Призма станочная чертёж
Призмой в машиностроении называется – самостоятельная деталь либо элемент станочного приспособления, предназначенного для крепления на металлорежущих станках заготовок цилиндрической формы. Также посредством этого приспособления возможно выполнение различных разметочных работ и контрольных операций.
По своим конструкционным особенностям призмы для станочного оснащения делятся на несколько типов:
• подвижные;
• опорные;
• неподвижные;
• установочные;
• с боковым типом монтажа.
Выбор подобной станочной оснастки должен осуществляться исходя из типа используемого оборудования на производстве и характера изготавливаемых деталей. Также во время подбора призм нужно учитывать финансовую сторону вопроса.
Наименование
Призма
Формат файла
*.dwg
Файл архива
*.rar
Размер файла
44,4 кб
Скачать
Бесплатно
Использование станочных призм на производстве
При изготовлении деталей цилиндрической формы иногда требуется просверлить поперечное отверстие в теле вала или оси. Для реализации подобных задач применяются разные приспособления для надежной фиксации такого плана изделий.
Как правило, перед дальнейшей обработкой заготовки или детали устанавливаются на призмы, закреплённые на приспособлении, которые свою очередь предварительно закрепляются на станках.
Со стороны одного из двух торцов тела вращения, как правило, монтируют специальный упор. Это делается для того чтобы обеспечить нужное положение отверстия по отношению к торцу заготовки и оси проделываемого отверстия.
С противоположной стороны торца заготовки в некоторых случаях используют подпружиненный упор. Данная деталь за счет усилия, создаваемой пружиной обеспечивает прижим изделия к упору, установленному с другой стороны торцевой части заготовки.
Фиксация детали вращения на призмах достигается за счёт прижатия специальными прижимами, передающими усилия эксцентрика. Прижим непосредственно воздействует на заготовку, обеспечивая её неподвижность при обработке поверхностей и стабильность установки каждой детали.
Особенности производства станочных призм
Для промышленного изготовления станочных призм используется сталь марки 20Х стандартизованной по ГОСТ 4543–71.
Однако для изготовления подобных приспособлений возможно применение и иных марок стали, но при этом их механические свойства должны быть не ниже чем у стали вышеуказанной марки.
Станочные призмы подвергаются термической обработке в виде цементации на глубину 0,8...1,2 мм
. Твердость рабочих поверхностей полученных в результате данного технологического процесса составляет 56...61 HRC
.
Преимущества использования станочных призм
Среди позитивных сторон применения специальных приспособлений такого плана на производстве можно выделить следующие моменты:
• снижение затрат на такие дорогостоящие операции, как выверка и разметка изготавливаемой детали, а также возможность автоматизации данного процесса;
• повышение уровня производительности труда. Применение станочных призм при изготовлении и обработки металлических изделий дает возможность сократить временные затраты на выполнение конкретной операции;
• возможность расширения спектра выполняемых операций на одном станке. Различные подобные приспособления позволяют с помощью одного станка выполнять не одну, а несколько операций, тем самым экономя производственные затраты. Что особенно актуально при серийном изготовлении деталей и комплектующих.
Экономическая целесообразность
Конечно же, покупка любого приспособления либо дополнительного оснащения для имеющегося оборудования требует определенных финансовых затрат. Поэтому при принятии решения нужно учитывать тот факт, что все затраты на покупку таких деталей, должны полностью компенсироваться за счет снижения производственных затрат. При выборе таких приспособлений нужно учитывать не только их стоимость, но и их функциональные возможности, а так же удобство в эксплуатации.
Анализ точности установки заготовок на опорные призмы с учетом влияния размерных связей Группа компаний ИНФРА-М — Эдиторум
Введение
При оценке достижимой точности изготов-ления деталей машин применяется расчетно-статистический метод учета различного рода элементарных погрешностей обработки дета-лей. Погрешность установки заготовок в при-способлении является одной из таких элемен-тарных погрешностей. Корректный расчет по-грешности установки важен для оценки на-дежности обеспечения точности выполнения технологической операции [1 4].
В станочных приспособлениях в качестве установочных элементов широко применяют-ся опорные призмы. Призмы позволяют цен-трировать заготовки, совмещая плоскость симметрии цилиндрической поверхности за-готовки с плоскостью симметрии паза.
