В95 ( 1950 ) — Проминвест-НН
Марка : | В95 ( другое обозначение 1950 ) |
Классификация : | Алюминиевый деформируемый сплав |
Применение: | для изготовления высоконагруженных конструкций, работающих в основном на сжатие |
Зарубежные аналоги: | Известны |
Химический состав в % материала В95
ГОСТ 4784 — 97
Fe | Si | Mn | Ni | Cr | Ti | Al | Cu | Mg | Zn | Примесей |
до 0.![]() |
до 0.5 | 0.2 — 0.6 | до 0.1 | 0.1 — 0.25 | до 0.05 | 86.3 — 91.5 | 1.4 — 2 | 1.8 — 2.8 | 5 — 7 | прочие, каждая 0.05; всего 0.1 |
Механические свойства при Т=20oС материала В95 .
Сортамент | Размер | Напр. | sв | sT | d5 | y | KCU | Термообр.![]() |
— | мм | — | МПа | МПа | % | % | кДж / м2 | — |
Трубы, ГОСТ 18482-79 | 490-510 | 375-400 | 5-7 | |||||
Пруток, ГОСТ 21488-97 | 490-530 | 390-420 | 4-6 | Закалка и искуственное старение | ||||
Пруток, высокой прочности, ГОСТ 51834-2001 | 550-570 | 480-490 | 6 | Закалка и искуственное старение | ||||
Лента отожжен.![]() |
245 | 10 | ||||||
Профили отожжен., ГОСТ 8617-81 | 275 | 10 | ||||||
Профили, ГОСТ 8617-81 | 510-520 | 451-461 | 6 | |||||
Плита, ГОСТ 17232-99 | 470-490 | 390-410 | 2-4 | Закалка и искуственное старение |
Твердость В95 , | HB 10 -1 = 125 МПа |
Твердость В95 после закалки и старения , | HB 10 |
Физические свойства материала В95 .
T | E 10— 5 | a 10 6 | l | r | C | R 10 9 |
Град | МПа | 1/Град | Вт/(м·град) | кг/м3 | Дж/(кг·град) | Ом·м |
20 | 0.74 | 2850 | ||||
100 | 23.2 |
Зарубежные аналоги материала В95
Внимание! Указаны как точные, так и ближайшие аналоги.
США | Германия | Япония | Франция | Англия | Евросоюз | Италия | Польша | Чехия | Австрия | Швейцария | Inter | ||||||
— | DIN,WNr | JIS | AFNOR | BS | EN | UNI | PN | CSN | ONORM | ISO | |||||||
|
|
|
характеристики и расшифовка, применение и свойства стали
Страна | Стандарт | Описание | ||||||||||
---|---|---|---|---|---|---|---|---|---|---|---|---|
Россия | ГОСТ 4784-97 | Алюминий и сплавы алюминиевые деформируемые.![]() | ||||||||||
Россия | ГОСТ 8617-81 | Профили прессованные из алюминия и алюминиевых сплавов. Технические условия | ||||||||||
Россия | ГОСТ 13726-97 | Ленты из алюминия и алюминиевых сплавов. Технические условия | ||||||||||
Россия | ГОСТ 17232-99 | Плиты из алюминия и алюминиевых сплавов.![]() | ||||||||||
Россия | ГОСТ 18482-79 | Трубы прессованные из алюминия и алюминиевых сплавов. Технические условия | ||||||||||
Россия | ГОСТ 21488-97 | |||||||||||
Россия | ГОСТ Р 51834-2001 | Прутки прессованные из алюминиевых сплавов высокой прочности и повышенной пластичности.![]() |
Алюминий и алюминиевые сплавы. Химический состав. ГОСТ 4784-97.
Этот стандарт распространяется на алюминий и деформируемые алюминиевые сплавы, предназначенные для изготовления полуфабрикатов (лент в рулонах, листов, кругов-дисков, плит, полос, прутков, профилей, шин, труб, проволоки, поковок и штампованных поковок) методом горячей или холодной деформации, а также слябов и слитков.
Марки и химический состав алюминия
* ГОСТ 1131, ГОСТ 8617, ГОСТ 15176, ГОСТ 17232, ГОСТ 18475, ГОСТ 18482, ГОСТ 21488, ГОСТ 22233, ГОСТ 23786.
Алюминиевые сплавы систем алюминий-медь-магний и алюминий-медь-марганец
*ГОСТ 1131, ГОСТ 8617, ГОСТ 15176, ГОСТ 17232, ГОСТ 18475, ГОСТ 18482, ГОСТ 21488, ГОСТ 22233, ГОСТ 23786
Алюминиевые сплавы системы алюминий-марганец
* ГОСТ 1131, ГОСТ 8617, ГОСТ 15176, ГОСТ 17232, ГОСТ 18475, ГОСТ 18482, ГОСТ 21488, ГОСТ 22233, ГОСТ 23786.
Алюминиевые сплавы системы алюминий-магний
* ГОСТ 1131, ГОСТ 8617, ГОСТ 15176, ГОСТ 17232, ГОСТ 18475, ГОСТ 18482, ГОСТ 21488, ГОСТ 22233, ГОСТ 23786
Алюминиевые сплавы системы алюминий-магний-кремний
* ГОСТ 1131, ГОСТ 8617, ГОСТ 15176, ГОСТ 17232, ГОСТ 18475, ГОСТ 18482, ГОСТ 21488, ГОСТ 22233, ГОСТ 23786
Алюминиевые сплавы системы алюминий-цинк-магний
* ГОСТ 1131, ГОСТ 8617, ГОСТ 15176, ГОСТ 17232, ГОСТ 18475, ГОСТ 18482, ГОСТ 21488, ГОСТ 22233, ГОСТ 23786
Сплавы, предназначенные для изготовления проволоки для холодной высадки
|
Деформируемые алюминиевые сплавы по ГОСТ 4784-97 – aluminium-guide.com
Кроме него отношение к химическому составу деформируемых сплавов имеют еще два стандарта:
- ГОСТ 1131-76 на сплавы алюминиевые деформируемые в чушках
- ГОСТ 11069-2001 на алюминий первичный в чушках.
Чушки из первичного алюминия и деформируемых сплавов переплавляют и получают слитки, пригодные для обработки горячей или холодной деформацией.
Марки алюминия и алюминиевых сплавов
Будем для удобства в наименовании алюминиевых сплавов опускать слово «марка», например, «алюминиевый сплав АД33», а не «алюминиевый сплав марки АД33». На мой взгляд, при наименовании сплавов слово «марка» представляется совершенно излишним – совершенно достаточно слова “сплав”.
Чтобы различать различные варианты чистого алюминия применяют термин “марка алюминия”, например, марка алюминия АД00. В этом случае это полезно, потому что марки алюминия не являются по определению алюминиевыми сплавами.
В стандартах стран СНГ применяет три вида обозначений марок алюминия и алюминиевых сплавов: традиционные бессистемные буквенно-цифровые и системные цифровые, а также международные цифровые и химические для имеющихся международных аналогов. Например, для сплава Д1 это: Д1, 1110, AlCu4MgSi и 2017.
Обозначения алюминиевых сплавов
Чисто цифровые обозначения были введены в конце шестидесятых прошлого века и были задуманы как часть общей системы обозначений всех сплавов всех металлов. Первая цифра 1 была закреплена за алюминиевыми сплавами. Вторая цифра должна обозначать систему легирования. Тогда первые две цифры, судя по ГОСТ 4784, обозначают алюминиевые сплавы различных систем легирования, например:
- 10хх – алюминий технический;
- 11хх – сплавы алюминиевые системы Al-Cu-Mg;
- 12хх – сплавы алюминевые системы Al-Cu-Mn;
- 13хх – сплавы алюминевые системы Al-Mg-Si;
- 14хх – сплавы алюминевые системы Al-Mn;
- 15хх – сплавы алюминевые системы Al-Mg;
- 19хх – сплавы системы Al-Zn-Mg.
