Оксидирование — что это, виды, особенности
В процессе обработки металла большое значение имеет правильная защита материала от коррозии. Именно коррозийное разрушение приводит к тому, что металлические изделия постепенно начинают терять свою прочность и надежность, значительно уменьшается их устойчивость к внешним нагрузкам.
В промышленности создано большое количество методов, которые могли бы существенно нарастить качество защиты от коррозии. И одним из таких распространенных средств является оксидирование.
Этот материал мы посвятим рассмотрению вопроса о том, что такое оксидирование, как оно проводится и работает. Это помогает лучше понять особенности процесса, провести его в полном соответствии со всеми установленными техническими требованиями.
Что такое оксидирование
Химический состав металла отличается возможностью появления на нем специальных оксидных пленок, если оказываются созданы соответствующие условия. Это необходимо для того, чтобы исключить контакт материала с источниками окисления, затормозить постепенный процесс разрушения металла.
Кроме непосредственной задачи по защите материала, оксидирование также может использоваться и в целях изменения внешнего вида материала. Это помогает придать ему особые внешние качества, сделать значительно более красивым и эстетичным.
Сам процесс оксидирования может проводиться различными способами. В промышленности встречается электрохимическое, химическое, микродуговое и термическое оксидирование. В этом материале мы расскажем о том, чем различные средства отличаются друг от друга.
Химическое оксидирование
Существует множество средств, при помощи которых потенциально может проводиться оксидирование. И химический способ относится к категории одних из наиболее часто используемых.
Применение такого средства предполагает, что будет проводиться обработка изделия в растворе с четко продуманной рецептурой. Это могут быть как расплавы, так и окислители. В составе такого раствора часто встречаются нитраты, хроматы и другие компоненты, способные оказывать на материал аналогичное окислительное воздействие.
В процессе проводится пассивация поверхности. Это значит, что в результате химической реакции начинает формироваться декоративный или защитный слой, блокируется воздействие агрессивных внешних сред, потенциальных катализаторов коррозии.
Химическим методом можно оксидировать как черные, так и цветные металлы. В случае с черными металлами, температура раствора должна составляет 30-100 °С. Лучше всего показывают себя при проведении обработки составы с большим содержанием щелочей или кислот.
Если оксидирование планируется проводить с использованием кислот, раствор выбирается с учетом текущего состава и других особенностей металла. Чаще всего смешивается сразу несколько кислот, которые могли бы сформировать на поверхности материала специальную оксидную пленку. Больше всего распространены соляная и азотная кислоты, к которым могут добавляться различные присадки.
Не менее распространено и щелочное оксидирование. Диапазон температур при его проведении составляет 30-180 °С и чтобы добиться корректного проведения процедуры, его стоит строго соблюдать. При этом раствор создается на основании различных типов окислителей. После того, как обработка будет завершена, с поверхности удаляются все следы рабочего состава, деталь проходит просушивание. Иногда этот метод комбинируется со специальной обработкой в окислительных растворах.
Химическое оксидирование хорошо показывает себя на практике. При этом стоит учитывать, что формируемый на поверхности материала слой менее стойкий и долговечный, чем пленка, которая вырабатывается при использовании другого распространенного метода – анодирования.
Термическое оксидирование
Как можно понять по названию, такой процесс напрямую связан с использованием при обработке металла высоких температур. Но просто нагреть металл недостаточно. Требуется также поместить изделие в среду, которая сформирована с нужным уровнем содержания кислорода.
Чтобы прогреть материал до установленного уровня, требуется использовать специальную печь. Если планируется оксидировать сталь низколегированной группы, либо сделать это с железом, температура не должна превышать отметку в 350 градусов.
Когда проводится обработка легированной стали, максимальная температура увеличивается до 700 °С. Длительность обработки при этом составляет около часа.
Этот метод формирования оксидной пленки наиболее распространен при работе с кремнием. Чтобы материал получил высокий уровень защитных свойств, требуется создавать температуру, которая будет находиться в диапазоне от 800 до 1200 °С.
Анодирование
Анодированием называют оксидирование анодным либо электрохимическим методом. Потому, если вы встречаете такие обозначения процесса, можно сразу понять, что речь идет об одной и той же процедуре.
Чтобы сформировать стойкую оксидную пленку, применяется электролит. Он может быть как твердым, так и жидким. Когда проводится анодирование, используется положительный потенциал поверхности металла.
Активно используется анодирование, если нужно изменить внешние свойства материала, сделать его более эстетичным. При этом удается комбинировать как декоративные, так и защитные свойства для достижения одной цели.
Метод отличается универсальностью. Его можно применять для разных вариантов металлов и сплавов, но с учетом их первоначального состава. Как показывает практика, более всего распространен такой метод в том случае, если требуется провести обработку алюминия.
Плазменное оксидирование
При рассмотрении особенностей такого процесса нельзя забывать про использование плазменного метода обработки. Его особенность заключается в том, что в отличие от термического оксидирования, формируется не высокая, а низкая температура. Само изделие при этом находится внутри специально созданной с учетом особенностей материала плазменной среды.
При формировании плазмы используется ток. Таким образом удается обрабатывать кремний, а также полупроводники из различных материалов. Кроме своих непосредственных задач по защите, метод востребован, потому что помогает повысить степень светочувствительности некоторых типов изделий, которые нуждаются в этом больше всего.
Микродуговое оксидирование
Еще один метод, который активно применяется в ходе работ по созданию оксидных пленок – это микродуговое оксидирование. Название этого процесса также можно встретить под кратким обозначением «МДО».
Оксидные слои, которые формируются в результате такого воздействия на материал, оказываются многофункциональными. Эта методика во многом схожа по своим особенностям с анодной обработкой. Защитные свойства, которые формируются в результате, оказываются очень высокими.
