Определение содержания ферритной фазы в наплавленном металле
Структура хромоникелевых сталей, содержащих хром (8 — 25%), никель (8 — 15%), молибден (<4%), а также, в небольших количествах, другие элементы, может быть как из полностью аустенитной стали, так и содержать некоторое количество ферритной фазы, даже при условии, что содержание отдельных элементов находится в пределах химического состава. Контроль ферритной фазы важно осуществлять во время выполнения различных технологических операций, актуальнее всего во время сварки.
Хорошо известно, что присутствие ферритной фазы меняет технологические и эксплуатационные свойства стали и изделий из нее. Например, при отсутствии ферритной фазы, или при малом ее содержании, обнаружена склонность к образованию горячих трещин в сварных швах. При более высоких показателях ферритной фазы наблюдается тенденция к снижению пластичности и ударной вязкости после выдержки при повышенных температурах (600 — 800 ° С) и к снижению коррозионной стойкости в некоторых агрессивных средах.
Присутствие ферритной фазы может ухудшать рабочие свойства стали в области криогенных температур, но положительно влиять на них в условиях коррозии под напряжением.
Особенности определения ферритной фазы
Особенность воздействия ферритной фазы заключается в том, что сравнительно малые изменения ее содержания (в некоторых случаях в пределах нескольких процентов и, даже, долей процента) могут вызвать существенное изменение свойств стали. Требования к содержанию ферритной фазы в данном случае более строгие, чем к химическому составу стали. Так, согласно ГОСТу 2246, содержание ферритной фазы должно быть строго в пределах 2 — 6% в сварочной проволоке марок Св-08Х16Н8М2 и Св-08Х18Н8Г2Б и 3 — 8% в проводе марки Св-04Х19Н11МЗ, но при этом допускается повышение содержания хрома свыше нормы, предусмотренное настоящим стандартом, для достижения необходимого уровня содержания ферритной фазы. Строгие требования предъявляются и к методам контроля, поскольку небольшая неточность при определении содержания ферритной фазы может послужить причиной ложного заключения при оценке качества материалов.
Регламентирование и контроль содержания ферритной фазы в хромоникелевых сталях аустенитного и аустенитно-ферритного классов является составной частью мероприятий по обеспечению качества изделий во многих отраслях промышленности в Украине и за рубежом.
Проведение измерения ферритной фазы лабораторией ООО «Центр промышленной диагностики и контроля»
ООО «Центр промышленной диагностики и контроля» предоставляет услуги по определению содержания ферритной фазы в диапазоне от 0% до 25% в изделиях, изготовленных из нержавеющей хромоникелиевой стали аустенитного и перлитного классов, как на собственной территории, так и на территории заказчика, с использованием многофункционального вихретокового прибора МПП -2м.
: Металлургия: образование, работа, бизнес :: MarkMet.ru
ГОСТ 11878-66
Группа В09
ГОСУДАРСТВЕННЫЙ СТАНДАРТ СОЮЗА ССР
СТАЛЬ АУСТЕНИТНАЯ
Методы определения содержания ферритной фазы в прутках
Austenitic steel bars.
Methods for the determination of the ferrite-phase
ОКСТУ 1909
Дата введения 1967-07-01
ИНФОРМАЦИОННЫЕ ДАННЫЕ
1. РАЗРАБОТАН И ВНЕСЕН Министерством черной металлургии СССР
РАЗРАБОТЧИКИ И.Н. Голиков, И.А. Павперова, Г.К. Семина, Г.П. Казакова, А.В. Горжевская
2. УТВЕРЖДЕН И ВВЕДЕН В ДЕЙСТВИЕ ПОСТАНОВЛЕНИЕМ Комитета стандартов, мер и измерительных приборов при Совете Министров СССР от 15.03.66
3. ВВЕДЕН ВПЕРВЫЕ
4. ССЫЛОЧНЫЕ НОРМАТИВНО-ТЕХНИЧЕСКИЕ ДОКУМЕНТЫ
Обозначение НТД, на который дана ссылка | Номер пункта, подпункта, перечисления, приложения |
ГОСТ 8.518-84 | 4.1а |
ГОСТ 26364-90 | 3.4, 4.1а |
5. Ограничение срока действия снято по решению Межгосударственного Совета по стандартизации, метрологии и сертификации (ИУС 2-93)
6. ПЕРЕИЗДАНИЕ (август 1995 г.) с Изменениями N 1, 2, утвержденными в октябре 1974 г., декабре 1987 г. (ИУС 10-74, 3-88)
Настоящий стандарт распространяется на аустенитные нержавеющие стали марок 17Х18Н9, 12Х18Н9, 12Х18Н9Т, 04Х18Н10Т, 12Х18Н10Т, 08Х18Н10, 04Х18Н10, 02Х18Н10, 06Х18Н11, 12Х18Н12Т, 08Х18Н12Т и 08Х18Н12Б и устанавливает металлографический и магнитный методы определения содержания ферритной фазы (СФФ).
Контролю на содержание СФФ подвергают кованые и катаные прутки диаметром или толщиной от 80 до 270 мм.
По согласованию сторон указанные методы определения СФФ могут быть распространены и на стали аустенитного класса других марок.
Выбор метода и его применение необходимо предусматривать в стандартах и технических условиях на металлопродукцию, устанавливающих технические требования на нее.

(Измененная редакция, Изм. N 1, 2).
1. ОТБОР ОБРАЗЦОВ И ВЫРЕЗКА ШЛИФОВ
1.1. Число образцов для определения содержания СФФ в плавке стали устанавливают стандартами и техническими условиями на продукцию; их должно быть не менее двух.
1.2. Образцы отбирают от любых прутков контролируемой плавки в произвольных местах:
а) при контроле на двух или трех шлифах — от разных прутков;
б) при контроле на большем числе шлифов образцы должны быть отобраны не менее чем от трех прутков.
Место отбора образцов от штанг, соответствующих определенному месту по высоте слитка, может быть установлено по соглашению сторон.
1.3. При металлографическом методе определения СФФ образцы для изготовления шлифов вырезают из круглого или квадратного профиля диаметром или толщиной от 80 до 270 мм от центра до середины радиуса или четверти толщины (см.
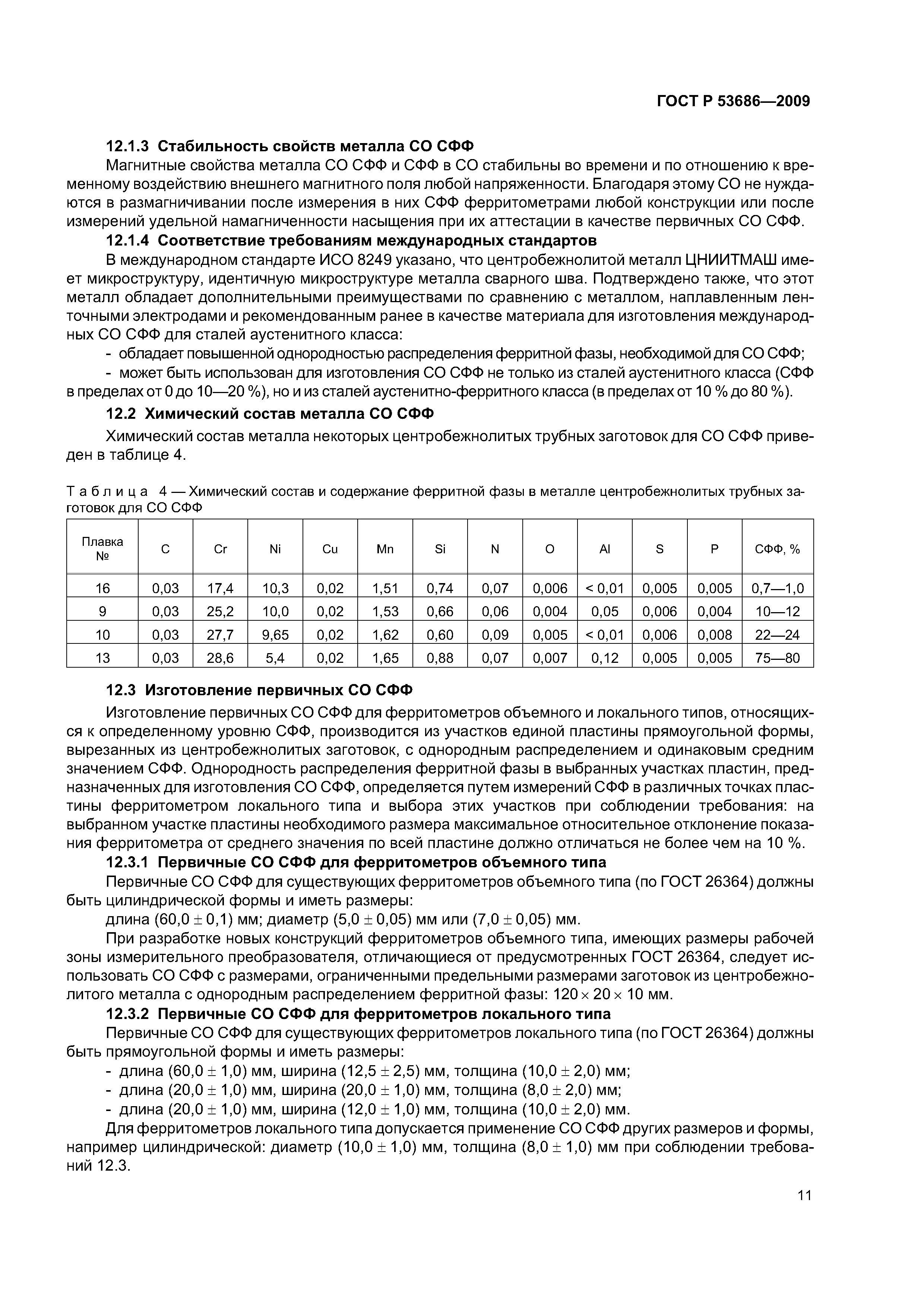
1.4. Длину образца в направлении оси прутка устанавливают не менее 10-12 мм. Припуск на шлифование должен быть больше или равен 0,5 мм (см. чертеж).
1.5. Исключен, Изм. N 2.
1.6. Образцы следует вырезать холодным механическим способом. Допускается автогенная резка при условии, что шлиф будет изготовлен от места реза на расстоянии не менее 25 мм.
1.7. Определение содержания СФФ металлографическим и магнитным методами проводят на образцах в состоянии поставки.
2. ОПРЕДЕЛЕНИЕ СОДЕРЖАНИЯ ФЕРРИТНОЙ ФАЗЫ МЕТАЛЛОГРАФИЧЕСКИМ МЕТОДОМ
2.1. На образцах, вырезанных вдоль волокна, изготовляют шлифы по плоскости, проходящей от центра до середины радиуса прутка (см. чертеж).
2.2. Микрошлиф подвергают электролитическому или химическому травлению. Электролитическое травление осуществляют в 10 %-ном водном растворе щавелевой кислоты при комнатной температуре и плотности тока 0,03-0,08 а/см в течение 20-40 с.
Химическое травление осуществляют в реактиве следующего состава: 20 мл воды, 20 мл концентрированной соляной кислоты и 4 г медного купороса. Травление проводят при комнатной температуре в течение 8-10 с.
Допускается травление в реактивах другого состава, обеспечивающих быстрое и качественное травление (участки не должны быть окисленными, а их границы должны быть тонкими и резкими).
2.3. Содержание СФФ в стали оценивают просмотром всей площади травленого микрошлифа.
2.4. На каждом шлифе при увеличении 280-320 и диаметре поля зрения микроскопа 0,38-0,43 мм определяют место с наибольшим содержанием СФФ, которое визуально оценивают в баллах или в процентах путем сравнения с фотоэталонами прилагаемой шкалы.
Арбитражные определения содержания СФФ проводят по фотоснимку, сделанному при увеличении 280-320, с диаметром фотоотпечатка, соответственно равным 115-130 мм.
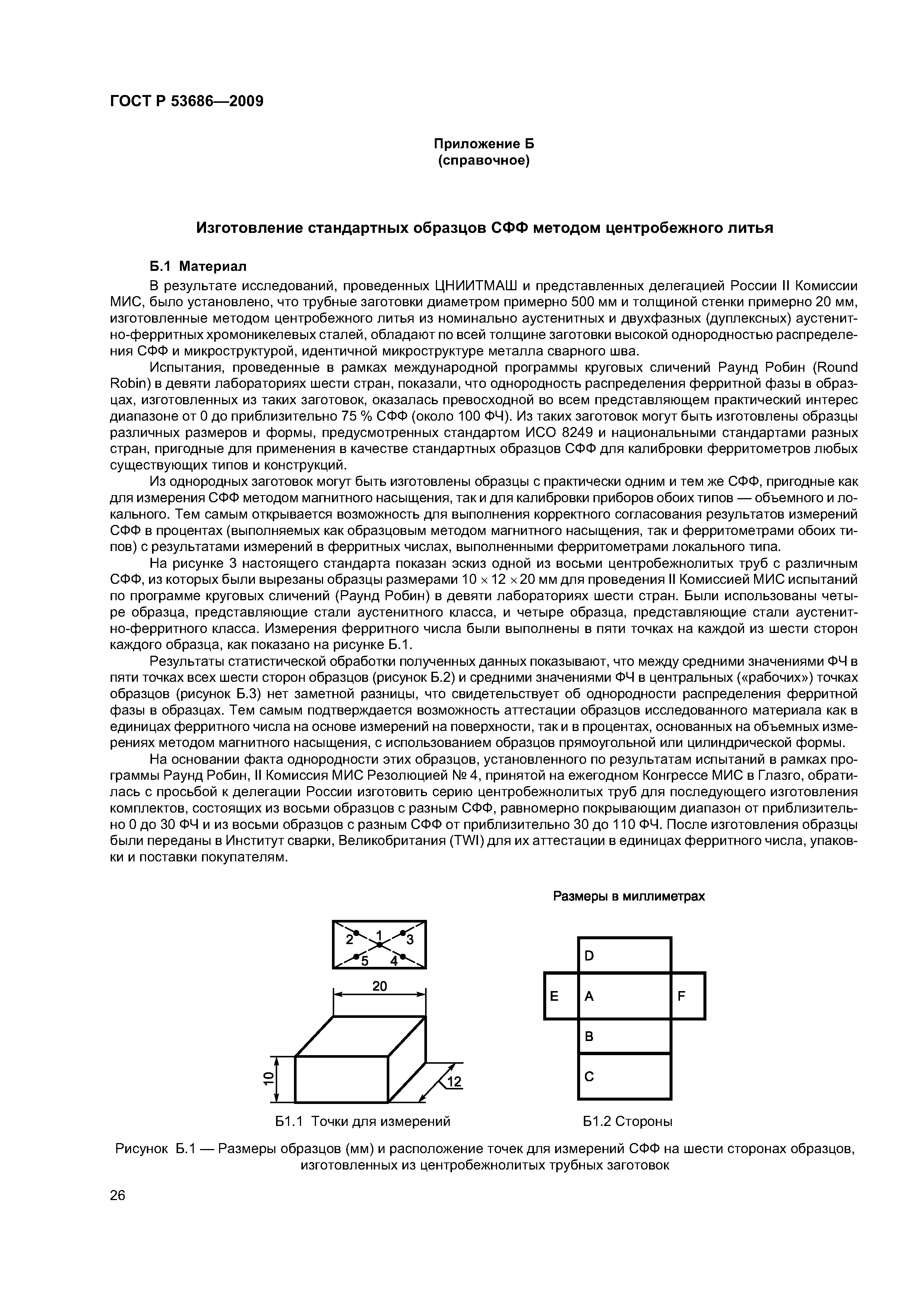
2.5. Прилагаемая к настоящему стандарту шкала для определения содержания СФФ — пятибалльная и имеет дополнительные фотоэталоны в 0,5; 1,5 и 2,5 балла.