Погрешность установки определяют как сумму погрешностей базирования, погрешно-сти закрепления и погрешности положения. В работах [5, 6] рассмотрены особенности фор-мирования погрешностей базирования и по-ложения в процессе установки заготовок в широкую призму, а также даются рекоменда-ции назначения точности основных парамет-ров призм. При этом все допуски рассматри-ваются как линейные параметры, в результате чего не учитываются некоторые дополнитель-ные эффекты.
При использовании станочных приспособ-лений с опорными призмами происходит са-моустановка заготовки в V-образном пазу призмы [7]. В результате самоустановки фор-мируются определенные размерные связи в системе «заготовка ‒ приспособление». Для оценки величины погрешности установки не-обходимо выполнить анализ этих связей ме-тодом размерного анализа (рис. 1).
Рис. 1. Расчетная схема с вогнутыми поверхностями призмы
На расчетной схеме (см. рис. 1) учитываются следующие параметры: контрольный размер L, характеризующий смещение верхней точки заготовки; контрольный размер , характеризующий смещение центра заготовки; радиус устанавливаемой заготовки R; размер до условного центра V-образного паза H; угол , равный половине угла V-образного паза; угол симметрии V-образного паза β; размер макроотклонения , характеризующий откло-нения от плоскостности базовых поверхностей V-образного паза; радиус цилиндров r, моделирующих отклонения от плоскостности базовых поверхностей V-образного паза; размеры a и b, определяющие положения центров цилиндров, моделирующих отклонения от плоскостности базовых поверхностей V-образного паза; размеры I, характеризующие износ призмы в процессе эксплуатации; размеры U, характеризующие упругие деформации заготовки при закреплении; углы 1 и 2, определяемые условием самоустановки заго-товок в призме.
Контрольный размер L на схеме изображен вертикальным условно. В действительности он замыкает размер H с верхней точкой раз-мера R заготовки. Таким образом, в общем случае размер L содержит погрешность уста-новки как вдоль оси OX, так и вдоль оси OY.
Макроотклонения в данной расчетной схе-ме представлены отклонением от плоскостно-сти поверхностей V образного паза и модели-руются в виде цилиндров. Допуск отклонения от плоскостности задается допуском размера . Положение максимума макронеровности задается размером a. Значения размера a мо-жет изменяться, при этом оставаясь в преде-лах длины боковой стороны паза призмы. Размер b также используется для моделирова-ния отклонений от плоскостности базовых поверхностей V-образного паза призмы. Значение размера b определяется значениями размеров и a.
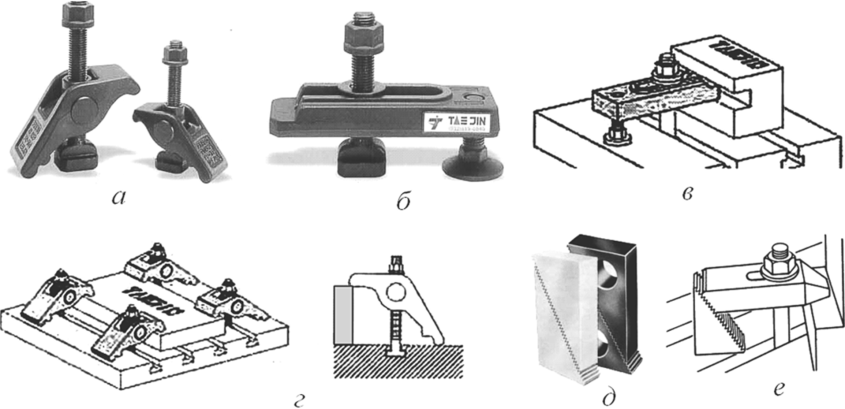
В данной расчетной схеме также учитыва-ется потеря точности призмы вследствие из-нашивания и контактных деформаций базовых поверхностей V-образного паза.
Если рассматривать параметры призмы не-зависимо, т.е. вместо a, b, r и δ ввести размеры a1, a2, b1, b2, r1, r2, δ1 и δ2, то для определения погрешностей контрольных размеров L и из расчетной схемы можно выделить несколько размерных цепей, формирующих следующую систему уравнений:
Первые четыре уравнения системы пред-ставляют две размерных цепи, описывающие самоустановку заготовки в опорной призме. Такие цепи называют замкнутыми. Остальные четыре уравнения системы описывают фор-мирование фактических значений конструк-торских размеров L и . Такие цепи называют открытыми.