Материал отлично защищается от термического воздействия, изолируется от агрессивных сред, которые провоцируют формирование коррозии. Нельзя также забывать и про декоративные особенности. Со стороны может показаться, что изделие после микродугового оксидирования становится керамическим. Но это только внешнее впечатление, потому что все остальные центральные особенности сохраняются.
Как отмечают специалисты, если рассматривать все методы оксидирования, то именно микродуговое привлекает к себе заметный интерес. Оно помогает формировать очень стойкое и прочное покрытие, что решает распространенную проблему – стирание оксидной пленки, потенциально приводящее к развитию коррозии и другим вариантам повреждения материала.
Чтобы провести микродуговое оксидирование применяется электролит с малым уровнем концентрации щелочи. При этом в него подается переменный или импульсный ток строго заданной частоты. Специального изменения свойств и какой-либо дополнительной подготовки при этом не требуется – материал просто нужно очистить.
Во время создания оксидных пленок применяется большое количество микроразрядов. Они передвигаются по хаотичным траекториям. При этом, удается сформировать как термическое, так и плазмохимическое воздействие.
Одно из преимуществ такого метода заключается в том, что само покрытие оказывается очень глубоко проникающим. Ему удается проникнуть вглубь материала на 70%. При этом еще 30% покрытия оказывается с наружной стороны, что позволяет формировать комплексную защиту с максимальной степенью защищенности.
Стоит также обратить внимание и на толщину покрытия. Она варьируется в диапазоне от 200 до 250 кг, что позволяет говорить о по-настоящему высоких показателях. При выборе определенной температуры электролита также уделяется большое внимание тому, с каким исходным материалом предстоит работать. Температура отличается от 15 до 400 °С.
Большое значение также имеет и то, какой именно электролит применяется в процессе. Вне зависимости от того, какой состав используется, какого-либо особого влияния на окружающую среду не оказывается.
В пользу выбора такого метода говорит доступность оборудования, его компактность и тот факт, что сами электролиты отличаются повышенным уровнем рассеивающих свойств. Это помогает работать с различными деталями, в том числе теми, у которых сложная форма, есть большое количество выемок и других особенностей рельефа поверхности.
Особенности использования оксидирования в процессе работы с алюминиевыми сплавами
При рассмотрении особенностей процесса оксидирования, особенно пристальное внимание стоит уделить вопросу создания оксидных слоев непосредственно на поверхности материала. Причина заключается в том, что в этом случае допустить ошибку становится значительно проще, чем с в случае с черными металлами. Тогда вся работа пойдет насмарку.
В процессе работы с алюминием используется несколько описанных ранее методов. Это химический, микродуговой и электрохимический. Рассмотрим их подробнее далее.
Анодное оксидирование алюминия и его сплавов
Во время работы с алюминием часто применяется его анодирование. Этот метод помогает значительно повысить степень защищенности от атмосферной коррозии, как для самого материала, так и для сплавов, которые формируются на его основе. Создание стойкой оксидной пленки таким методом также помогает подготовить поверхность для последующего успешного выполнения окрашивания выбранным типом состава.
Во время подобного метода обработки, с внешней стороны материала удается получить стойкое покрытие, которое будет отличаться повышенным уровнем защиты как от контакта с водой, так и кислот. Если рассматривать состав пленки, то больше всего в ней будет именно оксида алюминия. При этом стоит также обратить внимание на то, что основные характеристики твердости будут меняться в зависимости от того, какой состав у исходного материала:
- Технический алюминий – от 5000 до 6000 Мпа.
- Алюминиевые сплавы – от 2000 до 5000 Мпа.
Еще один важный показатель слоя, который формируется при использовании анодного оксидирования составляет 1014 – 1015 Ом·м.
Важная особенность анодного оксидирования заключается в том, что оно позволяет гибко формировать особенности каждого конкретного слоя. Он может иметь разную твердость, степень пористости, эластичность и другие ключевые показатели, которые стоит учитывать. Все что нужно при выполнении обработки для изменения характеристик конкретного слоя – отрегулировать состав электролита или сменить характеристики проводимого в конкретном случае электролиза.
Если электролит, который применяется в конкретном случае, создает кислую или нейтральную среду, на поверхности защитный слой создается очень быстро. При этом происходит стремительное твердение до заданных ранее показателей.
Электрохимическое оксидирование алюминия
Если в рамках выполняемой обработки выполняется электрохимическое оксидирование, то первичная пленка оказывается очень тонкой. Чтобы сделать ее значительно более толстой, требуется применять кислород.
На практике доказано, что рост пленки прекращается в том случае, если она достигает толщины 0,1 мкм. Чтобы спровоцировать дальнейшее разрастание защитного слоя, нужно использовать повышение напряжения строго в первоначально заданном диапазоне.
Стоит также обратить внимание на способность электролита к постепенному растворению формирующегося оксида алюминия и пленки, которую он способен создавать на поверхности материала. Потому нужно контролировать параметры проведения процедуры для того, чтобы пленка не растворялась, а наращивалась до уровня толщины до 2 мкм. Покрытие в таком случае будет отличаться как хорошими защитными показателями, так и низким уровнем пористости.
Если во время процедуры используется электролит, он может быстро растворить оксидный слой, либо сделать пленку значительно более толстой. Это зависит от состава, температуры и других условий.
В ряде случаев наблюдается ситуация, при которой скорость окисления значительно превышает скорость процесса, с которым на материале формируются окислы.
Также стоит обратить внимание на степень толщины оксидной пленки. На этот параметр напрямую влияет то, насколько хорошо электролит может растворять конкретные варианты оксидов, как ведет себя материал, который оказывается погружен в него.