Последние две цифры определяют порядковый номер сплава внутри конкретной системы, причем, как будто бы, нечетные числа должны обозначать деформируемые сплавы, а четные – литейные. Однако в ГОСТ 1583-93 на литейные алюминиевые сплавы никаких следов таких цифровых обозначений не видно.
По-существу, эта цифровая система обозначений так полностью и не прижилась и мало употребляется. Большинство сплавов обозначают «старыми», бессистемными буквенно-цифровыми обозначениями, а стандарты, например ГОСТ 4784, дублируют оба варианта. Правда, некоторые сплавы имеют только одно, цифровое обозначение, например, сплав 1105, который применяется для изготовления лент и у которого нет ни «старого» обозначения, ни “официального” международного аналога.
Деформируемые сплавы: ГОСТ 4784-97
ГОСТ 4784-97 распространяется на алюминий и деформируемые алюминиевые сплавы, предназначенные для изготовления полуфабрикатов (лент в рулонах, листов, плит, полос, прутков, профилей, шин, труб, проволоки, поковок и штамповок) методом горячей или холодной деформации, а также слябов и слитков для дальнейшей деформационной переработки.
Железо и кремний являются неизбежными постоянными примесями в алюминии и алюминиевых сплавах. Они образуют с алюминием тройные химические соединения, которые, особенно, если они находятся на границах зерен, снижают пластичность алюминия. Поэтому стандарт требует, чтобы в марках алюминия, а также сплаве АМцС, содержание железа было больше чем кремния.
ГОСТ 4784 относит к деформируемым сплавам легированный алюминий с суммарным содержанием легирующих элементов и примесей более 1,0 %. Таблица ниже представляет собой обзор сплавов ГОСТ 4784. Для большей ясности опущены специфические сварочные сплавы и варианты сплавов для проволоки для холодной высадки.
Мягкие сплавы
Марки алюминия (серия 1ххх)
Содержание примесей (или легирующих элементов) не более 1,00 %.
Алюминиевые сплавы Al-Mn (серия 3ххх)
Термически неупрочняемые сплавы.
(Заметим, что мы применяем слово “неупрочняемые” со слитным написанием частицы “не”. Это слово в данном случае – прилагательное, а не причастие. Прилагательные пишутся с частицей “не” слитно, а вот причастия – раздельно. Это мы помним со школьной скамьи. 🙂 )
Интересно, что эта система формально имеет соединение Al6Mg с переменной растворимостью и ее сплавы должны бы быть термически упрочняемыми. Однако, оказывается, в присутствии неизбежной примеси – железа – вместо растворимой фазы образуется нерастворимое в алюминии соединение Al6(Mn, Fe). Марганец, в отличие от других легирующих элементов, не ухудшает, а улучшает коррозионную стойкость сплава. Поэтому эти сплавы превосходят технический алюминий и по прочности, и коррозионной стойкости.
Сплавов этой системы в стандарте не так уж много:
- ММ,
- АМц,
- АМцС
- Д12.
Все они применяются, в основном, в виде листов и лент в различных нагартованных состояниях.
Обозначения сплавов этой системы пример полной бессистемности (извините за каламбур!) обозначений сплавов в наших стандартах. Похоже на тест для оценки IQ: “Д1, Д16, Д18, Д19 – дюралюмины. Является ли сплав Д12 также дюралюмином?” Правильный ответ – нет.
Умеренно прочные алюминиевые сплавы
Алюминиевые сплавы Al-Mg(серия 5ххх)
Термически не упрочняемые.
Магний в количестве до 6 % дает упрочнение твердого раствора сплава и высокую эффективность деформационного упрочнения. Поэтому сплавы серии 5ххх имеют довольно высокие прочностные свойства. Эти сплавы широко имеют хорошую коррозионную стойкость, особенно сопротивление коррозии в морской воде и морской атмосфере, и поэтому широко применяются в судостроении, в основном в виде листов. Из этих сплавов изготавливают штампованные детали корпуса и шасси автомобилей благодаря хорошей комбинации их прочности и формуемости.
Алюминиевые сплавы Al-Mg-Si (серия 6ххх)
Эти сплавы иногда (только у нас) называют «авиалями».
Упрочняющей фазой является соединение Mg2Si.
Алюминиевый сплав АД31 – полный аналог «американского» сплава 6063 и, частично, «европейского» сплава 6060. Соотношение среднего содержания кремния и магния в нем близко к стехиометрическому соотношению 1:1,73 для соединения Mg2Si.
- АД31 (6060/6063) – самый популярный промышленный алюминиевый сплав. Широко применяется для изготовления алюминиевых профилей для строительных ограждающих конструкций (окон, дверей, фасадов) и других, как правило, не несущих конструкций.
- Алюминиевый сплав АД33 – аналог сплава 6061. Большее содержание магния и кремния, чем у АД31 (кремний в избытке), а также добавки меди. Более прочный, чем АД31. Применяется в несущих строительных конструкциях.
- Алюминиевый сплав АД35 – аналог сплава 6082. По сравнению со сплавом АД33 магния почти столько же, как и у сплава АД33, а кремния раза в полтора больше и дополнительно до 1 % марганца. Поэтому сплав АД35 еще более прочный, чем АД33. Применяется в несущих строительных конструкциях.
Твердые алюминиевые сплавы
Серия 2ххх – Алюминиевые сплавы Al-Cu-Mg и Al-Cu-Mn
Термически упрочняемые сплавы.
Так называемые дуралюмины или дюралюмины. В зависимости от содержания меди и магния, а также соотношения их концентраций, в них могут образовываться различные упрочняющие фазы: двойные или тройные соединения алюминия с медью, магнием и марганцем.
- Алюминиевый сплав Д1 – «классический», нормальный дюралюминий с упрочняющей фазой CuAl2.
- Сплав Д16 – более прочный, так называемый «супердюралюмин», по сравнению с Д1 содержит повышенное количество магния (в среднем 1,5 %). Поэтому основной упрочняющей фазой у него является уже тройная фаза CuMgAl2, что и дает более высокую прочность.
Буква Д не обязательно означает “дюралюминий, дюраль”, как это может показаться. Существует алюминиево-марганцевый сплав Д12 – мягкий и пластичный.
Прочность дюралюминиев зависит от вида полуфабриката: в прутках больше, в листах – меньше. Предел прочности нормального листового Д1 достигает 410 МПа, а листового Д16 – 440 МПа.
- Алюминиевый сплав Д18 специально предназначен для заклепок, он содержит пониженное количество меди и магния и поэтому имеет существенно более низкую прочность, но и более высокую пластичность, чем, скажем, дюралюминий Д1.
- Алюминиевый сплав В65 предназначен для заклепок, которые работают при температуре не выше 100 °С.
- Алюминиевые сплавы АК (АК4, АК6 и АК8) – близкие «родственники» дюралюминия — предназначены для поковок и штамповок. Буква К как раз и обозначает: Ковочный.
Серия 7ххх – Алюминиевые сплавы Al-Zn-Cu-Mg
Термически упрочняемые сплавы.
Включают самый прочный алюминиевый сплав – сплав В95. Известен еще более прочный алюминиевый сплав – В96, но он не включен в ГОСТ 4784-97.
- Алюминиевый сплав В95 имеет содержание цинка от 5 до 7 %, магния от 1,8 до 2,8 % и меди от 1,4 до 2 % при пределе прочности до 600 МПа. Сплав В96 имеет прочность под 700 МПа при содержании цинка от 8 до 9 % и увеличенном содержании магния и меди.
- Алюминиевые сплавы 1915 и 1925 удобны тем, что являются, так сказать, самозакаливающимися. Их прочность мало зависят от вида закалочной среды (вода, воздух). Поэтому при прессовании из них профилей с толщиной полок до 10 мм их охлаждают на воздухе.
Старение проводят как при комнатной, так и при повышенных температурах.
Источники:
ГОСТ 4784-97 Алюминий и сплавы алюминиевые деформируемые
Гуляев А.П. Металловедение. М: Металлургия, 1986.