Шкала представлена двумя рядами фотоэталонов, различающимися по величине и количеству участков (см. вкладки).
2.4, 2.5 (Измененная редакция, Изм. N 2).
2.6. (Исключен, Изм. N 2).
2.7. Содержание СФФ в плавке оценивают двумя способами:
а) по максимальному баллу или проценту из оценок двух образцов;
б) по среднему баллу или проценту из оценок двух или более образцов.
Способ оценки устанавливается стандартами и техническими условиями на продукцию.
2.8. Норма содержания СФФ в зависимости от назначения стали устанавливается стандартами и техническими условиями на продукцию.
Если результаты испытаний неудовлетворительные, то повторно проводят испытания на образцах, отобранных от других штанг; при оценке плавки по п.
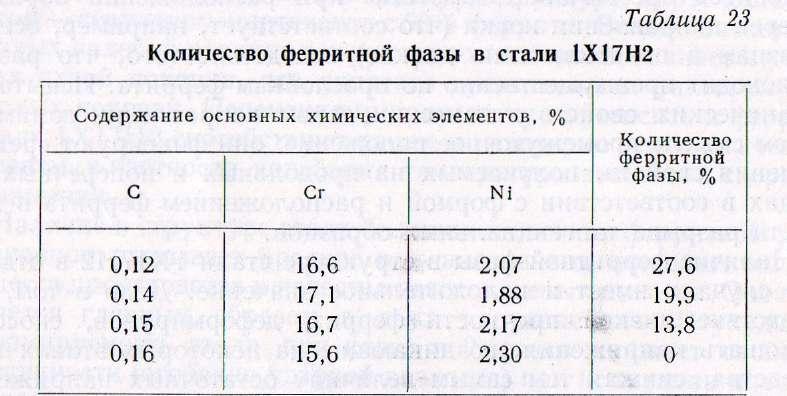
3. ОПРЕДЕЛЕНИЕ СОДЕРЖАНИЯ ФЕРРИТНОЙ ФАЗЫ МАГНИТНЫМ МЕТОДОМ
3.1. Для магнитного метода определения СФФ образцы отрезают от прутков в виде поперечных темплетов высотой не менее 10 мм.
3.2. Определения проводят на шлифованной поверхности макрошлифов, изготовленных на образцах. Допускается определение проводить на макрошлифах, применяемых для контроля макроструктуры до травления.
3.3. Основным магнитным методом высшей точности является метод магнитного насыщения.
3.4. Рабочими средствами измерения являются ферритометры по ГОСТ 26364-90 при измерении содержания ферритной фазы в пределах 0-20 %. При измерении СФФ более 20% допускается применение других приборов при наличии соответствующей градуировки.
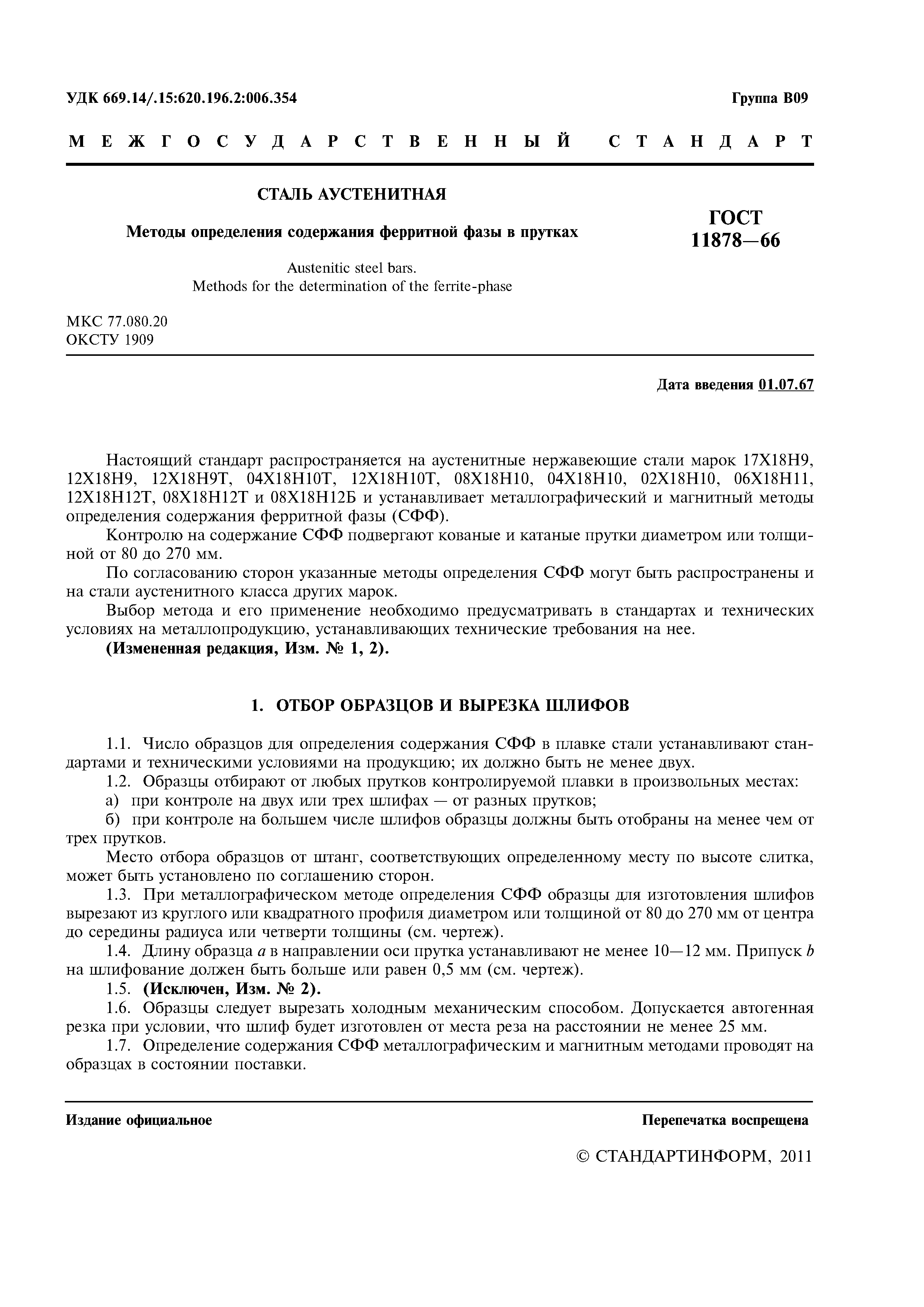
3.5. Градуировка рабочих средств измерения должна осуществляться по стандартным образцам СФФ, аттестованным методом магнитного насыщения или металлографическим методом.
3.6. Для определения СФФ на макрошлифе проводят не менее 40 измерений равномерно расположенных по двум-трем диаметрам (диагоналям). При установлении на макрошлифе зоны с наибольшим СФФ проводят меньшее число измерений, но не менее 20.
3.7. СФФ на макрошлифе определяют средним из трех максимальных показаний прибора в разных местах шлифа с последующим его выражением по градуировочной кривой в баллах или процентах.
3.8. СФФ в плавке оценивают двумя способами:
а) по максимальному показанию из оценок двух образцов;
б) по среднему показанию из оценок двух или более образцов.
Способ оценки устанавливается стандартами или техническими условиями на продукцию.
3.9.
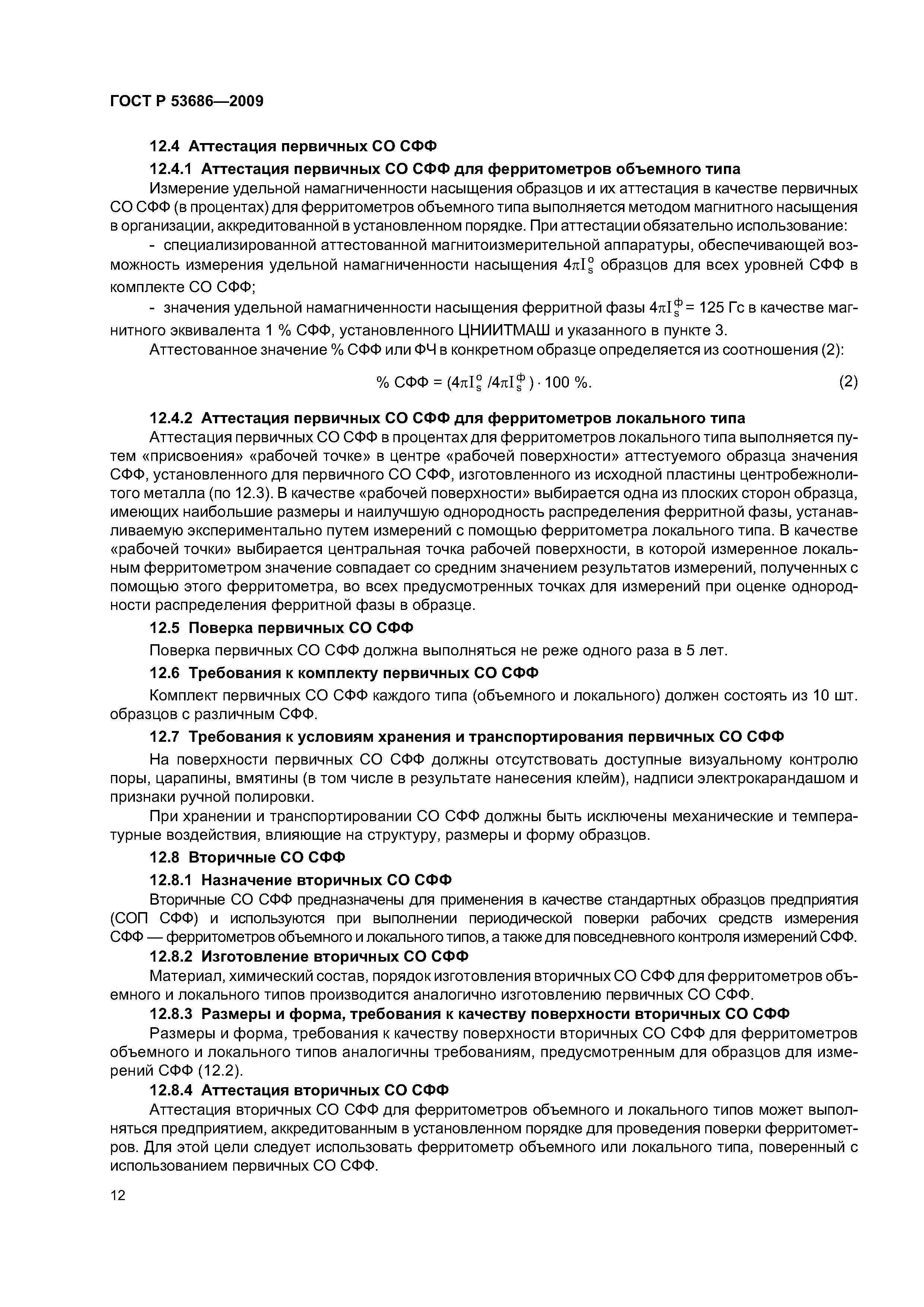
Разд. 3 (Измененная редакция, Изм. N 2)
4. ПОВЕРКА ПРИБОРОВ
4.1. Перед началом работы новый прибор градуируется.
4.1а. Методику первичной и периодических поверок ферритометров (по ГОСТ 26364-90) устанавливают в соответствии с ГОСТ 8.518-84.
(Введен дополнительно, Изм. N 2).
4.2. Градуировку прибора, т.е. получение градуировочной кривой зависимости показаний прибора от содержания СФФ, проводят по эталонным образцам с различным содержанием СФФ. Рекомендуется построение одной градуировочной кривой для прутков размером от 80 до 180 мм и второй — 180 мм и более.
4.3. Эталоны необходимо изготовлять из прутков контролируемой марки стали.
Допускается изготовление эталонов для стали марок 17Х18Н9, 12Х18Н9, 12Х18Н9Т, 04Х18Н10Т, 08Х18Н10, 04Х18Н10, 02Х18Н10, 06Х18Н11, 12Х18Н12Т, 08Х18Н12Т, 08Х18Н12Б, из стали марки 12Х18Н10Т.
(Измененная редакция, Изм. N 1).
4.4. В качестве эталонов используют микрошлифы, вырезанные и изготовленные в соответствии с пп. 1.3 и 2.1. Одну из сторон микрошлифа, расположенную поперек оси прутка, приготовляют как макрошлиф в соответствии с п. 3.2.
4.5. Содержание СФФ в эталонах металлографическим методом определяют путем балльной оценки по методике, изложенной в разд. 2.
4.6. Содержание СФФ в эталонах магнитным методом определяют в соответствии с методикой, изложенной в разд. 3.