Еще один параметр, на который стоит обратить внимание – это непосредственно сама толщина оксидного покрытия. Во многом на нее влияет состав алюминия и сплавов, которые создаются на его основе. Считается, что обработка чистого алюминия значительно проще, чем работа с его сплавами – при анодировании слой удается сформировать значительно быстрее.
Если в сплаве есть большое количество различных добавок, пленка будет образовываться медленнее, значительно сложнее будет сформировать пленку, которая по своим характеристикам полностью подходит под ваши требования. Особенно сильное негативное влияние на качество оксидирования оказывает наличие в составе сплава таких компонентов, как медь, железо, марганец и магний.
Применение оксидирования помогает получить пленку, которая состоит сразу из двух слоев. Один располагается непосредственно на границе с металлом. Именно он отвечает за формирование стабильной барьерной среды. Второй слой более толстый, в нем больше пор, выше мягкость. Он эффективно проникает в сам материал и делает его значительно более защищенным от большинства потенциальных внешних угроз.
Химическое оксидирование алюминия
Рассматривая процесс формирования на алюминии и его сплавах специальной оксидной пленки, стоит обратить внимание и на методы химического оксидирования. Эта технология востребована в промышленности, потому что отличается доступной стоимостью, сравнительной простой в реализации подготовкой изделия и рядом других преимуществ.
Важная особенность такого процесса заключается в том, что он не использует во время работы электрического тока. Изделие из алюминия или одного из сплавов помещается непосредственно в раствор хроматов. Это стимулирует постепенное появление оксидных пленок, помогает значительно ускорить процесс работы с крупными партиями – доступна одновременная параллельная обработка деталей.
Стоит отметить высокий уровень качества пленок, который, тем не менее, уступает анодированию и электрохимическим пленкам. Толщина подобного покрытия будет составлять до 3 мкм. Подобного оксидного слоя на практике вполне хватает для того, чтобы устранить большинство потенциальных угроз и оградить заготовку от негативного воздействия внешних агрессивных сред.
Именно при проведении химического оксидирования на первый план выходит контроль температуры. Большое значение имеет также и сам состав электролита, который активно будет использоваться в процессе.
Если в растворе, который применяется при подобной обработке детали, слишком мало щелочи, пленка будет слишком тонкой. Когда наблюдается перегрев есть вероятность получения рыхлой прослойки, которая не сможет выдержать значительного механического давления, сотрется и откроет путь для формирования коррозии.
Финишная обработка оксидных пленок
Наконец, стоит обратить внимание на проведение качественной финишной обработки оксидного слоя, который успел сформироваться на поверхности материала.
Существует два основных метода, которые могут использоваться в процессе:
- Проведение уплотнения. Средство направлено на то, чтобы слой оксидов стал заметно более стойким к коррозии, воздействию света. Это также помогает существенно нарастить его диэлектрические свойства – такая особенность проверена на практике. При проведении уплотнения хорошо показывает себя прогретая до температуры кипения вода. В нее могут добавляться соли, поверхностно-активные вещества. Все это помогает заметно увеличить скорость проведения такого процесса.
- Окрашивание. Пленки также могут окрашиваться – это позволяет сделать изделие более привлекательным внешне, а также сформировать дополнительный защитный слой, который ограничит потенциальный контакт с агрессивными средами.
Чтобы краска легла ровно и без дефектов, пленка качественно промывается, с нее удаляются все посторонние загрязнения. Потом начинается непосредственное окрашивание. При этом стоит обратить внимание на то, что показатели пористости созданного ранее активного слоя напрямую влияют на то, какой цвет получит покрытие и насколько стойким оно в итоге окажется.
Оцинковка как средство защиты от коррозии
Еще один метод, который помогает надежно защитить материал от контакта с внешними агрессивными средами – проведение цинкования. Наша компания предоставляет клиентам профессиональное горячее цинкование с применением передового современного оборудования.
Есть сразу несколько причин обратиться к нам:
- Большие производственные мощности. У нас есть три крупных цеха для выполнения горячего цинкования. Мощность предприятия составляет до 120 тысяч тонн продукции в год.
- Высокий уровень качества. Мы строго следим за требованиями ГОСТ 9.307-89. Также на предприятии используется лучшее оборудование немецко-австрийской фирмы KVK KOERNER и чешской фирмы EKOMOR.
Это позволяет нам быть уверенными в высоком уровне работы и предоставлять официальные гарантии.
- Большой опыт. Мы успешно работаем на рынке с 2007 года. За это время было реализовано множество проектов.
Чтобы связаться с нами, получить дополнительные консультации по всем вопросам, касающимся сроков выполнения вашего заказа и других задач, достаточно просто оставить заявку на сайте или позвонить по указанным телефонам.
Вернуться к статьямПоделиться статьей
Соединяем алюминиевые провода
Хотя по современным стандартам проводка в жилых квартирах делается преимущественно из медных проводов, нередко можно встретить электропроводку и из алюминия. Если заменить старую проводку на новую невозможно, тогда вам необходимо узнать, как соединить алюминиевые провода своими руками. Так, как например, подключать люстру, розетку и другие электрические приборы правильно? Можно ли соединять алюминиевые провода с другими? Как сделать соединение надежным? Как прочно соединить алюминиевые провода между собой? Ответы на эти вопросы вы сможете получить в этой статье.
Особенность алюминиевого провода
Из-за особых характеристик с алюминием сложно работать. Также в процессе окисления этого металла на поверхности образовывается оксидная пленка. Она в свою очередь препятствует хорошему прохождению тока. Данная пленка плавится при температуре двух тысяч градусов, а это показатель больше температуры плавления самого алюминия. Если счищать пленку механическим способом, то буквально за короткий промежуток времени она появляется снова. В результате оксидная пленка препятствует качественному контакту соединения.