Дюралевая плита д16, д16т, д16б
Где применяется дюралевая плита и чем она отличается от листов из дюраля
Различие – в толщине проката. Листы поставляются толщиной от 0,3 до 10,5 мм, плиты – от 11 до 200 мм. Сортамент и технические условия дюралевых листов регламентируются ГОСТ 21631-76, плит – ГОСТ 17232-99. Что качается применения. Плиты – полуфабрикат дли производства большой номенклатуры изделий методами штамповки, прессования ковки и т.д. Плиты поставляются без термической обработки, но по химическому составу и наличию плакирующего слоя полностью отвечают требованиям конечного изделия.
Помогите расшифровать маркировку и основные параметры плит из дюралюмина
Дюралевые плиты изготавливаются из сплавов системы Al-Cu-Mg с дополнительным легированием марганцем. Перечень марок регламентируется ГОСТ 4784-97. Толщина плит — от 11 до 200 мм, ширина — от 1200 до 2000 мм, длина – нормированная от 2000 до 8000 мм, либо не нормированная.
Плиты могут плакироваться (покрываться технически чистым алюминием) для повышения коррозионных свойств или с технологическими целями (базовое исполнение – без плакировки).
Состояние поставки: без термической обработки. При этом свойства материала контролируются по образцам, которые в соответствии с ГОСТ 17232-99, должны пройти весь цикл закалки и старения.
Точность изготовления может быть нормальной (базовой) или повышенной. Маркировка дюралевых плит достаточна проста, например, для плиты толщиной 40 мм, шириной 1000 мм и длиной 2000 мм, изготовленную из сплава Д16 с технологической плакировкой, нормальной точности изготовления:Плита Д16.Б. 40х1000х2000 ГОСТ 17232-99.
Чем отличаются сплавы Д16, Д16Т и Д16Б в маркировке плит
Все перечисленные марки – это один сплав дюралюмин Д16, содержащий согласно ГОСТ 4784-97 кроме алюминия 3,8-4,9% Cu; 1,2-1,8% Mg; 0,3-0,9% Mn. Отличие в обработке сплава. В частности, маркировка «плита Д16» указывает только на состав сплава. Плита Д16Т – не корректная маркировка, т.к. индекс «Т» соответствует термически обработанному состоянию (закалка + естественное старение), а плиты поставляются без термообработки.
Индексы «А» и «Б» указывают на наличие плакирования, нормального и технологического соответственно. Т.е. маркировка «плита Д16Б» соответствует дюралюмину с технологической плакировкой.
Что такое плакирование алюминиевых плит
В зависимости от требований заказчика, дюралевую плиту купить можно с разным способом изготовления. В соответствии с требованиями ГОСТ 17232-99, плиты могут быть плакированными и неплакированными. Плакирование (плакировка) – приварка в процессе горячей пластической деформации покрытия на поверхность плиты. В качестве плакирующего слоя применяют технически чистый алюминий марки АД1пл с содержанием примесей не более 0,7%. Для плит применяют нормальное и технологическое плакирование. Нормальное (толщиной 2-4% от толщины листа) служит для повышения коррозионной стойкости дуралюминов типа Д16. Чистый алюминий образует тонкую защитную пленку оксида, надежно предохраняющую лист от коррозии.
Цель технологического плакирования (1,5% толщины) – повышение технологичности при горячей прокатке с большими обжатиями. Технологическое плакирование коррозионную стойкость практически не повышает.
При плакировании к маркировке добавляются индексы «А» – нормальное и «Б» – технологическое плакирование.
В чем особенности расчета теоретической массы дюралевых плит
В связи с многообразием марок алюминиевых сплавов, ГОСТ 17232-99 приводит расчетную массу погонного метра плиты разной ширины, исходя из плотности сплава В95 – 2,85 г/м3. Для расчета массы погонного метра конкретного сплава приложена таблица пересчета плотности. Например, для дюралюмина Д16 переводной коэффициент – 0,976.
Алюминиевый сплав — Судовой металлопрокат
Применение: |
|
В95 / Алюминиевый деформируемый сплав / Алюминий, сплав алюминия / Материалы / Информация / ТехноСтали
-основа. процентное содержание
Сортамент | Размер | Напр. | sв | sT | d5 | y | KCU | Термообр. |
— | мм | — | МПа | МПа | % | % | кДж / м2 | — |
Трубы, ГОСТ 18482-79 | 490-510 | 375-400 | 5-7 | |||||
Пруток, ГОСТ 21488-97 | 490-530 | 390-420 | 4-6 | Закалка и искуственное старение | ||||
Пруток, высокой прочности, ГОСТ 51834-2001 | 550-570 | 480-490 | 6 | Закалка и искуственное старение | ||||
Лента отожжен.![]() | 245 | 10 | ||||||
Профили отожжен., ГОСТ 8617-81 | 275 | 10 | ||||||
Профили, ГОСТ 8617-81 | 510-520 | 451-461 | 6 | |||||
Плита, ГОСТ 17232-99 | 470-490 | 390-410 | 2-4 | Закалка и искуственное старение | ||||
Механические свойства : | ||||||||
sв | -Предел кратковременной прочности , [МПа] | |||||||
sT | -Предел пропорциональности (предел текучести для остаточной деформации), [МПа] | |||||||
d5 | -Относительное удлинение при разрыве , [ % ] | |||||||
y | -Относительное сужение , [ % ] | |||||||
KCU | -Ударная вязкость , [ кДж / м2] | |||||||
HB | -Твердость по Бринеллю , [МПа] | |||||||
Физические свойства : | ||||||||
T | -Температура, при которой получены данные свойства , [Град] | |||||||
E | -Модуль упругости первого рода , [МПа] | |||||||