В матричном виде система размерных уравнений имеет вид [8]:
,
где [A], [B] – матрицы частных производных, представляющих влияние конструкторских
размеров и самоустанавливающихся размеров в замкнутых цепях соответственно; [C], [D] – матрицы частных производных, представ-ляющих влияние конструкторских размеров и самоустанавливающихся размеров в открытых цепях соответственно; {x} – вектор допусков конструкторских размеров заготовок и опор-ной призмы; {} ‒ вектор допусков самоуста-навливающихся размеров, значения которых определяются другими размерами в замкну-тых цепях; {V} – вектор допусков замыкаю-щих звеньев, определяющих точность уста-новки заготовок в опорной призме.
В результате преобразований получаются следующие выражения передаточных коэф-фициентов Cj для всех рассматриваемых па-раметров (табл. 1).
1. Передаточные коэффициенты для расчетной схемы с вогнутыми поверхностями призмы
СH СR Сa1 Сa2 Сα Сβ Сδ1 Сδ2 СI1 СI2 СU1 СU2
Δx 0 0 0 0 0 sin a 2 cos 2 cos a 2 cos a 2 cos a 2 cos a 2 cos a
Δy 0 sin 0 0 cos2 — 1 0 2 sin 2 sin a 2 sin a 2 sin a 2 sin a 2 sin a
Lx 0 0 0 0 0 sin a 2 cos a 2 cos a 2 cos a 2 cos a 2 cos a 2 cos a
Ly 1 sin 0 0 cos2 — 1 0 2 sin a 2 sin a 2 sin a 2 sin a 2 sin a 2 sin a
Анализ результатов показывает отсутствие влияния допуска размера a на точность уста-новки из-за малости отклонения от плоскост-ности базовых поверхностей V-образного па-за. Также из полученных значений передаточ-ных коэффициентов Cj видно, что призма дает погрешность установки не только вдоль своей оси симметрии, вертикальной оси OY, но и вдоль горизонтальной оси OX (погрешность центрирования), что может вызывать допол-нительные отклонения операционных разме-ров в процессе выполнения технологических операций (например, эксцентриситеты отвер-стий, отклонения от симметричности шпоночных пазов и др.
Анализ передаточных
коэффициентов макроотклонений
Влияние погрешностей формы базовых по-верхностей V-образного паза призмы выпол-няется при помощи двух расчетных схем. Точность боковых сторон паза будет норми-роваться одинаково, т.е. δ1 = δ2.
Первая расчетная схема размерных связей, формирующихся при установке заготовок в опорной призме, аналогична описанной выше (см. рис. 1). В данной схеме макронеровности δ, износ I и контактные деформации U с обеих сторон V-образного паза принимаются одина-ковыми. Также одинаковы и вспомогательные параметры a, b и r.

Система размерных уравнений будет иметь следующий вид:
В результате получаем следующие выражения для определения передаточных коэффициентов Сj для всех рассматриваемых параметров, представленные в виде матрицы:
.
Из полученных выражений Cδ (см. табл.1) следует, что в заданных условиях макроот-клонения δ оказывают влияние только на по-грешность установки заготовки в направлении оси OY и при этом достигают максимальных значений.
Для получения другого предельного поло-
жения заготовки в опорной призме использо-валась расчетная схема, представленная на рис. 2. Ее особенность заключается в том, что левая плоскость паза призмы выпукла, а пра-вая – вогнута. При таких фактических значе-ниях отклонений от плоскостности смещение заготовки происходит преимущественно в на-
правлении горизонтальной оси ОX.
Построение системы размерных уравнений и ее решение выполняется аналогично. Полу-ченная матрица передаточных коэффициентов Сj отличается лишь значениями передаточных коэффициентов для допуска отклонения от плоскостности базовых поверхностей
Передаточные коэффициенты, характеризую-щие влияние на смещение вала вдоль оси OY равны 0, а передаточные коэффициенты, ха-рактеризующие влияние на смещение вала вдоль оси ОX, после подстановки номиналь-ного значения для размера а равны 1/cos . Направление выпуклости макронеровностей в расчетной схеме оказывает влияние лишь на знак передаточного коэффициента.