4.7. По данным, соответствующим эталонам с различным содержанием СФФ, строят градуировочную кривую прибора в координатах «показание прибора — балл СФФ». Каждые 5-6 точек кривой должны определяться не менее чем 10 результатами, полученными на разных эталонных образцах.
Примечание. Допускается градуировка прибора в координатах «показание прибора — объемное содержание СФФ». В этом случае содержание СФФ в эталонных образцах определяют одним из методов количественной металлографии, например точечным, и выражают в процентах.
4.8. Правильность работы прибора в течение эксплуатации и после ремонта проверяют периодически по двум-трем эталонным образцам с заранее фиксированными показаниями, соответствующими разным участкам градуировочной кривой прибора.
ШКАЛА ДЛЯ ОПРЕДЕЛЕНИЯ
УВЕЛИЧЕНИЕ 300Х
Баллы (проценты)
0,5 (1-2%)
1,0 (2,5-3,5%)
а
б
1,5 (4-5%)
2,0 (5,5-6,5%)
а
б
2,5 (8,5-9,5%)
3 (11,5-12,5%)
а
б
4 (23,5-24,5%)
5 (47,5-48,5%)
а
б
Текст документа сверен по:
официальное издание
М. : ИПК Издательство стандартов, 1995
Определение Ферритной фазы в металлах и сварных соединениях — заказать испытания | Лучшая Цена | Лаборатории SendLAB
Аналитическая лаборатория независимых экспертиз металлов SendLab, один из ведущих представителей на украинском рынке в сфере лабораторно-технических и химических анализов, предлагает проведение анализа на определение содержания ферритной фазы, а также другие испытания которые проводятся на современном европейском оборудовании высококвалифицированными специалистами в кратчайшие сроки.
При нагреве и последующем остывании сталей и чугунов, особенно после сварочных работ, проходят фазу кристаллизации. Ферритная фаза определяет процентное соотношение феррита в исследуемом материале. Допустим, в аустенитной стали содержание феррита варьируется от трёх до десяти. Такая концентрация дает возможность предотвратить образование трещин и предотвратить наступление хрупкости металла при больших перегревах в сварном шве .
Определение ферритной фазы в сварном шве – особенности
Известный факт, что наличие ферритной фазы меняет природные и свойства эксплуатации стали и стальных изделий. Когда ферритная фаза отсутствует, либо ее содержание незначительно, появляется тенденция к образованию трещин в сварном шве.
Когда же показатели ферритной фазы выше, наблюдается стремление к понижению пластичности, а также и ударной вязкости после выдержки при высоких температурах. Так же это приводит к понижению коррозионной сопротивления в определенных агрессивных средах.
Контроль ферритной фазы в металлах и сварных соединениях
Лаборатория SendLab производит испытания для определения ферритной фазы металлографическим методом в:
- в отливках металла;
- в трубах;
- в металле шва;
- в листовом прокате;
- в наплавленном металле
- в сталях и сплавах.
Наличие ферритной фазы может ослаблять рабочие характеристики стали в спектре криогенных температур, однако благоприятно воздействовать на них в условиях коррозионного напряжения.
Наша лаборатория SendLab предоставляет услуги по определению содержания ферритной фазы от 0% до 25% в прокате, изготовленном из нержавеющей хромоникелевой стали аустенитного и перлитного классов, как на собственной территории, так и на территории заказчика. В работе наши специалисты используют многофункциональный вихретоковый прибор (прибор для определения ферритной фазы).
Регламентируются такие исследования согласно ГОСТ 11878-66.
Как заказать определение содержания ферритной фазы в Украине
Аналитическая лаборатория независимых экспресс тестов и экспертиз SendLab располагается в г. Днепр (Днепропетровск). Наша сфера деятельности охватывает всю территорию Украины, и непосредственно крупнейшие центрами промышленности такие как:
- Киев;
- Харьков;
- Кривой Рог;
- Львов;
- Одесса;
- Запорожье.
Образцы для определения ферритной фазы, можно доставить нам любой удобной службой экспедиции, предварительно согласовав отправку с нашими специалистами.
Выдача результатов происходит через 3-5 дней после полной предоплаты услуг лаборатории SendLab, в любой удобной форме:
- по телефону,
- вайберу,
- электронной почте.
В случае надобности, по просьбе клиентов, оформляется протокол проведенных исследований установленного образца.
Предоплата производится также наиболее подходящим для клиента способом: по наличному, безналичному расчету, перечислением на банковскую карту.
Обращаясь в лабораторию SendLab https://www.sendlab.com.ua/, вы всегда можете рассчитывать на объективный и точный результат по интересующим экспертизам и анализам.
Определение содержания ферритной фазы
На основе данных диаграммы Железо-углерод, феррит является твердым раствором углерода в железе. Растворимость углерода в феррите составляет 0,025%. Это максимальный показатель при температуре 727 градусов по Цельсию. При температуре же 20 градусов растворимость в железе равна 0,006%. Среди главных свойств феррита выделяют:
- сильные ферромагнитные характеристики;
- теплопроводность и высокие показатели пластичности;
- хорошие показатели проводимости электротока.
При этом феррит не может похвастаться высокой твердостью и прочностью. Это относится к главным его недостаткам. Содержание ферритной фазы контролируется строго, поскольку феррит — составляющая микроструктуры материала, которая может оказывать как негативное, так и благотворное влияние. В первом случае речь идет об охрупчивании сварочного материала при высоких температурах, а также снижении ударной вязкости при отрицательных температурах. Что касается плюсов, наличие этого элемента способно предотвращать появление горячих трещин.
Измерение ферритной фазы в лаборатории
Компания «Феникс» в рамках своей лаборатории осуществляет измерение ферритной фазы в соответствии с ГОСТ 11878, для сварных швов – ГОСТ Р 53686. С учетом этих стандартов происходит проверка таких показателей как содержание ферритной фазы, его процент и ферритное число.
Используются два метода определения ферритной фазы. Среди них магнитный и металлографический. В первом случае в качестве образца анализируются поперечные темплеты с высотой не менее 10 мм для изготовления шлифа. Для определения ферритной базы в этом случае используется прибор – ферритометр. Металлографический метод подразумевает изготовление шлифа и его травление в реактиве.
Содержание ферритной фазы указывается в баллах или процентах при увеличении 280-330х на всей поверхности микрошлифа. Для сравнения используются эталоны, соответствующие ГОСТу.
Определение содержания ферритной фазы в аустенитных и аустенитно-ферритных сталях указывает на ее объёмную долю. Подобные испытания в частности важны для сталей, ориентированных в дальнейшем на применение сварки.
Ферритная фаза — Большая Энциклопедия Нефти и Газа, статья, страница 4
Ферритная фаза
Cтраница 4
При измерении содержания ферритной фазы в сварном шве плакирующего слоя на показания прибора может оказывать влияние магнитный слой основания биметалла. Поэтому содержание ферритной фазы следует определять прибором, предназначенным для поверхностного, а не объемного измерения содержания магнитной фазы в изделии. Например, ферритометром ФА-1, но его можно применять только в том случае, когда толщина плакирующего слоя превышает 1 5 мм.
[47]
С увеличением содержания ферритной фазы выше определенной нормы резко снижается пластичность сталей при механической обработке, образуются трещины и другие нарушения сплошности. При повышенном содержании ферритной фазы в сварных соединениях резко уменьшается их прочность. [48]
С увеличением содержания ферритной фазы выше определенной нормы резко снижается пластичность сталей при механической обработке, образуются трещины и другие нарушения сплошности. При повышенном содержании ферритной фазы в сварных соединениях резко уменьшается их прочность. Для определения содержания ферритной фазы в ряде случаев могут быть использованы приборы, действие которых основано на измерении магнитной проницаемости. Показания ферритометров в существенной мере зависят от магнитных характеристик материала контролируемого объекта, поэтому для градуировки необходимо применять специальные рабочие образцы ( эталоны) с известным содержанием ферритной фазы. По принципам работы ферритометры близки к магнитным толщиномерам, хотя в их работе используются другие магнитные характеристики материала. Портативный магнитный ферритометр — толщиномер магнитный ФТМ-2 ( разработчик прибора — филиал ФНПЦ Прибор), изображенный на рисунке 3.4.9, предназначен для измерения толвганы покрытий и относительного содержания ферритной фазы ( а-фазы) в сварных швах.
[49]
С увеличением содержания ферритной фазы выше определенной нормы резко снижается пластичность сталей при механической обработке, образуются трещины и другие нарушения сплошности. При повышенном содержании ферритной фазы в сварных соединениях резко уменьшается их прочность. [50]
С увеличением содержания ферритной фазы выше определенной нормы резко стекается пластичность сталей при механической обработке, образуются трещины и другие нарушения сплошности. При повышенном содержании ферритной фазы в сварных соединениях резко уменьшается их прочность. Дня определения содержания ферритной фазы в ряде случаев могут быть использованы приборы, действие которых основано на измерении магнитной проницаемости. Показания ферритометров в существенной мере зависят от магнитных характеристик материала контролируемого объекта, поэтому для градуировки необходимо применять специальные рабочие образцы ( эталоны) с известным содержанием ферритной фазы. По принципам работы ферритометры близки к магнитным толщиномерам, хотя в их работе используются другие магнитные характеристики материала. Портативный магнитный ферритометр — толщиномер магнитный ФТМ-2 ( разработчик прибора — филиал ФНПЦ Прибор), изображенный на рисунке 3.4.9, предназначен для измерения толщины покрытий и относительного содержания ферритной фазы ( а-фазы) в сварных швах.
[51]
Вследствие того, что ферритная фаза при высоких температурах обладает меньшей прочностью, при ковке и горячей прокатке следует уменьшать степень обжатия; двухфазные стали при обычных степенях деформации дают трещины и разваливаются.
[52]
Установлено [518], что ферритная фаза в аустенито-ферритных сталях обогащена хромом, что также способствует меньшей степени обеднения пограничных слоев твердого раствора хромом при образовании карбидов хрома. [53]
В течение дальнейшего обезуглероживания ферритная фаза всегда остается непосредственно следующей за образующимся двухфазным слоем. Это длится до тех пор, пока толщина ферритного слоя не достигнет величины, при которой быстрое удаление углерода с помощью диффузии станет затруднительным. [54]
При непрерывном охлаждении количество ферритной фазы, как правило, не достигает равновесного значения. При TiAr происходит перлитное ( или другое) превращение оставшейся части аустенита. При этом образуется перлит с С0 8 %, так называемый квазиэвтектоид. Такой перлит характеризуется увеличенной долей ферритной составляющей.
[56]
Ферритометрия применяется для контроля ферритной фазы, повышенное содержание которой снижает трещиностойкость сталей и особенно сварных соединений. Содержание этой фазы определяет магнитную проницаемость материала, поэтому для ее определения измеряют магнитное сопротивление. Измерительным элементом ферритометра является одно — или двухполюсный феррозондовый магнитный преобразователь, содержащий возбуждающую и измерительную катушки. Магнитный поток, создаваемый возбуждающей катушкой феррозонда, зависит от магнитного сопротивления участка объекта контроля, определяемого содержанием ферритной фазы. Поэтому ее величину оценивают по ЭДС, наведенной при этом в измерительной катушке. Градуировка ферритометров производится по эталонным образцам с известным содержанием ферритной фазы. [57]
Необходимость контроля и содержание ферритной фазы в наплавленном металле определяется техническим проектом. Содержание феррит-ной фазы измеряют альфа-фазометрами или металлографическим методом по ГОСТ 11878 — 66 на образцах, вырезанных из контрольных проб.
[58]
Эти электроды благодаря получению ферритной фазы в сварном шве обеспечивают отсутствие трещин при сварке не только сталей типа 18 — 8, но и при сварке этих сталей с углеродистой сталью. Швы, сваренные этими электродами, обладают высокими механическими свойствами, высокой прочностью и пластичностью, хорошей стойкостью против общей и межкри-сталлитной коррозии е только непосредственно после сварки, но и после воздействия так называемых критических температур. [59]
Страницы: 1 2 3 4 5
О СООТВЕТСТВИИ РЕЗУЛЬТАТОВ ИЗМЕРЕНИЙ ПРОЦЕНТНОГО СОДЕРЖАНИЯ ФЕРРИТА И ФЕРРИТНОГО ЧИСЛА В АУСТЕНИТНЫХ СТАЛЯХ ПРИ ИЗМЕРЕНИЯХ РОССИЙСКИМИ ФЕРРИТОМЕТРАМИ | Опубликовать статью ВАК, elibrary (НЭБ)
О СООТВЕТСТВИИ РЕЗУЛЬТАТОВ ИЗМЕРЕНИЙ ПРОЦЕНТНОГО СОДЕРЖАНИЯ ФЕРРИТА И ФЕРРИТНОГО ЧИСЛА В АУСТЕНИТНЫХ СТАЛЯХ ПРИ ИЗМЕРЕНИЯХ РОССИЙСКИМИ ФЕРРИТОМЕТРАМИ
Научная статья
Ригмант М. Б.1*, Корх М.К.2
1 ORCID: 0000-0001-8763-8784;
2 ORCID: 0000-0002-8016-5694;
1, 2 Институт физики металлов имени М.Н. Михеева Уральского отделения Российской академии наук, Екатеринбург, Россия
* Корреспондирующий автор (rigmant[at]imp.uran.ru)
Аннотация
Проведено сравнение ферритного числа (FN) стандартных образцов аустенитных сталей, изготовленных методом наплавки фирмой «Инспектор Гейдж» (Великобритания) с измерениями процентного содержания фазы феррита (СФФ) с помощью российских ферритометров ФМ-3 (ИФМ УрО РАН) и МК-1.2Ф (АО ИНТРОТЕСТ). Показано, что между значениями FN и СФФ во всем измеряемом диапазоне сохраняется линейная зависимость FN » 1,8 × СФФ с относительной погрешностью не более 12 % для всех измеренных образцов с различным содержанием ферритного числа. Такая однозначная связь FN и (СФФ) позволяет использовать российские ферритометры для контроля аустенитно-ферритных сталей изготовленных за рубежом, так и наоборот – калибровать иностранные приборы в единицах СФФ при контроле сталей изготовленных в России.
Ключевые слова: феррит, аустенит, фазовый состав, неразрушающий контроль.
