скорости и температуры в твердой и жидкой областях. Что касается потока жидкости, в области жидкости был получен рециркулирующий поток, который увеличивался с увеличением расхода. Двумерная численная модель двухвалковой непрерывной разливки, аналогичная моделям Миядзавы и Секели [23], была разработана Сайто и др.[24]. Они изучили характеристики теплопередачи и потока как в твердой, так и в жидкой фазах металла и решали основные уравнения отдельно, используя метод конечных разностей.
Двумерная стационарная математическая модель связанного турбулентного потока жидкости, теплопередачи и затвердевания для вертикальной двухвалковой разливочной машины была разработана Murakami et al. [25]. В их формулировке они рассматривались как естественная, так и вынужденная конвекция наряду с турбулентным потоком. Мягкая зона моделировалась энтальпийно-пористым методом. С помощью этого подхода автор проанализировал влияние входящего потока на формирование твердой оболочки в двухвалковой МНЛЗ. После Мураками и др. [25], математическая модель, основанная на методе конечного объема, была разработана Ли [26] для прогнозирования поля потока и явлений затвердевания в области вращающегося вала во время двухвалковой разливки жидкой стали (SUS304) со скоростью 1,41 м / с. (Рулон 18 об / мин) скорость. В своей модели они предсказали конечную точку затвердевания, которая дает ценную информацию о тепловом напряжении охлаждающих валков и силе разделения валков.Hwang и Kang [27] разработали стационарную двумерную модель теплопередачи и потока жидкости для двухвалкового ленточного литья из нержавеющей стали и сплава Pb-Sn с использованием метода конечных элементов. Было учтено тепловыделение из-за вязкой работы и пластического течения, и было обнаружено, что вязкая работа оказывает незначительное влияние на температурные профили. Результаты их моделирования показали только качественное согласие с экспериментальной работой, разработанной Saitoh et al.
[24]. Следуя тем же принципам исследования, представленного Murakami et al.[25] , Сейедейн и Хасан [28] также применили граничные координаты для моделирования двумерного стационарного турбулентного потока жидкости, теплообмена и затвердевания в клиновидной полости двухвалковой машины для разливки полосы. Они улучшили численную схему, принятую при решении основных уравнений; однако в своей первой модели они не включали явления затвердевания, а в более поздней модели они рассматривали явления затвердевания вместе с не зависящими от температуры свойствами жидкого металла и скоростью разливки 1 м / с (16 об / мин).Чанг и Венг [29] использовали метод конечных элементов для моделирования двухвалковой разливки. Они объединили поток жидкости и теплопередачу в этой модели и включили схему поиска интерфейса для метода локального преобразования, чтобы упростить модель, что помогло легко справиться с поведением различных материалов и неоднородностью свойств материала на разных фазах во время моделирования.
Трехмерная модель потока жидкости, теплопередачи и затвердевания была разработана Гатри и Таваресом [30] для изучения различных систем доставки металла для двухвалкового литья с использованием кода METFLO.Это моделирование было применено к экспериментальной литейной машине, изучаемой в Канаде, с радиусом валка 0,30 м, производящей стальные полосы толщиной от 4 до 7 мм при относительно низкой скорости разливки от 0,06 до 0,2 м / с (от 5 до 7 об / мин. ).
Santos et al. [31] разработали численную модель для моделирования затвердевания и теплопередачи в процессе разливки полосы со скоростью разливки 0,03 м / с (14 об / мин) с использованием метода конечных разностей. Модель помогает в проектировании и управлении двухвалковой экспериментальной системой.Автор ввел коэффициент теплопередачи между жидким металлом и валком вместо граничного условия постоянной температуры (290 K), использованного Saitoh et al. [24]. Двумерный метод конечных элементов (МКЭ) был сформулирован Гуптой и Сахаи [32] для моделирования потока жидкости, теплопередачи и затвердевания в двухвалковой разливке полосы со скоростью разливки 0,77 м / с (50 об / мин). Они использовали вязкость жидкого металла, зависящую от температуры, но остальные свойства материалов не менялись в зависимости от температуры.Они обнаружили, что скорость разливки и коэффициент теплопередачи расплава на валке были основными параметрами, влияющими на толщину полосы, в то время как перегрев расплава оказывал незначительное влияние. Ким и др. Провели численное исследование характеристик потока жидкости и теплопередачи в клиновидной ванне при ленточном литье нержавеющей стали при скорости разливки 0,3 м / с (16 об / мин). [33]. Они изучили влияние зазора валков и различной конструкции сопла на характер течения расплава и распределение температуры.На основе своей модели они разработали фундаментальное понимание конструкции двухвалковой разливочной системы.