Рис. 2. Расчетная схема с выпукло-вогнутыми по-верхностями призмы
.
Расчет погрешности установки заготовок в опорной призме. Погрешность установки заго-товки в опорную призму для размера Δ может быть определена следующим образом [9]:
‒ в вертикальном направлении (ось OY)
‒ в горизонтальном направлении (ось OX)
где Ki , KΣ – коэффициенты относительного рассеяния соответственно i-го параметра и исходного звена (погрешности установки) [9].
В полученных выражениях можно выде-лить составляющие погрешности установки: погрешность базирования, погрешность за-крепления и погрешность положения.
Учет точности обеспечения угловых па-
раметров V-образного паза при изготовле-нии опорной призмы. На практике часто точность опорных призм обеспечивается ме-тодом пригонки в процессе окончательной шлифовки установочных элементов приспо-собления в сборе. Контроль точности изготов-ления призмы выполняется при помощи кон-трольного вала по размеру L (рис. 3).
Рис. 3. Cхема пригонки призмы
Для стандартных опорных призм ГОСТ 12195-66 нормирует значения диаметра d кон-трольного вала и размер L, точность которого
должна соответствовать отклонению h6. Ана-логично точность задается в других стандар-тах, описывающих конструкции призм, ис-пользуемых в станочных приспособлениях.
В случае обеспечения точности размера L опорной призмы по контрольному валу в ка-честве компенсирующего звена выбирается размер H, определяющий высоту V образного паза относительно основания призмы или ба-зовой плоскости корпуса приспособления, ис-пользуемой для установки на стол станка. За-тем в процессе шлифовки призмы и снятия материала с боковых сторон паза добиваются необходимой точности по размеру L.
Такая схема срабатывает только без учета влияния угловых размеров на точности приз-мы. В частности, важно жестко лимитировать допуск угла V образного паза. Согласно ГОСТ 12195-66 диаметр d контрольного вала выбирается из середины интервала возмож-ных диаметров базовых поверхностей загото-вок. Следовательно, после пригонки призмы в размер L по диаметру d контрольного вала, установка и обработка заготовок с номиналом базовой поверхности больше d может приво-дить к браку.
В представленной расчетной схеме можно выделить следующие размерные контуры:
Коэффициент передаточного отношения размера L1 на точность размера заготовки L2, определяется выражением C – EB-1A. После подстановки номинальных значений размеров a1 = R1/tg и a2 = R2/tga получим:
Из данного выражения видно, что установ-ка заготовок с размером базовой поверхности R2, превышающей размер контрольного вала R1, может приводить к выходу за допуск по размеру L2. Таким образом, необходимо более жестко нормировать допуски угловых разме-ров стандартных призм, либо выбирать в ка-честве диаметра контрольного вала наиболь-ший диаметр из подходящего интервала уста-
навливаемых деталей.
Заключение
В статье на примере приспособления с опорной призмой показан анализ погрешности установки станочных приспособлений при помощи размерного анализа. Получены выражения для определения погрешности установки в целом, а также выражения для определения передаточных коэффициентов отдельных параметров опорной призмы. Показана необ-ходимость учета погрешности центрирования заготовок в опорных призмах (погрешность установки в горизонтальном направлении вдоль оси OY). Описаны недостатки задания точности V-образных пазов призм, используемых в стандартах.
OptiPro представляет станок для шлифования призм PZX
Управляемый простым в использовании программным обеспечением для шлифования призм, PZX оснащен пятиосевым ЧПУ и двумя шпинделями для черновой и тонкой шлифовки всех поверхностей призмы за один цикл.
Онтарио, штат Нью-Йорк. Компания OptiPro Systems, LLC (www.optipro.com), мировой лидер в производстве оборудования для производства прецизионной оптики, разработала станок для шлифовки призм PZX, который идеально подходит для компаний, стремящихся повысить эффективность процесса производства призм. PZX способен обрабатывать призмы толщиной до 6 дюймов с максимальной диагональю поверхности 10 дюймов.