ON CONFORMITY OF THE MEASUREMENT RESULTS OF PERCENTAGE OF FERRITE AND FERRITIC NUMBER IN AUSTENITIC STEELS AT MEASUREMENTS BY RUSSIAN FERRITOMETERS
Research article
Rigmant M.B.1, *, Korkh M.K.2
1 ORCID: 0000-0001-8763-8784;
2 ORCID: 0000-0002-8016-5694;
1, 2 Federal State Budgetary Institution of Science M.N. Mikheev Institute of Metal Physics Ural branch of the Russian Academy of Sciences, Yekaterinburg, Russia
* Corresponding author (rigmant[at]imp.uran.ru)
Abstract
The article contains the comparison of the ferritic number (FN) of standard samples of austenitic steels produced by the overlaying method by Inspector Gage (United Kingdom) with the measurements of the percentage of ferrite phase (PFP) with the help of Russian FM-3 ferritometers FM-3 (IPM UB RAS) and MK-1. 2F (INTROTEST JSC). It is shown that linear dependence of FN » 1.8PFP with a relative error of no more than 12% for all measured samples with different contents of ferritic number remains between the values of FN and PFP in the entire measured range. Such an unambiguous connection between FN and (PFP) allows the use of Russian ferritometers to monitor austenitic-ferritic steels produced abroad, and vice versa, to calibrate foreign instruments in PFP units when monitoring steels manufactured in Russia.
Keywords: ferrite, austenite, phase composition, non-destructive testing.
Магнитная ферритометрия в России основывается на представлении о ферритной фазе (α-фазе) в аустенитных и аустенитно-ферритных сталях, как мелкодисперсном сложнолегированном ферромагнетике, содержание и распределение которого в парамагнитной матрице изучается с помощью соответствующих методик и аппаратуры. Российские приборы ферритометры измеряют α-фазу двумя методами: объемным и локальным, которые взаимно дополняют друг друга [1]. При использовании объемного метода образцы стандартного размера, вырезанные из зоны контроля, намагничиваются до состояния технического насыщения. При локальном магнитном контроле материал намагничивается лишь на небольшом участке изделия. Локальный метод магнитной ферритометрии широко используется в неразрушающем контроле благодаря его оперативности, высокой производительности и возможности определения содержания ферритной фазы непосредственно в готовых изделиях.
Метод магнитного насыщения предусмотрен Государственными стандартами России [2] для аттестации стандартных образцов содержания феррита в аустенитных сталях. В России используется понятие «процент феррита», определяемый как одна сотая доля величины удельной намагниченности насыщения ферритной фазы в исследуемой стали. За рубежом контроль содержания ферритной фазы (СФФ) возник как инженерная проблема и развивался на базе методов и средств магнитной толщинометрии [14], [15]. Данные методы, основанные на измерении силы отрыва постоянного магнита от поверхности образца, также могут давать воспроизводимые результаты. При таком контроле используется понятие ферритное число («ferrite number» или FN). Цель данной работы – это установление связи между содержанием ферритной фазы и значением ферритного числа. Данное исследование проводится как на образцах СФФ, так и на образцах FN.
В Институте физики металлов УрО РАН были проведены прямые измерения СФФ образцов с различным ферритным числом с помощью российских ферритометров – МК-1.2 Ф (ОАО «Интротест») и ФХ-3 ИФМ (ИФМ УрО РАН). Образцы были изготовлены фирмой «Инспектор Гейдж» (Великобритания) методом наплавки аустенитной проволоки на ферромагнитную основу [1], [14], [15].
Образцы для измерений были предоставлены производственным объединением ООО «Ижорские заводы». Российские ферритометры для локальных измерений калибровались на Государственных стандартных образцах (комплект ГСО) в % ферритной фазы. Комплект ГСО разработан в Уральском центре стандартизации и метрологии Госстандарта (ныне «Уралтест», г. Екатеринбург) совместно с ЦНИИТМаш (г. Москва). Образцы изготовлены методом центробежного литья, который позволяет получить большой объем стали с однородным фазовым составом [1].
Содержание ферритной фазы в российских образцах определялось несколькими методами, в том числе – методом магнитного насыщения и методом оптической микроскопии.
Метод магнитного насыщения является наиболее информативным, так как при объемном контроле целиком намагничиваются образцы «свидетели», а при локальном контроле намагничивается достаточно большой участок изделия. Результат такого намагничивания и связан с содержанием ферритной фазы. В методе магнитного насыщения за процентное содержание феррита (%F) в аустенитной стали принимается значение
(1)
где – экспериментально определенная намагниченность насыщения исследуемой стали, содержащей некоторое количество феррита,
– намагниченность насыщения стали, содержащей максимально возможное (100%) количество феррита при данном химическом составе.
В работе [11] был развит эмпирический подход, предложенный ранее в [12], [13], который показал, что значение можно с высокой точностью получить, зная химический состав исследуемой стали, из формулы
(2)
где в скобках указано процентное содержание химических элементов в ферритной фазе исследуемой стали. Формула (2) для расчета достаточно понятна с физической точки зрения. Величина 1720 кА/м это величина намагниченности насыщения чистого железа. Наличие легирующих элементов в исследуемой стали понижает это значение.
На рис.1 для примера представлены результаты оптической микроскопии двух образцов из набора СФФ с содержанием ферритной фазы а) 5,3%, б) 10,3% при 500 кратном увеличении.
Рис.1 – Измерение фазы феррита при 500 кратном увеличении – а) 5,3%, б) 10,3%
Сравнительные измерения ферритометрами в процентах ферритной фазы на комплекте образцов ферритного числа, аттестованы Международным институтом сварки (г. Кембридж, Великобритания) представлены на рис. 2.
Рис. 2 – Связь значений ферритного числа с содержанием ферритной фазы. Измерения проведены ферритометрами МК-1.2 Ф и ФМ-3 ИФМ
Результаты сравнительных измерений показали, что связь ферритного числа – (FN) и процентного содержания α-фазы является близкой к линейной. Ферритное число можно определить, как FN≈1,80 × СФФ. Относительная погрешность измерений не превышает 12%. Это экспериментальное значение хорошо согласуется с данными Международного института сварки (Кембридж, Великобритания) которое определяется сложным расчетно-измерительным путем.
Однозначная линейная связь ферритного числа и процентного содержания феррита может быть объяснена тем, что в случае измерения FN, и в случае измерения СФФ, рассматривается магнитная связь между намагничивающим элементом измерительного преобразователя (датчика), создающего большое магнитное поле, и контролируемым аустенитно-ферритным материалом. Как в случае измерения FN, так и в случае определения СФФ, контролируемый материал намагничивается до магнитных полей, при которых происходит локальное намагничивание до состояния близкое к техническому насыщению. Для всех, рассматриваемых в данной статье приборов контроля, определяется характеристика, связанная с взаимодействием намагниченного участка и магнитоизмерительным преобразователем. При измерении ферритного числа определяется сила отрыва локального постоянного магнита от намагниченного участка. При измерении прибором МК-1.2Ф измеряется индукционный отклик контролируемого участка при импульсном намагничивании с помощью магнитомягкого сердечника.
Контроль СФФ прибором ФХ-3 ИФМ осуществляется следующим образом (см. рис.3): преобразователем Холла (2) измеряется магнитное поле рассеяния от контролируемого изделия (3) локально намагниченного сильным постоянным магнитом (1) из сплава редкоземельного элемента. Цифрой (4) на рис.3 обозначена намагниченная область (зона контроля) в контролируемом материале. Напряженность магнитных полей рассеяния в зоне контроля прямо пропорциональна содержанию ферромагнитных включений в данной зоне.
Рис. 3 – Устройство и принцип работы измерительного преобразователя прибора «Ферритометр ФХ-3 ИФМ», где: 1 – постоянный магнит; 2 – датчик Холла; 3 – контролируемый объект; 4 – «отражение» магнита в материале стали
Заключение
Измерения, выполненные в ИФМ УрО РАН, показали возможность использования российских ферритометров как для контроля фазы феррита, так и для определения ферритного числа на изделиях из аустенитных и аустенитно-ферритных сталей. Применение российских приборов вместе со стандартными образцами СФФ позволяет проводить измерения с большой локальностью. Зарубежные приборы для решения аналогичных задач часто используют для калибровки по измерению FN образцы имитаторы. В этих образцах сила отрыва калиброванного магнита регулируется немагнитным покрытием на ферромагнитной основе. Немагнитное покрытие, при этом, может совсем не содержать аустенитной фазы, что ограничивает использование образцов имитаторов, например, при замене одного магнитоизмерительного преобразователя на другой, или при использовании имитаторов для различных приборов по измерению значения ферритного числа.
Финансирование Работа выполнена в рамках государственного задания ФАНО России (тема «Диагностика», № АААА-А18-118020690196-3). | Funding The work was performed within the framework of the state assignment of the Federal Agency for Scientific Organizations of Russia (“Diagnostics,” No. |
Конфликт интересов Не указан. | Conflict of Interest None declared. |
Список литературы / References
- Международная инженерная энциклопедия. Неразрушающие методы контроля. Спецификатор различий в национальных стандартах различных стран. Под ред. проф. В. Я. Кершенбаума: – М.: Центр «Наука и техника». 1995. т. 3. С. 68-128.
- ГОСТ Р 53686-2009 Сварка. Определение содержания ферритной фазы в металле сварного шва аустенитных и двухфазных аустенитно-ферритных хромоникелевых коррозионностойких сталей. – М.: Стандартинформ, 2011. – 25 c.
- Курдюмов В. Г. Превращения в железе и стали. / В. Г. Курдюмов, Л. М. Утевский, Р. И. Энтин – М.: Наука. 236 с.
- Химченко Н. В. Неразрушающий контроль в химическом и нефтяном машиностроении. / Н. В.Химченко, В. А. Бобров – М.: Машиностроение. 356 c.
- Ригмант М.
Б. Прибор для контроля изменений магнитного состояния листов слабомагнитных аустенитных сталей – ферритометр Ф-01./ М. Б. Ригмант, М. А. Веденеев, В. С. Пономарев, и др. Прибор для контроля изменений магнитного состояния листов слабомагнитных аустенитных сталей – ферритометр Ф-01. // Дефектоскопия. – 1994. – №3. – С. 3-9.
- Меринов П. Е. Определение мартенсита деформации в сталях аустенитного класса магнитным методом / П. Е. Меринов, А. Г. Мазепа. // Заводская лаборатория. – 1997. – №3. – С. 47-49.
- Deryagin A. I. Formation of Nanosized Ferromagnetic Phases during Plastic Deformation and Subsequent Annealing of Stable Austenitic Steels / A. I. Deryagin, V. A. Zavalishin, V. V. Sagaradze and others // Russian journal of nondestructive testing. – 2007– V.43 – p. 427 (9 pp.)
- Rigmant M. B. Instruments for Magnetic Phase Analysis of Articles Made of Austenitic Corrosion-Resistant Steels / M. B. Rigmant, A. P. Nichipuruk, B. A. Khudyakov and others // Russian journal of nondestructive testing.
– 2005. – V. 41. – P. 701–709.
- Rigmant M. B. The possibility of separate measurements of the amounts of ferrite and deformation martensite in three-phase austenitic-class steels using the magnetic method / M. B. Rigmant, A. P. Nichipuruk, M. K. Korkh // Russian journal of nondestructive testing. – – V. 48. – P. 511–521.
- Korkh M. K. Determination of the phase composition of three-phase chromium-nickel steels from their magnetic properties / M. K. Korkh, M. B. Rigmant , D. I. Davydov, and others// Russian journal of nondestructive testing. – 2015. – V. 51. – P. 727–737.
- Merinov P. The magnetic testing of the ferrite content of austenitic stainless steel weld metal / P. Merinov , S. Entin, B. Beketov and others // NDT International. – 1978. – V. 11. – p. 9-12.
- Elmer J. Measuring determination the residual ferrite content of rapidly solidified stainless steel alloy/ J. Elmer, T. Eagar // Welding Research Saplement. – 1990. – V. 4. – p. 141-150.
- Stalmasek E.
Measurements of ferrite content in austenitic stainless steel weld metal giving internationally reproducible results / E. Stalmasek // Welding Research Council Bulletin. – 1986. – V.318. – p. 22 – 97.
- American National Standard ANSI/AWS A4.2-86 Standard procedure for calibrating magnetic instruments to measure the delta-ferrite content of austenitic stainless steel weld metal.: American welding society inc., 1998. – 27 p.
- International Standard ISO 8249. Welding — Determination of Ferrite Number (FN) in austenitic and duplex ferritic-austenitic Cr-Ni stainless steel weld metals.: ISO copyright office, Switzerland, 2000. – 11 p.
Список литературы на английском языке / ReferencesinEnglish
- Mezhdunarodnaja inzhenernajaj enciklopedija. Nerazrushajushhie metody kontrolja. Specifikator razlichij v nacional’nyh standartah razlichnyh stran. Pod red. prof. V.Ja. Kershenbauma [International Engineering Encyclopedia. Non-destructive control methods.
The specifier of differences in national standards of different countries. Ed. prof. V. Ya. Kershenbaum]: – M.: Centr «Naukaitehnika». 1995. Vol. 3. p. 68-128. [in Russian]
- GOST R 53686-2009 Svarka. Opredelenie soderzhanija ferritnoj fazy v metalle svarnogo shva austenitnyh i dvuhfaznyh austenitno-ferritnyh hromonikelevyh korrozionnostojkih stalej [Welding. Determination of the ferritic phase content in the weld metal of austenitic and two-phase austenitic-ferritic nickel-chromium corrosion-resistant steels]. – M.: Standartinform, 2011. – 25 p. [in Russian]
- Kurdjumov V. G. Prevrashhenija v zhelezeistali [Transformations in iron and steel] / V. G. Kurdjumov, L. M. Utevskij, R. I. Jentin – M.: Nauka. 1977. 236 p. [in Russian]
- Himchenko N. V. Nerazrushajushhij kontrol’ v himicheskom i neftjanom mashinostroenii [Non-destructive testing in chemical and petroleum engineering] / N. V. Himchenko, V. A. Bobrov – M.: Mashinostroenie. 1978. 356 p. [in Russian]
- Rigmant M.