a | -Коэффициент температурного (линейного) расширения (диапазон 20o-T ) , [1/Град] | |||||||
l | -Коэффициент теплопроводности (теплоемкость материала) , [Вт/(м·град)] | |||||||
r | -Плотность материала , [кг/м3] | |||||||
C | -Удельная теплоемкость материала (диапазон 20o-T ), [Дж/(кг·град)] | |||||||
R | -Удельное электросопротивление, [Ом·м] |
B95 / Aloro
Для изготовления высоконагруженных конструкций, работающих преимущественно на сжатие
Классификация
Страна | Раздел | Категория |
---|---|---|
СНГ, Россия, Украина | Алюминий, алюминиевые сплавы | Кованые алюминиевые сплавы |
Химический состав
Стандартный | Fe,% | Si,% | Мг,% | Mn,% | Cr,% | Ti,% | Cu,% | Zn,% | Ni,% | Al,% |
---|---|---|---|---|---|---|---|---|---|---|
ГОСТ 4784-97 | <0.![]() | |||||||||
20 | 74 | 2850 | ||||||||
100 | 23,2 |
Механические свойства при 20 ° C
Прокат | Стандартный | Размер, мм | Напряжение | Классификаторы | $$ \ sigma _ {U} $$, $$ МПа $$ | $$ \ sigma_ {P} $$, $$ МПа $$ | $$ \ epsilon_L $$,% | Лечение |
---|---|---|---|---|---|---|---|---|
Труба | 490–510 | 375–400 | 5–7 | |||||
Круглый | ГОСТ 21488-97 | 490–530 | 390–420 | 4–6 | Закалка и искусственное старение | |||
Круглый | высокая прочность | 550–570 | 480–490 | 6 | Закалка и искусственное старение | |||
Лента | отжиг | 245 | 10 | |||||
Профиль | отжиг | 275 | 10 | |||||
Профиль | 510–520 | 451–461 | 6 | |||||
Лист | 470–490 | 390–410 | 2–4 | Закалка и искусственное старение |
Число твердости по Бринеллю
Прокат | Стандартный | Классификаторы | Значение, HBW |
---|---|---|---|
Сплав | 125 | ||
Сплав | Закалка, старение | 150 |
Аналоги
Стандарты
Описание химических элементов
Элемент | Единицы измерения | Описание |
---|---|---|
Fe | % | Утюг |
Si | % | Кремний |
мг | % | Магний |
Мн | % | Марганец |
Cr | % | Хром |
Ti | % | Титан |
Cu | % | Медь |
Zn | % | Цинк |
Ni | % | Никель |
Al | % | Алюминий |
Описание физических характеристик
Параметр | Единицы измерения | Описание |
---|---|---|
$$ E \ cdot 10 ^ {9} $$ | $$ МПа $$ | Модуль упругости |
$$ \ alpha \ cdot 10 ^ {6} $$ | $$ K ^ {- 1} $$ | Коэффициент теплового (линейного) расширения (диапазон 20 ° C – T) |
$$ | $$ \ frac {kg} {m ^ 3} $$ | Плотность материала |
Описание механических свойств
Параметр | Единицы измерения | Описание |
---|---|---|
$$ \ sigma _ {U} $$ | $$ МПа $$ | Предел прочности на разрыв |
$$ \ sigma_ {P} $$ | $$ МПа $$ | Предел пропорциональности |
$$ \ epsilon_L $$ | % | Удлинение при разрыве (продольное) |
Исследование структуры и свойств длинномерных широких листов алюминиевого сплава В95пчТ2
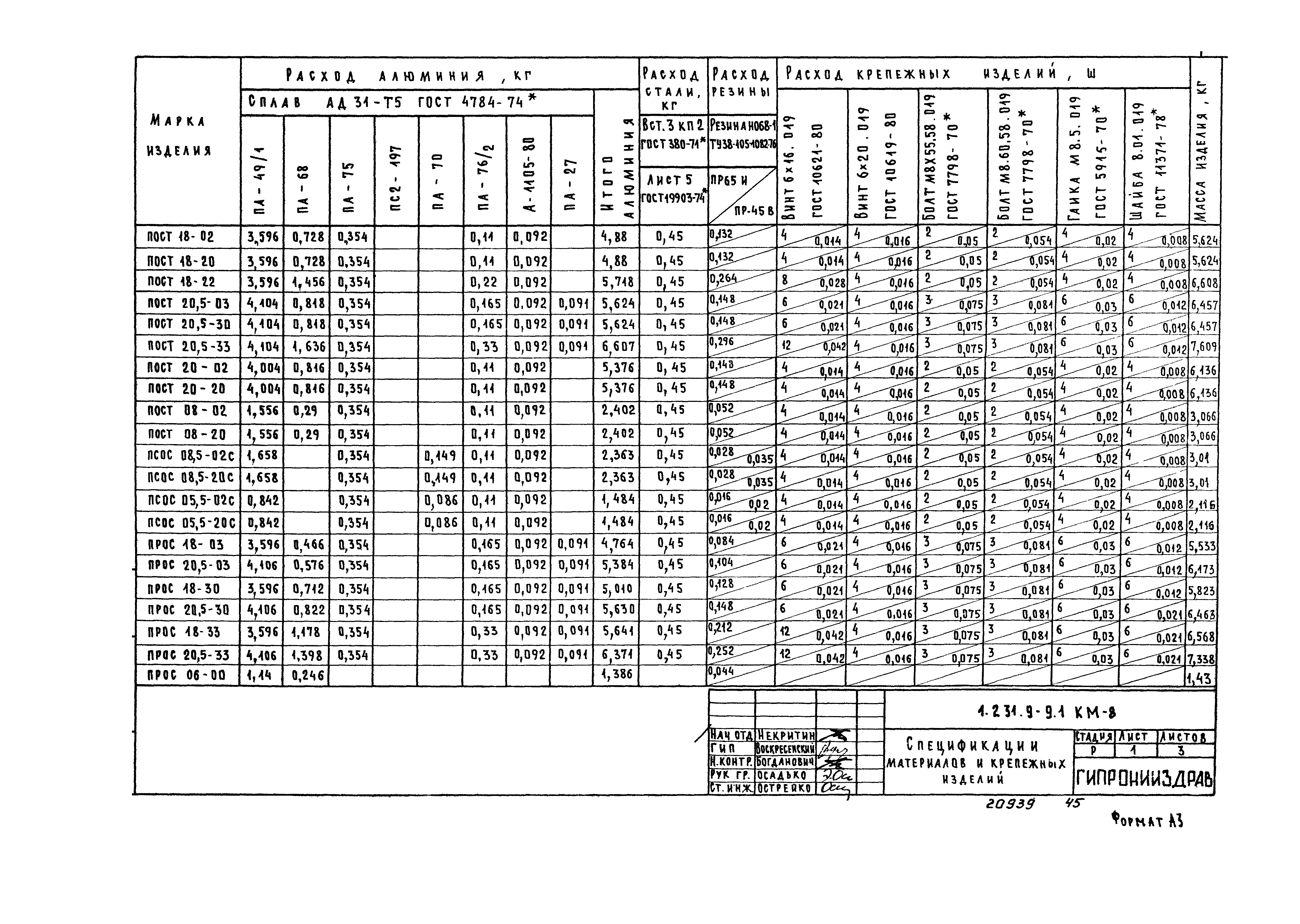
Фридляндер И. Н., Сенаторова О. Г., Ткаченко Е. А. Высокопрочные сплавы системы Al — Zn — Mg — Cu // Энциклопедия , т. 9, с. II-3, «Цветные металлы и сплавы» , Металлургия (2001), с. 94 — 128.
И. Н. Фридляндер, О. Г. Сенаторова, Е. А. Ткаченко, И. И. Молостова, «Развитие и применение высокопрочных сплавов системы Al — Zn — Mg — Cu в авиакосмической технике // Авиационные материалы , Авиационные материалы, , ВИАМ, 2007, с.155 — 163.
Каблов Е. Н. К 80-летию ВНИИ авиационных материалов, Деформация. Razrush. Матер. , № 6, 17–19 (2012).
Фридляндер И. Н., Сенаторова О. Г. Разработка и применение высокопрочных сплавов Al — Zn — Mg — Cu // В сб .: Proc. of ICAA-5, France (1996), pp. 1813 — 1815.
Каблов Е.Н. «Инновационные разработки ФГУП« ВИАМ »ГНЦ РФ по реализации« Стратегических направлений разработки материалов и технологии обработки материалов на период до 2030 года », Авиац. Матер. Технол. , № 1, 3 — 33 (2015) (https://doi.org/10.18577/2071-9140-2015-0-1-3-33).
Антипов В.В. Стратегии разработки сплавов титана, магния, бериллия и алюминия. Матер. Технол. , № S, 157 — 167 (2012).
Фридляндер И. Н., «К 90-летию. Высокопрочные алюминиевые сплавы с цинком, магнием и медью », Металловед. Срок. Обраб. Встретились. , № 9, 11–13 (2003).
Фридляндер И. Н. Алюминиевые сплавы в самолетостроении в период с 1970 по 2015 гг. // Технол. Легк. Сплавов , № 4, 12 — 17 (2002).
Каблов Е. Н. Стратегические направления развития материалов и технологий их обработки на период до 2030 г. // Авиац. Матер. Технол. , № 5, 7 — 17 (2012).
Каблов Е. Н. Аэрокосмическое материаловедение. В кн .: Все материалы, Энциклопедический справочник , Москва, ВИАМ, 2008, с.2 — 14.
Антипов В.В. Перспективы развития алюминиевых, магниевых и титановых сплавов для авиакосмической техники. Матер. Технол. , No. S, 186 — 194 (2017) (https://doi.org/10.18577/2071-9140-2017-0-S-186-194).
О.Г. Сенаторова, А.Ю. Сухих, В.В. Сидельников и др. «Разработка и перспективы применения высокопрочных алюминиевых сплавов для проката полуфабрикатов», Технол. Легк. Сплавов , №4, 28 — 33 (2002).
ОСТ–83 Полуфабрикаты из алюминиевых деформируемых сплавов. Механические и коррозионные свойства полуфабрикатов, выдержанных в условиях размягчения.
Милевская Т.В., Рущиц С.В., Ткаченко Е.А., Антонов С.М. Деформационное поведение высокопрочных алюминиевых сплавов в условиях горячей деформации. Матер. Технол. , No. 2, 3 — 9 (2015) (https: // doi.org / 10.18577 / 2071-9140-2015-0-2-3-9).
И. Н. Фридляндер, Алюминиевые деформируемые конструкционные сплавы , Металлургия, Москва (1979).