Численное исследование турбулентного потока жидкости и затвердевания в двухвалковой машине для литья под давлением было изучено Kim et al. [34]. Авторы изучили влияние различных параметров процесса, таких как тип сопла, толщина зазора валков, перегрев металла и т. Д., На явления затвердевания в клиновидной ванне расплава и оптимизировали параметры процесса на основе моделирования для литья качественных полос.Промышленный процесс двухвалкового литья был проанализирован Cruchaga et al. [35] с помощью МКЭ для изучения связанных потоков жидкости и явлений фазового перехода. В этой работе автор исследовал влияние различных скоростей прокатки, коэффициентов теплопередачи металлопроката на поток, а также характер теплопередачи и затвердевания и обнаружил, что температура полосы на выходе выше при более высокой скорости прокатки и меньшем количестве металла. коэффициент теплоотдачи валка. Интегральная трехмерная модель потока жидкости и теплопередачи во время двухвалковой разливки полосы была разработана Miao et al.[36] с помощью МКЭ, и они изучили влияние различных параметров процесса на поток жидкости и температурное поле. Их модель помогла спроектировать форсунку и контролировать технологические параметры процесса двухвалкового литья. Численное исследование характеристик потока жидкости и теплообмена в бассейне было исследовано Bae et al.
[37] и Cao et al. [38], скорость разливки варьировалась от 0,05 до 0,52 м / с (от 4 до 20 об / мин). Влияние скорости разливки и высоты ванны на структуру потока и затвердевание было изучено для получения полос хорошего качества.На основе своей модели они численно обнаружили, что положение конечной точки затвердевания зависит от параметров процесса, а расположение и размер вихря в области ванны имеют большое влияние на скорость охлаждения во время процесса двухвалкового литья. Zhang et al. [39] разработали модель FEM для моделирования процесса двухвалковой разливки полосы при скорости разливки 0,52 м / с (20 об / мин) и изучили влияние параметров процесса, то есть температуры разливки и высоты уровня жидкости для контроля двухвалковой разливки. процесс литья рулонной полосы и улучшения качества полос.Модель CFD, разработанная Zeng et al. [10] сосредоточены на лучшем понимании характеристик текучести расплава и теплообмена во время быстрого затвердевания расплава Mg во время двухвалкового литья.
Они также подчеркнули влияние скорости разливки и толщины (двухвалкового зазора) на течение расплава и затвердевание. Они использовали постоянные теплофизические свойства, такие как плотность, удельная теплоемкость, скрытая теплота, теплопроводность и вязкость, и измерили температуру литой полосы как на модели, так и на эксперименте и обнаружили, что результаты расчетов для различных скоростей литья хорошо согласуются с экспериментальное определение.Fang et al. В [40] моделировалось температурное поле полосы при двухвалковом способе литья и изучалось изменение температуры при различных радиусах валков и зазоров между валками. Они обнаружили, что при меньшем радиусе валков и большем зазоре между валками точка замерзания близка к выходу. В своей модели они смоделировали модель со скоростью разливки от 0,5 м / с до 1,33 м / с (от 10 до 43 об / мин) и не учли температурную зависимость теплофизических свойств. Трехмерная математическая модель была разработана для моделирования турбулентного потока жидкости, теплопередачи и затвердевания в ванне двухвалковой разливочной машины со скоростью разливки 1 м / с [41].
Подход Дарси-пористости был использован для изучения потока жидкости в кашицеобразной зоне в бассейне. Было изучено влияние коэффициента теплопередачи и постоянной проницаемости на явления течения и затвердевания, и было обнаружено, что теплопередача между валками и затвердевающим металлом оказывает большое влияние на расположение конечной точки затвердевания, а константа проницаемости была ключевой фактор для понимания поведения потока. Однако в модели учитывались постоянные теплофизические свойства.