B. Pribor dlja kontrolja izmenenij magnitnogo sostojanija listov slabomagnitnyh austenitnyh stalej – ferritometr F-01 [A device for monitoring changes in the magnetic state of low-magnetic austenitic steel sheets – ferrite meter F-01] / M. B. Rigmant, M. A. Vedeneev, V. S. Ponomarev, and others // Defektoskopija. – – V.3. – P. 3–9. [inRussian]
- Merinov P. E. Opredelenie martensita deformacii v staljah austenitnogo klassa magnitnym metodom [Determination of deformation martensite in austenitic steels by the magnetic method] / P. E. Merinov, A. G. Mazepa. // Zavodskajalaboratorija. – 3. – 1997. – P. 47–49. [in Russian]
- Deryagin A. I. Formation of Nanosized Ferromagnetic Phases during Plastic Deformation and Subsequent Annealing of Stable Austenitic Steels / A. I. Deryagin, V. A. Zavalishin, V. V. Sagaradze and others // Russian journal of nondestructive testing. – 2007 –43 – p.427 (9 pp.)
- Rigmant M. B. Instruments for Magnetic Phase Analysis of Articles Made of Austenitic Corrosion-Resistant Steels / M.
B. Rigmant, A. P. Nichipuruk, B. A. Khudyakov and others // Russian journal of nondestructive testing. – – V. 41. – P. 701–709.
- Rigmant M. B. The possibility of separate measurements of the amounts of ferrite and deformation martensite in three-phase austenitic-class steels using the magnetic method / M. B.Rigmant, A. P. Nichipuruk, M. K. Korkh // Russian journal of nondestructive testing. – – V. 48. – P. 511–521.
- Korkh M. K. Determination of the phase composition of three-phase chromium-nickel steels from their magnetic properties / M. K. Korkh, M. B. Rigmant, D. I. Davydov and others // Russian journal of nondestructive testing. – – V. 51. – P. 727–737.
- Merinov P. The magnetic testing of the ferrite content of austenitic stainless steel weld metal / P. Merinov, S. Entin, Beketov B. and others // NDT International. — 1978. — V. 11. —p. 9-14.
- Elmer J. Measuring Determination the residual ferrite content of rapidly solidified stainless steel alloy/ J.
Elmer T. Eagar // Welding Research Saplement. – – V.4. – p. 141–150.
- Stalmasek E. Measurements of ferrite content in austenitic stainless steel weld metal giving internationally reproducible results / E. Stalmasek // Welding Research Council Bulletin. – – V.318. – p. 22 – 97.
- American National Standard ANSI/AWS A4.2-86 Standard procedure for calibrating magnetic instruments to measure the delta-ferrite content of austenitic stainless steel weld metal.: American welding society inc., 1998. – 27 p.
- International Standard ISO 8249. Welding — Determination of Ferrite Number (FN) in austenitic and duplex ferritic-austenitic Cr-Ni stainless steel weld metals.: ISO copyright office, Switzerland, 2000. – 11 p.
Способ определения содержания ферритной фазы в изделии
Использование: может быть использован для контроля содержания ферритной фазы в аустенитных и аустенитно-ферритных сталях машиностроительного оборудования, включая сварные соединения и наплавку. Сущность изобретения: способ определения содержания ферритной фазы, согласно которому магнитным методом выполняют локальное измерение содержания ферритной фазы в основном металле, сварных швах и наплавках оборудования, для чего предварительно проводят измерение содержания ферритной фазы на эталонном образце при различных уровнях его нагружения, регистрируют напряжение и изменение содержания ферритной фазы, устанавливают зависимость между напряжением и изменением содержания ферритной фазы, определяют величину напряжения, действующего в контролируемой зоне оборудования, после чего измеряют содержание ферритной фазы в контролируемой зоне оборудования и вносят в полученное значение поправку на величину напряжения в соответствии с зависимостью между напряжением и изменением содержания ферритной фазы. Технический результат: возможность получения сопоставимых значений содержания ферритной фазы в разных лабораториях за счет исключения погрешности, вызываемой неучетом действующего в контролируемой зоне напряжения.
Изобретение относится к области контроля содержания ферритной фазы в аустенитных и аустенитно-ферритных сталях машиностроительного оборудования, включая сварные соединения и наплавку.
Известен металлографический метод определения содержания ферритной фазы. (Отраслевая инструкция по определению содержания ферритной фазы в наплавленном металле сварочных и наплавочных материалов, сварных швах аустенитных нержавеющих сталей и антикоррозионной наплавке оборудования и трубопроводов АЭС. АОИ-6-83. Министерство энергетики и электрификации СССР. М. 1984, с. 9). Недостатками этого способа являются невозможность неразрушающего контроля, необходимость наличия атласа микроструктур контролируемых металлов с различным количеством феррита, субъективность оценки оператора, зависимость от технологии травления шлифа и диаметра поля зрения микроскопа. Известен также объемный магнитный метод контроля ферритной фазы с помощью ферритометра (Контроль ферритной фазы при сварке оборудования и трубопроводов ТЭС и АЭС.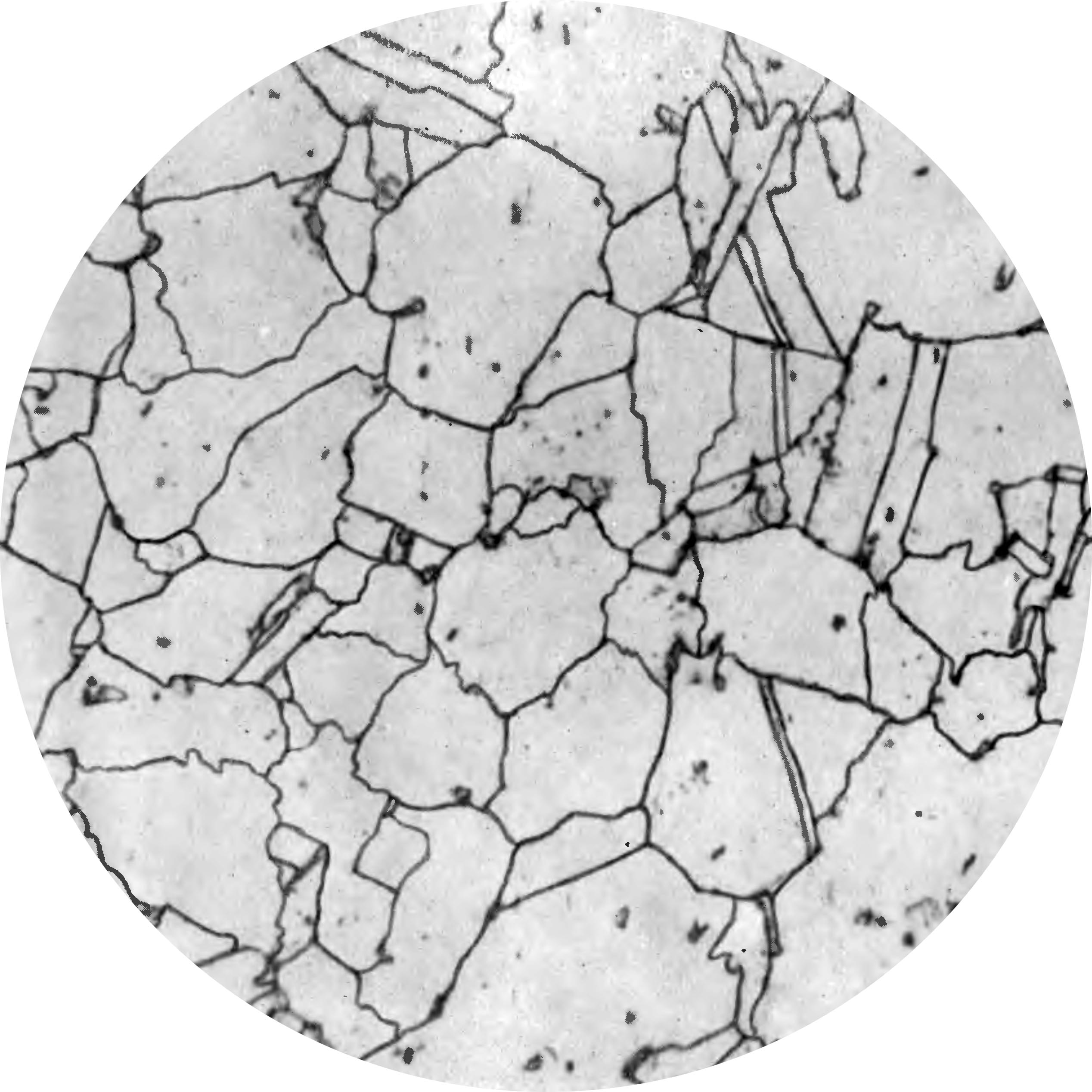
Формула изобретения
Способ определения содержания ферритной фазы в изделии, включающий локальное измерение содержания ферритной фазы магнитным методом, отличающийся тем, что предварительно на эталонном образце определяют зависимость между изменением содержания ферритной фазы и механическим напряжением, прикладываемым к образцу, после чего измеряют содержание ферритной фазы в изделии и вносят в полученное значение поправку с учетом механического напряжения, действующего на него.Содержание феррита в аустенитных нержавеющих сталях
Содержание феррита в аустенитных нержавеющих сталях
Основные нержавеющие материалы серии 300, такие как 304 / L и 316 / L, имеют аустенитную микроструктуру и немагнитны. То есть в отожженном состоянии они практически не содержат феррита, который является магнитным. Литые изделия из этих сплавов обычно содержат некоторое количество феррита. Эти сплавы также образуют некоторое количество феррита при холодной обработке или деформационном упрочнении. В обоих случаях продукты проявляют магнитную тенденцию.Феррит может отрицательно сказаться на коррозионной стойкости в некоторых средах. Есть также приложения, в которых магнитные характеристики влияют на производительность конечного продукта.
Содержание феррита в литом сплаве можно контролировать с помощью состава сплава. Углерод, азот, никель и марганец являются сильными образующими аустенит, и увеличение их содержания в сплаве снижает тенденцию к образованию феррита. Существует несколько различных методов прогнозирования содержания феррита, но одним из наиболее распространенных является диаграмма Делонга.Феррит снижает склонность стали к трещинам затвердевания во время охлаждения. Отливки из 304 (CF8) нередко содержат 8-20% феррита. Состав литых слитков деформируемой нержавеющей стали 304 также сбалансирован и содержит 1-6% феррита, поскольку это снижает вероятность растрескивания во время ковки или горячей обработки.
Отжиг в растворе приведет к растворению большей части феррита, который остался в результате затвердевания слитка. Поскольку литые изделия сбалансированы, чтобы иметь большее количество феррита, отжиг не приведет к его превращению в аустенит.Однако в отожженном деформируемом продукте феррита останется мало или совсем не останется.
Щелкните диаграмму, чтобы увеличить версию
Диаграмма Делонга также позволяет прогнозировать количество феррита, которое может присутствовать в наплавленном шве из деформируемого продукта. Нанесение на график состава деформируемого листа или прутка покажет, сколько феррита могло бы присутствовать, если бы материал был переплавлен (например, сваркой), но это не является достоверным показателем содержания феррита в отожженном продукте.Содержание феррита в реальном продукте можно определить путем кропотливого металлографического исследования или с помощью чувствительных магнитных инструментов в лабораторных условиях (магнитная проницаемость). Однако в большинстве случаев использование сравнительно откалиброванных магнитов позволяет установить приблизительное содержание феррита в пределах от ½ до 1%. Испытания стандартных отожженных 304, 316, 309 и 310 дают значения 2% или меньше. Содержание феррита обычно менее ½%. Эти манометры можно приобрести в компании Severn Engineering Company в Оберне, штат Алабама.
Следует также отметить, что подходящие присадочные металлы, используемые для соединения этих сплавов, также будут иметь более высокое содержание феррита. Это мера предосторожности против образования трещин при затвердевании во время сварки. Содержание феррита в наплавленных швах будет порядка 5-10% феррита в зависимости от сплава. Если также требуются сварные швы, не содержащие феррита, следует выбрать присадку из сплава с более высоким содержанием никеля, например Alloy 20 (ER320LR) или Alloy 625 (ERNiCrMo-3).
Содержание феррита в нержавеющей стали и охрупчивание — AMARINE
Краткое изложение важных замечаний по этой концепции:
- SS будет иметь охрупчивание 885 * F (475 * C) и / или сигма-фазовое продвижение из-за содержания феррита.
- Феррит, содержащийся в Austenite SS, составляет около 2-5% для свариваемости .
- Фаза охрупчивания из-за сигма предотвращается с помощью держателя FN <10
- Охрупчивание 475 * C предотвращается, если FN <14
- Пример: некоторые спецификации нефтеперерабатывающих заводов требовали FN на SS347 <9 для предотвращения охрупчивания (охрупчивание 475 * C + охрупчивание сигма-фазы)
Существует ряд различных типов сталей, которые можно назвать «нержавеющими»; В предыдущих статьях, например, рассматривались ферритные и дисперсионно-твердые стали.Поэтому рекомендуется быть конкретным и ссылаться на группу, к которой принадлежит сталь, во избежание путаницы. Хотя обычно их называют «нержавеющей сталью», стали, описанные в этой статье, более правильно называть аустенитными, 18/8 или хромоникелевыми нержавеющими сталями.
Как и другие типы нержавеющих сталей, аустенитные нержавеющие стали устойчивы к коррозии и окислению из-за присутствия хрома, который образует самовосстанавливающуюся защитную пленку на поверхности стали.Они также обладают очень хорошей ударной вязкостью при чрезвычайно низких температурах, поэтому широко используются в криогенных приложениях. Их можно закалить и повысить их прочность холодной обработкой, но не термообработкой. Они являются наиболее легко свариваемыми из семейства нержавеющих сталей и могут свариваться всеми сварочными процессами, при этом основные проблемы заключаются в предотвращении горячего растрескивания и сохранении коррозионной стойкости.
Удобное и обычно используемое сокращенное обозначение отдельного сплава в группе аустенитных нержавеющих сталей — это система ASTM.Здесь используется трехзначное число «3XX», «3», обозначающее сталь как аустенитная нержавеющая, и дополнительные буквы для обозначения состава и определенных характеристик сплава , например типа 304H, типа 316L и т. Д .; этот метод ASTM будет использован в этой статье.
Типичные составы некоторых сплавов приведены в Таблице 1 . Марка типа 304 может рассматриваться как типичная аустенитная нержавеющая сталь, из которой получены другие марки, и изменения в составе по сравнению с типом 304 приводят к изменению идентификационного номера и выделяются красным цветом.