ТР 50-31-70, Гомогенизация плит из алюминиевого сплава , ВИЛС, Москва (1970).
И. Н. Фридляндер, Металловедение алюминиевых сплавов , Наука, Москва (1985).
Белов Н.А., Фазовый состав промышленных и перспективных алюминиевых сплавов , Изд.Дом МИСиС, Москва (2010).
Иванов А.Л., Сенаторова О.Г., Митасов М.М. и др. Кинетика охлаждения деталей из листового металла из алюминиевых сплавов при малодеформационной закалке в полимерной среде // Металловедение. Срок. Обраб. Мет., № 11 (749), 31 — 36 (2017).
Нечайкина Т.А., Блинова Н.Е., Иванов А.Л. и др. Исследование структуры и механических свойств катаных колец из сплава В95очТ2 в условиях гомогенизации и закалки // Труды ВИАМ: Электрон.Науч. Тех. Ж. , No. 10 (70), 27 — 36 (2018) (URL: http: www.viam-works.ru (дата обращения: 30 апреля 2019 г.), https://doi.org/10.18577/2307-6046 -2018-0-10-27-36).
Арчакова З. Н., Балахонцев Г. А., Басова И. Г. и др., Алюминиевые сплавы. Структура и свойства полуфабрикатов из алюминиевых сплавов: Справочник , Металлургия, Москва (1974).
В. М. Белецкий, Г. А. Кривов, Алюминиевые сплавы (состав, свойства, технология, применение): Справочник , Коминтех, Киев (2005).
Алюминиевые сплавы. Физические характеристики алюминия Amg2m расшифровка
— Магний (Al — Mg), который является одним из деформируемых давлением сплавов. Кроме того, этот материал отличается высокой коррозионной стойкостью, пластичностью и хорошей свариваемостью. По прочности он превосходит АМС, но уступает ему по пластичности. Теплопроводность и электропроводность этого материала ниже, чем у алюминиево-марганцевого сплава.
В этой связи интересно продемонстрировать сравнительную гистограмму, которая показывает предел прочности на разрыв и предел текучести различных алюминиевых сплавов. И здесь мы видим, что AMg2 по своим свойствам примерно равен AMg3. Однако коррозионная стойкость AMg2, естественно, выше.
Существенная разница присутствует при увеличении количества магния в сплаве до 4% и выше, что влияет на пластичность и твердость. При увеличении содержания магния в составе пластичность будет снижаться, а прочность увеличиваться до определенных пределов, при которых проявляется хрупкость.
Химический состав
Химический состав AMg2 можно назвать сбалансированным. Содержание магния в нем не превышает 4%, что положительно сказывается на пластичности, коррозионной стойкости и свариваемости этого материала. При этом содержание Mg превышает 2%, что положительно сказывается на прочности сплава.
Благодаря более высокой прочности по сравнению с более чистыми алюминиевыми сплавами, AMg2 чаще используется в качестве материала для оконных и дверных профилей, а также других легких сборных или сварных конструкций.В то же время он легкий и простой в использовании, а также более чистые сплавы.
Физические свойства материала
В таблице ниже показаны физические свойства материала AMg2, полученные при температуре — T. E — модуль упругости. a — коэффициент линейного расширения, l — коэффициент. теплопроводность, r — плотность, C — удельная теплоемкость, R — удельное электрическое сопротивление.
Что производится из алюминия АМг2
Так как АМг2 обладает массой положительных свойств, нарды средней прочности и высокой пластичности, из него изготавливают широкий ассортимент заготовок.От AMg2 продано:
Из них профили в виде уголков пользуются особым спросом ввиду их легкости, хорошей коррозионной стойкости, свариваемости и большей прочности, чем у того же AMC.
Как видно из приведенной ниже таблицы, большинство видов металла из этого материала производятся в обычном состоянии, но также довольно часто используются спекшиеся или отожженные листы и ленты. Нагартинг позволяет добиться большей прочности от этого материала, а отжиг, наоборот, способствует рекристаллизации материала и большей пластичности.
Жесткие листы, вероятно, используются для создания стеновых конструкций, различных панелей, возможно, в холодильных установках. А вот отожженные листы целесообразно применять для изготовления широкого спектра изделий, производимых методом холодной или горячей деформации, в том числе сварных конструкций.
Предлагаем лист алюминия АМг2 без покрытия с гладкой и рифленой поверхностью. Плоский прокат изготавливается по ГОСТ 21631-76. Химический состав алюминиевого сплава марки АМг2 по ГОСТ 4784-74.Виды гофры: алмазная и квинтетная. Широкий размерный ряд. Продажа со склада в Москве или под заказ в кратчайшие сроки.
Сервис
Поставки из деформируемого алюминиевого сплава марки АМг2 осуществляются в листах и рулонах. Выгодные цены на качественный отечественный и зарубежный прокат. Индивидуальный подход к каждому покупателю. Профессиональные услуги по шлифовке, анодированию, гибке и резке алюминиевого листа по размеру. Временная антикоррозионная защита, упаковка, транспортировка и хранение по ГОСТ 9.510-93.
Характеристики
Алюминиевый лист АМг2 обладает хорошей коррозионной стойкостью, пластичностью и свариваемостью. Цифра 2 в маркировке деформируемого сплава указывает на процентное содержание магния.
По состоянию материала:
- лист алюминиевый АМг2М отожженный;
- Лист алюминиевый вулканизированный АМг2Н.
Термическая обработка изменяет структуру материала, его физико-механические свойства. В результате отжига листы АМг2М становятся более пластичными и податливыми.Значительно улучшает удобоукладываемость продукта при нарезке. Для частичного восстановления твердости металла применяется тренировка — прокатка с сжатием 2-5%. Способ холодной обработки для получения листов АМг2Н повышенной прочности. Это снижает пластичность и вязкость материала. Алюминиевый лист АМг2Н2 изготовлен из сплава с отсечкой на одну секунду. Он сочетает в себе хорошие прочность и механические свойства. Алюминиевые листы АМг2ХП изготавливаются из отвержденного и очищенного сплава. Минимальное содержание примесей позволяет улучшить электропроводность полуфабрикатов.
По способу производства:
Матовая отделка с обычными покрытиями. Нормальная точность изготовления по толщине, ширине и длине.
Область применения
Листы АМг2М и АМг2Н используются для изготовления строительных конструкций, деталей транспорта. Изготавливают гидрооборудование, промышленные трубопроводы, футеровку грузовиков, химических сосудов, работающих под давлением.
АЛЮМИНИЕВЫЕ СПЛАВЫ Классификация сплавов Физические свойства Коррозионные свойства Механические свойства Круглый и профильный алюминиевый прокат Плоский алюминий Классификация алюминиевых сплавов. Алюминиевые сплавы условно делятся на литейные (для производства отливок) и деформируемые (для производства проката и поковок). Далее будут рассмотрены только деформируемые сплавы и прокат на их основе. Под прокаткой алюминия подразумевается прокат из алюминиевых сплавов и технического алюминия (А8 — А5, АД0, АД1). Химический состав деформируемых сплавов общего назначения приведен в ГОСТ 4784-97 и ГОСТ 1131. делятся по способу упрочнения : упрочненные давлением (деформацией) и термически упрочненные. Другая классификация основана на ключевых свойствах : сплавы низкой, средней или высокой прочности, высокой пластичности, жаропрочные, кованые и т. Д. В таблице приведены наиболее распространенные деформируемые сплавы с кратким описанием основных свойств. присущие каждой системе. Маркировка производится по ГОСТ 4784-97 и международной классификации ISO 209-1.