Zhao et al. В [42] разработана математическая модель двухвалковой разливки магниевого сплава. В своей модели авторы считали, что коэффициент теплопроводности валка и полосы был постоянным, а теплофизические параметры были функцией температуры, но скорость разливки была ограничена от 0,03 м / с до 0,06 м / с (от 2 до 3 об / мин). Ли и др. [43] разработали стационарную модель конечных элементов для изучения влияния параметров обработки, таких как скорость разливки и температура разливки, на положение точки замерзания нержавеющей стали 304 в процессе двухвалковой разливки полосы, и обнаружили, что положение точки замерзания уменьшается с увеличение скорости разливки и температуры разливки. С помощью модели авторы оптимизировали скорость разливки и температуру разливки для получения качественной полосы. Но в своей модели они также учли теплофизические свойства, не зависящие от температуры, и скорость разливки 0,5 м / с (16 об / мин). Модель терможидкостного напряжения была разработана Хададзаде и Уэллсом [44] для процесса TRC из магниевого сплава AZ31 с использованием метода конечных элементов (МКЭ). Эта модель одновременно рассматривает явления переноса с развитием напряжений и деформаций в литой полосе и анализирует влияние расстояния возврата на термомеханическое поведение полосы AZ31 во время TRC.Шоудонг и Цзинчао [45] разработали микромодель для моделирования структуры затвердевания при двухвалковом литье из Al-4,5% Cu. На основе микромодели они изучили влияние коэффициента теплопередачи и температуры разливки на микроструктуру затвердевания полосы и обнаружили, что с увеличением температуры разливки жидкого металла размер зерна увеличивается. Хададзаде и др. [46] разработали модель конечных элементов для процесса двухвалкового литья для прогнозирования потока жидкости, теплопередачи и развития напряжений в литой полосе.
Математическая модель была разработана Sahoo et al. [17, 47] для высокоскоростного процесса двухвалкового литья полосы со скоростью разливки> 1 м / с. Модель также предсказывает влияние параметров обработки, таких как скорость разливки, начальная температура разливки и зазор между валками, на процесс затвердевания и обнаруживает, что при высокой скорости разливки образуется многослойная композитная лента. Численное моделирование было выполнено Sahoo и Ghosh [48] для расчета переходной длины полосы во время начала двухвалковой разливки полосы.Их исследование помогает определить переходную длину полосы, а также рассчитать время, необходимое для достижения установившегося состояния в процессе литья. Ли и др. [49] провели двухмерный анализ методом конечных элементов на горизонтальной двухвалковой отливке алюминиевых полос A7075 и изучили влияние скорости валков и обнаружили, что с увеличением скорости разливки толщина затвердевшей оболочки увеличивается. Парк [50] разработал модель конечных элементов для изучения процесса плакирования сплавов Mg и Al в двухвалковой машине для литья полосы.
В ходе своего исследования они обнаружили, что коэффициент межфазной теплопередачи является основным фактором скорости охлаждения, которая влияет на процессы облицовки.
4.2. Экспериментальные исследования
Было проведено множество экспериментальных работ по изучению развития технологии двухвалкового литья полосы и литья различных сплавов. Устройство для разливки тонких полос было разработано Shibuya et al. [51], который состоит из сдвоенных охлаждающих валков для отливки сплава Si-Fe с концентрацией 4,5 мас.% И толщиной от 0,2 до 1 мм.Двухвалковая разливочная машина бессемеровского типа горячей модели была создана Фидлером и др. [18], чтобы исследовать влияние ключевых компонентов этой разливочной машины на качество продукции и свойства стальных полос прямого литья. Cook et al. [52] разработал процесс двухвалкового литья, чтобы преодолеть некоторые недостатки традиционного процесса, чтобы повысить производительность и разливку широкого диапазона сплавов и избежать проблемы прилипания. Но в этой разработке они добились скорости разливки до 0.25 м / с (12 об / мин). Чтобы лучше понять влияние технологических параметров, таких как геометрия паза сопла, толщина гильзы валка, диаметр, длина валка и т. Д., На форму поперечного сечения полосы, был исследован процесс двухвалкового литья лабораторных размеров. Запускалов и Верещагин [53]. Различные типы двухвалковой разливочной машины, такие как вертикальная двухвалковая разливочная машина [11], двухвалковая разливочная машина с выталкиванием расплава [13] и двухвалковая разливочная машина с выталкиванием расплава [16], были разработаны для производства полос из алюминиевого сплава путем изменения скорости литья от 0.От 33 до 2,5 м / с (от 22 до 160 об / мин). В этих литейных машинах использовались медные валки, а смазка не использовалась для увеличения скорости разливки. Литье с низким перегревом выполняли для улучшения микроструктуры и механических свойств полос по сравнению с традиционными методами. Хага и Сузуки [13] изучали микроструктуру литых полос из алюминиевого сплава А356, полученных непрерывной разливкой с последующей прокаткой и двухвалковой разливкой полосы.