Таблица 1 Типичный состав некоторых сплавов аустенитной нержавеющей стали
ASTM № (тип) | Состав мас.% | Микроструктура | ||||||
---|---|---|---|---|---|---|---|---|
C (макс.) | Si (макс.) | Mn (макс.) | Кр | Ni | Пн | Прочие | Аустенит — A Феррит — F | |
304 | 0.08 | 0,75 | 2,0 | 18/20 | 11.08 | – | – | A + 2/8% F |
304L | 0,035 | 0,75 | 2,0 | 18/20 | 11.08 | – | – | A + 2/8% F |
304H | 0,04 — 0,10 | 0,75 | 2,0 | 18/20 | 11.08 | – | – | A + 2/8% F |
304N | 0.08 | 0,75 | 2,0 | 18/20 | 11.08 | – | 0,1 / 0,16N | A + 2/8% F |
316 | 0,08 | 0,75 | 2,0 | 16/18 | 14/11 | 2/3 | – | A + 3/10% F |
347 | 0,08 | 0,75 | 2,0 | 17/20 | 13 сентября | – | Nb: 10xC | A + 4/12% F |
321 | 0.08 | 0,75 | 2,0 | 17/19 | 12 сентября | – | Ti: 5xC | A + 4/12% F |
310 | 0,15 | 0,75 | 2,0 | 24/26 | 19/22 | – | – | 100% А |
309 | 0,08 | 1,0 | 2,0 | 22/24 | 15/12 | – | – | A + 8/15% F |
308L (обычно только присадочный металл) | 0.03 | 1,0 | 2,0 | 19/21 | 12.10 | A + 4/12% F |
За 3ХХ может следовать буква, дающая дополнительную информацию о конкретном сплаве, как показано в таблице . «L» — это аустенитная нержавеющая сталь с низким содержанием углерода, предназначенная для использования в агрессивной коррозионной среде; «H» для высокоуглеродистой стали с повышенной жаропрочностью для использования в условиях ползучести; «N» для азотсодержащей стали, где требуется более высокий предел прочности на разрыв, чем у обычной стали.Эти суффиксы используются с большинством обозначений сплава , например типа 316L, типа 316LN, типа 347H, где состав был изменен по сравнению с составом основного сплава.
Аустенитные нержавеющие стали — это простые в металлургическом отношении сплавы. Они либо 100% аустенит, либо аустенит с небольшим количеством феррита (см. Таблица 1 ). Это не феррит, который можно найти в углеродистой стали, а высокотемпературная форма, известная как дельта (δ) -феррит. В отличие от углеродистых и низколегированных сталей аустенитные нержавеющие стали не претерпевают фазовых превращений при остывании от высоких температур.Поэтому они не могут подвергаться закалке с образованием мартенсита, и их механические свойства в значительной степени не зависят от сварки. Поэтому холодное (вызванное водородом) растрескивание не является проблемой, и предварительный нагрев не требуется независимо от толщины детали.
Легирующие элементы в аустенитной нержавеющей стали можно разделить на две группы; те, которые способствуют образованию аустенита, и те, которые способствуют образованию феррита. Основными образцами аустенита являются никель, углерод, марганец и азот; важными образующими ферриты являются хром, кремний, молибден и ниобий.Изменяя количество этих элементов, сталь можно сделать полностью аустенитной или сконструировать так, чтобы она содержала небольшое количество феррита; важность этого будет обсуждаться позже.
В 1949 году Антон Шеффлер опубликовал структурную или фазовую диаграмму, которая иллюстрирует влияние состава на микроструктуру. На диаграмме Шеффлер присвоил коэффициент для различных элементов, коэффициент, отражающий силу воздействия на образование феррита или аустенита; эти факторы можно увидеть на диаграмме.Затем элементы объединяют в две группы, чтобы получить «эквиваленты» хрома и никеля. Они образуют оси x и y диаграммы и, зная состав аустенитной нержавеющей стали, позволяют определять пропорции фаз.
Типичные положения некоторых распространенных сплавов приведены на Fig.1 . На эту диаграмму также наложены цветные области, указывающие на некоторые производственные проблемы, с которыми можно столкнуться при использовании аустенитных нержавеющих сталей.
Хотя все аустенитные нержавеющие стали чувствительны к горячему растрескиванию, полностью аустенитные стали, попадающие в вертикально синюю область на Fig.1 , такие как тип 310, особенно чувствительны.
Основные виновники — сера и фосфор. С этой целью количество этих случайных элементов было постепенно уменьшено, так что теперь стали легко доступны стали с содержанием серы менее 0,010% и фосфора менее 0,020%. В идеале сплав типа 310 или 317 должен иметь уровни серы и фосфора ниже примерно 0.003%. Чистота также является наиболее важным фактором, поэтому необходимо провести тщательное обезжиривание непосредственно перед сваркой.
Стали, такие как тип 304, тип 316, тип 347, которые попадают в небольшую неокрашенную треугольную область в центре диаграммы или близко к ней, содержат небольшое количество дельта-феррита и, не будучи невосприимчивыми к горячему растрескиванию, обладают повышенной стойкостью к образованию пленок серосодержащих жидкостей. Причины этого заключаются в том, что а) феррит может растворять больше серы и фосфора, чем аустенит, поэтому они удерживаются в растворе, а не становятся доступными для образования жидких пленок вдоль границ зерен, и б) присутствие довольно небольшого количества феррита увеличивает зерно. граничная область, так что любые жидкие пленки должны растекаться по большей площади и больше не могут образовывать сплошную жидкую пленку.У 100% аустенитных сталей этого преимущества нет.
Одной из проблем, возникающих при использовании сталей с очень низким содержанием серы, является явление, известное как «изменение отливки к разливке» или «переменное проникновение». Сварочная ванна в стали с низким содержанием серы (<0,005%) имеет тенденцию быть широкой с неглубоким проваром; сталь с содержанием серы более 0,010% имеет более узкий и более глубоко проникающий сварной шов.
Как правило, это проблема только при использовании полностью автоматизированного процесса сварки TIG, поскольку ручной сварочный аппарат способен справиться с колебаниями глубины проплавления из-за различий в содержании серы в разных стальных отливках.Однако автоматизированные процедуры сварки TIG, разработанные для стали с «высоким» содержанием серы, при использовании для сварки стали с низким содержанием серы могут привести к отсутствию дефектов проникающего типа; обратная ситуация может привести к чрезмерному проникновению.
Изменения в процедуре, которые снизили, но так и не устранили эту проблему, включая низкую скорость перемещения, импульсный ток, использование смесей защитных газов Ar / H 2 . Другие методы включают определение минимального содержания серы, скажем, 0,010% или разделение сталей на партии с известными характеристиками проплавления и разработку подходящих процедур сварки.Процесс активированного флюса A-TIG также оказался полезным.
Проблемы при сварке полностью ферритных сталей, попадающих в розовую зону, где рост зерна и охрупчивание являются проблемой.
Аустенитные нержавеющие стали, попадающие в желтую область, также будут хрупкими, но это происходит в результате образования твердых хрупких фаз, называемых «сигма» (σ) и «чи» (χ). Это охрупчивание происходит в диапазоне температур приблизительно от 500 до 900 ° C. Это медленный процесс, который не представляет проблемы при сварке аустенитных нержавеющих сталей, но может происходить при повышенных температурах или при снятии напряжений в свариваемом элементе.
Образованию этих фаз способствует высокое содержание хрома и молибдена (ферритообразующие элементы), поэтому стали типа 310 и 316 являются особенно чувствительными и могут проявлять значительную потерю пластичности после снятия напряжения. Дельта-феррит также преобразуется быстрее аустенита, поэтому сплавы, содержащие большое количество этой фазы, будут разрушаться быстрее, чем аустенитная сталь с небольшим процентным содержанием феррита; отсюда и проблемы с дуплексными и супердуплексными нержавеющими сталями.
Когда необходимо снять напряжение с изготовления, необходимо учитывать потерю пластичности. В сталях, содержащих дельта-феррит, эта фаза должна быть сведена к минимуму, чтобы минимизировать риск горячего растрескивания, путем контроля ферритообразующих элементов, обычно требуя от 2% до 5% дельта-феррита.
Явление охрупчивания в сварных швах из аустенитной нержавеющей стали, подвергающихся воздействию высоких температур, ускоряется присутствием дельта-феррита.
Чтобы избежать растрескивания при затвердевании в сварных швах из аустенитной нержавеющей стали (см. Что такое горячее растрескивание / растрескивание при затвердевании?), Состав присадочного материала должен быть оптимизирован, чтобы обеспечить присутствие в металле сварного шва некоторого количества дельта-феррита (обычно> 3%). .
Однако дельта-феррит превращается в интерметаллические фазы, особенно в сигма-фазу, быстрее, чем аустенит, либо во время высокотемпературной эксплуатации, либо во время термообработки после сварки (PWHT). Сигма-фаза представляет собой интерметаллид с приблизительной химической формулой FeCr и, как и большинство интерметаллидов, очень хрупкий и, следовательно, оказывает вредное влияние на механические свойства.Было показано, что для различных сплавов железо-хром-никель ударная вязкость по Шарпи экспоненциально падает с увеличением содержания сигма-фазы. [1] Чем больше дельта-феррита в номинально аустенитной нержавеющей стали, тем больше она подвержена образованию сигма-фазы. Чтобы избежать значительного охрупчивания, обычно желательно ограничить содержание дельта-феррита в исходной микроструктуре до уровня ниже 10%.
Дельта-феррит, содержащий металл сварного шва, также будет подвержен «охрупчиванию при 475 ° C».Это явление наблюдается, когда нержавеющая сталь нагревается до диапазона 400–550 ° C (хотя эффект наиболее выражен при 475 ° C), и после продолжительного воздействия наблюдается резкое падение ударной вязкости. Это связано с образованием богатых хромом доменов и выделений внутри богатой железом матрицы в результате спинодального разложения феррита при этих температурах. Этот эффект становится более выраженным с увеличением содержания хрома. Однако охрупчивание при 475 ° C обычно незначительно для материалов с ферритным числом менее 14FN.
Урок 5 — Сварка присадочных металлов для нержавеющих сталей
Урок 5 — Сварка присадочных металлов для нержавеющих сталей © АВТОРСКИЕ ПРАВА 2000 УРОК ГРУППЫ ЭСАБ, ИНК. V 5.4.2.2 Количество феррита в аустенитном металл сварного шва из нержавеющей стали можно измерить магнитным устройств, потому что феррит магнитный. Небольшое количество феррита в аустенитном нержавеющий металл шва хорош, потому что предотвращает растрескивание сварного шва. Если сварная деталь должна быть работа при очень низких температурах, однако, следует избегать большого количества феррита, потому что феррит не выдерживает низких температур.Кроме того, если сварная конструкция будет использоваться в высокая температура (выше более 1000 ° F), уровень феррита должен поддерживаться на низком уровне, потому что феррит становится хрупкие при таких температурах. 5.5 РАСЧЕТ СОДЕРЖАНИЯ ФЕРРИТА ВНЕРЖАВЕЮЩАЯ СТАЛЬ
Несколько разработаны простые, но точные методы определения баланса между аустенитом и ферритом, образующим элементы в железе. Когда химический состав металл сварного шва известен, Schaeffler или диаграммы WRC-1992.См. Рисунки 9 и 10. 5.5.0.1 Назначение этих диаграмм — рассчитать никелевый и хромовый эквивалент сварите рассматриваемый металл и нанесите точку на соответствующей диаграмме. В никелевый эквивалент представляет собой сумму содержания никеля и всех других образующих аустенит, умноженную на коэффициенты, представляющие их аустенитообразующий эффект по сравнению с никелем. Хром эквивалент рассчитывается в том же манера.На обеих диаграммах никелевым эквивалентом является вертикальная ось, а хромовый эквивалент — горизонтальная ось. На диаграмме WRC-1992 есть преимущество, так как также учитывается содержание азота. Азот мощный аустенитообразующий элемент. Если содержание азота неизвестно, мы предполагаем 0,06% для GTAW электроды SMAW и 0,08% для присадочных металлов GMAW и FCAW. 5.5.0.2 Когда химический состав недоступен, два общих инструмента также могут быть используется для определения содержания феррита.Поскольку феррит при комнатной температуре магнитный, а аустенитный нет, связь между магнитными могут быть определены отклик и содержание феррита. В больше магнитного отклика на инструмент, тем больше феррита присутствует в металле. Два коммерчески доступные инструменты, использующие этот принцип для измерения содержания феррита: Датчик Magne и датчик Severn. В Манометр Magne — это лабораторный прибор, в то время как Severn Измеритель — это карманный прибор, предназначенный для считывания показаний на месте.5.5.0.3 В Раньше феррит выражался как объемный процент металла. Тем не мение, из-за нестандартной калибровки, часто возникали противоречивые и неточные результаты. К устраните эту проблему, ферритовый объемный процент был изменен на стандартное выражение, известное как ферритовое число (FN) и было одобрено Исследовательским советом по сварке. (WRC), Американское сварочное общество (AWS) и другие агентства. Ферритовые числа (FN) равныИзмерение содержания феррита в сварных швах из супердуплексной нержавеющей стали
В данном разделе представлены и обсуждаются результаты измерений содержания феррита.В первом разделе различные методы определения фракции феррита сравнивались на эталонном образце, чтобы найти наилучший подход, подходящий для сварных швов SDSS. Затем этот метод был использован для связи числа феррита и доли феррита в однопроходных сварных швах. Основные результаты настоящего исследования обобщены в «Заключительных комментариях», которые будут использоваться в качестве руководства для измерения содержания феррита в сварных швах SDSS.
Разработка методики измерения доли феррита
Целью данной серии экспериментов было найти и проверить наилучшую методику измерения доли феррита в однопроходных сварных швах.Был выбран надлежащий метод травления, и доля феррита была измерена с использованием методов PC и IA и сравнена с EBSD в качестве эталонного метода. Параллельно с этим на эталонном образце был проведен круговой тест для изучения разброса результатов ВА в лабораториях разных партнеров.
Сравнение различных методов травления
Поперечное сечение зоны сварного шва в контрольном образце, специально изготовленном для исследования измерения доли феррита, показано на рис.4. Для выявления зоны сварного шва эталонный образец подвергали электролитическому травлению с использованием 20% NaOH. Граница плавления и осевая линия сварного шва указаны на рисунке. Как можно видеть, равноосные зерна образовывались вблизи границы плавления и в верхней части зоны сварного шва. Однако столбчатые зерна образовывались в середине зоны сварного шва между равноосными областями зерен. Все микроструктурные исследования проводились на центральной линии сварного шва эталонного образца, чтобы обеспечить постоянство расположения.