Вдохновленный отзывами клиентов, PZX включает в себя множество функций, упрощающих и повышающих эффективность обработки призм. Станок оснащен удобным программным обеспечением OptiPro серии G, которое позволяет операторам быстро настраивать задания для создания всех поверхностей призм за один цикл. Пользователи могут вводить различные параметры при настройке задания, например, указывать угол и удаление материала для каждой поверхности.
Пять осей движения с числовым программным управлением (ЧПУ), включая ось B с -9от 0 до 180 градусов движения, позволяют обрабатывать сложные углы при использовании программного обеспечения Mastercam для автоматизированного производства. PZX также имеет двойные шпиндели, которые могут быть оснащены инструментами для грубой и тонкой шлифовки. После завершения чернового шлифования головка с двумя шпинделями поворачивается на 180 градусов по оси B, позволяя станку плавно перейти к тонкому шлифованию. С PZX больше не требуется ручная замена инструментов после чернового шлифования.
«PZX предназначен для повышения эффективности всего процесса шлифования призм, — сказал Майк Бехтольд, президент OptiPro. «Понятные и простые вводные данные в нашем программном обеспечении серии G упрощают настройку заданий по призме, движение по пяти осям и двойные шпиндели позволяют полностью обработать призму за один цикл, а встроенный инструмент и измерение детали упрощают выполнение операций в реальном времени. обрабатывать призматические поправки».
PZX является одним из серии гибких оптических шлифовальных станков с ЧПУ, предлагаемых OptiPro. Каждая машина спроектирована и изготовлена командой опытных инженеров и техников на предприятии компании площадью 40 000 квадратных футов в Онтарио, штат Нью-Йорк. Каждая машина проходит тщательное тестирование, чтобы гарантировать удовлетворенность клиентов после продажи.
Об ОптиПро:
OptiPro Systems — единственная американская компания, которая разрабатывает и производит оборудование для оптической шлифовки с ЧПУ, высокоскоростной сферической полировки, субапертурной полировки и метрологическое оборудование. Компания ОптиПро была основана в 1982 на принципах честности продаж в сочетании с беспрецедентным обслуживанием и поддержкой. Сохранение этой бизнес-модели позволило компании стать мировым лидером в предоставлении инновационных производственных и метрологических решений для точной оптики и передовой керамической промышленности.
###
Контактное лицо для СМИ:
Пэт Бехтольд, координатор по маркетингу
OptiPro Systems
585-265-0160 x235
pbechtold@optipro.com
Подпишитесь на нашу рассылку, чтобы получать новости и обновления от OptiPro Подпишитесь сейчас
Сандвик – Designit
70% машинного программирования для простых деталей происходит на станке, но их интерфейсы застряли в 80-х. Мы сотрудничали с Sandvik, чтобы улучшить рабочие процессы промышленной обработки с помощью Prism, первого сенсорного автоматизированного производственного приложения.
Совместно с Sandvik мы разработали инструмент программирования с числовым программным кодом (ЧПУ), который позволил бы сократить дорогостоящее время программирования, сократить кривую обучения пользователей и оптимизировать рабочий процесс. Чтобы понять повседневный путь различных ролей пользователей в механическом цехе, мы опросили экспертов Sandvik по механической обработке, прежде чем прототипировать и тестировать в итеративных спринтах. Благодаря тесному сотрудничеству с их инженерной командой мы смогли создать и запустить MVP для нового продукта менее чем за шесть месяцев.
Prism — первое CAM-приложение для iPad. Он управляет всем циклом обработки — программированием, моделированием, постобработкой и экспортом в ЧПУ-код. Обратная связь 3D-интерфейса в режиме реального времени позволяет почти любому понять программирование ЧПУ. Prism также открывает новую эру более разумного производства, став первым продуктом, предлагающим поваренные книги для станков с ЧПУ, что позволяет специалистам по обработке и монетизации их опыта, делая ноу-хау отрасли доступным для всех.
Prism — это интегрированное решение, которое сокращает время программирования до 94%.
Результат
Red Dot
Награда за дизайн в 2019 году
Подробнее
ЦУР 9: Создание устойчивой инфраструктуры, содействие инклюзивной и устойчивой индустриализации и стимулирование инноваций
Благодаря новому приложению, которое сокращает время обучения и программирования, Sandvik поддерживает разработку новых интеллектуальных производственных инструментов.