Микроструктура показывает, что на поверхности полосы существовали некоторые дефекты, полученные путем непрерывной разливки по сравнению с двухвалковой разливкой.В обоих процессах микроструктура и свойства меняются в зависимости от параметров процесса. Поскольку параметры процесса, такие как скорость литья, перегрев металла и т. Д., Меняются, скорость охлаждения изменяется, что напрямую влияет на микроструктуру и свойства полосы. Поскольку скорость охлаждения у двухвалковой разливочной машины выше по сравнению с непрерывной разливкой, микроструктура и свойства полосы лучше. Это верно для различных сплавов, таких как сталь, Mg и сплавы Al [54–57]. Wang et al. [58] исследовали влияние технологических параметров двухвалковой разливочной машины на формирование микроструктуры алюминиевых сплавов и обнаружили, что скорость литья и зазор между валками являются двумя основными факторами формирования микроструктуры, поскольку они непосредственно контролируют скорость охлаждения.
Была изготовлена и успешно смонтирована тандемная двухвалковая разливочная машина вертикального типа, которая может лить плакированные полосы. Многослойная плакированная лента из различных сплавов была отлита с использованием тандемной двухвалковой разливочной машины вертикального типа только за один процесс. Граница между полосами была четкой и плоской. Полоски были прочно скреплены, что дает лучшую микроструктуру и механические свойства [59]. Высокопрочные алюминиевые и магниевые сплавы были отлиты на двухвалковой машине несколькими авторами [58, 60, 61].Из их исследования было замечено, что параметры процесса были основными важными факторами для получения качественной полосы. Из микроструктурных наблюдений они обнаружили, что микроструктура полосы имеет более мелкие зерна с лучшими механическими свойствами по сравнению с полосой, полученной путем непрерывного литья.
5. Качество литых полос
Основное преимущество процесса TRSC заключается в сокращении большого количества этапов обработки и производственных затрат. Однако процесс TRSC позволяет получать тонкие полосы там, где требуется хорошее качество поверхности, поскольку для изменения этих параметров доступна лишь ограниченная вторичная обработка [1]. Растрескивание при последующей прокатке и формовке может быть вызвано внутренними и внешними дефектами. Возможность предотвратить образование дефектов или, по крайней мере, отсрочить их появление для повышения производительности, является очевидной промышленной проблемой [62].
При двухвалковой разливке полосы качество полос является важным вопросом. Что касается качества поверхности полос, Hwang et al. [63] обнаружили, что основными дефектами двухвалковых литых полос являются продольные трещины, поперечные трещины и небольшие углубления или складки.
Образование продольных трещин на поверхности полосы, полученной методом двухвалкового литья полосы, изучалось несколькими группами исследователей. В центральной части поверхности полосы возникают продольные трещины.
Это вызвано (i) неравномерной теплопередачей по ширине полосы, (ii) неравномерной деформацией сжатия, возникающей из-за неравномерного охлаждения, (iii) трещиной, которая образуется в результате нарастания сильной локализованной деформации растяжения.
Задержка затвердевания происходит из-за неравномерной теплопередачи по ширине полосы, которая подвергается растягивающей деформации внутри полосы, в то время как деформация сжатия появляется на поверхности.Эта деформация растяжения в поверхностной области с замедленным затвердеванием ответственна за образование трещин. Неравномерная теплопередача произошла из-за (i) колебаний свободной поверхности, (ii) неоднородной температуры внутри ванны расплава и (iii) изменения теплопередачи по ширине валка.