Фиг.4Поперечное сечение образца толщиной 6 мм, изготовленного методом GTAW «валик на пластине» для эксперимента по измерению доли феррита (контрольный образец). Образец был протравлен с использованием 20% NaOH
. Микроструктура эталонного образца, протравленного щавелевой кислотой, двухступенчатым травлением, 20% NaOH и модифицированным Beraha, показана на рис. 5. Цель заключалась в том, чтобы получить максимальную и равномерную фазу. контраст и четкое определение фазовых границ между ферритом и аустенитом. Этот критерий приводит к получению микрофотографий с надлежащим порогом и качеством для ПК и ИА.Если феррит и аустенит имеют одинаковую реакцию на травление и низкий контраст, программное обеспечение IA не может разделить фазы, что приводит к ошибкам в измерениях.
Рис. 5Образец, полученный методом GTAW-переплавки толщиной 6 мм, электролитически протравленный с использованием a 10% щавелевой кислоты, b двухступенчатого травления, c 20% NaOH и d цвета, протравленного модифицированным Бераха. Модифицированный Beraha обеспечил лучший контраст между ферритом и аустенитом
Как показано на рис.5а, электролитическое травление 10% -ной щавелевой кислотой дает минимальный контраст между ферритом и аустенитом по сравнению с другими процедурами травления. Этот результат был ожидаемым, поскольку щавелевая кислота обычно используется для поиска сенсибилизированных участков, таких как участки рядом с нитридами и интерметаллидами [23]. Двухступенчатое травление не показало достаточного контраста между ферритом и аустенитом, чтобы использовать его для измерения доли феррита (рис. 5b). Однако его успешно использовали для измерения интерметаллических фракций в ЗТВ того же образца [6].Как показано на рис. 5c, качество изображения для 20% NaOH намного выше, чем у щавелевой кислоты и двухступенчатого травления. Однако контраст между ферритом и аустенитом значительно варьировался от одного зерна феррита к другому. Например, в правом верхнем углу рис. 5c, феррит и аустенит были вытравлены совсем иначе, чем в центре микрофотографии. Из микрофотографий видно, что цветное травление модифицированным Beraha обеспечило наилучшее качество изображения с самым высоким контрастом между ферритом и аустенитом, где феррит был вытравлен черным, а аустенит — ярким.
Для дальнейшего изучения травителей микрофотографии были импортированы в программу ImagePro. Единственным травителем, который обеспечивал полное разделение фаз за счет регулировки порога, был модифицированный Beraha.
Однако травление модифицированным Beraha требует большей осторожности по сравнению с большинством других травителей, поскольку подготовка образца, химический состав травителя и время травления могут заметно повлиять на качество. Микроструктура двух других сварных швов с неправильным травлением Бераха показана на рис.6. Низкий контраст между мелкодисперсным ферритом, расположенным между зернами аустенита на рис. 6а, может внести большую ошибку в измерение доли феррита. Это может быть нежелательным результатом большой задержки между полировкой и травлением и / или неправильным химическим составом травителя. Время между полировкой и травлением должно быть минимальным (около 10 с), чтобы иметь минимальное влияние образования оксида на поверхности полированного образца. Перенапряжение по Бераха, как показано на рис. 6b, также может отрицательно повлиять на контраст между ферритом и аустенитом, где феррит показывает некоторые сломанные протравленные слои, а аустенит имеет неоднородный контраст.
Рис. 6Неправильное травление модифицированным методом Бераха. a Низкий контраст между мелкодисперсным ферритом и аустенитом и b образование трещин в цветных областях феррита и светлых областях аустенита. Из сварного L-образного соединения, полученного методом GMAW
В итоге, лучшим травителем оказался модифицированный Beraha; однако для получения высококачественных микрофотографий, особенно для IA, необходимо соблюдать надлежащую процедуру травления. Поэтому модифицированный травитель Бераха используется для сравнения PC и IA с EBSD в следующем разделе.
Метод измерения феррита
В таблице 3 подробно описана доля феррита на центральной линии сварного шва эталонного образца, измеренная с использованием IA, PC и EBSD. Среднее значение, указанное для IA, было измерено с учетом измерения 6 полей на осевой линии сварного шва каждой компанией. Более подробная информация о каждом измерении представлена в следующем разделе. Помимо модифицированного Бераха, SMT также измерял долю феррита с помощью ПК на эталонном образце, электролитически травленом с использованием 10% КОН.
Таблица 3 Доля феррита, измеренная с использованием различных методовМетодика IA и EBSD показали разницу всего 0,4%, в то время как стандартные отклонения фракций феррита, измеренные с помощью IA и EBSD, составили 2,6% и 2,3% соответственно. Ожидается, что результаты EBSD будут более точными, поскольку уровень индексации для эталонной выборки составил 98%. Это ясно продемонстрировало, что IA произвел очень точное измерение доли феррита, где его стандартное отклонение и среднее значение почти аналогичны таковым для эталонного метода EBSD.Сравнение ПК с IA и EBSD показывает, что ПК занижает долю феррита, которая более выражена для 10% КОН. Таким образом, метод ПК не только занимает гораздо больше времени, чем ИА, но и имеет более низкую точность. Таким образом, IA эталонного образца, протравленного модифицированным Beraha, был выбран как лучший метод для выполнения теста Round Robin, который будет обсуждаться в следующем разделе.
Циклический тест
Как описано, циклический тест был проведен на эталонном образце, протравленном с помощью Beraha, в лабораториях различных партнеров.Микроструктура образца в верхней, средней и нижней частях зоны сварного шва показана на рис. 7. Как можно видеть, распределение феррита однородно, и между зернами аустенита можно обнаружить только несколько мелких ферритных областей. Таким образом, образец подходит для кругового испытания, так как он имеет микроструктуру с подходящим распределением феррита и соответствующим контрастом феррита и аустенита во всех областях.
Рис. 7Микроструктура верхней, средней и нижней части поперечного сечения эталонного образца GTAW диаметром 6 мм, протравленного модифицированным методом Бераха, показывающая равномерное распределение феррита и аустенита с высокой контрастностью
Фракция феррита в эталонном образце на центральной линии сварного шва, измеренной в различных лабораториях, показано на рис.8. Места, где были сделаны микрофотографии, показаны на рис. 2. Тенденция изменения доли феррита от зоны сварного шва к основному металлу одинакова во всех лабораториях. SMT измерил самую высокую, а OS — самую низкую фракцию феррита в целом. На основании рис. 2 было установлено, что первые восемь микрофотографий, сделанных каждой лабораторией, относятся к зоне сварного шва. Однако, чтобы минимизировать риск измерения доли феррита в ЗТВ, использовались только первые шесть микрофотографий из каждой лаборатории. Доли феррита в зоне сварного шва были в том же диапазоне, и никаких неожиданных фракций зарегистрировано не было.
Рис. 8Доля феррита в образце, переплавленном GTAW толщиной 6 мм, измеренная разными партнерами. Рассмотрев рис.2 и микрофотографии, было решено использовать первые шесть изображений для сравнения, так как они более вероятно расположены в одном и том же положении.
Как объяснено в эксперименте, OS измеряла долю феррита на протравленном образце (без повторного измерения). -травливание) с помощью различных микроскопов. Поскольку OS получила эталонный образец от SMT в протравленном состоянии, доля феррита, измеренная SMT и OS с помощью различных микроскопов, показана на рис.9. Сравнение рисунков 8 и 9 показывает, что различия между лабораториями с повторной полировкой и повторным травлением образца могут иметь такой же эффект, как и изменение микроскопов без изменения других переменных. Комбинации различных микроскопов и камер, а также небольшое изменение положения микрофотографий, вероятно, являются объяснением разброса результатов, полученных с использованием разных микроскопов.
Рис. 9Доля феррита в поперечном сечении эталонного образца (6 мм GTAW-переплав), измеренная с помощью различных микроскопов в Outokumpu и Sandvik для того же протравленного образца
Средняя доля феррита в зоне сварного шва, измеренная с помощью партнеры подробно описаны в Таблице 4.Как можно видеть, средняя доля феррита, измеренная разными партнерами и разными микроскопами, находится в диапазоне от 65,8 ± 2,4% до 70,7 ± 3,1%. Включая стандартное отклонение для максимальной и минимальной фракций феррита, они показывают перекрытие на уровне 67,6–68,2%, что точно находится в диапазоне, измеренном EBSD. Таким образом, это показывает, что измерения фракции феррита можно повторить в разных лабораториях и с использованием разных микроскопов.
Таблица 4 Средняя доля феррита в зоне сварного шва для каждого партнераКак показано на рис.9 и Таблица 4, значения SMT выше, чем у других участников. Причина не ясна, но возможным объяснением может быть установка порога в программном обеспечении IA.
В заключение результатов Round Robin, измерения фракции феррита, проведенные в разных лабораториях, показали очень небольшое отклонение, которое находилось в диапазоне изменения микроскопов в одной и той же лаборатории. Результаты были очень воспроизводимыми и точными. Таким образом, метод IA на модифицированных травленых по Берахе образцах подходит для измерения доли феррита в однопроходных сварных швах SDSS.
Доля феррита и число феррита для однопроходных сварных швов
Следующим шагом было измерение доли феррита в 14 однопроходных сварных швах, выполненных с различными параметрами сварки, и определение взаимосвязи между долей феррита и числом феррита. Места, используемые для измерения доли и количества феррита в каждом сварном шве, показаны на рис. 2. Ожидается, что для определения взаимосвязи между долей и количеством феррита измерения поперечного сечения сварных швов дадут наилучшую корреляцию.Следовательно, измерения числа феррита проводились точно в тех же местах, где измерялись доли феррита.
Соотношение между долей феррита и количеством в поперечном сечении зон сварного шва показано на рис. 10а. Формула была извлечена путем линейной регрессии между числами и дробями, действительными для диапазона фракции феррита 45–65%, следующим образом:
$$ \ mathrm {Феррит} \ \ mathrm {Number} \ \ left (\ mathrm {FN} \ справа) = 1,057 \ times \ mathrm {Феррит} \ \ mathrm {фракция} \ \ left (\% \ right) $$
(1)
Фиг.10Взаимосвязь между средней долей феррита и числом феррита для 14 однопроходных сварных швов: a поперечное сечение металла шва и b верхняя часть поперечного сечения и поверхность сварных швов
Другие возможные и Более практичный подход — найти взаимосвязь между числом феррита и долей феррита на поверхности зон сварного шва. При таком подходе фракции феррита измерялись в верхней части поперечного сечения (примерно 0,2 мм от поверхности, как показано на рис.2), а ферритные числа были измерены по средней линии поверхности шва (рис. 2). Доли и количества феррита, определенные с использованием этого подхода, показаны на рис. 10b. Соотношение линейного уравнения между числами и дробями выглядит следующим образом:
$$ \ mathrm {Феррит} \ \ mathrm {Number} \ \ left (\ mathrm {FN} \ right) = 1.081 \ times \ mathrm {Феррит} \ \ mathrm {дробь} \ \ left (\% \ right) $$
(2)
Сравнение рис. 10a и b показывает, что результаты, полученные для верха и поверхности, более разбросаны по сравнению с результатами для поперечного сечения.Следовательно, необходимо найти корреляцию между средними долями феррита по всему поперечному сечению (определяется из минимум 21 изображения сверху, посередине и снизу каждого сварного шва) и сверху, а также между числом феррита на поперечном сечении. и верхняя поверхность сварного шва. В результате можно будет найти причину повышенного отклонения на рис. 10б.
Типичная микроструктура для верхнего, среднего и нижнего участков при однопроходном сварном шве (для SMAW) показана на рис.11. Как можно видеть, распределение феррита вверху поперечного сечения (рис. 2) очень похоже на распределение в середине и внизу. Соотношение между долей феррита в верхней части и средними значениями для каждых 14 сварных швов представлено на рис. 12а (таблица 5). Диаграмма показывает, как эти два значения хорошо согласуются друг с другом, и доказывает, что доля феррита в верхней части является хорошим представителем средней доли феррита, как визуально показано на рис. 11.
Рис. , и дно образца с V-образной канавкой, сваренного методом SMAW с электродом 2509 Рис.12a Соотношение между долей феррита в верхней части поперечного сечения и средней долей феррита во всем поперечном сечении 14 однопроходных сварных швов. b Связь между числом феррита на поверхности сварного шва и поперечным сечением сварных швов
Таблица 5 Подробная информация о количестве феррита и доле феррита в 14 однопроходных сварных швахСвязь между числом феррита в поперечном сечении и поверхности проиллюстрирована на Рис. 12б. Как видно, отклонение намного больше, чем для ферритной фракции; однако они демонстрируют разумное согласие.Некоторыми возможными причинами отклонения могут быть различная кривизна на поверхности сварных швов, измерение металла шва и ЗТВ вместе, и неоднородное содержание феррита вдоль сварных швов, а также различное микроструктурное текстурирование в x- и z-направлениях.
Для сравнения уравнений количества феррита, полученных для сварных швов SDSS на поперечном сечении и на поверхности, Рис. 13 составлен с использованием формул. 1 и 2. Как можно видеть, оба уравнения предсказывают очень похожие числа феррита.Можно сделать вывод, что измерение числа феррита на шлифованной поверхности однопроходного сварного шва является приемлемым представителем доли феррита в верхней части поперечного сечения, а также всего поперечного сечения зоны сварного шва.
Рис. 13Прогнозирование зависимости числа феррита от доли феррита на поперечном сечении и поверхности сварного шва с использованием формул. 1 и 2 (14 сварных швов). Пунктирные линии представляют собой экстраполяцию для более высоких и более низких фракций, которые не были оценены в этом исследовании
Заключительные комментарии
Настоящее исследование ясно показало, что использование модифицированного реагента Бераха для травления с последующим анализом изображений является воспроизводимым, надежным и точным метод измерения доли феррита.Этот подход согласуется с исследованиями, проведенными Jonsson et al. [16], Варбай и др. [17] и Putz et al. [22], где все предложенные травления с последующим IA могут быть использованы для точного измерения доли феррита. Подходящая практика травления сведет к минимуму требуемую постобработку микрофотографий, в противном случае для измерения фракции феррита потребуется более совершенное программное обеспечение с регулируемыми настройками.