Среди других особенностей алюминия можно выделить повышенную степень хрупкости и текучести. Исходя из этого, контакт не должен подвергаться никаким механическим воздействиям. Например, если соединение выполнено с помощью болта, то время от времени его необходимо постоянно подтягивать. Это связано с тем, что алюминий со временем вытечет из-под контакта.
Электрохимическая коррозия
Можно ли соединять алюминиевый провод с другими? Да! Но здесь важно учесть некоторые важные моменты. Если отсутствует влага, то такое соединение будет вечным. Однако влага присутствует везде, она в свою очередь способствует разрушению контактов. Важно учитывать и тот факт, что каждый проводник электрического тока имеет свой электрохимический потенциал. В связи с этим были созданы аккумуляторы и батарейки, однако, в момент попадания воды в месте соединения металлов образовывается короткозамкнутый гальванический элемент. В результате происходит разрушение одного из металлов. Чтобы узнать, какие металлы можно соединять, а какие нет, важно знать величину электрохимического потенциала того или иного проводника тока.
Так, например, соединять разные провода допустимо в том случае, когда между ними уровень электрохимического потенциала не превышает 0,6 мВ. Исходя из этого, получается, что соединение меди с нержавеющей сталью будет качественным с разницей потенциала 0,1 мВ, в отличие от соединения с серебром (0,25 мВ) или золотом (0,4 мВ).
Обратите внимание! Если медный провод имеет покрытие из оловянно-свинцового припоя, то допускается любое механическое соединение с алюминиевым проводом.
Методы соединения алюминия с медью
Исходя из вышесказанного, может показаться, что соединение алюминиевых проводов дело непростое. Однако это не так! В процессе соединения алюминиевого провода с медным проводом нужно просто соблюдать технологию. Рассмотрим несколько известных методов соединения алюминиевого провода с медным:
Скрутка
Это один из легких методов соединения провода. При этом абсолютно не требуется никакая квалификация, а также особые знания. Но в результате получается далеко не надежное соединение. Почему? Все связано с тем, что в период колебания температуры происходит линейное расширение проводов и, как следствие, между ними образовывается зазор, который в свою очередь увеличивает сопротивление. После, контакт окисляется и спустя некоторое время разрушается.
Обратите внимание! Такое явление произойдет не в первый год. Но если вам хочется создать надежное и качественное соединение, тогда стоит подумать об более надежном альтернативном варианте.
Как же выполняется такое соединение? Здесь важно чтобы один провод не обвивал другой, а они оба обвивались между собой. Чтобы соединение вышло качественным медный провод можно залудить припоем. При этом нет ограничения по диаметру соединяемых проводов. Если медный провод многожильный, то в обязательном порядке его необходимо пролудить припоем. Если провод толстый, то достаточно будет три витка, а на тонком до Ø1 мм необходимо сделать пять витков.
Резьбовое соединение
Один из самых надежных вариантов соединения алюминиевых и медных проводов при помощи гаек и винтов. Такое соединения обеспечит на протяжении долгих лет качественный контакт. Данным методом можно соединять провода разного сечения, многожильные и одножильные.
Итак, с конца провода для начала требуется снять изоляцию. После на винт надевают пружинную шайбу, обычную шайбу, колечко одного проводника, простую шайбу, колечко другого проводника, шайбу и в конце гайку, которая закручивает всю конструкцию.
Обратите внимание! Если проводник имеет жилу Ø2 мм, то винт должен быть М4.
Клеммная колодка
Клеммная колодка это еще один современный метод соединения алюминиевого и медного проводов. Хотя он пользуется большой популярностью, метод соединения винтами и болтом гораздо надежнее. Однако клеммная колодка позволяет быстро и качественно соединить провода. При этом нет потребности в формировании колечек на конце провода, а также в дополнительной изоляции. Данная конструкция полностью исключает возможность соприкосновения двух оголенных проводов.
Выполняется такое соединение следующим образом: Конец провода зачищается от изоляции на длину до 5 мм. После в отверстие клеммной колодки вставляется провод, который затягивается винтом.
Обратите внимание! Затягивать винт следует с чувством, особенно алюминиевый провод.
Такое соединение очень выручает в тех случаях, когда из потолка торчит короткий отрезок алюминиевого провода. Если в таком случае пользоваться методом скруток, то провод рано или поздно попросту обломается. Это нельзя сказать об использовании клеммной колодки. Также если случайно в стене были перебиты алюминиевые провода, то данная технология упрощает их соединение. Но здесь есть одно но! Клеммную колодку нельзя прятать в штукатурке или в стене без специальной распределительной коробки.
Клеммная колодка и плоско-пружинный зажим
Такой метод соединения проводов появился сравнительно недавно. Существует два их вида: одноразовый и многоразовый. В последнем случае имеется специальный рычаг, который позволяет вынимать и вставлять провод несколько раз. Такие клеммные колодки позволяют соединять многожильные провода разных видов алюминиевых с медными проводами.
Они широко используются для монтажа люстр, а также для соединения проводов в распределительных коробках. В отверстие колодки провод вставляется с усилием и там надежно фиксируется. Чтобы вынуть провод, потребуются большие усилия. На практике лучше пользоваться многоразовыми клемниками, которые позволяют в случае просчета переделать соединение.
С провода снимается изоляция на 10 мм. Рычажок на многоразовом клемнике поднимается вверх и вставляется провод. Затем рычаг возвращается в обратное положение. Соединение готово!
Неразъемное соединение
Данный вид соединения имеет практически все преимущества резьбового. Можно выделить быстроту монтажа, прочность, доступную цену и простоту соединения. Принцип его действия прост. Для соединения провода заклепкой подготавливаются колечки диаметром 4 мм. Сперва надевается алюминиевый провод, после пружинная шайба, медный провод и плоская шайба. В заклепочник вставляется стержень из стали и сжимается до щелчка ручки. В результате обрезается лишний проводник и соединение полностью готово.