Состояние поставки Закаленные под давлением сплавы упрочняются только холодной деформацией (холодной прокаткой или волочением). без термообработки 2) M — отожженный 3) h5 — ежеквартально зафрахтованный 4) h3 — полугарантированный 5) h4 — спекшийся 3/4 6) N — зафрахтованный Полуфабрикаты из термоупрочненные сплавы , упрочненные специальной термообработкой.Он заключается в закалке при определенной температуре и последующей выдержке в течение некоторого времени при другой температуре (старение). Происходящее при этом изменение структуры сплава увеличивает прочность и твердость без потери пластичности. Есть несколько вариантов термической обработки. Наиболее распространены следующие условия поставки термоупрочненных сплавов, отраженные в маркировке проката: 1) не имеет обозначения — после прессования или горячей прокатки без термообработки 2) M — отожженный 3) T — закаленный и естественно состаренный (для максимальной прочности) 4) T1 — закаленный и искусственно состаренный (для максимальной прочности) Для некоторых сплавов термомеханическое упрочнение проводят при закалка проводится после закалки. Данная маркировка условий соответствует Российским ГОСТам. Физические свойства алюминиевых сплавов. Плотность алюминиевых сплавов немного отличается от плотности чистого алюминия (2,7 г / см 3). Она варьируется от 2.От 65 г / см 3 для сплава АМг6 до 2,85 г / см 3 для сплава В95. Легирование практически не влияет на величину модуля упругости и модуля сдвига. Например, модуль упругости упрочненного дюралюминия Д16Т практически равен модулю упругости чистого алюминия А5 ( E = 7100 кгс / мм 2). Однако в связи с тем, что предел текучести сплавов в несколько раз превышает предел текучести чистого алюминия, алюминиевые сплавы уже могут использоваться в качестве конструкционного материала с разным уровнем нагрузок (в зависимости от марки сплава и его состояния). Из-за малой плотности удельные значения прочности на разрыв, предела текучести и модуля упругости (соответствующие значения, разделенные на значение плотности) для прочных алюминиевых сплавов сопоставимы с соответствующими значениями. удельных значений для стали и титановых сплавов. Это позволяет высокопрочным алюминиевым сплавам конкурировать со сталью и титаном, но только до температур, не превышающих 200 C. Большинство алюминиевых сплавов имеют худшую электрическую и теплопроводность, коррозионную стойкость и свариваемость по сравнению с чистым алюминием. В таблице ниже приведены значения твердости, теплопроводности и электропроводности для нескольких сплавов в различных состояниях. Поскольку значения твердости коррелируют со значениями предела текучести и предела прочности, данная таблица дает представление о порядке этих значений. Из таблицы видно, что сплавы с более высокой степенью легирования имеют значительно меньшую электрическую и теплопроводность, эти значения так же существенно зависят от состояния сплава (М, h3, T или T1):
Из таблицы видно, что только сплав АД31 сочетает в себе высокую прочность и высокую электропроводность. Поэтому «мягкие» электрические шины изготавливают из АД0, а «сплошные» — из АД31 (ГОСТ 15176-89). Электропроводность этих шин составляет (в мкОм * м): 0,029 — от AD0 (без термообработки, сразу после прессования) 0,031 — от AD31 (без термообработки, сразу после прессования) 0,035 — от AD31T (после закалки и естественного старения) Теплопроводность многих сплавов (АМг5, Д16Т, В95Т1) вдвое ниже, чем у чистого алюминия, но все же выше, чем у сталей. Коррозионные свойства. Наилучшими коррозионными свойствами обладают сплавы АМц, АМг, АД31, а наихудшими — высокопрочные сплавы Д16, В95, АК. Кроме того, коррозионные свойства термоупрочненных сплавов существенно зависят от условий закалки и старения. Например, сплав Д16 обычно используется в естественно состаренном состоянии (Т). Свариваемость. Сплавы АМц и АМг хорошо свариваются всеми видами сварки. При сварке вальцованного проката в зоне шва происходит отжиг, поэтому прочность шва соответствует прочности основного материала в отожженном состоянии. Из жаропрочных сплавов, воздуховоды, сплав 1915 хорошо свариваются. Сплав 1915 относится к самоотверждающимся, поэтому сварной шов со временем приобретает прочность основного материала.Большинство других сплавов свариваются только точечной сваркой. Механические свойства . Прочность сплавов АМц и АМг увеличивается (а пластичность снижается) с увеличением степени легирования. Термоотверждаемые сплавы допускают упрочнение деталей после их изготовления, если исходный полуфабрикат не подвергался термообработке. Наибольшей прочностью после упрочняющей термообработки (закалки и старения) обладают сплавы Д16, В95, АК6, АК8, АК4-1 (доступны в свободной продаже). Самый распространенный сплав — Д16. При комнатной температуре он уступает многим сплавам по статической прочности, но обладает лучшей структурной прочностью (трещиностойкостью). Обычно применяется в состарившемся естественным образом состоянии (Т).Но выше 80 C его коррозионная стойкость начинает ухудшаться. Для использования сплава при температурах 120-250 С изделия из него подвергают искусственному старению. С повышением температуры прочностные свойства сплавов изменяются в разной степени, что определяет их различную применимость в зависимости от диапазона температур. Из этих сплавов до 120 ° C V95T1 имеет самую высокую прочность и предел текучести.Выше этой температуры он уже уступает сплаву Д16Т. Однако следует учитывать, что B95T1 имеет значительно худшую конструкционную прочность, т.е. низкую трещиностойкость, по сравнению с D16. Кроме того, B95 в состоянии T1 подвержен коррозии под напряжением. Это ограничивает его использование в изделиях, работающих на растяжение. Улучшение коррозионных свойств и значительное улучшение трещиностойкости достигается в изделиях, обработанных в соответствии с Т2 или Т3. При температуре 150-250 ° С большую прочность имеют Д19, АК6, АК8.При высоких температурах (250-300 С) целесообразно использовать другие сплавы — АК4-1, Д20, 1201. Сплавы АК6 и АК8 пластичны при высоких температурах, что позволяет использовать их для изготовления поковок и штамповок. Сплав АК8 отличается большей анизотропией механических свойств, имеет меньшую трещиностойкость, но сваривает лучше, чем АК6. Перечисленные высокопрочные сплавы плохо свариваются и обладают низкой коррозионной стойкостью.Сплав 1915 относится к сварным термоупрочненным сплавам нормальной прочности. Это самозатвердевающий сплав (позволяет закаливать со скоростью естественного охлаждения), что обеспечивает высокую прочность сварного шва. Сплав 1925, не отличаясь от него механическими свойствами, сваривается хуже. Сплавы 1915 и 1925 обладают большей прочностью, чем АМг6, и не уступают ему по характеристикам сварного шва. Они хорошо свариваются, сплавы средней прочности — авиационные (АВ, АД35, АД31, АД33) обладают высокой коррозионной стойкостью. Из алюминия и его сплавов производят все виды проката — фольгу, листы, ленты, пластины, прутки, трубы, проволоку. Следует иметь в виду, что для многих термоупрочненных сплавов существует «эффект прессования» — механические свойства прессованных изделий выше, чем у горячекатаных (т.е. круги имеют лучшие показатели прочности, чем листы). Прутки, профили, трубыПрутки из закаленных сплавов поставляются в состоянии «без термической обработки» или в закаленном состоянии (закалка с последующим естественным или искусственным старением).Прутки из термически неупрочненных сплавов производятся прессованием и поставляются в состоянии «без термической обработки». Общее представление о механических свойствах алюминиевых сплавов дает гистограмма, которая показывает гарантированные характеристики экструдированных стержней при нормальных температурах: Из всего представленного разнообразия в свободной продаже всегда есть прутки из D16, а круги диаметром до 100 мм включительно обычно поставляются в естественно состаренном состоянии (Д16Т). Поскольку алюминиевый сплав Д16 не обладает хорошими антикоррозийными свойствами, желательна дополнительная защита изделий из него путем анодирования или нанесения лакокрасочных покрытий.