Корреляцию доли феррита и числа феррита (уравнения 1 и 2) можно округлить и представить следующим уравнением для однопроходных сварных швов супердуплексной нержавеющей стали:
$$ \ mathrm {Феррит} \ \ mathrm {Число } \ \ left (\ mathrm {FN} \ right) = 1.1 \ times \ mathrm {Феррит} \ \ mathrm {дробь} \ \ left (\% \ right) $$
(3)
Максимальный разброс чисел феррита, зарегистрированный по этому уравнению, составил + 10 FN и — 5 FN для поверхности сварного шва и + 6 FN и — 10 FN для поперечных сечений.
Сравнение этого уравнения с приведенными в литературе приведено на рис. 14. Это исследование предсказало более низкие доли феррита по сравнению с Shinozaki et al. [25] и Liljas et al. [26]. Однако сравнение с диаграммой, представленной Фишером [24], показывает, что результаты в основном попадают в предложенную область корреляции.Следует отметить, что разница между этим исследованием и литературой может быть результатом нескольких факторов. Химический состав сварных швов SDSS содержит примерно на 6% меньше железа, чем сварные швы DSS, полученные из присадочного металла типа 2209, что может объяснить разницу при сравнении с формулой, представленной Liljas [26]. Кроме того, было показано, что анализ изображений более точен, чем на ПК, использованном в этом исследовании, где ПК занижал долю феррита примерно на 8%. Поэтому ожидается, что формула, определенная с использованием IA, будет отличаться от приведенной в литературе, поскольку использовались разные методы измерения.
Рис. 14Связь между долей и числом феррита для настоящего исследования и из литературы. Оранжевый заштрихованный участок — это ожидаемое соотношение, предложенное в руководстве Fischer FERITSCOPE® [24]
. Следует отметить, что уравнение. 3 и 14 основаны на результатах однопроходной дуговой сварки с долей феррита в диапазоне 40–70%. Потребуются дальнейшие исследования, чтобы проверить применимость формулы для других процессов сварки и фракций феррита.
Тестирование феррита | Полевая инженерия
Тестирование феррита — это быстрый, недорогой и точный процесс, который измеряет процентное содержание феррита в нержавеющей стали, особенно в аустенитной и дуплексной нержавеющей стали.
Специалисты Acuren по испытанию материалов оценивают содержание феррита в микроструктурах вашей нержавеющей стали, чтобы гарантировать надлежащую ударную вязкость, коррозионную стойкость и предотвращение трещин.
Тестирование феррита используется в различных отраслях промышленности, в том числе:
Что такое феррит?
Феррит — одна из металлургических фаз или компонентов, присутствующих в микроструктуре как аустенитных, так и дуплексных нержавеющих сталей.
В наплавленном металле аустенитной нержавеющей стали влияние феррита:
- Механические свойства
- Свариваемость (склонность к растрескиванию при затвердевании)
- Коррозионная стойкость
В дуплексных нержавеющих сталях влияние феррита:
- Механические свойства
- Коррозионные характеристики
Правильное содержание феррита обеспечивает баланс между пластичностью, ударной вязкостью, стойкостью к коррозии и предотвращением трещин.
Что можно сделать при тестировании феррита?
- Оценить содержание феррита в сварных швах и накладках из нержавеющей стали в полевых и лабораторных условиях
- Определить процентное содержание феррита в трубах из дуплексной нержавеющей стали, сосудах высокого давления, резервуарах, отливках, механических компонентах
- Удовлетворять требованиям спецификации, например API 938C, API 582, NACE MR0175, NACE MR0103
Зачем использовать Acuren для тестирования феррита?
Потенциальных отказов или увеличения затрат на техническое обслуживание из-за коррозии в процессе эксплуатации, растрескивания или плохих механических свойств можно избежать, воспользовавшись услугами Acuren по тестированию ферритов.
У Acuren есть технические специалисты и инженеры по всей Северной Америке с многолетним опытом, и они могут предложить эту услугу целому ряду отраслей:
Опытные специалисты по испытанию ферритов
Наши технические специалисты имеют квалификацию в соответствии с конкретными процедурами в рамках нашей задокументированной программы качества, а технические специалисты имеют квалификацию проверены, чтобы гарантировать компетентность с течением времени.
Технические специалисты Acuren, которые проводят это испытание, часто являются конкретными технологами-металлургами и понимают, что означают результаты в отношении свойств материала.Не все организации, занимающиеся тестированием, имеют такой уровень строгости в своей программе качества, равно как и уровень квалификации в рамках своего технического резерва ресурсов.
Кроме того, в Acuren работает около 100 инженеров, которые обучены и квалифицированы, чтобы давать рекомендации клиентам, нуждающимся в дополнительной помощи при интерпретации результатов или принятии решений о наиболее эффективных действиях на основе результатов теста.
Какой желательный процент содержания феррита?
Правильный процент феррита зависит от типа нержавеющей стали, с которой вы работаете.
Содержание феррита в аустенитной нержавеющей стали
Присутствие феррита в сварных швах из аустенитной нержавеющей стали в диапазоне 4-8% является идеальным. Этот процент оказался эффективным в борьбе с микротрещинами металла шва во время охлаждения.
Содержание феррита в дуплексной нержавеющей стали
В дуплексной нержавеющей стали предпочтительно от 35 до 65% феррита, хотя 50% является оптимальным. Это обеспечивает коррозионную стойкость, ударную вязкость и прочность.
Как измеряется содержание феррита?
Проверка содержания феррита выполняется быстро, а результаты сразу же.
- Зонд помещается на исследуемый материал и формируется замкнутая магнитная цепь. Это позволяет нам измерить магнитную проницаемость.
- Эта проницаемость измеряется относительно стандартных процентов других материалов с известным содержанием феррита.
- Проницаемость анализируемого материала указывает процент содержания феррита.
- Содержание феррита считывается с цифрового считывающего устройства.
Повреждает ли материал при испытании?
Используемый нами метод неразрушающий.Проверяемая поверхность должна быть чистой и гладкой.
Насколько точна проверка феррита?
Калибровочные детали используются для обеспечения точности, но на результаты могут влиять форма, размер и состояние поверхности компонента. Типичная точность в отрасли составляет +/- 5%.
Измерение содержания феррита в сварных швах из нержавеющей стали с использованием новой шкалы плотности феррита
Реферат
Остаточное содержание δ-феррита в сварных швах из аустенитной нержавеющей стали является важным параметром, который необходимо контролировать, поскольку от этого зависят несколько свойств сварного шва. .Обычно он измеряется с использованием шкалы ферритового числа (FN), которая была определена в международно признанных стандартах, таких как ISO 8249 и AWS A4.2M. Для измерения FN сварных швов обычно используется FeritScope®. того факта, что остаточная фаза δ-феррита при комнатной температуре является магнитной, а аустенит — нет. Известно, что на показания, полученные с помощью FeritScope®, влияют несколько ограничений, таких как толщина листа, толщина сварного шва, кривизна поверхности и т. Д.Производитель FeritScope® ввел некоторые поправочные коэффициенты для учета этих влияющих условий. Однако, когда скорректированные значения FN сварных швов, выполненных на тонких листах из нержавеющей стали 304L (толщиной ≤ 2,4 мм), были нанесены на график в зависимости от скорости охлаждения, полученные тенденции противоречили имеющимся в литературе. Было обнаружено, что FN увеличивается с увеличением скорости охлаждения, тогда как ожидалось, что она уменьшится. Более того, добавление азота в качестве легирующего элемента, который, как известно, является сильным активатором аустенита, не влияет на измеренное FN сварных швов, что снова противоречит литературным данным.При дальнейшем исследовании было обнаружено, что при измерении FN необходимо учитывать некоторые дополнительные геометрические особенности, помимо упомянутых в руководстве пользователя FeritScope®. Это привело к определению новой шкалы — числа плотности феррита (FDN), которая оказалась лучшим индикатором количества остаточного δ-феррита в сварных швах по сравнению с традиционно используемой шкалой FN. Использование шкалы FDN может устранить противоречия с литературными данными и объяснить сильное стимулирующее аустенит поведение азота.
Ключевые слова
Ферритовый номер
Сварка тонких листов
Плотность феррита
FeritScope®, датчик FGAB1.3-Fe
Соотношение сторон
Рекомендуемые статьи Цитирующие статьи (0)
Просмотреть полный текст© 2019 Elsevier Все права защищены.
Рекомендуемые статьи
Цитирующие статьи
Литейный цех нержавеющей стали
Литейным цехам часто приходится производить специальные марки нержавеющей стали.Одним из контролируемых факторов является содержание феррита в нержавеющей стали. В отдельном информационном листе обсуждается вопрос «Почему отливки из нержавеющей стали обладают магнитными свойствами?» и описаны некоторые из преимуществ и недостатков наличия в структуре металла аустентитной нержавеющей стали с низким содержанием феррита. Но какие факторы определяют количество феррита в нержавеющей стали и как ими управлять? А как определяется количество феррита?
Но сначала, что такое феррит? ASTM A800 определяет феррит как «ферромагнитную объемно-центрированную кубическую микроструктурную составляющую переменного химического состава в сплавах железо-хром-никель.Он может образовываться при затвердевании из расплавленного металла (дельта-феррит) или в результате превращения из аустенита или сигма-фазы при охлаждении в твердое состояние (альфа-феррит) ». Для сравнения, аустенит — неферромагнитная гранецентрированная кубическая фаза, которая содержится в сплавах железо-хром-никель. Важно отметить, что обе фазы являются легированными, то есть они содержат большое количество хрома, никеля, молибдена и т. Д. Феррит не следует путать со «свободным железом» или «нелегированным железом», которые могут находиться на поверхности любого из них. кованый или литой материал.
Основными факторами, определяющими количество феррита, являются химический состав, толщина отливки и цикл термообработки.
- Состав — Спецификация ASTM A800 объясняет, как по химическому составу можно оценить среднее количество феррита в отливках, отлитых из плавки расплавленной нержавеющей стали. Используя формулы, приведенные в A800, количества «элементов, способствующих ферриту» и «элементов, активирующих аустенит», объединяют в хромовый эквивалент и никелевый эквивалент, соответственно.Затем соотношение двух (Creq / Nieq) используется для определения ожидаемого феррита по графику или по таблице. Элементы, способствующие ферриту, — это Cr, Mo, Si и Cb. Элементами, способствующими развитию аустенита, являются Ni, C, Mn и N. Феррит восстанавливается за счет уменьшения количества элементов, способствующих развитию феррита (Creq) и / или повышения элементов, способствующих развитию аустенита (Nieq). Конечно, каждый из элементов также должен удерживаться в пределах, установленных для конкретного производимого сорта.
- Толщина секции — содержание феррита будет варьироваться от одного места к другому в данной отливке.Как правило, более толстая секция будет иметь более высокий феррит, чем более тонкая секция в той же отливке. Этот эффект обусловлен, прежде всего, более низкой скоростью затвердевания в более толстой части. Соответственно более низкая скорость охлаждения во время закалки после термообработки также может иметь значение. В качестве дополнительного объяснения материал, используемый для развития взаимосвязи, приведенной в ASTM A800, был взят из испытательных стержней, отлитых в песчаные формы, толщиной от одного до шести дюймов и подвергнутых термообработке на твердый раствор при температурах от 2000 до 2150 F в течение от 1 до 4 часов.Следует отметить, что Литейный завод практически не контролирует толщину сечения отливки; они определяются разработчиком детали и функцией отливки. Некоторые секции отлиты толще, чем первоначально было предусмотрено, для обеспечения механической обработки или улучшения целостности отливки.
- Термическая обработка — известно, что температура термообработки и время выдержки при этой температуре влияют на конечное содержание феррита в отливках. Однако исследования еще не проводились, чтобы предсказать величину изменения или даже направление изменения с учетом начального химического состава и толщины среза.К счастью, эффект термической обработки обычно невелик по сравнению с эффектом состава и толщины отливки. Феррит обычно считается полезным. Обеспечивает повышенную прочность и устойчивость к растрескиванию. Фактически, в атомной энергетике требуется минимум 5–7% феррита, чтобы обеспечить требуемый уровень свариваемости (предотвращение «микротрещин» во время сварки). Такой же минимальный уровень феррита обеспечивает гораздо более высокую литейную способность (сопротивление разрыву во время затвердевания) по сравнению с полностью аустенитными марками.
Теперь несколько комментариев по поводу определения количества феррита, присутствующего в данной отливке. Существует три основных метода: металлографический, магнитный и расчет по композиции.
- Металлографический — этот метод обычно считается «рефери» и используется для калибровки других методов. Образец удаляется из отливки (таким образом, он является разрушительным) или из репрезентативного испытательного купона (который может быть, а может и не быть репрезентативным, как можно заключить из вышеизложенного обсуждения).Образец полируется, а затем подвергается химическому травлению для обеспечения необходимого оптического контраста между фазами феррита и аустенита. Затем полированную поверхность исследуют с помощью металлургического микроскопа. Объемный процент феррита определяется с использованием любого из ряда хорошо зарекомендовавших себя методов «ручного точечного подсчета». Если скорость затвердевания высокая (например, в тонкостенных отливках или сварных швах), фаза феррита очень мелкая, и даже метод подсчета точек подвержен значительной погрешности.Это основная причина того, что сварочная промышленность предпочла присваивать «ферритное число» на основе магнитного отклика, а не использовать объемный процент феррита на основе металлографических измерений.
- Магнитный — этот метод зависит от того факта, что феррит является магнитным, а аустенит немагнитным. Обычно используются два варианта этой техники: магнитное притяжение и магнитная проницаемость.
- Магнитное притяжение — в этих приборах магнит помещается в контакт с металлической поверхностью и измеряется сила, необходимая для его оттягивания.Эта сила является показателем количества присутствующего феррита. Типичными приборами этой категории являются Magna-Gage и Elcometer. Третий прибор, Severn Gage, определяет, имеет ли испытуемый образец большее или меньшее притяжение к магниту, чем эталонный образец; таким образом, он «ограничивает» содержание феррита между двумя доступными стандартами.
- Магнитная проницаемость — эти инструменты подают ток низкой частоты на катушку, которая находится в контакте с металлической поверхностью.