Поперечные трещины возникают случайным образом, особенно на начальном этапе процесса разливки, что вызвано колебаниями свободной поверхности ванны расплава [18, 63]. Поперечные трещины также связаны с горячей прокаткой полосы до того, как она покинет зазор между валками.Это происходит, когда два фронта затвердевания, образующиеся на поверхности валков, встречаются перед зазором валков. Таким образом, адекватное сочетание скорости литья и силы разделения валков для полосы определенной толщины исключает трещины.
При заданном зазоре валков увеличение скорости разливки вызывает быстрое уменьшение силы разделения валков. Это может означать, что затвердевание завершилось в точке зажима валков. Увеличение скорости валков также вызывает смещение вниз конечной точки затвердевания, где встречаются два фронта затвердевания, и обнаруживается, что поперечные трещины устраняются путем регулирования силы разделения валков [18].
Mizoguchi et al. [64] обнаружили, что образование поверхностных складок на двухвалковых литых полосах происходит из-за локально замедленного затвердевания, которое вызвано тепловыми колебаниями на границе раздела валков и металлом и колебаниями свободной поверхности жидкого металла. Колебания свободной поверхности вызывают неравномерную теплопередачу между жидкими металлами к поверхности валка, что вызывает дефекты поверхности в литой полосе. Это предполагает, что эти дефекты могут быть связаны с поведением потока и колебаниями поверхности ванны расплава между двумя валками. Авторы заметили, что колебания свободной поверхности зависят от скорости разливки. Увеличение скорости разливки уменьшает колебания свободной поверхности и уменьшает глубину поверхностных морщин стали SUS304.
Наряду с продольными и поперечными трещинами, другими типами дефектов, связанных с поверхностью полосы, являются вытекание поверхности [63], коробление [3], микросегрегация [65], полосчатая структура [66], краевые трещины и дефекты ряби [67 ] и т.д., которые образуются из-за низкой скорости разливки.
На основании упомянутых выше свидетельств, за образование дефектов ответственны следующие факторы: (i) неравномерная передача тепла от жидкого металла к поверхности валка. (Ii) колебания свободной поверхности в ванне расплава. (Iii) низкая скорость литья.
Чтобы свести к минимуму дефекты в литой полосе, необходимо уменьшить колебания свободной поверхности в ванне расплава и неравномерную теплопередачу, что, в свою очередь, может быть минимизировано путем увеличения скорости разливки. Таким образом, это явное свидетельство важности высокоскоростной вертикальной двухвалковой разливочной машины для производства качественных полос.
6. Результаты моделирования процесса с экспериментальными / производственными данными
Sahoo et al. [17, 47, 68] смоделировали высокоскоростную вертикальную двухвалковую разливочную машину с использованием платформы ANSYS. Они изучили влияние различных параметров процесса на явления затвердевания, а также микроструктуру полосы.
6.1. Влияние скорости разливки
Моделирование выполнено для разливки лент из Al-33Cu толщиной 2 мм в двухвалковой разливочной машине при различных скоростях разливки, то есть 0.От 0239 м / с до 3,98 м / с (3–500 об / мин). На рис. 3 показан профиль затвердевания сплава Al-33Cu при разной скорости разливки. При очень низкой скорости разливки жидкий металл остается в ванне расплава в течение более длительного времени. Таким образом, жидкий металл получает достаточно времени, чтобы передать тепло валку, а точка поцелуя находится перед зазором валков, и полоса прокатывается до того, как она уйдет. При дальнейшем увеличении скорости разливки увеличивается доля жидкого металла в зазоре валков. На более высоких скоростях остается жидкий металл.При более высокой скорости разливки время контакта жидкого металла с валком меньше; следовательно, время затвердевания жидкого металла также меньше, что приводит к уменьшению толщины затвердевшей оболочки в зазоре валков [17].