Надежность такого соединения очень высокая. Его применяют для сращивания проводов. Самое главное требование при его использовании – изоляция участка соединения.
Скрутка алюминиевых проводов между собой
О преимуществах и особенностях скрутки мы говорили выше, но сейчас рассмотрим этот вопрос под другим углом, а именно, соединение алюминиевого провода с себе подобным. В данном случае успех применения метода скрутки напрямую будет зависеть от сечения, диаметра проводов и других важных факторов. В идеале алюминиевые провода лучше всего паять, предварительно скрутив их желобком.
Однако здесь важно быть внимательным, так как на поверхности алюминиевых проводов образовывается оксидная пленка. Даже если ее зачистить, то она очень быстро снова появиться, как уже отмечалось выше, поэтому концы провода можно зачистить напильником до блеска или наждачной бумагой. Самый нижний виток рекомендуется сжать плоскогубцами. Такое соединение будет долговечным и прочным.
Полезные советы и рекомендации
Каждое соединение провода должно быть качественно заизолировано.
Рекомендуется размещать их в распределительных коробках. Если такое соединение просто заштукатурить в стене, то так ограничивается доступ к нему и, соответственно, подтянуть контакты будет невозможно. Хотя если использовать технологию пружинных зажимов, то в этом необходимости не будет.
Если вы хотите сделать такое соединение своими руками в домашних условиях, то не рекомендуется пользовать пайкой или сваркой провода при отсутствии опыта выполнения подобных работ. Лучшим вариантом будет контактный зажим или один из вышеописанных методов соединения алюминиевого провода с медным или между собой.
Итак, мы рассмотрели с вами наиболее распространенные методы соединения алюминиевого провода. Безусловно, если у вас нет опыта или вы попросту боитесь браться за такую работу, то лучше не рисковать и обратиться к специалисту. В противном случае, если у вас есть опыт таких работ, действуйте, следуя всем рекомендациям из этой статьи.
Окисление монооксида углерода наночастицами золота, нанесенными на пленку оксида алюминия, выращенную на подложке Mo(110): эффект туннелирования заряда через оксидную пленку
1. Ведрин Дж. К. Оксиды металлов в гетерогенном катализе. Эльзевир; Амстердам, Нидерланды: 2018. с. 618. [Google Scholar]
2. Chen S., Xiong F. , Huang W. Химия поверхности и катализ оксидных модельных катализаторов от монокристаллов до нанокристаллов. Серф. науч. Отчет 2019; 74:100471. doi: 10.1016/j.surfrep.2019.100471. [CrossRef] [Google Scholar]
3. Пиконе А., Рива М., Брамбилла А., Каллони А., Буссетти Г., Финацци М., Чиккаччи Ф., Дуо Л. Реактивные границы раздела металл-оксид: микроскопический вид. Серф. науч. Отчет 2016; 71: 32–76. doi: 10.1016/j.surfrep.2016.01.003. [CrossRef] [Google Scholar]
4. Цай Ю., Фэн Ю.П. Обзор переноса заряда и химической активности TiO 2 : механизм и применение. прог. Серф. науч. 2016;91:183–202. doi: 10.1016/j.progsurf.2016.11.001. [Перекрестная ссылка] [Академия Google]
5. Хонкала К. Адаптация свойств оксидов: влияние на адсорбционные характеристики молекул и металлов. Серф. науч. Отчет 2014; 69: 366–388. doi: 10.1016/j.surfrep.2014.09.002. [CrossRef] [Google Scholar]
6. Окадзаки К., Морикава Ю., Танака С., Танака К., Кохьяма М. Электронные структуры Au на TiO2(110) расчетами из первых принципов. физ. Ред. Б. 2004; 69:235404. doi: 10.1103/PhysRevB.69.235404. [CrossRef] [Google Scholar]
7. Sanchez A., Abbet S., Heiz U., Schneider W.-D., Ha1kkinen H., Barnett R.N., Landman U. Когда золото не благородно: наноразмерные золотые катализаторы. Дж. Физ. хим. А. 1999;103:9573–9578. doi: 10.1021/jp9935992. [CrossRef] [Google Scholar]