При эксплуатации при температурах выше 80-100 С проявляется склонность к межкристаллитной коррозии. Необходимость дополнительной защиты от коррозии касается и других высокопрочных сплавов (D1, V95, AK). Прутки из АМц и АМг обладают высокой коррозионной стойкостью, допускают возможность дополнительного формования горячей штамповкой (в диапазоне 510–380 ° С). Широко представлены разнообразные профили из сплава АД31 с различными вариантами термообработки. Их используют для конструкций малой и средней прочности, а также для декоративных изделий. Стержни, трубы и профили из АД31 обладают высокой общей коррозионной стойкостью, не подвержены коррозии под напряжением. Сплав хорошо сваривается точечной, роликовой и аргонодуговой сваркой. Коррозионная стойкость сварного шва такая же, как и у основного материала. Для повышения прочности сварного шва необходима специальная термообработка. Углы изготавливаются в основном из AD31, D16 и AMg2. Трубы изготавливаются из большинства сплавов, показанных на рисунке. Поставляются в ненагреваемом (прессованном) состоянии, закалены и состарены, а также отожжены и отверждены.Параметры их механических свойств примерно соответствуют приведенным на гистограмме. При выборе материала трубы, помимо прочностных характеристик, учитывается ее коррозионная стойкость и свариваемость. Самые доступные трубы от AD31. Наличие кругов, труб и уголков — смотрите на странице сайта «Алюминиевые круги, трубы и уголки» Прокат плоский алюминиевый. Листы общего назначения изготавливаются по ГОСТ 21631-76, ленты — по ГОСТ 13726-97, плиты — по ГОСТ 17232-99. Плакируют листы из сплавов с низкой или низкой коррозионной стойкостью (АМг6, 1105, Д1, Д16, ВД1, В95). Химический состав плакированного сплава обычно соответствует марке AD1, а толщина слоя составляет от 2 до 4% от номинальной толщины листа. Плакирующий слой обеспечивает электрохимическую защиту основного металла от коррозии. Это означает, что защита металла от коррозии обеспечивается даже при наличии механических повреждений защитного слоя (царапин). Маркировка листов включает: обозначение марки сплава + статус поставки + тип покрытия (при наличии). Примеры маркировки: А5 — лист А5 без плакировки и термообработки А5Н2 — лист без гальванического покрытия, полугарантированный АМг5М — лист АМг5 без плакировки, отожженный Д16АТ — лист марки Д16 с нормальным покрытие, закаленное и естественно состаренное. Гистограмма показывает основные характеристики механических свойств листов в различных условиях поставки для наиболее часто используемых марок.Состояние «без термической обработки» не показано. В большинстве случаев предел текучести и предел прочности такого проката близки к соответствующим значениям для отожженного состояния, а пластичность ниже. Пластины производятся в состоянии «без термической обработки». Из рисунка видно, что выпускаемый ассортимент листов дает широкие возможности для выбора материала по прочности, пределу текучести и пластичности с учетом коррозионной стойкости и свариваемости.Для ответственных конструкций из прочных сплавов необходимо учитывать характеристики трещиностойкости и сопротивления усталости. Листы из технического алюминия (АД0, АД1, А5-А7). Консервы и полуклетки используются для изготовления ненагруженных конструкций, резервуаров (в том числе для криогенных температур), требующих высокой коррозионной стойкости и допускающих применение сварки. Листы в мягком состоянии используются для герметизации неразъемных швов. Высокая пластичность отожженных листов позволяет производить изделия глубокой вытяжки. Технический алюминий обладает высокой коррозионной стойкостью во многих средах (см. Страницу «Свойства алюминия»). Однако из-за разного содержания примесей в перечисленных марках их антикоррозионные свойства в некоторых средах все же различаются. Алюминий сваривают всеми способами. Технический алюминий и его сварные соединения обладают высокой коррозионной стойкостью к межкристаллитной, расслаивающей коррозии и не подвержены коррозионному растрескиванию. Помимо листов, изготовленных по ГОСТ 21631-76, в свободной продаже имеются листы, изготовленные по европейскому стандарту с маркировкой 1050А. По химическому составу они соответствуют марке АД0. Листы (и ленты) из сплава 1105. Из-за пониженной коррозионной стойкости изготавливают плакированную. Широко применяется для изоляции теплотрасс, для изготовления легконагруженных деталей, не требующих высоких коррозионных свойств. Листы из сплава АМц . Листы из сплава АМц хорошо деформируются в холодных и горячих условиях. Из-за невысокой прочности (низкого предела текучести) их используют для изготовления только легконагруженных конструкций.Высокая пластичность отожженных листов позволяет изготавливать из них легконагруженные изделия методом глубокой вытяжки. По коррозионной стойкости АМС практически не уступает техническому алюминию. Листы из сплава АМг. Чем выше содержание магния в сплавах этой группы, тем они прочнее, но менее пластичны. Механические свойства . Чаще всего используются листы из сплавов AMg2 (состояния M, h3, H) и AMg3 (состояния M и h3), в том числе гофрированные. Сплавы АМг1, АМг2, АМг3, АМг4 хорошо деформируются как в горячих, так и в холодных условиях. Листы имеют удовлетворительную штампуемость. Закалка значительно снижает штампуемость листов. Листы этих марок используются для конструкций средней нагрузки. Листы из AMg6 и AMg6 не поставляются в закаленном состоянии. Применяются для конструкций повышенной нагрузки. Коррозионная стойкость Сплавы АМг характеризуются высокой коррозионной стойкостью в растворах кислот и щелочей. Сплавы АМг1, АМг2, АМг3, АМг4 обладают высокой коррозионной стойкостью к основным видам коррозии как в отожженном, так и в отвержденном состоянии. Сплавы АМг5, АМг6 склонны к коррозии под напряжением и межкристаллитной коррозии. Для защиты от коррозии листы и пластины из этих сплавов плакируются, а заклепки из АМг5п только анодируются. Свариваемость.Все сплавы АМг хорошо свариваются аргонодуговой сваркой, но характеристики шва зависят от содержания магния. С увеличением его содержания коэффициент трещинообразования уменьшается, а пористость сварных соединений увеличивается. Сварка налипших листов исключает налипание в зоне термического влияния сварного соединения, механические свойства в этой зоне соответствуют свойствам в отожженном состоянии. Поэтому сварные соединения закаленных листов АМг имеют меньшую прочность по сравнению с основным материалом. Сварные соединения АМг1, АМг2, АМг3 обладают высокой устойчивостью к коррозии. Для обеспечения коррозионной стойкости шва АМг5 и АМг6 требуется специальная термообработка. Листы и плиты из Д1, Д16, В95 . Высокопрочные сплавы Д1, Д16, В95 обладают низкой коррозионной стойкостью. Самые распространенные листы дюралюминия Д16. Фактические значения механических параметров для листов Д16АТ (согласно паспортам качества) составляют: предел текучести ? 0,2 = (28-32), предел прочности при разрыве ? при = (42-45) удлинение ? = (26-23%). Сплавы этой группы свариваются точечной сваркой, но не плавлением. Поэтому основной способ их соединения — заклепки. Для заклепок используется проволока от Д18Т и В65Т1. Сопротивление сдвигу для них составляет 200 и 260 МПа соответственно. Из листового проката доступны листы Д16 и В95. Пластины поставляются в состоянии «без термической обработки», но есть возможность термического упрочнения уже готовых деталей после их изготовления. Листы и плиты из B95 имеют большую (по сравнению с D16) прочность на сжатие. Наличие листов и плит — см. На странице сайта «Алюминиевые листы» ******************** Свойства алюминиевых сплавов общего назначения кратко рассмотрены выше.Для специальных целей используются либо другие сплавы, либо более чистые версии сплавов D16 и B95. Чтобы представить разнообразие специальных сплавов, используемых в ракетно-авиационной технике, посетите сайт http: // |
Химический состав в% сплава АМг2 | ||
Fe | до 0,4 | |
Si | до 0,4 | |
Мн | 0,2 — 0,6 | |
Ti | до 0.![]() | |
Al | 95,3 — 98 | |
Cu | до 0,1 | |
мг | 1,8 — 2,8 | |
Zn | до 0,2 |
Производство проката (труб) из сплава АМг2 (и т.п.) методом волочения: Для волочения используют трубную заготовку, полученную прессованием или прокаткой на станах ВДН. В последнем случае в основном проводят только волочение без волочения, чтобы получить трубы необходимого диаметра и устранить характерный дефект прокатки — волнистость.Диаметр заготовки из фрез HPT 85-16 мм, толщина стенки от 5 до 0,35 мм, разница 10%. Заготовка для вытяжки, полученная прессованием на горизонтальных или вертикальных прессах, используется для вытяжки оправки и предохранителя. Диаметр заготовок от 360 до 20 мм, толщина стенки не менее 1,5 мм, разница 20%. Чтобы уменьшить количество переходов при волочении и дорогостоящем промежуточном отжиге, они стремятся получить толщину стенки прессованной заготовки как можно ближе к готовой трубе. Этому препятствуют повышение удельных давлений и низкая производительность при прессовании, а также увеличение относительной разницы в прессуемой заготовке более 20%. Последнее особенно важно, так как при рисовании относительная разница практически не уменьшается.