На рис. 4 показана микроструктура литого сплава Al-33 мас.% Cu при скорости разливки 100–500 об / мин. Микроструктура затвердевшей ленты из Al-33 мас.% Cu не была однородной, и наблюдались две отчетливые зоны. При скорости вращения валка 100 об / мин микроструктура полосы не является полностью пластинчатой.Он имеет как пластинчатую, так и волнистую структуру. При скорости валка 100 об / мин некоторая часть жидкого металла затвердевает в зазоре валков, а некоторая часть находится в жидком состоянии. Жидкий металл, который находится в прямом контакте с поверхностью валка, образует пластинчатую структуру из-за более высокой скорости передачи тепла от жидкого металла к поверхности валка, а остающаяся часть, которая позже охлаждается, образует волнистую структуру. По мере увеличения скорости валков увеличивается доля жидкости в зазоре валков. При увеличении скорости валка жидкий металл получает меньше времени, чтобы оставаться в металлической ванне, и время контакта расплавленного металла с поверхностью валка намного меньше.Ожидается, что большая разница в скорости охлаждения / скорости фронта затвердевания приведет к появлению отчетливой структуры во внешнем слое и внутренней части отлитого Al-33 мас.% Cu. При увеличении скорости разливки от 100 до 500 об / мин ширина пластинчатой структуры уменьшается, а волнистая структура увеличивается. Это эффект разницы скоростей фронта затвердевания [17, 69].
6.2. Влияние перегрева жидкого металла
Численное моделирование проводится для изучения влияния перегрева жидкого металла на затвердевание Al-33 мас.% Cu при высокоскоростной двухвалковой разливке. Моделирование выполнено для разливки лент из Al-33 мас.% Cu толщиной 2 мм в двухвалковой разливочной машине при скорости разливки 0,7979 м / с (100 об / мин). На рис. 5 показан профиль затвердевания жидкого Al-33 мас.% Cu в ванне расплава для различных температур заливки. Из профиля затвердевания видно, что когда температура разливки жидкого металла составляет 831 К, толщина затвердевшей оболочки составляет 0,29 мм, а толщина затвердевшей оболочки равна 0.08 мм при температуре разливки 941 К. Выше 941 К наличие застывшей оболочки не наблюдается [68].
Лента из эвтектического сплава Al-Cu была приготовлена при различных перегревах жидкого расплава 30–70 К (начальная температура жидкого металла от 851 К до 921 К) со скоростью разливки 0,79 м / с. На рис. 6 показана микроструктура литой эвтектической ленты Al-Cu для различных перегревов жидкого расплава. Из микроструктуры видно, что при низком перегреве жидкого расплава микроструктура полосы состоит из темных глобулярных выделений, подобных цветочному узору, внутри матрицы эвтектической структуры.С увеличением перегрева жидкого расплава цветочный узор увеличивается и распространяется по всей поверхности полосы. Это происходит из-за уменьшения скорости охлаждения, что также снижает скорость роста затвердевания. По мере увеличения перегрева жидкого металла температура жидкого металла в ванне расплава будет увеличиваться, если все остальные параметры остаются постоянными. Когда температура жидкого металла увеличивается, для его затвердевания потребуется больше времени. Таким образом, на поверхности полосы можно увидеть множество эвтектических морфологий.Считается, что этот переход в микроструктуре эвтектики связан с уменьшением скорости локального охлаждения и скорости затвердевания [69].
7. Заключение
По сравнению с обычным процессом литья, вертикальное двухвалковое литье полосы является экономичным для производства тонких полос. В этом обзоре кратко описывается процесс вертикального двухвалкового литья полосы и дается представление о влиянии параметров процесса на затвердевание, а также на качество отлитой полосы.Несмотря на то, что в течение последнего десятилетия проводились обширные исследовательские работы по двухвалковой разливке полосы, все еще остаются некоторые важные вопросы, требующие дальнейшего изучения. (I) Из-за взаимодействия нескольких сложных явлений, таких как поток жидкости, теплопередача и затвердевание. Всестороннее моделирование высокоскоростной вертикальной двухвалковой разливки полосы является сложной задачей. (ii) Ожидается, что микроструктура, сформированная на переходной стадии, будет отличаться от микроструктуры в установившемся состоянии.В результате необходимо отбраковывать начальную часть полосы. Таким образом, всестороннее моделирование потока, теплопередачи и затвердевания во время переходного состояния необходимо для оценки длины полосы, которая, таким образом, имеет другую микроструктуру. (Iii) Большая работа была сосредоточена на понимании образования дефектов в полосах во время TRC; однако было сделано не так много попыток устранить внутренние дефекты, в частности сегрегацию по средней линии. Дальнейшая работа необходима в этом направлении, чтобы расширить диапазон сплавов, которые можно лить двумя валками с допустимой степенью сегрегации для конкретного конечного применения.
|