8. Yan Z., Chinta S., Mohamed A.A., Fackler J.J.P., Goodman D.W. Роль F-центров в катализе Au, нанесенным на MgO. Варенье. хим. соц. 2005; 127:1604–1605. doi: 10.1021/ja043652m. [PubMed] [CrossRef] [Google Scholar]
9. Тваури И.В., Гергиева Б., Магкоева В., Григоркина Г., Блиев А., Ашхотов О.Г., Созаев В., Фукутани К., Магкоев Т. Окисление угарного газа на золотых наночастицах, нанесенных на фторид лития: значение F-центров. Твердотельный коммун. 2015; 213–214:42–45. doi: 10.1016/j.ssc.2015.04.017. [Перекрестная ссылка] [Академия Google]
10. Юн Б., Хаккинен Х., Ландман Ю. Взаимодействие O2 с кластерами золота: молекулярная и диссоциативная адсорбция. Дж. Физ. хим. А. 2003; 107:4066–4071. doi: 10.1021/jp027596s. [CrossRef] [Google Scholar]
11. Лопес Н., Норсков Дж.К., Янссенс Т.В.В., Карлссон А., Пуч-Молина А., Клаузен Б.С., Грюнвальдт Дж.Д. Адгезия и форма наноразмерных частиц золота в катализаторе Au/TiO2 . Дж. Катал. 2004; 225:86–94. doi: 10.1016/j.jcat.2004.03.036. [CrossRef] [Google Scholar]
12. Fu Q., Wagner T. Взаимодействие наноструктурированных металлических слоев с оксидными поверхностями. Серф. науч. Представитель 2007; 62: 431–49.8. doi: 10.1016/j.surfrep.2007.07.001. [CrossRef] [Google Scholar]
13. Химайер М., Стемпель С., Шайхутдинов С.К., Либуда Дж., Баумер М., Олдман Р.Дж., Джексон С.Д., Фройнд Х.-Дж. О термостойкости металлических частиц, нанесенных на тонкую пленку оксида алюминия. Серф. науч. 2003; 523:103–110. doi: 10.1016/S0039-6028(02)02404-4. [CrossRef] [Google Scholar]
14. Libuda J., Frank M.M., Sandell A., Andersson S., Brühwiler P., Bäumer M., Mårtensson N., Freund H.-J. Взаимодействие родия с модельными подложками из гидроксилированного оксида алюминия. Серф. науч. 1997;384:106–119. doi: 10.1016/S0039-6028(97)00170-2. [CrossRef] [Google Scholar]
15. Баумер М., Бинер Дж., Мэдикс Р. Электронные свойства роста и реакционная способность ванадия, нанесенного на тонкую пленку оксида алюминия. Серф. науч. 1999; 432:189–198. doi: 10.1016/S0039-6028(99)00400-8. [CrossRef] [Google Scholar]
16. Brause M., Ochs D., Günster J., Mayer T., Braun B., Puchin V., Maus-Friedrichs W., Kempter V. Адсорбция Cs на оксидных пленках ( Al 2 O 3 , MgO, SiO 2 ) Прибой. науч. 1997; 383: 216–225. doi: 10.1016/S0039-6028(97)00174-X. [CrossRef] [Google Scholar]
17. Hirschmugl C. J. Границы в инфракрасной спектроскопии на поверхностях и интерфейсах. Серф. науч. 2002; 500: 577–604. doi: 10.1016/S0039-6028(01)01523-0. [CrossRef] [Google Scholar]
18. Гудман Д.В. Химические и спектроскопические исследования поверхностей оксидов металлов. Дж. Вак. науч. Технол. А. 1996; 14:1526–1531. дои: 10.1116/1. 580290. [CrossRef] [Google Scholar]
19. Ву М.-К., Гудман Д.В. Частицы Cu на упорядоченном Al2O3: реакции с оксидом азота и оксидом углерода. Дж. Физ. хим. 1994;98:9874–9881. doi: 10.1021/j100090a023. [CrossRef] [Google Scholar]
20. Григоркина Г., Тваури И.В., Калоева А., Бурдзиева О., Секиба Д., Огура С., Фукутани К., Магкоев Т.Т. – поверхностный сплав Mo(110). Твердотельный коммун. 2016; 233:11–14. doi: 10.1016/j.ssc.2016.02.010. [CrossRef] [Google Scholar]
21. Jaeger R.M., Kuhlenbeck H., Freund H.-J., Wuttig M., Hoffmann W., Franchy R., Ibach H. Формирование упорядоченного верхнего слоя оксида алюминия с помощью окисление NiAl(110) Surf. науч. 1991;259:235–252. doi: 10.1016/0039-6028(91)90555-7. [CrossRef] [Google Scholar]
22. Becker C., Kandler J., Raaf H., Linke R., Pelster T., Dräger M., Tanemura M., Wandelt K. Адсорбция кислорода и образование оксида на Ni3Al ( 111) Дж. Вак. науч. Технол. А. 1998; 16:1000–1005. дои: 10.1116/1.581221. [CrossRef] [Google Scholar]