Заготовка перед вытяжкой очищается, сортируется и нарезается на необходимую длину с учетом длины захвата, торцевой обрезки и технологического припуска на точность номинальной толщины стенки (от 100 до 300 мм).После резки труб дефекты зачищаются, а захваты скручиваются с помощью пневмомолота, ковочных роликов, кривошипно-ковочных или роторно-ковочных машин.
Вытяжки для волочения труб
Значения оптимальных кожухов могут сильно различаться для труб из одного и того же сплава, что объясняется множеством факторов, действующих в производственной среде. Чем выше культура производства, тем короче диапазон разброса крайних значений оптимальных вытяжек.
На рисунке слева показан график, показывающий поле вариации значений интегрального показателя оптимальных вытяжек, полученных в производственной среде. Как видно из этого рисунка, разброс очень большой и его необходимо учитывать.
Поэтому ниже представлены средние значения оптимальных вытяжек при волочении труб из алюминиевых сплавов. Наряду с частыми вытяжками для перехода, также выполняются полные вытяжки от отжига к отжигу.
Краткое обозначение: | ||||
σ в | — временная прочность на разрыв (предел прочности), МПа | ε | — относительный осадок при появлении первой трещины,% | |
σ 0,05 | — предел упругости, МПа | Дж до | — прочность на скручивание, максимальное напряжение сдвига, МПа | |
σ 0.2 | — условный предел текучести, МПа | σ на выходе | — предел прочности при изгибе, МПа | |
δ 5 , δ 4 , δ 10 | — удлинение после разрыва,% | σ -1 | — предел выносливости при испытании на изгиб с симметричным циклом нагружения, МПа | |
σ кр 0,05 и σ кр | — предел текучести при сжатии, МПа | Дж -1 | — предел выносливости при испытании на кручение с симметричным циклом нагружения, МПа | |
ν | — относительный сдвиг,% | n | — количество циклов нагружения | |
сек в | — кратковременная прочность, МПа | R и ρ | — удельное электрическое сопротивление, Ом · м | |
ψ | — относительное сужение,% | E | — нормальный модуль упругости, ГПа | |
KCU и Kcv | — ударная вязкость, определенная на образце с концентраторами соответственно формы U и V, Дж / см 2 | т | — температура, при которой достигаются свойства, Grad | |
с T | — предел пропорциональности (предел текучести при остаточной деформации), МПа | l и λ | — коэффициент теплопроводности (теплоемкость материала), Вт / (м · ° С) | |
HB | — Твердость по Бринеллю | С | — удельная теплоемкость материала (диапазон 20 o — T), [Дж / (кг · град)] | |
Hv | — твердость по Виккерсу | p n и r | — плотность кг / м 3 | |
HRC e | — твердость по Роквеллу, шкала C | , и | — коэффициент температурного (линейного) расширения (диапазон 20 o — T), 1 / ° С | |
HRB | — твердость по Роквеллу, шкала B | σ т T | — предел прочности, МПа | |
Hsd | — твердость по Шору | г | — модуль сдвига при кручении, ГПа |
Механические свойства алюминиевых сплавов определяются их химическим составом, состоянием (обработкой), видом и размерами полуфабрикатов, наличием или отсутствием плакировки и т. Д.Поэтому приведенные в табл. 1 данные по химическому составу и механическим характеристикам приняты с некоторым усреднением по сравнению с данными СНиП П-Э.5-64. Диаграммы растяжения и сжатия различных алюминиевых сплавов относительно мало отличаются друг от друга, однако, в отличие от стали, они не имеют предела текучести; Напряжение обычно принимается за условный предел текучести сплавов с относительным остаточным удлинением 0,2%.
Таблица 1. Алюминиевые сплавы для строительства (СНиП II-Б.5-64)
Группа сплава | Марка и состояние сплава | Легирующие компоненты в% | Механические свойства | |||||||||
магний | марганец | кремний | цинк | медь | другое | σ дюйм, кг / мм 2 | σ 0.![]() | τ дюйм, кг / мм 2 | δ,% | HB, кг / мм 2 | ||
А. Сплавы деформируемые для элементов конструкций | ||||||||||||
Технический алюминий | Количество примесей 0,7% | |||||||||||
Алюминий марганец | ||||||||||||
Алюминий и магний (Magnalias) | 0,2-0,6 * | |||||||||||
0,2-0,6 * | ||||||||||||
Титан 0. | ||||||||||||
АМг61-М ** | ||||||||||||
Алюминий-магний-кремний | ||||||||||||
Хром 0. | ||||||||||||
0,15-0,35 * | ||||||||||||
Алюминий Цинк Магний | ||||||||||||
Алюминий-медно-магний (дюралюминий) | ||||||||||||
Алюминий-цинк-магний-медь | Хром 0. | |||||||||||
Б. Сплавы деформируемые для заклепок и болтов | ||||||||||||
Алюминий-медно-магний | ||||||||||||
Алюминий-цинк-магний-медь | Титан 0.02-0.08 | |||||||||||
Б. Сплавы для литых деталей | ||||||||||||
Алюминий магний | ||||||||||||
Д. | ||||||||||||
Проволока сварочная из алюминия и алюминиевых сплавов принимается по ГОСТ 7871 . | ||||||||||||
* Марганец или хром в том же количестве. ** Данные приблизительны. |
Химический состав и механические характеристики алюминиевых сплавов для строительства, включенных в СНиП П-В.5-64, приведены в таблице. 1.
Занесено в таблицу. 1 алюминиевые сплавы предназначены:
для ограждающих конструкций — АД1-М, АМц-М, АМг-М и АД31-Т; эти сплавы отличаются высокой коррозионной стойкостью и технологичностью;
для конструкций, совмещающих несущие и ограждающие функции (в зависимости от необходимой прочности и коррозионной стойкости) — АМц-М, АМц-П, АМг-М, АМг-П, АМг5-М, АД31-Т, АД31-Т1, АД33-Т, АД33-Т1, АД35-Т, АБ-М, АБ-Т; эти сплавы характеризуются высокими или средними показателями коррозионной стойкости и технологичности;
для несущих сварных конструкций — АМг5-М, АМг6-М, АМг61-М, АД33-Т1, АБ-Т1, В92-Т; сплав АВ-Т1 по условиям коррозионной стойкости следует использовать с содержанием меди до 0. 1%;
для несущих клепанных и болтовых конструкций — те же сплавы, что и для несущих сварных конструкций с добавлением сплавов Д1-Т, Д16-Т и В95-Т1; однако последние три сплава обладают пониженной коррозионной стойкостью.
Дополнительно к перечисленным СНиП II-Б.5-64 предусматривает применение при соответствующем обосновании других марок и состояний алюминиевых сплавов.
Для заклепок и болтов в дополнение к указанным в табл. 4.17, сплавы АД1-М (заклепки с сепаратором), АМц, АМг5п-М (здесь индекс «р» обозначает сплав для изготовления проволоки и прутков), АМг, АД33-Т1, АВ-Т1 и др.
Нормативное сопротивление деформируемых алюминиевых сплавов растяжению, сжатию и изгибу принимается меньшим из двух значений: 0,7 наименьшего временного предела прочности, установленного стандартами или техническими условиями, или условного предела текучести, соответствующего напряжению при относительной остаточной величине. удлинение 0,2%.
Ударная вязкость алюминиевых сплавов колеблется от 1 кгГ / см 2 (В95-Т1) до 9 кг / см 2.