23. Дженнисон Д.Р., Вердоцци К., Шульц П.А., Сирс М.П. Ab initio структурные прогнозы ультратонких пленок оксида алюминия на металлических подложках. физ. Преп. Б. 1999;59:15605–15612. doi: 10.1103/PhysRevB.59.R15605. [CrossRef] [Google Scholar]
24. Магкоев Т.Т., Владимиров Г.Г. Рост ультратонкой пленки оксида алюминия на поверхности Mo(110): исследование работы выхода. Дж. Физ. Конденс. Иметь значение. 2001; 13: L655–L661. doi: 10.1088/0953-8984/13/28/101. [CrossRef] [Google Scholar]
25. Магкоев Т.Т., Кристманн К., Моутинью А., Мурата Ю. Конденсация паров оксида алюминия на поверхности Mo() и адсорбция атомов меди и золота на образующемся оксидном слое. Серф. науч. 2002; 515: 538–552. дои: 10.1016/S0039-6028(02)01972-6. [CrossRef] [Google Scholar]
26. Магкоев Т.Т., Владимиров Г., Ремар Д., Моутинью А. Сравнительное исследование адсорбции металлов на поверхности металла и оксида. Твердотельный коммун. 2002; 122:341–346. doi: 10.1016/S0038-1098(01)00511-7. [CrossRef] [Google Scholar]
27. Фредерик Б.Г., Апаи Г., Родин Т.Н. Поверхностные фононы в тонких пленках оксида алюминия: толщина, энергия пучка и эффекты смешения симметрии. физ. Преподобный Б. 1991; 44: 1880–1890. doi: 10.1103/PhysRevB.44.1880. [PubMed] [CrossRef] [Академия Google]
28. Фьерро Х.Л.Г., де ла Банда Х.Ф.Г. Хемосорбция молекул-зондов на оксидах металлов. Катал. 1986; 28: 265–333. doi: 10.1080/01614948608082252. [CrossRef] [Google Scholar]
29. Кэмпбелл К.Т. Ультратонкие металлические пленки и частицы на оксидных поверхностях: структурные, электронные и хемосорбционные свойства. Серф. науч. Республика 1997; 27: 1–111. doi: 10.1016/S0167-5729(96)00011-8. [CrossRef] [Google Scholar]
30. Zecchina A., Scarano D., Bordiga S., Ricchiardi G., Spoto G., Geobaldo F. ИК-исследования CO и NO, адсорбированных на хорошо охарактеризованных оксидных одиночных микрокристаллах. Катал. Сегодня. 1996;27:403–435. doi: 10.1016/0920-5861(95)00202-2. [CrossRef] [Google Scholar]
31. Рено Г., Виллет Б. , Вильфан И., Бурре А. Атомная структура реконструкции α-Al2O30001 (√31×√31)R ± 90. физ. Преподобный Летт. 1994; 73: 1825–1828. doi: 10.1103/PhysRevLett.73.1825. [PubMed] [CrossRef] [Google Scholar]
32. Casarin M., Maccato C., Vittadini A. Сравнительное исследование хемосорбции CO на неполярных поверхностях Al2O3 и Ti2O3. Дж. Физ. хим. Б. 2002; 106: 795–802. doi: 10.1021/jp011140d. [Перекрестная ссылка] [Академия Google]
33. Оссичини С., Мемео Р., Чиккаччи Ф. АЭС-анализ механизма роста металлических слоев на металлических поверхностях. Дж. Вак. науч. Технол. А. 1985; 3: 387–391. doi: 10.1116/1.573226. [CrossRef] [Google Scholar]
34. Богичевич А., Дженнисон Д.Р. Вариации характера адсорбции металлов на ультратонких пленках Al2O3. физ. Преподобный Летт. 1999;82:4050–4053. doi: 10.1103/PhysRevLett.82.4050. [CrossRef] [Google Scholar]
35. Маттссон А.Э., Дженнисон Д. Вычисление точных поверхностных энергий и важность собственной энергии электрона в адгезии металла/оксида металла. Серф. науч. 2002; 520:L611–L618. дои: 10.1016/S0039-6028(02)02209-4. [CrossRef] [Google Scholar]
36. Cao Y., Hu S., Huang S., Yu M., Wang T., Yan S.S., Xu M. Управление зарядовым состоянием кластеров Au на рутиловом TiO 2 (110 ) монокристаллические поверхности посредством молекулярных реакций, исследуемых с помощью инфракрасной спектроскопии. физ. хим. хим. физ. 2016;18:17660–17665. doi: 10.1039/C6CP02324J. [PubMed] [CrossRef] [Google Scholar]
37. Маркес А. М., Грасиани Дж., Санс Дж. Ф. Зарядовое состояние атомов металлов на оксидных носителях: систематическое исследование, основанное на моделируемой инфракрасной спектроскопии и теории функционала плотности. Теор. хим. Счета. 2009 г.;126:265–273. doi: 10.1007/s00214-009-0703-0. [CrossRef] [Google Scholar]
38. Мейер Р., Лемир К., Шайхутдинов С.К., Фройнд Х.-Дж. Поверхностная химия катализа золотом. Золотой бюллетень. 2004; 37: 72–124. doi: 10.1007/BF03215519. [CrossRef] [Google Scholar]
39. Grisel R., Weststrate K. , Gluhoi A., Nieuwenhuys B.E. Катализ наночастицами золота. Золотой бюллетень. 2002; 35:39–45. doi: 10.1007/BF03214836. [CrossRef] [Google Scholar]
40. Hussain A., Ferre C.D., Gracia J., Nieuwenhuys B.E., Niemantsverdriet J.W. DFT-исследование адсорбции CO и NO на золотых поверхностях с низким показателем преломления и ступенчатых поверхностях. Серф. науч. 2009 г.;603:2734–2741. doi: 10.1016/j.susc.2009.07.023. [CrossRef] [Google Scholar]
41. Davis S.P., Abrams M.C., Brauet J.W. Фурье-спектроскопия. Академическая пресса; Нью-Йорк, штат Нью-Йорк, США: Лондон, Великобритания: 2001. с. 261. [Google Scholar]
42. Дойен Г., Эртль Г. Теория хемосорбции монооксида углерода на переходных металлах. Серф. науч. 1974; 43: 197–229. doi: 10.1016/0039-6028(74)90228-3. [CrossRef] [Google Scholar]
43. Hussain A., Muller A., Nieuwenhuys B.E., Gracia J., Niemantsverdriet J. (Hans) Две поверхности золота и кластер с замечательной реакционной способностью для окисления CO, исследование теории функционала плотности . Вершина. Катал. 2011;54:415–423. doi: 10.1007/s11244-011-9672-3. [CrossRef] [Google Scholar]
44. Ван Ю.-Г., Юн Ю., Глезаку В.-А., Ли Дж., Руссо Р. Роль восстанавливаемого переноса заряда кластера оксид-металл в каталитических процессах: Новое понимание каталитического механизма окисления CO на Au/TiO2 из молекулярной динамики ab Initio. Варенье. хим. соц. 2013; 135:10673–10683. doi: 10.1021/ja402063v. [PubMed] [CrossRef] [Google Scholar]
45. Camellone M.F., Kowalski P.M., Marx D. Идеальные, дефектные и промотированные золотом рутиловые поверхности TiO 2 (110), взаимодействующие с CO, h3 и h3O: структуры, энергии , термодинамика и динамика из PBE +U. физ. Ред. Б. 2011; 84:035413. doi: 10.1103/PhysRevB.84.035413. [Перекрестная ссылка] [Академия Google]
46. Harding C., Habibpour V., Kunz S., Farnbacher A.N.-S., Heiz U., Yoon B., Landman U. Контроль и управление нанокатализом золота: влияние толщины и состава оксида металла. Варенье. хим. соц. 2009; 131: 538–548. doi: 10.1021/ja804893b. [PubMed] [CrossRef] [Google Scholar]
Улучшенная антибактериальная активность трехмерных морщинистых пленок оксида графена, изготовленных из необратимо усаживаемых полимерных подложек с памятью формы
Улучшенная антибактериальная активность трехмерных складчатых пленок оксида графена, выполненных с использованием необратимо усаживаемых полимерных подложек с памятью формы†
* Соответствующие авторы
и Инженерно-исследовательский центр технологий экстрасенсорного восприятия с цветовой модуляцией, Пусанский национальный университет, Пусан 46241, Республика Корея
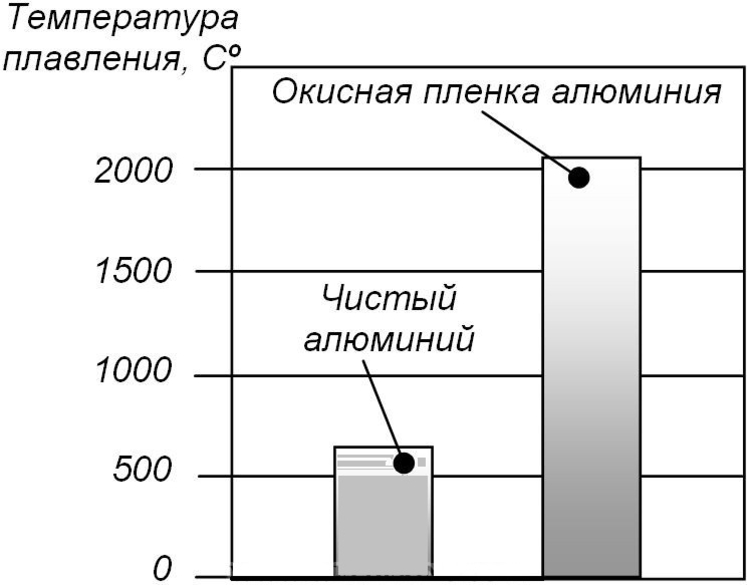
б Кафедра когно-мехатроники, кафедра оптики и мехатроники, Колледж нанонауки и нанотехнологий, Пусанский национальный университет, Пусан 46241, Республика Корея
Аннотация
Растущая лекарственная устойчивость бактерий и возникающие инфекционные заболевания создают серьезные проблемы для сохранения общественного здоровья. Недавно внимание привлекли исследования превосходной антибактериальной активности с использованием уникальных механических, электрических и поверхностных свойств материалов на основе графена. Антибактериальный механизм этих материалов известен как физическое повреждение, вызванное прямым контактом между острыми краями графена и бактериальной мембраной, и дополнительными химическими взаимодействиями, вызывающими окислительный стресс за счет переноса заряда и образования активных форм кислорода.
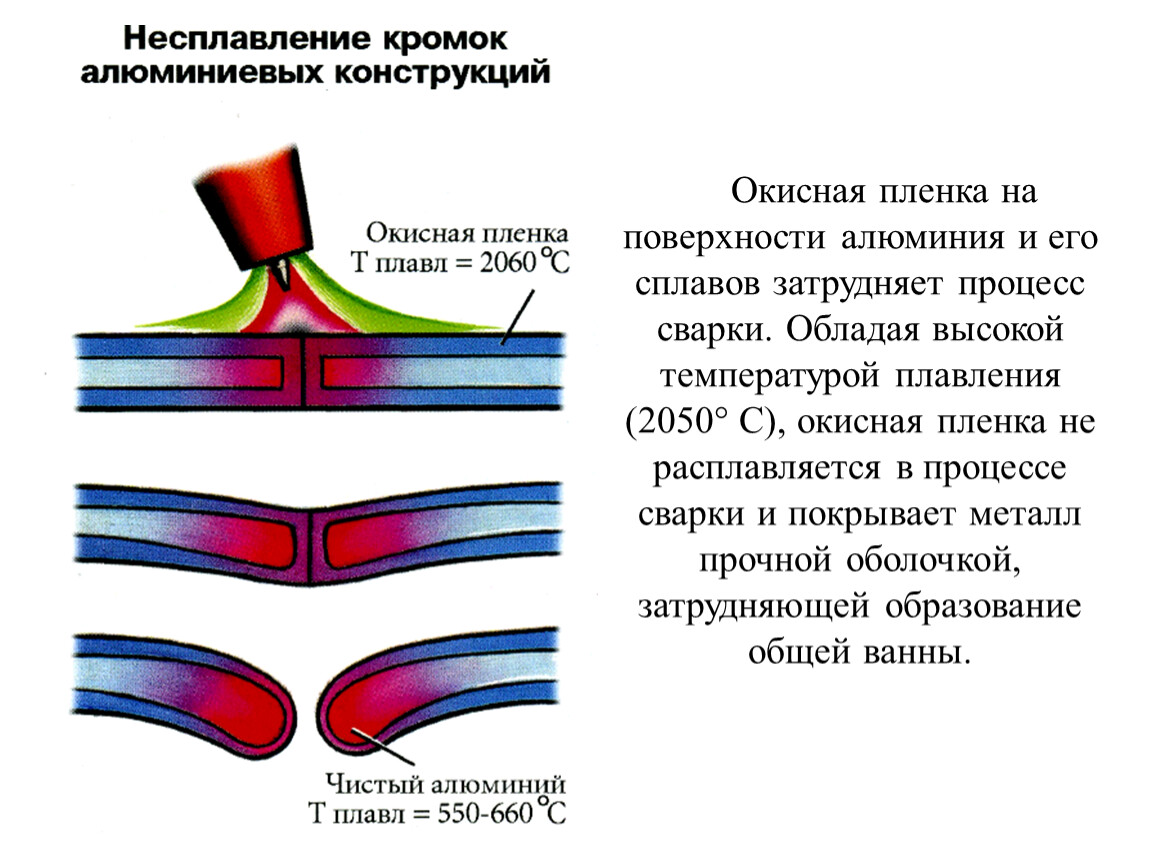